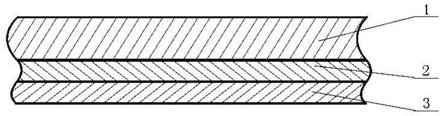
1.本发明涉及炼钢技术领域,具体而言,涉及一种三体式复合铸造抗磨衬板及其制造方法。
背景技术:2.双金属抗磨衬板以其得天独厚的优异使用性能正日益得到广泛的重视和应用。两种不同性状的金属材料铸造成为完整的铸件,面层(工作面)采用抗磨合金材料,具备强度和硬度,背层采用非脆性金属材料,具备塑性和韧性,形成互补,相得益彰。
3.传统上面层材料选用hrc≥55的高铬钼抗磨白口铸铁,背层材料选用中低碳钢。这样,双金属衬板将两者优势结合起来,在不破碎、不断裂的前提下,使用性能较之普通的高锰钢抗磨衬板大幅度地提高,不仅抗磨,而且能够经受剧烈的撞击工况,极具社会和经济效益,用途广泛。
4.然而,这样成型的双金属抗磨衬板在制造应用过程中发现不少弊端,有必要在实施过程中加以优化。
5.首先,面层选用抗磨白口铸铁,背层选用中低碳钢,一个是铁,一个是钢,两者含碳量相差甚大,组织不同,相图不同,在高温下熔融产生差异,结合存在一定的难度,容易形成阻隔,凝固、冷却之后无法无缝对接,以致造成裂纹,甚至分层。
6.其次,两者的铸造收缩率相差一倍,包括线收缩和体收缩,铁的收缩率是1%,钢的收缩率是2%,如此熔融的过程中结合不是十分顺畅,并且形成可观的铸造应力先天不足,为日后装机应用留下隐患。
7.最后,两者的熔点不尽相同,铁的熔点在1400℃左右,钢的熔点在1500℃以上,这样两者的铸造性能如流动性、充型性均不一样,对浇注工艺、耐火材料、凝固时间要求不尽相同,增加了制造过程的难度。
技术实现要素:8.本发明为了克服现有技术的缺陷,在背层中低碳钢和面层高铬钼抗磨白口铸铁中间增加一层过渡层,使得抗磨衬板不仅具有抗磨性,而且能够经受剧烈的撞击工况,各层之间的贴附性更好,并且简化了铸造工艺流程。
9.本发明提供了一种三体式复合铸造抗磨衬板,包括依次排列的背层、过渡层和面层,其中,背层由中低碳钢制成,过滤层由铁素体球墨铸铁制成,面层由高铬钼抗磨白口铸铁制成。
10.与现有技术相比,本发明的三体式复合铸造抗磨衬板具有如下优点:(1)铁素体球铁属于铁的范畴,又兼具钢的性能,可以缓冲两者之间的巨大差异,铁素体球铁密度比钢更小,自重更轻,装机后设备负荷减少,可延长设备的使用寿命,节约能源;(2)铁素体球铁不仅具有优异的强度、塑性和韧性,综合力学性能突出,而且安装、使用过程中还具有钢不具备的微小的依附粘着变形,亲和力良好,贴附更紧密;(3)球铁组织中含有球状石墨,设备运
行中可产生减震、吸噪的效果,不仅改善设备的使用性能,而且兼具环保效益;(4)采用铁素体球铁过渡层可以明显改善三体式复合铸造抗磨衬板的铸造性能和力学性能;(5)铁素体球铁的铸造工艺参数介于两者之间,可以减少铸造过程中的工艺难度;(6)三体式复合铸造抗磨衬板的制造成本低,可操作性强。
11.进一步地,中低碳钢的质量分数百分比组分为,c:0.3~0.4w%,si:≤0.50w%,mn:≤0.90w%,s:≤0.04w%,p:≤0.04w%,余量为fe。
12.进一步地,铁素体球墨铸铁的质量分数百分比组分为,c:2.8~3.2w%,si:2.6~3.1w%,mn:≤0.35w%,p:≤0.06w%,s:≤0.02w%,mg:0.03~0.06w%,re:0.024~0.04w%,余量为fe。
13.进一步地,高铬钼抗磨白口铸铁的质量分数百分比组分为,c:2.0~3.0w%,si:≤1.0w%,mn:0.5~1.0w%,cr:13.0~18.0w%,mo:0.5~2.5w%,ni:0~1.0w%,cu:0~1.2w%,s:≤0.06w%,p:≤0.10w%,余量为fe。
14.进一步地,三体式复合铸造抗磨衬板可广泛应用于冶金、矿山、建材、电力、机械等行业的球磨机衬板、隔仓板、齿板、颚板、轧臼壁、布料溜槽、炉篦条、锤头、冲渣沟等各类耐磨备件。
15.本发明还提供了一种三体式复合铸造抗磨衬板制造方法,包括以下步骤:
16.s1、铸造:采用三台中频感应电炉,分别熔炼中低碳钢、铁素体球墨铸铁和高铬钼抗磨白口铸铁,铁素体球墨铸铁在熔炼时进行球化处理和孕育处理;待熔炼完毕后,首先浇注中低碳钢,并凝固、结晶,再浇注铁素体球墨铸铁,并凝固、结晶,最后浇注高铬钼抗磨白口铸铁,凝固、结晶、冷却后,制得三体式复合铸造抗磨衬板胚料;
17.s2、热处理:先将三体式复合铸造抗磨衬板胚料进行淬火处理,然后再进行回火处理,制得三体式复合铸造抗磨衬板。
18.采用上述三体式复合铸造抗磨衬板铸造方法,可以获得理想的三体式复合铸造抗磨衬板,收缩率平缓过渡,结合紧密、自然,铸造应力大大降低,铸造缺陷显著减少;再将三体式复合铸造抗磨衬板胚体经过淬火和回火处理,使面层材料(高铬钼抗磨白口铸铁)保留原有马氏体组织,又使过渡层球铁获得高塑性和高韧性的铁素体,还可消除面层、过渡层、背层三者的铸造应力和热处理应力;金相组织为铸态铁素体,三体式衬板需淬火,会导致珠光体返现,因此需要实行高温回火,让铁素体重现。
19.进一步地,铁素体球墨铸铁的球化处理工艺采用包内冲入法,球化处理的同时进行孕育处理,具体包括以下步骤:
20.s11、装料:按照铁水量,称取1.3w%~1.8w%铁水量的球化剂和1.0w%~1.2w%铁水量的孕育剂,将球化剂、孕育剂和铁屑放入球化包的反应堤坝内,并依次用捣锤平整捣实,然后再用聚渣剂平铺一层;
21.s12、球化反应:调整好球化包的停放位置,设置球化温度并开始出铁反应,铁水冲入位置为放球化剂及孕育剂的另一侧提坝内开始反应;反应结束后,用聚渣剂撒入铁液表面搅拌,拔渣处理2-3次,将渣拔净后,再用聚渣剂覆盖严实铁液表面,然后进行下一步的浇注。
22.进一步地,孕育剂采用含钡、钙的75fe-si,孕育处理具体包括以下步骤:
23.s121、将20%的孕育剂与球化剂混合后置于包底堤坝内;
24.s122、将70%的孕育剂置于出铁槽上部漏斗内,从出铁开始孕育剂即随铁液溜入包内,铁液出毕,漏斗内孕育剂用尽;
25.s123、将10%的孕育剂进行浮硅处理,在处理扒渣后的铁液表面放上1~2块孕育剂,在铁液表面形成一层富硅层,盖上草灰进行浇注。
26.进一步地,球化剂为采用y-si-fe-mg中间合金的钇基重稀土球化剂,其质量分数百分比的化学成分为,y:3.24w%,mg:7.06w%,si:42.78w%,ba:0.24w%,ca:2.75w%,余量为fe。
27.进一步地,聚渣剂包括草灰、苏打、珍珠岩。
28.进一步地,淬火处理按照高合金抗磨白口铸铁材料工艺执行,即将三体式复合铸造抗磨衬板胚料放入箱式电阻炉,升温至980℃,保温1-2h后,出炉空冷。
29.进一步地,回火处理是将淬火后的三体式复合铸造抗磨衬板胚料重新放入箱式电阻炉,升温至720-750℃,保温1-2h,降温至600℃后,出炉空冷。
附图说明
30.附图1为本发明的三体式复合铸造抗磨衬板的结构示意图;
31.附图标记:1、面层,2、过渡层,3、背层。
具体实施方式
32.为了进一步理解本发明,下面结合实施例对本发明优选实施方案进行描述,但是应当理解,这些描述只是为进一步说明本发明的特征和优点,而不是对本发明权利要求的限制。
33.实施例一
34.一种三体式复合铸造抗磨衬板,包括依次排列的背层、过渡层和面层,其中,背层由中低碳钢制成,过滤层由铁素体球墨铸铁制成,面层由高铬钼抗磨白口铸铁制成,结构示意图参考附图1。
35.中低碳钢的质量分数百分比组分为,c:0.3~0.4w%,si:≤0.50w%,mn:≤0.90w%,s:≤0.04w%,p:≤0.04w%,余量为fe。中低碳钢的力学性能如表1所示。
36.表1
[0037][0038]
高铬钼抗磨白口铸铁的质量分数百分比组分为,c:2.0~3.0w%,si:≤1.0w%,mn:0.5~1.0w%,cr:13.0~18.0w%,mo:0.5~2.5w%,ni:0~1.0w%,cu:0~1.2w%,s:≤0.06w%,p:≤0.10w%,余量为fe。经热处理后的hcr≥55,热处理后的金相组织为共晶碳化物(cr,fe)7c3+二次碳物+马氏体+残余奥氏体。
[0039]
铁素体球墨铸铁的质量分数百分比组分为,c:2.8~3.2w%,si:2.6~3.1w%,mn:≤0.35w%,p:≤0.06w%,s:≤0.02w%,mg:0.03~0.06w%,re:0.024~0.04w%,余量为
fe。热处理后的金相组织为铁素体+少量珠光体+球状石墨+少量团絮状石墨;铁素体球墨铸铁力学性能如表2所示。
[0040]
表2
[0041][0042]
铁素体球铁属于铁的范畴,又兼具钢的性能,可以缓冲两者之间的巨大差异,铁素体球铁密度比钢更小,自重更轻,装机后设备负荷减少,可延长设备的使用寿命,节约能源;铁素体球铁不仅具有优异的强度、塑性和韧性,综合力学性能突出,而且安装、使用过程中还具有钢不具备的微小的依附粘着变形,亲和力良好,贴附更紧密;球铁组织中含有球状石墨,设备运行中可产生减震、吸噪的效果,不仅改善设备的使用性能,而且兼具环保效益;采用铁素体球铁过渡层可以明显改善三体式复合铸造抗磨衬板的铸造性能和力学性能;铁素体球铁的铸造工艺参数介于两者之间,可以减少铸造过程中的工艺难度。
[0043]
实施例二
[0044]
一种三体式复合铸造抗磨衬板的制造方法,包括以下步骤:
[0045]
s1、铸造:采用三台中频感应电炉,分别熔炼中低碳钢、铁素体球墨铸铁和高铬钼抗磨白口铸铁,铁素体球墨铸铁在熔炼时进行球化处理和孕育处理;待熔炼完毕后,首先浇注中低碳钢,并凝固、结晶,再浇注铁素体球墨铸铁,并凝固、结晶,最后浇注高铬钼抗磨白口铸铁,凝固、结晶、冷却后,制得三体式复合铸造抗磨衬板胚料;铁素体球墨铸铁的球化处理工艺采用包内冲入法,球化处理的同时进行孕育处理,具体包括以下步骤:
[0046]
s11、装料:按照铁水量,称取1.3w%~1.8w%铁水量的球化剂和1.0w%~1.2w%铁水量的孕育剂,将球化剂、孕育剂和铁屑放入球化包的反应堤坝内,并依次用捣锤平整捣实,捣实程度依据球化反应的强弱程度进行调整,然后再用聚渣剂平铺一层,以延缓球化剂的起爆时间,从而提高吸收率;球化剂为采用y-si-fe-mg中间合金的钇基重稀土球化剂,其质量分数百分比的化学成分为,y:3.24w%,mg:7.06w%,si:42.78w%,ba:0.24w%,ca:2.75w%,余量为fe;球化剂加入量要适宜,根据出铁温度、出铁量、铸件形状大小、壁厚、浇注时间长短来确定加入量;加入量偏大,则铁水中的含镁量和稀土量升高,降低了力学性能,造成石墨球异化、反白口、加大缩松锁孔倾向、黑渣等缺陷;加入量偏小,则铁水中的含镁量和稀土量降低,造成球化不良或球化衰退等缺陷;聚渣剂由草灰或苏打或珍珠岩组成;通过在球化剂上覆盖薄钢板,以延长球化剂起爆时间,再通过选择钢板的厚度来调整球化潜伏期,启爆前的潜伏时间如表3所示;本发明首次提出球化潜伏期概念,以调整球化剂起爆时间,具有突出的创新性。
[0047]
表3
[0048]
[0049]
s12、球化反应:调整好球化包的停放位置,设置球化温度并开始出铁反应,铁水冲入位置为放球化剂及孕育剂的另一侧提坝内开始反应(切忌直冲球化剂,否则严重影响球化剂的吸收);开始出铁时流速要快易于起爆,待反应激烈时,逐渐减小流速不断流,随着球化反应由强变弱,逐渐加大流速,铁水放至要求值时,球化反应刚好停止;反应结束后,铁液镇静3-5min,用聚渣剂撒入铁液表面搅拌,拔渣处理2-3次,将渣拔净后,再用聚渣剂覆盖严实铁液表面,加入量为拔渣时的2倍,然后进行下一步的浇注,在浇注倒包过程中,聚渣剂要时刻浮在铁液表面,不得挂在包壁上,防止球化元素的逃逸,同时对铁液起保温作用;球化温度要适宜,理想温度为1480-1520℃,温度偏高,球化反应时间短,球化元素烧损大,造成球化衰退或球化不良;解决办法是,出铁时视情况添加冷铁降温;温度偏低,球化反应时间长,甚至在出完铁水还反应,将造成铁水温度低,流动性变差,铸件易出现气孔或冷隔等缺陷;解决办法是,出铁20s后还没有起爆,应该直接用铁水冲击球化提坝引爆反应,球化反应时间在60-90s之间;出铁量,必须听从配料员的指令,因为球化剂加入量是按出铁量确定的;铁水多出,则铁水中的含镁量降低,可能造成球化衰退和球化不良;铁水少出,则铁水中的含镁量和稀土量升高,降低了力学性能;
[0050]
为了避免孕育衰退,采用多次孕育或全程孕育工艺,不宜采用一次性大剂量孕育,在球化处理的同时即开始进行孕育处理,从炉前出铁槽开始到铁液进入型腔,甚至在凝固阶段,铁液始终处于孕育状态,孕育处理具体包括以下步骤:
[0051]
s121、将20%的孕育剂与球化剂混合后置于包底堤坝内;
[0052]
s122、将70%的孕育剂置于出铁槽上部漏斗内,从出铁开始孕育剂即随铁液溜入包内,铁液出毕,漏斗内孕育剂用尽;
[0053]
s123、将10%的孕育剂进行浮硅处理,在处理扒渣后的铁液表面放上1~2块孕育剂,在铁液表面形成一层富硅层,盖上草灰进行浇注;富硅层和下部铁液在浇注时一同流出,混合实施孕育处理。
[0054]
s2、热处理:先将三体式复合铸造抗磨衬板胚料进行淬火处理,然后再进行回火处理,制得三体式复合铸造抗磨衬板;
[0055]
s21、淬火处理按照高合金抗磨白口铸铁材料工艺执行,即将三体式复合铸造抗磨衬板胚料放入箱式电阻炉,升温至980℃,保温1-2h后,出炉空冷;
[0056]
s22、回火处理是将淬火后的三体式复合铸造抗磨衬板胚料重新放入箱式电阻炉,升温至720-750℃,保温1-2h,降温至600℃后,出炉空冷,主要目的是让球铁中珠光体分解,获得最大体积分数的铁素体,同时在面层材料高合金抗磨白口铸铁马氏体分解的临界点温度之下,保留原有组织马氏体,还可消除三者的铸造应力和热处理应力。
[0057]
采用上述三体式复合铸造抗磨衬板铸造方法,可以获得理想的三体式复合铸造抗磨衬板,收缩率平缓过渡,结合紧密、自然,铸造应力大大降低,铸造缺陷显著减少;再将三体式复合铸造抗磨衬板胚体经过淬火和回火处理,使面层材料(高铬钼抗磨白口铸铁)保留原有马氏体组织,又使过渡层球铁获得高塑性和高韧性的铁素体,还可消除面层、过渡层、背层三者的铸造应力和热处理应力。
[0058]
虽然本公开披露如上,但本公开的保护范围并非仅限于此。本领域技术人员,在不脱离本公开的精神和范围的前提下,可进行各种变更与修改,这些变更与修改均将落入本发明的保护范围。