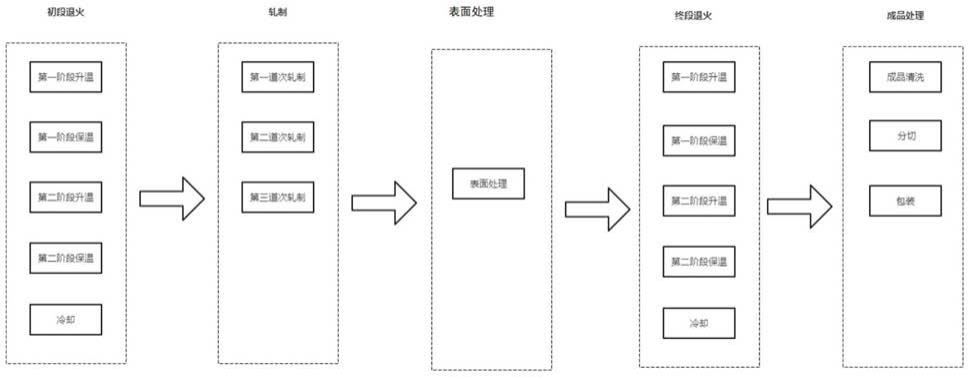
1.本发明涉及铜箔生产技术领域,具体涉及一种高挠曲铜箔及其生产方法。
背景技术:2.铜材作为助推科技进步的一大强有力的基础金属材料,被广泛应用在各大工业领域内。随着工业技术不断进步,电子产品的革新,市场对于铜材的需求扩张,铜材的消耗量占比不断提升的同时,科技的进步对于铜带的要求也越来越高。
3.具有高挠曲的压延铜箔作为一种功能材料应用在电子电力等相关工业领域,进行量产高挠曲压延铜箔能够有效解决市场对于该种铜箔的要求,辅助高端科技的研发。
4.目前高挠曲压延铜箔的产量以及性能满足不了市场的需求,现有技术工艺生产流程较长,产品性能与技术发展所需不适配,产量较低。水平连铸的紫铜中存在部分不可避免的微量元素,紫铜因其晶格结构的以及元素固溶的方式不同,形成的固溶作用对铜箔的性能产生影响。
技术实现要素:5.本发明的目的在于提供一种高挠曲铜箔及其生产方法,通过改变工艺流程以及轧制工艺、改进退火工序,获得质量更高的高挠曲性压延铜箔,提升产品的性能。
6.本发明具体技术方案如下:
7.一种高挠曲铜箔的生产方法,包括以下步骤:
8.1)初段退火;
9.2)轧制;
10.3)终段退火。
11.步骤1)具体为:将厚度0.15mm-0.20mm的硬态铜带放入钟罩式光亮退火炉中,进行抽真空,充入保护气进行初段退火。保护气体在初段退火中全程通入,保证铜箔不发生氧化。
12.步骤1)所述保护气为氮气,纯度为99.999%。
13.步骤1)所述初段退火包括以下步骤:
14.1-1)第一升温阶段;
15.1-2)第一保温阶段;
16.1-3)第二升温阶段:
17.1-4)第二保温阶段;
18.1-5)冷却。
19.步骤1-1)所述第一升温阶段具体为:第一阶段从室温进行升温至220
±
5℃,升温时间1-1.5小时;
20.步骤1-2)所述第一保温阶段具体为:在220
±
5℃的条件下保温时间3小时;
21.步骤1-3)所述第二升温阶段具体为:在220
±
5℃升温1-1.5小时至480
±
5℃;
22.步骤1-4)所述第二保温阶段具体为:在480
±
5℃的条件下进行保温12-15小时;
23.步骤1-5)所述冷却具体为:风冷至100℃切换水冷,降低温度为60-65℃出炉;
24.步骤2)所述轧制具体为:在六辊轧机进行精轧,精轧3道次,第一道次加工率30%-40%,第二道次加工率为20%-30%,第三道次加工率22%-27%;
25.步骤2)轧制后进行表面处理,具体为:进行表面脱脂处理。
26.铜带进行表面处理后再进行终段退火工艺。
27.步骤3)所述的终段退火具体为:将脱脂处理后的铜带放入钟罩式光亮退火炉,使用抽真空装置保证退火炉中的真空状态,在有保护气氛的条件下进行终段退火;保护气体在初段退火中全程通入,保证铜箔不发生氧化。
28.步骤3)所述保护气为氮气,纯度为99.999%。
29.步骤3)所述终段退火包括以下步骤:
30.3-1)第一升温阶段;
31.3-2)第一保温阶段;
32.3-3)第二升温阶段:
33.3-4)第二保温阶段;
34.3-5)冷却。
35.步骤3-1)所述第一升温阶段具体为:从室温升温至280
±
5℃,升温1.5小时;
36.步骤3-2)所述第一保温阶段具体为:在280℃
±
5℃的温度下进行保温2小时;
37.步骤3-3)所述第二升温阶段具体为:从280℃
±
5℃升温至340℃
±
5℃,升温时间0.5小时;
38.步骤3-4)所述第二升温阶段具体为:在340℃
±
5℃保温8小时;
39.步骤3-5)所述冷却具体为:风冷至100℃切换水冷,冷却至温度为40℃出炉。
40.步骤3)终段退火处理后,进行成品处理;
41.所述成品处理具体为:进行表面脱脂处理,清水清洗、钝化处理和挤干工艺,以去除铜带表面的油迹、氧化和残留物质;按照使用要求进行分切包装。
42.本发明提供的一种高挠曲铜箔,采用上述方法生产得到。所述高挠曲铜箔的厚度为0.022-0.050mm。
43.本发明生产工艺中,初段退火对于钟罩式光亮退火炉进行抽真空,之后充入保护气,在这个状态下进行升温之后进行保温,在保温结束之后进行风冷、水冷,冷却到60-65℃出炉;终段退火需要对钟罩式光亮退火炉进行抽真空,充入保护气,在这个氛围下进行终段退火。表面处理包括进行脱脂、清水清洗、钝化处理和挤干工艺用以去除铜带表面的油迹、氧化和残留物质。
44.本发明设计思路:改变压延轧制过程的参数和退火的工艺及参数对于铜箔的性能变化影响显著,控制生产流程中的参数,有助于获得质量更高的高挠曲性压延铜箔。本发明在设计技术方案时,改变加工工序,优化退火过程,实现内部晶粒细化,稳定铜箔的状态,晶粒在轧制过程变形,在退火阶段进行回复,在回复过程中晶粒长大,变形方向基本不变,织构的方向基本相同,再结晶行为发生择优取向,挠曲性更好。
45.采用以上技术方案后,本发明相对于传统高挠曲铜箔压延工艺主要有以下优点:
46.一、本发明在初段退火中使用分段退火,回复之后再结晶行为有效的细化晶粒,在
这个基础上进行轧制,轧制之后组织形貌发生变化,原有的晶粒组织改变,纤维状的组织出现,终段退火改变上一道工序中的晶粒大小,有效的提供能量,进行回复和再结晶行为,在这个过程中由于轧程的方向相同,纤维的流变方向基本一致,铜箔的挠曲性在晶粒和组织形貌上发生改变;
47.二、在轧制工序中通过控制三个道次的加工率,保证变形量和退火温度适配,在终段退火之后获得细小晶粒;减少一个道次的轧制,节省成本;
48.三、本发明工艺中退火过程中保护气体在升温阶段、保温阶段和冷却阶段全程通入,保证铜箔不发生氧化,设计初段退火和终段退火工艺,有利于内部组织均匀化,使不可避免的存在杂质元素发挥有益作用;
49.四、传统工艺生产36小时,本发明通过对生产工艺的优化,在满足原有带材性能要求下,减少了加工时间,缩短了加工流程,提高了生产效率。
附图说明
50.图1为本发明的高挠曲铜箔压延工艺的流程图。
具体实施方式
51.一种高挠曲铜箔的生产方法,包括以下步骤:
52.1)初段退火:
53.使用0.15
×
650mm(厚度
×
宽度)硬态铜带放入钟罩式光亮退火炉,进行初段退火处理,抽真空之后,在纯度为99.999%氮气的保护气氛中进行升温,升温过程中持续通入保护气体。初段退火具体包括以下步骤:
54.1-1)第一升温阶段:第一阶段从室温进行升温至220
±
5℃,升温时间1小时;
55.1-2)第一保温阶段:在220
±
5℃的条件下保温时间3小时;
56.1-3)第二升温阶段:在220
±
5℃升温1小时至480℃;
57.1-4)第二保温阶段:在480
±
5℃的条件下进行保温12小时;
58.1-5)冷却:风冷至100℃切换水冷;温度为60-65℃出炉;
59.步骤1)初段退火通过阶段式退火并进行冷却,使得成分更加均匀,消除上一道工序带来的内部缺陷,阶段式退火能够使得性能更加均一。
60.2)轧制:在六辊轧机进行精轧,精轧3个道次;第一道次加工率30%-40%,轧制厚度为0.09mm;第二道次加工率为25%-30%,轧制厚度为0.063mm;第三道次加工率22%-27%,轧制厚度为0.046mm。
61.3)表面处理;进行表面脱脂处理。
62.4)终段退火:将脱脂处理后的铜带放入钟罩式光亮退火炉,抽真空完成之后,充入纯度为99.999%氮气作为保护气体,在有保护气氛的条件下进行终段退火;具体终段退火包括以下步骤:
63.4-1)第一升温阶段:从室温升温至280
±
5℃,升温1.5小时;
64.4-2)第一保温阶段:在280℃
±
5℃的温度内进行保温2小时;
65.4-3)第二升温阶段:从280℃
±
5℃升温至340℃
±
5℃,升温时间0.5小时;
66.4-4)第二升温阶段:在340℃
±
5℃保温8小时;
67.4-5)冷却:风冷至100℃切换水冷,冷却至温度为40℃出炉。
68.5)成品处理:进行表面脱脂处理,清水清洗、钝化处理和挤干工艺,以去除铜带表面的油迹、氧化和残留物质;按照使用要求进行分切包装。产品挠曲性能相比之前的生产方式生产的提升15%,本发明挠曲次数大于11500次,本发明通过退火和轧制,晶粒改变,延伸性增加。
69.其中:初段退火对于钟罩式光亮退火炉进行抽真空,整个过程持续充入保护气体,在这个状态下进行第一阶段升温之后进行第一阶段保温,在第一阶段保温的基础上进行第二阶段升温,在第二阶段保温结束之后进行风冷、水冷,冷却到60-65℃出炉;终段退火,对于钟罩式光亮退火炉进行抽真空,然后充入保护气体,在这个状态下进行第一阶段的升温和保温,在第一阶段保温结束之后进行,继续升温,在第二阶段保温完成之后在进行降温风冷到100℃切换水冷,冷却到40℃出炉。