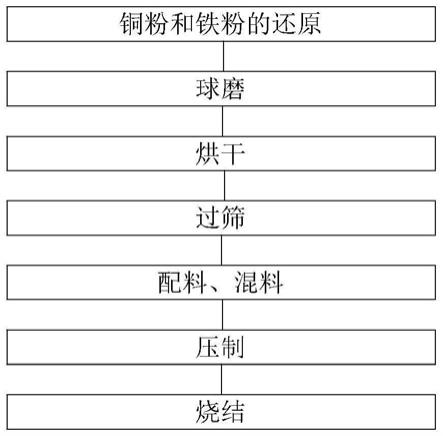
1.本发明涉及粉末冶金铜基刹车材料领域,具体是一种动车组闸片用铜基粉末冶金摩擦材料及其制备方法。
背景技术:2.随着动车组速度的不断提升,作为确保高速下运行安全的制动闸片所受的热负荷和磨损量将成倍增加,其对制动摩擦材料的摩擦磨损性能要求也越来越苛刻。目前我国动车组制动闸片大部分需要进口,不仅增加了成本,而且订货的周期也会延长,严重制约着动车组的发展。现有的铜基粉末冶金摩擦材料存在耐热负荷性能低和使用寿命短等问题,因此不能满足动车组闸片用铜基摩擦材料的使用要求。
3.在公开号为cn108916277a的发明创造中提出了一种铜基刹车片摩擦材料的制备方法,但仅适用轻型车辆,且未明确摩擦试验条件,具有一定的局限性。
4.在公开号为cn107326248a的发明创造中公开了一种高铁制动粉末冶金铜基摩擦材料的制备方法,虽然制备出满足性能的铜基摩擦材料,但未明确摩擦试验条件,具有一定的局限性。
5.在公开号为cn107299300a的发明创造中公开了一种重负荷低磨损铜基摩擦材料及其制备方法,虽制备出铜基摩擦材料,但未经过摩擦试验验证其性能,缺少摩擦试验数据支撑。
6.在公开号为cn110387212a的发明创造中公开了摩擦材料组合物以及用其制备的高速列车制动闸片和应用,其组分中加入一定量的纳米氟化钙,因氟化物对人体有害,不适于大规模工业化生产。
7.在公开号为cn105063459a的发明创造中公开了一种高速列车制动用铜基粉末冶金摩擦材料及其制备方法,仅在摩擦磨损试验机上模拟380km/h高速列车的制动工况,其验证试验不全面,且未说明摩擦试验后铜基摩擦材料的状态,具有一定的局限性。
8.在公开号为cn104480342a的发明创造中公开了一种高摩擦系数耐腐蚀铜基刹车材料及其制备方法,但未说明其摩擦稳定性,具有一定的局限性。
技术实现要素:9.为提高铜基粉末冶金摩擦材料的热稳定性和摩擦稳定性,降低铜基摩擦材料的磨损量,提高铜基摩擦材料的使用时间,本发明提出了一种动车组闸片用铜基粉末冶金摩擦材料及其制备方法。
10.本发明提出的动车组闸片用铜基粉末冶金摩擦材料由45~55%的电解铜粉、10~ 15%的还原铁粉、2~4%的锰粉、4~8%的菱镁石粉、4~8%的铬铁合金、1~4%的钼粉、 10~15%的碳化硅和10~15%的石墨组成。所述的百分比为质量百分比,组分总和为 100。
11.所述电解铜粉中cu的含量≥99.8%。所述还原铁粉中fe的含量≥98.5%。所述锰粉中mn的含量≥99.7%。所述菱镁石粉中mg含量≥75%。所述铬铁合金中cr含量≥60%。所
述钼粉中mos2≥99%。所述碳化硅中sic含量≥98%。所述石墨中c的含量≥99.99%。
12.本发明提出的制备所述动车组闸片用铜基粉末冶金摩擦材料的具体过程是:
13.步骤1,铜粉和铁粉的还原:
14.将铜粉和铁粉分别置于还原炉中进行还原,得到还原后的铜粉和还原铁粉。
15.所述铜粉和铁粉还原时,铜粉的还原温度为400~450℃,升温速率为150℃/h;铁粉的还原温度为650~700℃,升温速率为200℃/h;所述铜粉与铁粉的还原反应的保温时间均为2~3h。
16.步骤2,球磨:
17.将还原合格的铜粉和铁粉分别放入球磨机中球磨0.5~1h。钢球:铜粉=钢球:铁粉=10:1。所述的比例为重量比。
18.所述球磨用的钢球中,大球的直径为96mm,小球的直径为40mm,并且大球:小球=3:1,所述的比例为重量比。
19.步骤3,烘干:
20.将锰粉、菱镁石粉、铬铁合金、二硫化钼、碳化硅和石墨分类放入烘箱内烘干。
21.步骤4,过筛:将烘干的锰粉、铬铁合金、碳化硅和石墨分别进行过筛,取-100 目的锰粉、-200目的铬铁合金、-120目的碳化硅和+80目的石墨备用。
22.烘干时,所述烘箱的升温时间为30min,烘干温度为120~150℃,保温时间为4.0~ 6.0h。
23.步骤5,配料、混料:
24.按质量百分比依次称取所述电解铜粉45~55%、还原铁粉、锰粉、菱镁石粉、铬铁合金、钼粉、碳化硅和石墨,与混合油在双锥型混料机中混合20~24h;得到混合料。
25.在配料、混料时,各配料的总和与该混合油的比例为1:10;所述比例为重量比。其中该配料的重量单位为kg,该混合油的重量单位为ml。
26.所述混合油为汽油与机油的混合物;该汽油:机油=1:1;所述比例为重量比。
27.步骤6,压制:
28.根据产品的设计要求称取得到的混合料并倒入模具中,刮平并冷压成型,得到多个动车组闸片用铜基粉末冶金摩擦材料的压坯。
29.各所述动车组闸片用铜基粉末冶金摩擦材料压坯的密度4.8~5.5g/cm3。
30.所述冷压成型中,铜基粉末冶金摩擦材料压坯单位面积承受的压力为500~ 600mpa,保压时间10s。
31.步骤7,烧结:
32.将叠放后的组装件装入加压烧结炉中进行烧结,得到铜基粉末冶金摩擦材料。
33.烧结时,对所述加压烧结炉在通氢气或氨分解气的条件下以5℃/min升温至120℃保温1.5~2h;保温结束后以2℃/min升温至700℃保温1.5~2h;继续以5℃/min升温至烧结温度890~950℃,加压至烧结压力为0.5~0.7/mpa并保压保温3~5h。烧结结束后,水冷却到60℃以下卸压,出炉。
34.所述得到的铜基粉末冶金摩擦材料的硬度为40~45hrf,剪切强度为7.6~8.2 kg/mm2,抗压强度为4.7~5.1kg/mm2,平均摩擦系数为0.32~0.41,摩擦系数稳定度为4.0~4.6%,磨损量为0.19~0.25cm3/mj
35.本发明成功地制备出了一种动车组闸片用铜基粉末冶金摩擦材料及其制备方法。平均摩擦系数0.32≤μcp≤0.41,磨损量≤0.27cm3/mj。
36.本发明的优点在于:
37.1.采用导热性良好和成本较低的菱镁石粉作为增强材料,不但使铜基粉末冶金摩擦材料的力学性能、抗高温性能和导热性能有明显地提高,而且菱镁石粉原料充足和价格便宜,明显可以降低生产成本,也特别适用于大规模生产。
38.与现有技术相比较,本发明取得的有益效果是:
39.1.本发明利用粉末冶金制备技术,科学地设计材料的各种成分组成,详细地给出了铜基粉末冶金摩擦材料各种原材料的配比及原材料还原、球磨、烘干、过筛、配料、混料、压制、烧结等整个生产过程中的工艺方案及参数。
40.2.本发明通过科学设计材料的各种成分组成,发挥了铜合金基体、润滑组元、固体组元等系统匹配效应,提供了一种具有良好机械强度,适用于速度为350km/h的一种动车组闸片技术要求的铜基粉末冶金摩擦材料,平均摩擦系数0.32≤μcp≤0.41,磨损量≤0.27cm3/mj。
41.3.按照本发明制造的摩擦材料在摩擦过程未出现摩擦层脱落、掉块、卡滞、粘结等现象,制动曲线平稳,无噪音产生、无异味生成、制动稳定可靠。
42.4.本发明的有益效果在于采用导热性良好和成本较低的菱镁石粉作为增强材料,不但使铜基粉末冶金摩擦材料的力学性能、抗高温性能和导热性能有明显地提高,而且菱镁石粉原料充足和价格便宜,明显可以降低生产成本,也特别适用于大规模生产。
附图说明
43.图1是本发明获得铜基粉末冶金摩擦材料试样。
44.图2是本发明获得铜基粉末冶金摩擦材料的sem图。从图中以看出铜基基体与其他组元紧密的连接在一起,并存在一定的孔隙,增大了铜基摩擦材料在摩擦过程中的热稳定性。
45.图3是本发明获得的铜基粉末冶金摩擦材料制成的试样在惯量1.57kg
·
m2、正向压力4.8kn、转速4800rpm、有效半径0.1m条件下测定的摩擦磨损性能试验曲线。图中,图中1是随刹车时间测定的摩擦系数曲线,2是随刹车时间测定的转速曲线,3 是刹车时给定的正向压力曲线。从图中可以看出在一定的压力和转速下,当制备的铜基摩擦材料与摩擦对偶材料形成良好的摩擦接触后,该铜基摩擦材料的摩擦系数趋势较稳定,满足产品技术要求。
46.图4为经过摩擦试验后的铜基粉末摩擦材料,可以看出铜基摩擦材料表面完整,未出现表层剥落、掉块、卡滞、粘结等现象,产品性能稳定。
47.图5为公司投入市场的铜基粉末冶金摩擦材料产品。图6是本发明的流程图。
具体实施方式
48.本发明是一种动车组闸片用铜基粉末冶金摩擦材料及其制备方法,由45~55%的电解铜粉、10~15%的还原铁粉、2~4%的锰粉、4~8%的菱镁石粉、4~8%的铬铁合金、 1~4%的钼粉、10~15%的碳化硅和10~15%的石墨组成。所述的百分比为质量百分比,组
分总和为100。
49.本发明通过4个实施例具体说明其技术方案。各实施例的组分见表1:
50.本发明提出的各实施实施例的组分见表1,其中各组分含量为质量百分比(%)。
51.表1
[0052][0053]
所述电解铜粉中铜的含量≥99.8%,执行标准为gb/t5246-2007。
[0054]
所述还原铁粉中fe的含量≥98.5%,执行标准为gb/t4136-94。
[0055]
所述锰粉中mn的含量≥99.7%,执行标准为yb/t051-2015。
[0056]
所述菱镁石粉中mg含量≥75%,执行标准为中华人民共和国黑色冶金行业标准 yb/t5208-2016。
[0057]
所述铬铁合金中的cr≥60%,执行标准为gb/t 5683-2008。
[0058]
所述钼粉中的mos2≥99%,执行标准为gb/t23271-2009。
[0059]
所述碳化硅中sic含量≥98%,执行标准为gb/t 2480-96。
[0060]
所述石墨中c的含量≥99.99%,执行标准为gb/t3518-95。
[0061]
本发明还提出了一种制备所述铜基粉末冶金摩擦材料的方法。
[0062]
制备所述铜基粉末冶金摩擦材料的具体过程是:
[0063]
步骤1,铜粉和铁粉的还原:
[0064]
将铜粉和铁粉分别置于还原炉中,对该还原炉升温,并以氢气作为保护气氛进行还原,以消除所述铜粉和铁粉中的氧含量及加工硬化现象。还原温度:铜粉为400~ 450℃,升温速率为150℃/h;铁粉为650~700℃,升温速率为200℃/h;铜粉与铁粉的还原反应的保温时间均为2~3h。
[0065]
得到还原后的铜粉和还原铁粉。合格的铜粉为玫瑰红色海绵状,铁粉为银灰色海绵状。
[0066]
本发明提出的各实施例的还原温度工艺参数见表2:
[0067]
表2
[0068][0069]
[0070]
步骤2,球磨:
[0071]
将还原合格的铜粉和铁粉分别放入球磨机中球磨0.5~1h。钢球:铜粉/铁粉= 10:1。所述的比例为重量比。
[0072]
所述钢球包括大球与小球。该大球的直径为96mm,小球的直径为40mm,并且大球: 小球=3:1,所述的比例为重量比。
[0073]
步骤3,烘干:
[0074]
将锰粉、菱镁石粉、铬铁合金、二硫化钼、碳化硅和石墨分类放入烘箱内,将该烘箱升温120~150℃条件下保温4.0~6.0h,以去除上述各种粉末中的水分。
[0075]
所述烘箱的升温时间为30min。
[0076]
本发明提出的各实施例的烘干工艺参数见表3:
[0077]
表3
[0078]
实施例1234烘干温度/℃120130140150保温时间/h6544
[0079]
步骤4,过筛:
[0080]
将烘干的锰粉、铬铁合金、碳化硅和石墨分别进行过筛,取-100目的锰粉、-200 目的铬铁合金、-120目的碳化硅和+80目的石墨备用。
[0081]
步骤5,配料、混料:
[0082]
按质量百分比依次称取电解铜粉45~55%、还原铁粉10~15%、锰粉2~4%、菱镁石粉4~8%、铬铁合金4~8%、钼粉1~4%、碳化硅10~15%和石墨10~15%与混合油在双锥型混料机中混合20~24h,使其颗粒分布均匀;得到混合料。双锥型混合机转速为40~45r/min。
[0083]
所述各配料的总和与该混合油的比例为1:10;所述比例为重量比。其中该配料的重量单位为kg,该混合油的重量单位为ml。
[0084]
所述混合油为汽油与机油的混合物;该汽油:机油=1:1;所述比例为重量比。
[0085]
步骤6,压制:
[0086]
根据产品的设计要求称取得到的混合料并倒入模具中,用刮平器刮平,在5000kn 的液压机上冷压成型,得到密度4.8~5.5g/cm3的铜基粉末冶金摩擦材料的压坯。所述冷压成型中,铜基粉末冶金摩擦材料压坯单位面积承受的压力为500~600mpa,保压时间10s。得到多个动车组闸片用铜基粉末冶金摩擦材料的压坯。
[0087]
本发明提出的各实施例的压制工艺参数见表4:
[0088]
表4
[0089][0090]
步骤7,烧结:
[0091]
将得到的各动车组闸片用铜基粉末冶金摩擦材料的压坯与钢背分别组装成组装
件。按现有技术将各组装件叠放形成料柱,并使各组装件之间用石墨垫板隔开。
[0092]
将叠放后的组装件装入加压烧结炉中进行烧结。
[0093]
对所述加压烧结炉在通氢气或氨分解气的条件下先以5℃/min升温至120℃保温 1.5~2h,以2℃/min升温至700℃保温1.5~2h,再以5℃/min升温至烧结温度890~ 950℃,加压至烧结压力为0.5~0.7/mpa并保压保温3~5h。烧结结束后,水冷却到 60℃以下卸压,出炉,得到铜基粉末冶金摩擦材料。
[0094]
本发明提出的各实施例的烧结工艺参数见表5:
[0095]
表5
[0096]
序号烧结温度℃烧结压力mpa保温时间h实施例19500.73实施例29200.64实施例39000.64实施例38900.55
[0097]
为验证本发明的效果,本发明模拟具体工况条件,通过试验以验证本发明的效果。
[0098]
所述试验机为mm-3000型摩擦磨损性能试验台;摩擦材料制品试样规格为s=6cm2,其中s为试样的表面积;对偶材料为30crmnsi,硬度hrf26~32。
[0099]
试验条件:摩擦材料制品j=1.57kg
·
m2,f=4.8kn,n=4800rpm;其中j为惯量, f为正向压力,n为所述试验机转速。试验环境为干燥环境。
[0100]
试验结果为:通过在mm-3000型摩擦磨损性能试验台上进行摩擦磨损性能试验,本发明获得的铜基摩擦材料制成的试样在惯量1.57kg
·
m2、正向压力4.8kn、转速 4800rpm的摩擦试验条件下,该铜基摩擦材料的平均摩擦系数在0.31~0.41之间,单位面积吸收动能ws≥34539.51j/cm2,平均制动距离s≤803.28m,摩擦制动温度 s≤530.9s,磨损量≤0.27cm3/mj,产品满足技术要求,可用于批量化工业生产。
[0101]
按照上述各实施例中配方所生产的铜基粉末冶金摩擦材料主要物理机械性能下表 6所示:
[0102]
表6
[0103]