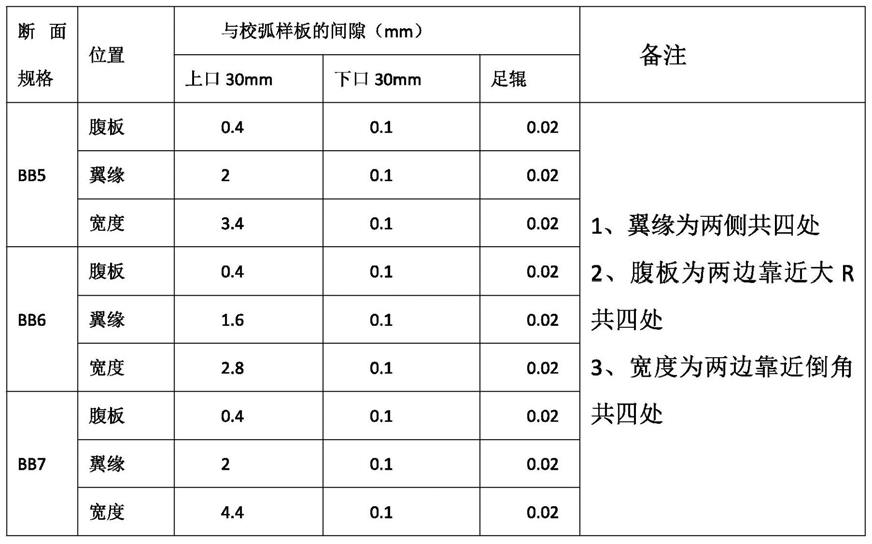
一种用于重型h型钢结晶器的校弧装置及校弧方法
技术领域
1.本发明涉及钢结晶器设备技术领域,具体涉及一种用于重型h型钢结晶器的校弧装置及校弧方法。
背景技术:2.重型h型钢结晶器是国内最大断面规格的连铸连轧生产线,其关键部件-重型h型钢异形坯结晶器铜板全部从国外购置。该结晶器的内部型腔为倒八字形,由内、外弧板及两块窄板拼合成“h”形状,钢水从上口注入,通过结晶器内部的循环水进行冷却,从而形成坯壳从下口拉出。
3.原设计的结晶器“抛物线倒锥度”的弧度精度无法正常保证故在开浇过程中普遍出现了铸坯裂纹较多、铸坯跑偏、弯曲、漏钢次数频繁等弊端,直接导致结晶器寿命低,造成生产线生产不顺利、铸坯成品率不高。此外进口备件费昂贵、供货周期长。
4.鉴于上述缺陷,本发明创作者经过长时间的研究和实践终于获得了本发明。
技术实现要素:5.为解决上述技术缺陷,本发明采用的技术方案在于,提供一种用于重型h型钢结晶器的校弧装置包括第一检测板、第二检测板和加强筋柱,所述第一检测板、所述第二检测板平行设置,若干所述加强筋柱设置在所述第一检测板和所述第二检测板之间,且所述第一检测板和所述第二检测板通过所述加强筋柱固定连接,
6.所述重型h型钢结晶器包括贯通设置的型腔,所述型腔包括腹板内弧段、腹板外弧段、翼缘内弧段、翼缘外弧段、翼缘边缘段,所述腹板内弧段和所述腹板外弧段形成腹板腔,所述翼缘内弧段、所述翼缘外弧段、所述翼缘边缘段形成翼缘腔,所述翼缘内弧段的端部和所述腹板内弧段的端部连接,所述翼缘外弧段的端部和所述腹板外弧段的端部连接,所述翼缘边缘段的两端分别连接所述翼缘内弧段和所述翼缘外弧段,两所述翼缘腔对称设置在所述腹板腔两端从而形成横截面为h型的所述型腔。
7.较佳的,所述第一检测板和所述第二检测板均包括上检测端面、下检测端面、外检测端面和内连接面,所述加强筋柱的端部和所述内连接面连接,所述上检测端面设置和所述下检测端面均设置为圆弧面,且所述第一检测板和所述第二检测板的所述上检测端面圆弧半径相同,所述第一检测板和所述第二检测板的所述下检测端面圆弧半径相同,所述第一检测板和所述第二检测板的所述外检测端面设置为倾斜面。
8.较佳的,所述上检测端面的圆弧半径和所述腹板外弧段或翼缘外弧段的圆弧半径相同,所述下检测端面的圆弧半径和所述腹板内弧段或翼缘内弧段的圆弧半径相同,所述第一检测板和所述第二检测板的所述外检测端面分别与两所述翼缘边缘段的倾斜角度相同。
9.较佳的,在所述型腔的上型腔口位置处沿所述型腔的延伸方向设置有曲线延长段,所述曲线延长段的横截面为与所述型腔横截面相对应的h型,且所述曲线延长段上设置
有腹板内弧检测段、腹板外弧检测段、翼缘内弧检测段、翼缘外弧检测段、翼缘边缘检测段,所述腹板内弧检测段为所述腹板内弧段延伸形成,且所述腹板内弧检测段的圆弧半径与所述腹板内弧段的圆弧半径相同,相对应的,所述腹板外弧检测段为所述腹板外弧段延伸形成,且所述腹板外弧检测段的圆弧半径与所述腹板外弧段的圆弧半径相同;所述翼缘内弧检测段为所述翼缘内弧段延伸形成,且所述翼缘内弧检测段的圆弧半径与所述翼缘内弧段的圆弧半径相同;所述翼缘外弧检测段为所述翼缘外弧段延伸形成,且所述翼缘外弧检测段的圆弧半径与所述翼缘外弧段的圆弧半径相同;所述翼缘边缘检测段为所述翼缘边缘段延伸形成,且所述翼缘边缘检测段的倾斜角度与所述翼缘边缘段的倾斜角度相同。
10.较佳的,所述下型腔口下方设置有足辊,所述足辊包括对应所述翼缘外弧段的外弧侧翼缘足辊、对应所述腹板外弧段的外弧侧腹板足辊、对应所述腹板内弧段的内弧侧腹板足辊、对应所述翼缘内弧段的内弧侧翼缘足辊。
11.较佳的,所述第一检测板和所述第二检测板均包括上检测段、中减重段和下检测段,所述上检测段通过所述中减重段和所述下检测段连接,所述上检测段对应所述曲线延长段设置,所述下检测段靠近所述中减重段的一端对应所述下型腔口设置,所述下检测段远离所述中减重段的一端对应所述足辊设置。
12.较佳的,通过对所述第一检测板和所述第二检测板进行减薄处理从而形成所述中减重段。
13.较佳的,一种所述校弧装置的校弧方法为:计算钢水在结晶器内的收缩情况,从而进一步计算所述下型腔口和所述上型腔口的容差,再根据容差至选择对应塞尺,在校弧时将不同厚度的所述塞尺垫入指定的位置,然后调整所述足辊的高度值,确保所述足辊与所述校弧装置间留有≤0.02mm的缝隙后所述足辊转动即可。
14.与现有技术比较本发明的有益效果在于:1,本发明通过将型腔壁设置成连续平滑倒锥度的平面,来确保冷却一致,确保铸坯均匀生长、坯壳韧性高,大幅度降低铸坯微裂纹等质量缺陷,提高铸坯成品率,实现本地供货,降低备件费用、缩短供货周期;2,采用本发明所述校弧装置有利于模拟铸坯在结晶器型腔内的均匀生长、增加坯壳韧性,大幅度降低了铸坯漏钢几率,提高了铸坯成品率,大幅度降低了备件费用、大大缩短了供货周期,有效地节约时间,提高生产效率,降低劳动强度,增加了安全性。
附图说明
15.图1为所述h型铸坯冷坯的结构视图;
16.图2为所述型腔的结构视图;
17.图3为所述翼缘腔的结构剖视图;
18.图4为所述腹板腔的结构剖视图;
19.图5为所述翼缘边缘段的结构剖视图;
20.图6为优化设计的倒锥度的比较示意图;
21.图7为所述校弧装置的结构视图;
22.图8为所述校弧装置的校弧示意图。
23.图中数字表示:
24.1-腹板内弧段;2-腹板外弧段;3-翼缘内弧段;4-翼缘外弧段;5-翼缘边缘段;6-第
一圆弧段;7-第一圆弧段;11-腹板腔;12-翼缘腔;13-曲线延长段;21-外弧侧翼缘足辊;22-外弧侧腹板足辊;23-内弧侧腹板足辊;24-内弧侧翼缘足辊;31-第一检测板;32-第二检测板;33-加强筋柱;34-上检测段;35-中减重段;36-下检测段。
具体实施方式
25.以下结合附图,对本发明上述的和另外的技术特征和优点作更详细的说明。
26.实施例一
27.如图1、图2所示,图1为所述h型铸坯冷坯的结构视图;图2为所述型腔的结构视图。
28.本发明所述重型h型钢结晶器包括贯通设置的型腔,所述型腔包括腹板内弧段1、腹板外弧段2、翼缘内弧段3、翼缘外弧段4、翼缘边缘段5,所述腹板内弧段1和所述腹板外弧段2形成腹板腔11,所述翼缘内弧段3、所述翼缘外弧段4、所述翼缘边缘段5形成翼缘腔12,所述翼缘内弧段3的端部和所述腹板内弧段1的端部连接,所述翼缘外弧段4的端部和所述腹板外弧段2的端部连接,所述翼缘边缘段5的两端分别连接所述翼缘内弧段3和所述翼缘外弧段4,两所述翼缘腔12对称设置在所述腹板腔11两端从而形成横截面为h型的所述型腔。
29.一般的,所述翼缘内弧段3的端部和所述腹板内弧段1的端部通过倾斜的第一过渡段连接,所述翼缘外弧段4的端部和所述腹板外弧段2的端部通过倾斜的第二过渡段连接,所述第一过渡段和所述腹板内弧段1、所述第二过渡段和所述腹板外弧段2通过第一圆弧段6圆弧过渡,所述第一圆弧段6的半径均相同,且沿所述型腔的延伸方向所述第一圆弧段6的半径保持一致;所述第一过渡段和所述翼缘内弧段3、所述第二过渡段和所述翼缘外弧段4通过第二圆弧段7圆弧过渡,所述第二圆弧段7的半径均相同,且沿所述型腔的延伸方向所述第二圆弧段7的半径保持一致。
30.通过将现有设计的结晶器型腔的大r角(即第一圆弧段6对应图1中的r角)变径尺寸进行了半径统一,有利于减小铸坯在结晶器内部该处的运动阻力;将现有设计的结晶器型腔的小r角(即第二圆弧段7对应图1中的r角)变径尺寸进行了半径统一,有利于减小铸坯在结晶器内部该处的运动阻力。
31.如图3、图4、图5所示,图3为所述翼缘腔的结构剖视图;图4为所述腹板腔的结构剖视图;图5为所述翼缘边缘段的结构剖视图。
32.所述型腔内部沿所述型腔的延伸方向排列设置有若干等宽设置的倒锥度段,各所述倒锥度段上均包括设置在所述腹板内弧段1上的腹板内弧锥度段、设置在所述腹板外弧段2上的腹板外弧锥度段、设置在所述翼缘内弧段3上的翼缘内弧锥度段、设置在所述翼缘外弧段4上的翼缘外弧锥度段、设置在所述翼缘边缘段5上的翼缘边缘锥度段,所述腹板内弧锥度段、所述腹板外弧锥度段、所述翼缘内弧锥度段、所述翼缘外弧锥度段、所述翼缘边缘锥度段均设置为平面,通过设置连续连接的不同倾斜度的倒锥度段以在所述腹板内弧段1、所述腹板外弧段2、所述翼缘内弧段3、所述翼缘外弧段4上形成类圆弧状的弧形端面,所述翼缘边缘段5上形成倾斜平端面,既符合铸坯冷坯的尺寸要求,也有利于保护渣在液面区均匀搅拌,更好地保护结晶器表面镀层,防止液面区镀层脱落。
33.由于倒锥度更加接近平滑,消除了现有设计中“抛物线倒锥度”结晶器中间部位尺寸较大“过度兜钢”情况,确保了冷却一致,有利于铸坯均匀生长、增加坯壳韧性,大幅度降
低了铸坯微裂纹等质量缺陷,提高了铸坯成品率,大幅度降低了备件费用、大大缩短了供货周期,有效地节约时间,提高生产效率,降低劳动强度,增加了安全性。
34.较佳的,所述倒锥度段的宽度设置为100mm。
35.实施例二
36.所述重型h型钢结晶器中型腔的设计方法,包括:
37.s1,通过根据h型铸坯冷坯的尺寸,设置下型腔口尺寸,所述下型腔口尺寸包括腹板尺寸、翼缘尺寸、宽度尺寸、转角尺寸;
38.s2,基于所述下型腔口尺寸设计翼缘外弧弧形端面的半径,并基于翼缘外弧弧形端面的半径设计翼缘内弧弧形端面的半径,通过翼缘外弧弧形端面的半径和翼缘内弧弧形端面的半径,以设计翼缘内弧锥度段和翼缘外弧锥度段的各倒锥度;
39.s3,基于翼缘内弧锥度段和翼缘外弧锥度段的倒锥度,并基于所述下型腔口尺寸,设计腹板内弧弧形端面的半径和腹板外弧弧形端面的半径,并基于腹板内弧弧形端面的半径和腹板外弧弧形端面的半径,以设计腹板内弧锥度段和腹板外弧锥度段的各倒锥度;
40.s4,基于腹板内弧锥度段和腹板外弧锥度段的倒锥度,设计在宽度方向上的两翼缘边缘平端面的倾斜角度,并进一步设计翼缘边缘锥度段的各倒锥度。
41.如图6所示,图6为优化设计的倒锥度的比较示意图;
42.具体的,所述腹板外弧半径的确定过程为,如下图4所示,沿着浇铸半径按100mm间隔等分取值,再将若干直线段进行光滑连接,将最高点
→
中间点
→
最低点进行三点作弧做为基准弧,同时对间距宽度100mm处取值,并确定外弧半径的圆心坐标值。
43.所述腹板内弧半径的确定过程为,如下图4所示,在确定好的腹板外弧半径间距100mm处作水平线,按优化设计的倒锥度见图8所示进行长度取值,并做好点位标记。同理将最高点
→
中间点
→
最低点进行三点作弧做为基准弧,同时对间距宽度100mm处取值,并确定外弧半径的圆心坐标值。
44.所述翼缘外弧半径的确定过程为,如下图3所示,沿着浇铸半径按100mm间隔等分取值,再将若干直线段进行光滑连接,将最高点
→
中间点
→
最低点进行三点作弧做为基准弧,同时对间距宽度100mm处取值,并确定外弧半径的圆心坐标值。
45.所述翼缘内弧半径的确定过程为,如下图3所示,在确定好的翼缘外弧半径间距100mm处作水平线,按优化设计的倒锥度进行长度取值,并做好点位标记。同理将最高点
→
中间点
→
最低点进行三点作弧做为基准弧,同时对间距宽度100mm处取值,并确定外弧半径的圆心坐标值。
46.实施例三
47.基于实施例一特殊结构的型腔,本发明还提供一种用于检测所述腹板内弧段1、所述腹板外弧段2、所述翼缘内弧段3、所述翼缘外弧段4弧度、所述翼缘边缘段5倾斜度以及足辊相对位置的校弧装置。
48.具体的,在所述型腔的上型腔口位置处沿所述型腔的延伸方向设置有曲线延长段13,所述曲线延长段13的横截面为与所述型腔横截面相对应的h型,且所述曲线延长段13上设置有腹板内弧检测段、腹板外弧检测段、翼缘内弧检测段、翼缘外弧检测段、翼缘边缘检测段,所述腹板内弧检测段为所述腹板内弧段1延伸形成,且所述腹板内弧检测段的圆弧半径与所述腹板内弧段1的圆弧半径相同,相对应的,所述腹板外弧检测段为所述腹板外弧段
2延伸形成,且所述腹板外弧检测段的圆弧半径与所述腹板外弧段2的圆弧半径相同;所述翼缘内弧检测段为所述翼缘内弧段3延伸形成,且所述翼缘内弧检测段的圆弧半径与所述翼缘内弧段3的圆弧半径相同;所述翼缘外弧检测段为所述翼缘外弧段4延伸形成,且所述翼缘外弧检测段的圆弧半径与所述翼缘外弧段4的圆弧半径相同;所述翼缘边缘检测段为所述翼缘边缘段5延伸形成,且所述翼缘边缘检测段的倾斜角度与所述翼缘边缘段5的倾斜角度相同。
49.较佳的,所述下型腔口下方设置有足辊,所述足辊包括对应所述翼缘外弧段4的外弧侧翼缘足辊21、对应所述腹板外弧段2的外弧侧腹板足辊22、对应所述腹板内弧段1的内弧侧腹板足辊23、对应所述翼缘内弧段3的内弧侧翼缘足辊24,通过所述足辊起到“扶动”铸坯行走的效果,有效保护结晶器型腔工作面不被划伤。
50.如图7所示,图7为所述校弧装置的结构视图;所述校弧装置包括第一检测板31、第二检测板32和加强筋柱33,所述第一检测板31、所述第二检测板32平行设置,若干所述加强筋柱33设置在所述第一检测板31和所述第二检测板32之间,且所述第一检测板31和所述第二检测板32通过所述加强筋柱33固定连接。
51.具体的,所述第一检测板31和所述第二检测板32均包括上检测端面、下检测端面、外检测端面和内连接面,所述加强筋柱33的端部和所述内连接面连接,所述上检测端面设置和所述下检测端面均设置为圆弧面,且所述第一检测板31和所述第二检测板32的所述上检测端面圆弧半径相同,所述第一检测板31和所述第二检测板32的所述下检测端面圆弧半径相同,所述第一检测板31和所述第二检测板32的所述外检测端面设置为倾斜面。
52.所述上检测端面和所述下检测端面上下对应设置,所述外检测端面和所述内连接面内外对应设置。
53.所述上检测端面的圆弧半径和所述腹板外弧段2或翼缘外弧段4的圆弧半径相同,所述下检测端面的圆弧半径和所述腹板内弧段1或翼缘内弧段3的圆弧半径相同,所述第一检测板31和所述第二检测板32的所述外检测端面分别与两所述翼缘边缘段5的倾斜角度相同。
54.较佳的,所述第一检测板31和所述第二检测板32均包括上检测段34、中减重段35和下检测段36,所述上检测段34通过所述中减重段35和所述下检测段36连接,所述上检测段34对应所述曲线延长段13设置,所述下检测段36靠近所述中减重段35的一端对应所述下型腔口设置,所述下检测段36远离所述中减重段35的一端对应所述足辊设置。
55.通过对所述第一检测板31和所述第二检测板32进行减薄处理从而形成所述中减重段35,减少了接触面,有利于上、下口有效接触获得较为精确的检测数据。
56.通过设计成双片型增加测量宽度,中间等距离焊接4个筋柱,这样可以提高其刚性,延长使用寿命,降低更换所产生的费用。
57.所述校弧装置采用铝镁合金材质,质量减轻便于单人举升控制,大大降低了工人的劳动强度,避免了疲劳导致样板与结晶器型腔碰撞破坏工作面的情况,有利于提高校弧效率。
58.所述校弧装置的有效量程为两端的所述上检测段34和所述下检测段36,以将内、外弧及宽度平面检测集中在一起,极大程度增加了校弧样板的检测功能。
59.采用本发明所述校弧装置有利于模拟铸坯在结晶器型腔内的均匀生长、增加坯壳
韧性,大幅度降低了铸坯漏钢几率,提高了铸坯成品率,大幅度降低了备件费用、大大缩短了供货周期,有效地节约时间,提高生产效率,降低劳动强度,增加了安全性。
60.实施例四
61.如图8所示,图8为所述校弧装置的校弧示意图;采用所述校弧装置的校弧方法为:计算钢水在结晶器内的收缩情况,具体的,预测钢水在在结晶器内、外弧的腹板和翼缘及宽度方向上、下口的收缩情况,从而进一步计算所述下型腔口和所述上型腔口的容差,再根据容差至选择精度较高的塞尺,见下表所示3个断面上的对应设置,在校弧时将不同厚度的精密塞尺垫入指定的位置,然后调整所述足辊的高度值,确保所述足辊与所述校弧装置间留有≤0.02mm的缝隙(通常塞入等厚精密塞尺)后所述足辊转动即可。
[0062][0063]
以上所述仅为本发明的较佳实施例,对本发明而言仅仅是说明性的,而非限制性的。本专业技术人员理解,在本发明权利要求所限定的精神和范围内可对其进行许多改变,修改,甚至等效,但都将落入本发明的保护范围内。