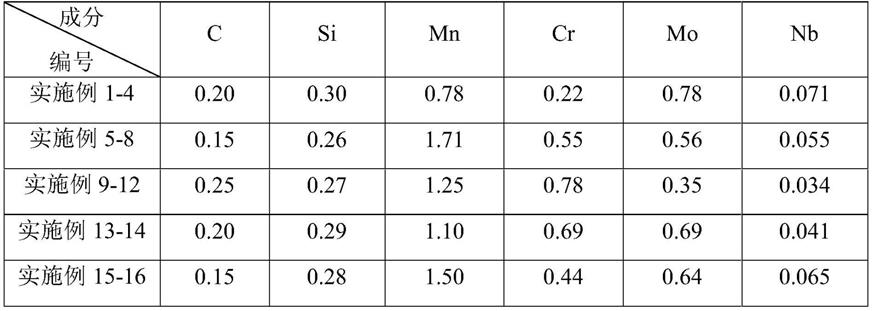
1.本发明属于石油天然气管材技术领域,具体涉及一种基于控制冷却的高强含铌石油套管及其制备方法。
背景技术:2.近年来,随着石油开采朝着深井/超深井方向发展,所需的油井管的服役条件相较以前更为恶劣,随之对油井管用钢的强度与韧性要求也更为严苛。传统的热轧无缝钢管生产工艺流程为:管坯经环形加热炉加热后在高温下连续进行穿孔、轧制、定径等工序,然后置于冷床上空冷至室温,最后进行再加热淬火及高温回火的离线调质热处理。该工艺条件下,经过热变形后的钢管采取在冷床上自然空冷的方式冷却至室温,对于冷却过程的相变组织缺乏有效的在线调控手段,为此对轧态的显微组织及力学性能的改善与提升极为受限。随着钢管控制冷却技术的研发成功,为轧态组织的调控提供了工艺手段,同时通过结合合金元素的特殊设计,可充分发挥细晶、析出、相变等强化机制,提升钢管轧态的力学性能,进而通过组织的遗传性细化最终组织,达到全面提升产品综合性能的目的。
3.申请号为201010221794.6的专利公开了一种石油套管及其制造方法。其主要化学成分为c:0.18~0.35%,si:0.20~0.50%,mn:0.45~1.25%,cr:0.95~1.45%,mo:0.65~1.25%,ni:0.30~0.85%,v:0.01~0.20%,nb:0.01~0.08%,ca:0.0015~0.0050%,al:0.010~0.060%,ti≤0.02%,b≤0.0005%等,其余为铁,并采用轧后空冷至室温,然后进行离线热处理的工艺路径。该专利技术在定径后采用空冷的方法进行冷却,在轧态组织相变中缺乏有效调控,导致组织粗化,并且无法将nb元素及其复合析出相的强化效果充分发挥,在最终组织细晶强化与析出强化方面受到限制。
技术实现要素:4.本发明的目的在于提供一种基于控制冷却的高强含nb石油套管及其制备方法,在管材领域引入控制冷却工艺,并结合特殊的成分设计,针对轧态组织进行调控,进而改善最终的微观组织,更加充分发挥nb等合金元素作用,全面提升力学性能,满足深井/超深井对石油套管提出的强韧性要求。
5.为达到上述目的,本发明主要提供如下石油套管及其制备技术方案:
6.本发明提供的一种基于控制冷却的高强含nb石油套管,其化学元素质量百分比含量(%)为:c:0.15~0.25;si:0.26~0.30;mn:0.7~1.8;cr:0.2~0.8;mo:0.3~0.8;nb:0.03~0.08;其余为fe和其他不可避免的杂质;并且同时满足关系式(1):([mo]
1.6-8.5[nb])2<0.012和关系式(2):0.015<[nb]
×
([c]+[mn]/6+[cr]/5)<0.03。
[0007]
本发明提供的高强含铌石油套管钢中50~95wt.%的nb元素以碳氮化物的形式存在,即nb(c,n),其余的nb以固溶状态存在;并且nb(c,n)颗粒的平均尺寸为5~25nm,nb(c,n)颗粒的平均间距为20~100nm;在所有nb(c,n)颗粒中,按颗粒数量计,5~50%的nb(c,n)颗粒中还含有mo元素。
[0008]
同时,其微观组织为回火索氏体,平均有效晶粒尺寸为0.5~2.5μm,大角晶界(≥15
°
)即晶体取向角15
°
及以上的界面占比为21~39%。主要力学性能为屈服强度1180~1300mpa,抗拉强度1250~1450mpa,断后延伸率15~19%,0℃横向冲击功80~150j。
[0009]
上述基于控制冷却的高强含nb石油套管的制造方法,主要包括:
[0010]
冶炼,连铸得到铸坯;
[0011]
在炉内均热,穿孔;
[0012]
进行轧制;
[0013]
定径处理;
[0014]
进行控制冷却;
[0015]
进行离线热处理工艺。
[0016]
其中:
[0017]
在冶炼过程中根据钢管成分要求调整钢水成分,首先调整mo、nb元素含量达到mo:0.3~0.8%、nb:0.03~0.08%,并且满足关系式(1):([mo]
1.6-8.5[nb])2<0.012;然后调整c、si、mn、cr元素含量达到c:0.15~0.25%、si:0.26~0.30%、mn:0.7~1.8%、cr:0.2~0.8%,并且满足关系式(2):0.015<[nb]
×
([c]+[mn]/6+[cr]/5)<0.03。将成分合格的钢水浇铸成铸坯。
[0018]
在轧制成形过程中,将铸坯在1250~1300℃的炉内均热后,进行穿孔、轧管、定径,得到热轧后的钢管。其中,开轧温度为1150~1200℃,控制终轧温度为900~950℃,所得热轧后的钢管壁厚为8~16mm。
[0019]
热轧后的钢管进行控制冷却,平均冷却速度为20~60℃/s,控制冷却终止温度t为400~650℃,然后自然冷却至室温,得到控冷后的钢管。其中,在550℃≤t≤650℃的工艺范围内时,控制冷却采用连续冷却方式,即将钢管不间断地连续冷却至终止温度t;在400℃≤t<550℃时,控制冷却采用稀疏冷却方式,即将钢管通过水冷-空冷交替进行的方式冷却至终止温度t,每次水冷与空冷时间相等。
[0020]
经控制冷却后获得的钢管显微组织以贝氏体为主、铁素体+珠光体含量不超过10%,平均有效晶粒尺寸为3.0~9.5μm。
[0021]
将控制冷却后的钢管进行淬火加回火热处理:淬火加热温度为900~920℃,保温时间为40~60min;然后在540~600℃回火,保温时间为60~100min。
[0022]
本发明的设计原理:
[0023]
传统工艺下,钢管轧制后空冷至室温,冷却速度缓慢,奥氏体和析出物的长大未能有效得到抑制,导致过冷奥氏体及其相变组织和nb析出相的尺寸较大,最终钢的轧态组织及亚结构较为粗大;进一步的,由于组织的遗传性,在后续的淬火和回火处理后,得到的回火索氏体及其亚结构尺寸较大。细晶强化是目前唯一可以同时提高强度和韧性的强化机制,为此如何通过特殊的成分设计,并匹配适当的工艺路径,充分发挥元素作用及在线组织调控效果进行组织细化是关键。
[0024]
本发明引入控制冷却实现了轧后冷却路径的灵活控制。冷却速度的提高抑制了高温奥氏体和析出相的长大,同时降低相变温度,有利于获得细化的轧态组织,根据组织的遗传性,离线热处理后的所得最终组织相对细小。同时,进行了特殊的成分设计,一方面考虑了在控制冷却条件下nb等元素的析出相作用,高温轧制过程中,在位错、亚晶界、晶界上沉
淀析出铌的碳、氮化物,进一步与控制冷却相结合,使得无缝钢管高温轧制下可更有效的控制晶粒尺寸,同时还可降低冷却过程中nb的析出温度,获得更为弥散、细小的析出物;另一方面,还充分考虑了nb析出强化贡献与其它合金元素在热处理过程中固溶强化贡献的协同关系,通过“特殊成分设计—轧后控制冷却—热处理”全流程一体化设计实现最终产品性能的全面提升。特别的,针对控制冷却工艺,当终止冷却温度相对较低时,为防止内应力过大导致微裂纹产生,还提供了一种稀疏冷却工艺方法。
[0025]
与现有技术相比,本发明具有如下优点及有益效果
[0026]
(1)本发明提供的特殊成分设计,建立了nb析出强化贡献与其它合金元素在热处理过程中固溶强化贡献的协同关系,进一步与轧后控制冷却及热处理工艺相结合,可更为充分的发挥各元素的强化效果,在相对较低合金含量的条件下通过细晶、析出、相变的综合强化实现性能的全面提升。
[0027]
(2)针对控制冷却工艺,根据不同工艺参数的需要,提供了“连续冷却”和“稀疏冷却”的工艺方法,解决了高温钢材在线快速冷却过程中由于内应力过大而易于导致形成微裂纹的共性技术难题。
附图说明
[0028]
图1为本发明实施例1制备的石油套管最终组织形貌;
[0029]
图2为本发明实施例1制备的石油套管晶界分布图。
具体实施方式
[0030]
下面将根据具体实施例对本发明所述的基于控制冷却的高强含铌石油套管及其制造方法做出进一步说明。
[0031]
实施例1
[0032]
一种基于控制冷却的高强含铌石油套管,其化学元素质量百分比含量为:c:0.20%;si:0.30%;mn:0.78%;cr:0.22%;mo:0.78%;nb:0.071%;其余为fe和其他不可避免的杂质,满足关系式(1):([mo]
1.6-8.5[nb])2<0.012和关系式(2):0.015<[nb]
×
([c]+[mn]/6+[cr]/5)<0.03。
[0033]
上述基于控制冷却的高强含铌石油套管的制备方法,包括步骤如下:
[0034]
冶炼,连铸得到管坯;
[0035]
在炉内均热,穿孔,其加热温度为1300℃;
[0036]
进行轧制过程,其开轧温度为1200℃、终轧温度为950℃;
[0037]
定径,最终壁厚为10mm;
[0038]
进行控制冷却,冷却方式为连续冷却至550℃,然后空冷至室温,平均冷却速度约为53℃/s;
[0039]
进行离线热处理工艺,淬火加热温度为900℃,淬火保温时间为60min,回火的加热温度为540℃,回火保温时间为100min。
[0040]
本实施例1所制得石油套管屈服强度为1290mpa,抗拉强度1428mpa,0℃横向冲击功为89j,延伸率19%。
[0041]
参见图1,本实施例1制备得到的高强含nb石油套管的最终组织为回火索氏体。
[0042]
参见图2,本实施例1制备得到的高强含nb石油套管的微观组织中有效晶粒尺寸细小,其有效晶粒尺寸约为0.86μm-0.90μm,大角晶界占比约为30.7%-33%。
[0043]
实施例2
[0044]
一种基于控制冷却的高强含铌石油套管,其化学元素质量百分比含量同实施例1。
[0045]
上述基于控制冷却的高强含铌石油套管的制备方法,包括步骤如下:
[0046]
冶炼,连铸得到管坯;
[0047]
在炉内均热,穿孔,其加热温度为1280℃;
[0048]
进行轧制过程,其开轧温度为1180℃、终轧温度为945℃;
[0049]
定径,最终壁厚为8mm;
[0050]
进行控制冷却,冷却方式为连续冷却至650℃,然后空冷至室温,平均冷却速度约为44℃/s;
[0051]
进行离线热处理工艺,淬火加热温度为900℃,淬火保温时间为60min,回火的加热温度为540℃,回火保温时间为100min。
[0052]
本实施例2所制得石油套管屈服强度为1289mpa,抗拉强度1420mpa,0℃横向冲击功为95j,延伸率18%。
[0053]
实施例3
[0054]
一种基于控制冷却的高强含铌石油套管,其化学元素质量百分比含量同实施例1。
[0055]
上述基于控制冷却的高强含铌石油套管的制备方法,包括步骤如下:
[0056]
冶炼,连铸得到管坯;
[0057]
在炉内均热,穿孔,其加热温度为1260℃;
[0058]
进行轧制过程,其开轧温度为1160℃、终轧温度为920℃;
[0059]
定径,最终壁厚为13mm;
[0060]
进行控制冷却,冷却方式为稀疏冷却(冷却喷环间隔一个打开一个)至500℃,然后空冷至室温,平均冷却速度约为36℃/s;
[0061]
进行离线热处理工艺,淬火加热温度为900℃,淬火保温时间为60min,回火的加热温度为540℃,回火保温时间为100min。
[0062]
本实施例3所制得石油套管屈服强度为1283mpa,抗拉强度1438mpa,0℃横向冲击功为86j,延伸率19%。
[0063]
实施例4
[0064]
一种基于控制冷却的高强含铌石油套管,其化学元素质量百分比含量同实施例1。
[0065]
上述基于控制冷却的高强含铌石油套管的制备方法,包括步骤如下:
[0066]
冶炼,连铸得到管坯;
[0067]
在炉内均热,穿孔,其加热温度为1250℃;
[0068]
进行轧制过程,其开轧温度为1150℃、终轧温度为900℃;
[0069]
定径,最终壁厚为9mm;
[0070]
进行控制冷却,冷却方式为稀疏冷却(冷却喷环间隔两个打开两个)至400℃,然后空冷至室温,平均冷却速度约为27℃/s;
[0071]
进行离线热处理工艺,淬火加热温度为900℃,淬火保温时间为60min,回火的加热温度为540℃,回火保温时间为100min。
[0072]
本实施例4所制得石油套管屈服强度为1273mpa,抗拉强度1403mpa,0℃横向冲击功为94j,延伸率18%。
[0073]
实施例5
[0074]
一种基于控制冷却的高强含铌石油套管,其化学元素质量百分比含量为:c:0.15%;si:0.26%;mn:1.71%;cr:0.55%;mo:0.56%;nb:0.055%;其余为fe和其他不可避免的杂质,满足关系式(1):([mo]
1.6-8.5[nb])2<0.012和关系式(2):0.015<[nb]
×
([c]+[mn]/6+[cr]/5)<0.03。
[0075]
上述基于控制冷却的高强含铌石油套管的制备方法,包括步骤如下:
[0076]
冶炼,连铸得到管坯;
[0077]
在炉内均热,穿孔,其加热温度为1300℃;
[0078]
进行轧制过程,其开轧温度为1200℃、终轧温度为950℃;
[0079]
定径,最终壁厚为10mm;
[0080]
进行控制冷却,冷却方式为连续冷却至550℃,然后空冷至室温,平均冷却速度约为53℃/s;
[0081]
进行离线热处理工艺,淬火加热温度为910℃,淬火保温时间为50min,回火的加热温度为560℃,回火保温时间为80min。
[0082]
本实施例5所制得石油套管屈服强度为1244mpa,抗拉强度1357mpa,0℃横向冲击功为119j,延伸率19%。
[0083]
实施例6
[0084]
一种基于控制冷却的高强含铌石油套管,其化学元素质量百分比含量同实施例5。
[0085]
上述基于控制冷却的高强含铌石油套管的制备方法,包括步骤如下:
[0086]
冶炼,连铸得到管坯;
[0087]
在炉内均热,穿孔,其加热温度为1280℃;
[0088]
进行轧制过程,开轧温度为1180℃、终轧温度为945℃;
[0089]
定径,最终壁厚为8mm;
[0090]
进行控制冷却,冷却方式为连续冷却至650℃,然后空冷至室温,平均冷却速度约为44℃/s;
[0091]
进行离线热处理工艺,淬火加热温度为910℃,淬火保温时间为50min,回火的加热温度为560℃,回火保温时间为80min。
[0092]
本实施例6所制得石油套管屈服强度为1238mpa,抗拉强度1344mpa,0℃横向冲击功为112j,延伸率17%。
[0093]
实施例7
[0094]
一种基于控制冷却的高强含铌石油套管,其化学元素质量百分比含量同实施例5。
[0095]
上述基于控制冷却的高强含铌石油套管的制备方法,包括步骤如下:
[0096]
冶炼,连铸得到管坯;
[0097]
在炉内均热,穿孔,其加热温度为1260℃;
[0098]
进行轧制过程,其开轧温度为1160℃、终轧温度为920℃;
[0099]
定径,最终壁厚为13mm;
[0100]
进行控制冷却,冷却方式为稀疏冷却(冷却喷环间隔一个打开一个)至500℃,然后
空冷至室温,平均冷却速度约为36℃/s;
[0101]
进行离线热处理工艺,淬火加热温度为910,℃淬火保温时间为50min,回火的加热温度为560℃,回火保温时间为80min。
[0102]
本实施例7所制得石油套管屈服强度为1234mpa,抗拉强度1341mpa,0℃横向冲击功为115j,延伸率18%。
[0103]
实施例8
[0104]
一种基于控制冷却的高强含铌石油套管,其化学元素质量百分比含量同实施例5。
[0105]
上述基于控制冷却的高强含铌石油套管的制备方法,包括步骤如下:
[0106]
冶炼,连铸得到管坯;
[0107]
在炉内均热,穿孔,其加热温度为1250℃;
[0108]
进行轧制过程,其开轧温度为1150℃、终轧温度为900℃;
[0109]
定径,最终壁厚为9mm;
[0110]
进行控制冷却,冷却方式为稀疏冷却(冷却喷环间隔两个打开两个)至400℃,然后空冷至室温,平均冷却速度约为27℃/s;
[0111]
进行离线热处理工艺,淬火加热温度为910℃,淬火保温时间为50min,回火的加热温度为560℃,回火保温时间为80min。
[0112]
本实施例8所制得石油套管屈服强度为1238mpa,抗拉强度1348mpa,0℃横向冲击功为112j,延伸率17%。
[0113]
实施例9
[0114]
一种基于控制冷却的高强含铌石油套管,其化学元素质量百分比含量为:c:0.25%;si:0.27%;mn:1.25%;cr:0.78%;mo:0.35%;nb:0.034%;其余为fe和其他不可避免的杂质,满足关系式(1):([mo]
1.6-8.5[nb])2<0.012和关系式(2):0.015<[nb]
×
([c]+[mn]/6+[cr]/5)<0.03。
[0115]
上述基于控制冷却的高强含铌石油套管的制备方法,包括步骤如下:
[0116]
冶炼,连铸得到管坯;
[0117]
在炉内均热,穿孔,其加热温度为1300℃;
[0118]
进行轧制过程,其开轧温度为1200℃、终轧温度为950℃;
[0119]
定径,最终壁厚为10mm;
[0120]
进行控制冷却,冷却方式为连续冷却至550℃,然后空冷至室温,平均冷却速度约为53℃/s;
[0121]
进行离线热处理工艺,淬火加热温度为920℃,淬火保温时间为40min,回火的加热温度为600℃,回火保温时间为60min。
[0122]
本实施例9所制得石油套管屈服强度为1186mpa,抗拉强度1253mpa,0℃横向冲击功为134j,延伸率18%。
[0123]
实施例10
[0124]
一种基于控制冷却的高强含铌石油套管,其化学元素质量百分比含量同实施例9。
[0125]
上述基于控制冷却的高强含铌石油套管的制备方法,包括步骤如下:
[0126]
冶炼,连铸得到管坯;
[0127]
在炉内均热,穿孔,其加热温度为1280℃;
[0128]
进行轧制过程,开轧温度为1180℃、终轧温度为945℃;
[0129]
定径,最终壁厚为8mm;
[0130]
进行控制冷却,冷却方式为连续冷却至650℃,然后空冷至室温,平均冷却速度约为44℃/s;
[0131]
进行离线热处理工艺,淬火加热温度为920℃,淬火保温时间为40min,回火的加热温度为600℃,回火保温时间为60min。
[0132]
本实施例10所制得石油套管屈服强度为1191mpa,抗拉强度1251mpa,0℃横向冲击功为131j,延伸率17%。
[0133]
实施例11
[0134]
一种基于控制冷却的高强含铌石油套管,其化学元素质量百分比含量同实施例9。
[0135]
上述基于控制冷却的高强含铌石油套管的制备方法,包括步骤如下:
[0136]
冶炼,连铸得到管坯;
[0137]
在炉内均热,穿孔,其加热温度为1260℃;
[0138]
进行轧制过程,其开轧温度为1160℃、终轧温度为920℃;
[0139]
定径,最终壁厚为13mm;
[0140]
进行控制冷却,冷却方式为稀疏冷却(冷却喷环间隔一个打开一个)至500℃,然后空冷至室温,平均冷却速度约为36℃/s;
[0141]
进行离线热处理工艺,淬火加热温度为920℃,淬火保温时间为40min,回火的加热温度为600℃,回火保温时间为60min。
[0142]
本实施例11所制得石油套管屈服强度为1193mpa,抗拉强度1250mpa,0℃横向冲击功为137j,延伸率17%。
[0143]
实施例12
[0144]
一种基于控制冷却的高强含铌石油套管,其化学元素质量百分比含量同实施例9。
[0145]
上述基于控制冷却的高强含铌石油套管的制备方法,包括步骤如下:
[0146]
冶炼,连铸得到管坯;
[0147]
在炉内均热,穿孔,其加热温度为1250℃;
[0148]
进行轧制过程,其开轧温度为1150℃、终轧温度为900℃;
[0149]
定径,最终壁厚为9mm;
[0150]
进行控制冷却,冷却方式为稀疏冷却(冷却喷环间隔两个打开两个)至400℃,然后空冷至室温,平均冷却速度约为27℃/s;
[0151]
进行离线热处理工艺,淬火加热温度为920℃,淬火保温时间为40min,回火的加热温度为600℃,回火保温时间为60min。
[0152]
本实施例12所制得石油套管屈服强度为1190mpa,抗拉强度1258mpa,0℃横向冲击功为141j,延伸率17%。
[0153]
实施例13
[0154]
一种基于控制冷却的高强含铌石油套管,其化学元素质量百分比含量为:c:0.20%;si:0.29%;mn:1.10%;cr:0.69%;mo:0.69%;nb:0.041%;其余为fe和其他不可避免的杂质。不满足关系式(1):([mo]
1.6-8.5[nb])2<0.012,满足关系式(2):0.015<[nb]
×
([c]+[mn]/6+[cr]/5)<0.03。
[0155]
上述基于控制冷却的高强含铌石油套管的制备方法,包括步骤如下:
[0156]
冶炼,连铸得到管坯;
[0157]
在炉内均热,穿孔,其加热温度为1270℃;
[0158]
进行轧制过程,其开轧温度为1170℃、终轧温度为930℃;
[0159]
定径,最终壁厚为14mm;
[0160]
进行控制冷却,冷却方式为连续冷却至600℃,然后空冷至室温,平均冷却速度约为54℃/s;
[0161]
进行离线热处理工艺,淬火加热温度为910℃,淬火保温时间为50min,回火的加热温度为580℃,回火保温时间为80min。
[0162]
本实施例13所制得石油套管屈服强度为1140mpa,抗拉强度1201mpa,0℃横向冲击功为99j,延伸率15%。
[0163]
实施例14
[0164]
一种基于控制冷却的高强含铌石油套管,其化学元素质量百分比含量同实施例13。
[0165]
上述基于控制冷却的高强含铌石油套管的制备方法,包括步骤如下:
[0166]
冶炼,连铸得到管坯;
[0167]
在炉内均热,穿孔,其加热温度为1290℃;
[0168]
进行轧制过程,其开轧温度为1190℃、终轧温度为940℃;
[0169]
定径,最终壁厚为12mm;
[0170]
进行控制冷却,冷却方式为稀疏冷却(冷却喷环间隔一个打开一个)至450℃,然后空冷至室温,平均冷却速度约为39℃/s;
[0171]
进行离线热处理工艺,淬火加热温度为910,℃淬火保温时间为50min,回火的加热温度为580,℃回火保温时间为80min。
[0172]
本实施例14所制得石油套管屈服强度为1136mpa,抗拉强度1197mpa,0℃横向冲击功为102j,延伸率15%。
[0173]
实施例15
[0174]
一种基于控制冷却的高强含铌石油套管,其化学元素质量百分比含量为:c:0.15%;si:0.28%;mn:1.50%;cr:0.44%;mo:0.64%;nb:0.065%;其余为fe和其他不可避免的杂质。满足关系式(1):([mo]
1.6-8.5[nb])2<0.012,不满足关系式(2):0.015<[nb]
×
([c]+[mn]/6+[cr]/5)<0.03。
[0175]
上述基于控制冷却的高强含铌石油套管的制备方法,包括步骤如下:
[0176]
冶炼,连铸得到管坯;
[0177]
在炉内均热,穿孔,其加热温度为1270℃;
[0178]
进行轧制过程,其开轧温度为1170℃、终轧温度为930℃;
[0179]
定径,最终壁厚为14mm;
[0180]
进行控制冷却,冷却方式为连续冷却至600℃,然后空冷至室温,冷却速度为54℃/s;
[0181]
进行离线热处理工艺,淬火加热温度为910℃,淬火保温时间为50min,回火的加热温度为580℃,回火保温时间为80min。
[0182]
本实施例15所制得石油套管屈服强度为1136mpa,抗拉强度1199mpa,0℃横向冲击功为104j,延伸率16%。
[0183]
实施例16
[0184]
一种基于控制冷却的高强含铌石油套管,其化学元素质量百分比含量同实施例15。
[0185]
上述基于控制冷却的高强含铌石油套管的制备方法,包括步骤如下:
[0186]
冶炼,连铸得到管坯;
[0187]
在炉内均热,穿孔,其加热温度为1290℃;
[0188]
进行轧制过程,其开轧温度为1190℃、终轧温度为940℃;
[0189]
定径,最终壁厚为12mm;
[0190]
进行控制冷却,冷却方式为稀疏冷却(冷却喷环间隔一个打开一个)至450℃,然后空冷至室温,冷却速度为39℃/s;
[0191]
进行离线热处理工艺,淬火加热温度为910℃,淬火保温时间为50min,回火的加热温度为580℃,回火保温时间为80min。
[0192]
本实施例16所制得石油套管屈服强度为1135mpa,抗拉强度1195mpa,0℃横向冲击功为105j,延伸率16%。
[0193]
上述实施例1-16中的制备过程工艺参数及制得产品的力学性能数据如下表1-4所示。表1中只体现元素c、si、mn、cr、mo、nb及其含量。
[0194]
表1化学元素质量百分比
ꢀꢀꢀꢀꢀꢀꢀꢀꢀꢀꢀꢀꢀꢀꢀꢀꢀꢀꢀ
单位:%
[0195][0196]
表2炉内均热温度、轧制温度及冷却方式
[0197]
[0198]
表3淬火及回火工艺参数
[0199][0200]
表4制得的石油套管力学性能
[0201]
编号rm/mpar
t0.2
/mpa冲击功/j延伸率/%实施例1142812908919实施例2142012899518实施例3143812838619实施例4140312739418实施例51357124411919实施例61344123811217实施例71341123411518实施例81348123811217实施例91253118613418实施例101251119113117实施例111250119313717实施例121258119014117实施例13120111409915实施例141197113610215实施例151199113610416实施例161195113510516
[0202]
。