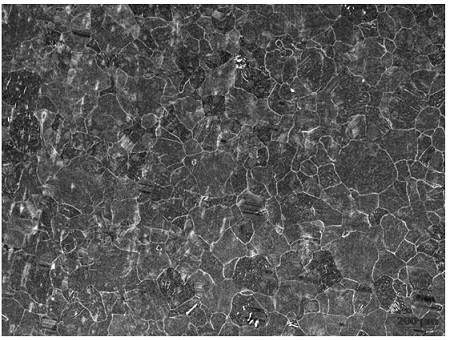
1.本发明涉及一种真空冶炼方法,尤其是一种高铝锰铜合金的真空冶炼方法。
背景技术:2.伴随着时代的快速发展,在装备制造领域零部件轻量化越来越受到科学家们的重视。al-cu-mn系列铸造合金作为一种高强度轻量化合金,由于具有良好的性能,在航空航天、船舶、机械等领域用作承受大载荷的结构件和耐热零件。但是合金在冷却结晶过程中由于结晶温度区间较宽,流动性差等原因极易造成成分上的偏析甚至使铸锭产生缺陷。同时,在铸造过程中,由于内部铸锭各部位的冷却速率不一样,凝固时局部温度差异较大,也极易产生宏观偏析。偏析和缺陷的产生极大的限制了其广泛的应用。
3.为了减少偏析和缺陷,众多学者们做了大量的研究工作。例如在专利公开号cn106399883a中公开了一种消除al-cu-mg-si-mn合金铸造结晶相的均匀化热处理工艺;在专利公开号cn110284086a中公开了一种消除铸造铝铜锰合金中结晶相偏析的方法。以上专利申请均是在热处理工艺方面进行的研究,但是关于直接从熔炼工艺来消除高铝锰铜合金成分偏析的研究相对较少。
技术实现要素:4.本发明要解决的技术问题是提供一种能有效解决成分偏析的高铝锰铜合金的真空冶炼方法。
5.为解决上述技术问题,本发明所采取的方法步骤为:(1)将铜、镍、钴放入感应熔炼炉的坩埚中;(2)将感应熔炼炉抽真空后给电升温;所述入炉料开始熔化时,感应熔炼炉内充入氩气进行保护;(3)所述入炉料熔清后,降低功率并加入部分铝粒;所述铝粒熔化并在液面形成薄膜,随后加入电解锰;待电解锰熔清后,加入剩余铝粒;直至全部熔清;(4)将熔清料浇铸至水冷锭模内,并随炉冷却。
6.本发明所述步骤(2)中,给电升温时功率升至额定功率的40%~45%。
7.本发明所述步骤(3)中,降低功率并加入铝粒总重4%~6%的铝粒。
8.本发明所述步骤(3)中,降低功率至额定功率的26%~32%。
9.本发明所述步骤(3)中,在1280~1350℃分批次加入电解锰。
10.本发明所述步骤(3)中,降温至1100~1150℃加入剩余铝粒。
11.本发明所述步骤(4)中,升温至1180~1250℃分批次浇铸至水冷锭模内。
12.本发明所述浇铸过程中,出钢时间累计到18~22s时,停止出钢并停顿2~4s,调低功率;然后继续出钢,出钢时间累计到40~44s时,停止出钢并停顿2~4s,调低功率;随后出钢至结束。
13.采用上述技术方案所产生的有益效果在于:本发明加料前降低功率来保正液面平
稳,预加入的铝粒会在钢液面形成一层保护膜,利用
ꢀ“
结膜法”即表面形成渣膜来减少冷炉料与高温钢液的直接接触,减少电解锰、金属铜及铝粒的氧化和烧损,并阻止钢液和气体的接触从而使得钢液洁净度和合金收得率大大提高;本发明利用“结膜法”可以精准控制合金成分,同时水冷锭模的使用避免合金铸锭发生成分偏析和质量缺陷问题,从而提高该合金的机械加工性能;本发明在保护气氛条件下,降低了感应炉内氧分压从而减少了炉料的氧化与氧化渣的形成,提高了合金的洁净度和整体的性能;本发明生产工艺简单,适应性广,有利于大规模生产。
14.本发明通过对钢液的搅拌及对钢液温度和浇铸次数的控制,可以使得铸锭内部成分均匀减少偏析,同时还可以显著降低铸锭内部的缩孔,使得成品率大大提高。
附图说明
15.下面结合附图和具体实施方式对本发明作进一步详细的说明。
16.图1是本发明实施例1所得高铝锰铜合金的金相组织图。
具体实施方式
17.本高铝锰铜合金的真空冶炼方法包括装料阶段、熔化阶段、加料阶段和浇铸阶段;各阶段工艺如下所述:(1)装料阶段:根据高铝锰铜合金的目标成分来计算各原料所需质量,并对所有原料进行表面打磨和高温烘干处理。随后将铜块装入感应熔炼炉的坩埚底部,镍、钴置于铜块上方。所用铜为紫铜、锰为电解锰、镍为电解镍,纯铝粒及纯金属钴,所用锰、镍、钴、铝、铜均为纯度>99%的纯料。所述坩埚采用质量纯度大于97%的氧化铝制坩埚。
18.所述高铝锰铜合金的目标成分的质量分数含量为:cu 75%~80%、al 6.5%~9.5%、mn 9%~12%、co 0.5%~0.7%、ni 1.8%~2%,余量为不可避免的杂质。
19.(2)熔化阶段:启动真空抽气系统,将感应熔炼炉的熔炼室真空度降至50pa及以内,送电升温,初始功率为额定功率的8%~12%,每间隔15~20min功率增加额定功率的8%~12%,功率达到额定功率的40%~45%时保持不变。待坩埚内的入炉料开始熔化时,停止抽真空并充入氩气至0.05~0.06mpa作为保护气,直至入炉料熔清。
20.(3)加料阶段:待入炉料熔清后将功率由额定功率的40%~45%降至额定功率的26%~32%,并加入铝粒总重4%~6%的铝粒,熔化的铝粒会在液面形成一层薄膜。保持功率待温度降至1280~1350℃时,分批次加入电解锰,待电解锰熔清后将功率调至额定功率的18%~25%,待温度降至1100~1150℃,将剩余铝粒加入其中至熔清。
21.(4)浇铸阶段:浇铸前将功率升至额定功率的36%~38%,升温并搅拌2~4min,利用坩埚外感应线圈自有的“驼峰效应”将液面表面渣膜推向边缘散去;待温度升高至1180~1280℃,开始带电匀速分批次出钢,以减少铸锭内部缩孔;所述出钢过程中,出钢时开始计时,出钢量达到总装入量的30%~35%,停止出钢并停顿2~4s,将功率调至额定功率的26%~30%;然后继续出钢,出钢量达到总装入量的60%~70%,停止出钢并停顿2~4s,将功率调至额定功率的16%~20%;随后出钢至结束,关闭电源;采用断续出钢法目的是减少铸锭内部缩孔和疏松,从而提高铸锭质量和减少成分偏析。所采用的锭模为水冷锭模,出钢前打开锭模水循环系统,出钢2h~3h后破空至常压,脱出锭模。
22.实施例1:本高铝锰铜合金的真空冶炼方法具体如下所述。
23.(1)采用50kg真空感应炉,额定功率100kw,极限真空度为6.67
×
10-2
pa。
24.结合钢种目标成分及装入量35kg计算并称取铜板27.3kg、电解镍0.728kg、电解锰3.885kg、金属钴0.182kg、铝粒2.905kg。将铜板、电解镍和金属钴放入坩埚中;120g铝粒放入料斗中,电解锰及剩余铝粒放置于加料仓内。
25.(2)盖上炉盖,开始抽真空待腔室内压力降至50pa时开始送电升温。初始功率为8kw,间隔20min升高8kw,待功率升高至40kw保持不变;待炉料开始熔化时停止抽真空充入氩气至0.05mpa,直至炉料熔清。
26.(3)待坩埚内部炉料熔清以后,调整功率至28kw,随后加入料斗内的铝粒。待温度降至1300℃,随后通过料仓向料斗补充电解锰合金料并分批次加入电解锰;待电解锰加入完成后调低功率至20kw;待温度降至1150℃,加入剩余所有铝粒,直至熔清。
27.(4)调高功率至38kw升温到1250℃,提前打开锭模水循环系统,待液面表面渣膜向边缘散去,开始带电匀速分阶段出钢;出钢量达到总装入量的30%,停止出钢并停顿3s,将功率调至28kw;然后继续出钢,出钢量达到总装入量的65%,停止出钢并停顿3s,将功率调至18kw;随后出钢至结束,关闭电源;待出钢完成,2h后破空至常压,脱出锭模。
28.(5)在距离铸锭底部1/5处切割,采用对角及中线处取屑。图1是本实施例所得高铝锰铜合金的金相组织图;由图可知,该合金金相组织分布均匀。利用icp检测方法测定各元素含量,结果见表1。
29.表1:实施例1所得铸锭成分(wt%)表1中,余量为不可避免的杂质。由表1可见,本方法减少了电解锰、金属铜及铝粒的氧化和烧损,所得合金的成分与目标成分相比更为精准。
30.实施例2:本高铝锰铜合金的真空冶炼方法具体如下所述。
31.(1)采用500kg真空感应炉,额定功率360kw,极限真空度6.67
×
10-2
pa。
32.结合钢种目标成分及装入量400kg计算并称取铜板304kg、电解镍7.2kg、电解锰48kg、金属钴2.4kg、铝粒38kg。将铜板、电解镍和金属钴放入坩埚中,铝粒跟电解锰分别放入加料仓中。
33.(2)抽真空待腔室内压力降至20pa时开始送电升温。初始功率为40kw,每间隔20min升高40kw,功率升至160kw时保持不变;待铜板开始熔化时停止抽真空充入氩气至0.06mpa,直至炉料熔清。
34.(3)待坩埚内炉料全部熔清以后,调整功率至110kw,随后加入2000g铝粒。待温度降至1300℃,随后通过将料仓内的电解锰分批次加入其中,待电解锰加入完成后调低功率至90kw,待温度降至1140℃,并加入剩余所有铝粒,加入完成后保持2min。
35.(4)调高功率至130kw,待温度升至1250℃,提前打开锭模水循环系统,待液面表面渣膜向边缘散去,开始带电匀速分阶段出钢;出钢量达到总装入量的35%,停止出钢并停顿
3s,将功率调至108kw;然后继续出钢,出钢量达到总装入量的60%,停止出钢并停顿4s,将功率调至65kw;随后出钢至结束,关闭电源;待出钢完成,2.5h后破空至常压,脱出锭模。
36.(5)在距离铸锭底部1/5处切割,采用对角及中线处取屑。利用icp检测方法测定各元素含量,结果见表2。
37.表2:实施例2所得铸锭成分(wt%)表2中,余量为不可避免的杂质。由表2可见,本方法减少了电解锰、金属铜及铝粒的氧化和烧损,所得合金的成分与目标成分相比更为精准。
38.实施例3:本高铝锰铜合金的真空冶炼方法具体如下所述。
39.(1)采用50kg真空感应炉,额定功率100kw,极限真空度为6.67
×
10-2
pa。
40.按目标成分及装入量35kg计算并称取铜板27.965kg、电解镍0.665kg、电解锰3.15kg、金属钴0.245kg、铝粒2.975kg。将铜板、电解镍和金属钴放入坩埚中。将150g铝粒放入料斗中,电解锰及剩余铝粒放置于加料仓内。
41.(2)抽真空待腔室内压力降至50pa时开始送电升温。初始功率为8kw,间隔20min升高10kw待功率升高至40kw保持不变,待炉料开始熔化时停止抽真空充入氩气至0.05mpa,直至炉料熔清。
42.(3)待坩埚内炉料熔清以后,调整功率至28kw,随后加入料斗内的铝粒。待温度降至1330℃,随后通过料仓向料斗补充电解锰合金料并分批次加入电解锰,待电解锰加入完成后调低功率至18kw,待温度降至1150℃,并加入剩余所有铝粒,直至熔清。
43.(4)调高功率至38kw升温至1240℃,提前打开锭模水循环系统,待液面表面渣膜向边缘散去,开始带电匀速分阶段出钢;出钢量达到总装入量的32%,停止出钢并停顿4s,将功率调至26kw;然后继续出钢,出钢量达到总装入量的65%,停止出钢并停顿2s,将功率调至16kw;随后出钢至结束,关闭电源;待出钢完成,2h后破空至常压,脱出锭模。
44.(5)在距离铸锭底部1/5处切割,采用对角及中线处取屑。利用icp检测方法测定各元素含量,结果见表3。
45.表3:实施例3所得铸锭成分(wt%)表3中,余量为不可避免的杂质。由表3可见,本方法减少了电解锰、金属铜及铝粒的氧化和烧损,所得合金的成分与目标成分相比更为精准。
46.实施例4:本高铝锰铜合金的真空冶炼方法具体如下所述。
47.(1)采用50kg真空感应炉,额定功率100kw,极限真空度为6.67
×
10-2
pa。
48.按下述表4所述目标成分及装入量35kg计算并称取铜板、电解镍、电解锰、金属钴
和铝粒。将铜板、电解镍和金属钴放入坩埚中。将4%的铝粒放入料斗中,电解锰及剩余铝粒放置于加料仓内。
49.(2)抽真空待腔室内压力降至40pa时开始送电升温。初始功率为12kw,间隔18min升高12kw待功率升高至45kw保持不变,待炉料开始熔化时停止抽真空充入氩气至0.05mpa,直至炉料熔清。
50.(3)待坩埚内炉料熔清以后,调整功率至32kw,随后加入料斗内的铝粒。待温度降至1280℃,随后通过料仓向料斗补充电解锰合金料并分批次加入电解锰,待电解锰加入完成后调低功率至22kw,待温度降至1130℃,并加入剩余所有铝粒,直至熔清。
51.(4)调高功率至36kw升温至1180℃,提前打开锭模水循环系统,待液面表面渣膜向边缘散去,开始带电匀速分阶段出钢;出钢量达到总装入量的30%,停止出钢并停顿2s,将功率调至27kw;然后继续出钢,出钢量达到总装入量的70%,停止出钢并停顿3s,将功率调至17kw;随后出钢至结束,关闭电源;待出钢完成,3h后破空至常压,脱出锭模。
52.(5)在距离铸锭底部1/5处切割,采用对角及中线处取屑。利用icp检测方法测定各元素含量,结果见表4。
53.表4:实施例4所得铸锭成分(wt%)表4中,余量为不可避免的杂质。由表4可见,本方法减少了电解锰、金属铜及铝粒的氧化和烧损,所得合金的成分与目标成分相比更为精准。
54.实施例5:本高铝锰铜合金的真空冶炼方法具体如下所述。
55.(1)采用500kg真空感应炉,额定功率360kw,极限真空度6.67
×
10-2
pa。
56.结合下述表5所述钢种目标成分及装入量400kg计算并称取铜板、电解镍、电解锰、金属钴和铝粒。将铜板、电解镍和金属钴放入坩埚中,铝粒跟电解锰分别放入加料仓中。
57.(2)抽真空待腔室内压力降至30pa时开始送电升温。初始功率为36kw,每间隔15min升高40kw,功率升至150kw时保持不变;待铜板开始熔化时停止抽真空充入氩气至0.06mpa,直至炉料熔清。
58.(3)待坩埚内炉料全部熔清以后,调整功率至93.6kw,随后加入6%的铝粒。待温度降至1350℃,随后通过将料仓内的电解锰分批次加入其中,待电解锰加入完成后调低功率至75kw,待温度降至1100℃,并加入剩余所有铝粒,加入完成后保持2min。
59.(4)调高功率至133kw,待温度升至1280℃,提前打开锭模水循环系统,待液面表面渣膜向边缘散去,开始带电匀速分阶段出钢;出钢量达到总装入量的33%,停止出钢并停顿3s,将功率调至97kw;然后继续出钢,出钢量达到总装入量的60%,停止出钢并停顿3s,将功率调至72kw;随后出钢至结束,关闭电源;待出钢完成,2.5h后破空至常压,脱出锭模。
60.(5)在距离铸锭底部1/5处切割,采用对角及中线处取屑。利用icp检测方法测定各元素含量,结果见表5。
61.表5:实施例5所得铸锭成分(wt%)
表5中,余量为不可避免的杂质。由表5可见,本方法减少了电解锰、金属铜及铝粒的氧化和烧损,所得合金的成分与目标成分相比更为精准。