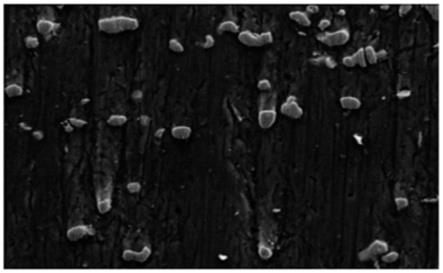
一种mn颗粒增强的mg-zn复合材料及其制备方法
技术领域
1.本发明涉及金属基复合材料领域,具体涉及mn颗粒增强的mg-zn复合材料及其制备方法。
背景技术:2.由于镁合金具有密度低,比强度、比刚度高、易于回收利用等优点,被誉为二十一世纪的绿色工程材料。发展高性能镁及镁合金材料,推动其大规模应用能实现二氧化碳减排,对实现“碳达峰、碳中和”的国家战略有着重要的意义。
3.锌元素可以溶入镁基体,造成晶格畸变,增大位错运动阻力,以及挤压过程中会大量析出的镁锌相,小尺寸镁锌相钉扎位错,抑制晶界迁移,大尺寸镁锌相可以作为动态再结晶形核点,协同作用促进动态再结晶晶粒细化,使得镁锌合金具有一定的强度、塑性。但是镁锌合金作为结构材料,其模量、刚度还不够高,限制了其应用。金属颗粒不仅具有高的强度还具有优异的塑性。发展金属颗粒增强的镁基复合材料是解决上述问题的有效途径之一。
4.由mg-mn二元相图可知,金属锰在镁中固溶度随温度的降低而急剧降低,600℃时,其固溶度达到2.0%;但室温条件下固溶度小于0.2%,表明锰能作为镁基复合材料的增强体。目前大量的研究认为含有微量锰元素的合金在挤压过程中动态析出的细小弥散的锰单质颗粒能显著细化mg-zn及mg-zn-re等体系合金的再结晶组织,此外,微量mn元素加入镁合金还具有非常好的去除杂质的效果,特别是对杂质fe,这能显著改善材料的性能。
5.目前,随着对镁合金的深入,镁合金室温力学性能已有很大的提升,毛建军于《杂质元素对镁合金组织与性能的影响及镁合金纯化工艺的研究》中对商用镁合金az31进行研究,发现该合金抗拉强度为277mpa,拉伸屈服强度为231mpa,延伸率为17%,有良好的工程应用前景。但是,此类常规商用镁合金中各相弹性模量都偏低,这导致合金模量一般在35.0~45.0gpa之间。由混合定律可知,多相合金的弹性模量是由其组成相的弹性模量及体积分数决定的。纯镁的弹性模量较低45.0gpa,镁合金的模量的提高可以通过添加高模量增强体来实现。王晓军于《microstructure and strengthening mechanism of carbon nanotubes reinforced magnesium matrix composite》研究了mg-6zn合金,发现该合金弹性模量仅40.0gpa;黄巍在《300℃等温处理时间对az91d压铸镁合金组织和性能的影响》中对铸态az91d进行研究,发现该合金弹性模量39.8gpa;张诗昌于《温度及应变率对挤压态az31镁合金弹性模量的影响》研究了az31镁合金,发现该合金弹性模量为43.8gpa;cn104342591a专利中表明,传统的mg-re镁合金中第二相的模量也很低,例如典型的mggd、mg3gd以及mg7gd模量为56.9gpa、46.1gpa与52.6gpa,mgy相的模量为55.7gpa,mg
24
y5相的模量53.8gpa,mgnd相的模量55.4gpa。因此,很难通过合金成分调控第二相的体积分数提高合金的模量,难以满足工程领域对高模量镁合金材料的需求。
6.袁秋红等于《碳纳米管增强镁基复合材料弹性模量的研究进展》公开了采用碳纳米管作为增强体,虽然大幅提升了镁基复合材料的弹性模量,但是整个工艺流程复杂,设备
要求高,增强体制备繁琐,成本高;需要同时控制搅拌速度和温度以及超声分散时间才能获得分布均匀的增强体;温度过高容易造成增强体碳化,搅拌速度低以及超声分散时间短会造成增强体团聚夹杂。
7.cn101020981公开了一种镁锌锰合金,其锰元素作为合金化元素添加到mg-zn合金中,含量低于2.0%。2.0%的锰能固溶在镁基体中,难以获得金属颗粒的增强体,并不属于复合材料的范畴。由mg-zn-mn相图可知,超过2.0%的锰能获得单相的锰颗粒。根据mg-zn-mn三元合金相图可知,在富mg端,其相组成为:α-mg、α-mn以及mg-zn相,具备形成单质α-mn相的条件。因此,高锰含量的mg-zn-mn体系是一种理想的金属颗粒增强的镁基复合材料体系。
技术实现要素:8.本发明的目的是提供一种金属mn颗粒增强的mg-zn复合材料及其制备方法,其能够在保证材料强度和塑性满足要求的前提下,提高材料的弹性模量,制备工艺简单,成本低。
9.本发明所述的mn颗粒增强的mg-zn复合材料,以mg-zn合金为基体,以mn为增强颗粒,复合材料按重量百分比计包括如下组分:2.5%~10.0%mn,1.0%~6.0%的zn,余量为mg和不可避免的杂质。
10.进一步,按重量百分比计包括如下组分:2.5%~10.0%mn,4.0%的zn,余量为mg和不可避免的杂质。
11.一种mn颗粒增强的mg-zn复合材料的制备方法,其包括如下步骤:
12.步骤一,按照上述的mn颗粒增强的mg-zn复合材料的组分重量百分比称取镁锭、锌粒和镁锰中间合金,所述镁锰中间合金中锰的重量百分比为3.0%~20.0%;
13.步骤二,对称取的镁锭、锌粒和镁锰中间合金进行熔炼得到熔体,将熔体直接冷却或浇铸得到铸锭;
14.步骤三,对铸锭进行热挤压得到mn颗粒增强的mg-zn复合材料的型材。
15.进一步,所述步骤二中的熔炼具体为:在保护气体环境中进行熔炼,先对镁锭在温度为720~740℃进行熔炼,镁锭全部融化后将温度调节至740℃,加入镁锰中间合金,最后加入锌粒,待原料全部融化后,充分搅拌3~6min,打掉表面浮渣,得到熔体。
16.进一步,所述保护气体为sf6和co2的混合气体。
17.进一步,所述步骤三中的热挤压具体为:去除铸锭表面的氧化层,再将铸锭在温度为250℃~450℃的条件下预热1~2h,表面涂覆润滑剂,使用挤压模具在温度为250℃~450℃的条件下对铸锭进行热挤压得到型材,挤压比为10:1~100:1,挤压速度为0.1~10.0m/min。
18.进一步,所述步骤二中当复合材料中mn的重量百分比≤5时,采用电阻炉或真空感应炉进行熔炼,当复合材料中mn的重量百分比>5时,采用真空感应炉进行熔炼。
19.本发明与现有技术相比具有如下有益效果。
20.1、本发明通过限定复合材料中mn的重量百分比为2.5%~10%,利用mn在镁中固溶度随温度降低急剧降低,使得复合材料具有更好的界面润湿性;以及mn在mg-zn-mn体系中以单质α-mn相存在的特点,保证了mn以颗粒的形式均匀分布于mg-zn基体合金中,以起到
强化的作用;并且这些均匀分布的α-mn相可以在动态再结晶过程中诱导形核以及钉扎再结晶晶界,阻碍再结晶晶粒长大,细化挤压过程中的再结晶晶粒,从而在保证材料强度和塑性满足要求的前提下,提高复合材料的弹性模量。
21.2、本发明限定了zn的重量百分比为1.0%~6.0%,锌含量过低会使得固溶强化效果以及镁锌相析出强化效果不好,导致合金材料强度低,同时不能细化镁基体晶粒尺寸,不能有效降低镁合金中有害杂质对镁合金性能高的影响;锌含量过高,会形成大量的带状组织,且在挤压变形过程中极易热裂。
22.3、本发明在进行熔炼时,先对镁锭进行熔炼,镁锭全部融化后再依次加入镁锰中间合金和锌粒,避免了锌粒因温度过高造成烧蚀,保证了铸锭质量。
23.4、本发明采用热挤压的方式将铸锭加工成型材,使得材料内部组织更均匀,提升了产品质量。
附图说明
24.图1是本发明实施例四所述的mn颗粒增强的mg-zn复合材料的sem图,放大倍数为500;
25.图2是本发明实施例四所述的mn颗粒增强的mg-zn复合材料的eds数据图。
具体实施方式
26.下面结合附图和具体实施例对本发明作详细说明。
27.实施例一,一种mn颗粒增强的mg-zn复合材料,以mg-zn合金为基体,以mn为增强颗粒,复合材料按重量百分比计包括如下组分:2.6%mn,4.0%的zn,余量为mg和不可避免的杂质。该复合材料的制备方法包括如下步骤:
28.步骤一,以镁锭、锌粒和mg-5.0mn中间合金作为原料,所述镁锭纯度在99.0%以上,锌粒纯度在99.5%以上,mg-5.0mn中间合金中锰的重量百分比为5.0%,按照上述组分重量百分比称取原料备用。
29.步骤二,在电阻炉中,先对镁锭和mg-5.0mn中间合金在温度为300℃的条件下预热30min,然后将镁锭在温度为740℃的条件下进行熔炼,并在通入co2和sf6混合气体保护下使其完全熔化得到镁熔体,将所述镁熔体温度上升到740℃稳定之后,加入预热的mg-5.0mn中间合金,然后加入锌粒,并强力搅拌5min,打掉熔体表面浮渣,得到纯净的镁基复合材料熔体,mn以单质颗粒的形式分布于镁基复合材料熔体中。将得到的熔体直接冷却得到铸锭。
30.步骤三,机械去除铸锭的表面氧化皮,再在温度为350℃的条件下预热2h,表面涂覆润滑剂,使用挤压模具在温度为350℃的条件下对铸锭进行热挤压得到棒材,挤压比为11:1,挤压速度为0.9~1.2m/min,得到mn颗粒增强的mg-zn复合材料的棒材。
31.对得到的棒材进行力学性能检测,抗拉强度为301mpa,拉伸屈服强度为192mpa,延伸率为12%,弹性模量44.9gpa,相较于对比例一mg-4zn合金,抗拉强度、拉伸屈服强度以及弹性模量提高了约20%、33%、1%,相较于对比例二mg-4zn-1.2mn合金,抗拉强度、拉伸屈服强度以及弹性模量提高了约3%、7%、1%,相较于商用镁合金az31,抗拉强度提高了约9%、拉伸屈服强度有所下降,弹性模量提高了约3%。
32.实施例二,一种mn颗粒增强的mg-zn复合材料,以mg-zn合金为基体,以mn为增强颗
粒,复合材料按重量百分比计包括如下组分:3.0%mn,4.0%的zn,余量为mg和不可避免的杂质。该复合材料的制备方法包括如下步骤:
33.步骤一,以镁锭、锌粒和mg-5.0mn中间合金作为原料,所述镁锭纯度在99.0%以上,锌粒纯度在99.5%以上,mg-5.0mn中间合金中锰的重量百分比为5.0%,按照上述组分重量百分比称取原料备用。
34.步骤二,在电阻炉中,先对镁锭和mg-5.0mn中间合金在温度为300℃的条件下预热30min,然后将镁锭在温度为740℃的条件下进行熔炼,并在通入co2和sf6混合气体保护下使其完全熔化得到镁熔体,将所述镁熔体温度上升到740℃稳定之后,加入预热的mg-5.0mn中间合金,然后加入锌粒,并强力搅拌5min,打掉熔体表面浮渣,得到纯净的镁基复合材料熔体,mn以单质颗粒的形式分布于镁基复合材料熔体中。将得到的熔体直接冷却得到铸锭。
35.步骤三,机械去除铸锭的表面氧化皮,再在温度为350℃的条件下预热2h,表面涂覆润滑剂,使用挤压模具在温度为350℃的条件下对铸锭进行热挤压得到棒材,挤压比为25:1,挤压速度为0.9~1.2m/min,得到mn颗粒增强的mg-zn复合材料的棒材。
36.对得到的棒材进行力学性能检测,抗拉强度为300mpa,拉伸屈服强度为205mpa,延伸率为24%,弹性模量44.9gpa,相较于对比例一mg-4zn合金,抗拉强度、拉伸屈服强度以及弹性模量提高了20%、42%、1%,相较于对比例二mg-4zn-1.2mn合金,抗拉强度、拉伸屈服强度以及弹性模量提高了约3%、14%、1%,相较于商用镁合金az31,抗拉强度提高了约8%、拉伸屈服强度有所下降,弹性模量提高了约3%。
37.实施例三,一种mn颗粒增强的mg-zn复合材料,以mg-zn合金为基体,以mn为增强颗粒,复合材料按重量百分比计包括如下组分:5.0%mn,4.0%的zn,余量为mg和不可避免的杂质。该复合材料的制备方法包括如下步骤:
38.步骤一,以镁锭、锌粒和mg-11.4mn中间合金作为原料,所述镁锭纯度在99.0%以上,锌粒纯度在99.5%以上,mg-11.4mn中间合金中锰的重量百分比为11.4%,按照上述组分重量百分比称取原料备用。
39.步骤二,在电阻炉中,先对镁锭和mg-11.4mn中间合金在温度为300℃的条件下预热30min,然后将镁锭在温度为740℃的条件下进行熔炼,并在通入co2和sf6混合气体保护下使其完全熔化得到镁熔体,将所述镁熔体温度上升到740℃稳定之后,加入预热的mg-11.4mn中间合金,然后加入锌粒,并强力搅拌5min,打掉熔体表面浮渣,得到纯净的镁基复合材料熔体,mn以单质颗粒的形式分布于镁基复合材料熔体中。将得到的熔体直接冷却得到铸锭。
40.步骤三,机械去除铸锭的表面氧化皮,再在温度为350℃的条件下预热2h,表面涂覆润滑剂,使用挤压模具在温度为350℃的条件下对铸锭进行热挤压得到棒材,挤压比为25:1,挤压速度为0.9~1.2m/min,得到mn颗粒增强的mg-zn复合材料的棒材。
41.对得到的棒材进行力学性能检测,抗拉强度为319mpa,拉伸屈服强度为225mpa,延伸率为21%,弹性模量45.6gpa,相较于对比例一mg-4zn合金,抗拉强度、拉伸屈服强度以及弹性模量提高了27%、56%、2%,相较于对比例二mg-4zn-1.2mn合金,抗拉强度、拉伸屈服强度以及弹性模量提高了约10%、25%、3%,相较于商用镁合金az31,抗拉强度提高了约15%、拉伸屈服强度基本相当,弹性模量提高了约4%。
42.实施例四,一种mn颗粒增强的mg-zn复合材料,以mg-zn合金为基体,以mn为增强颗
粒,复合材料按重量百分比计量,包括如下组分:10.0%mn,4.0%的zn,余量为mg和不可避免的杂质。该复合材料的制备方法包括如下步骤:
43.步骤一,以镁锭、锌粒和mg-11.4mn中间合金作为原料,所述镁锭纯度在99.0%以上,锌粒纯度在99.5%以上,mg-11.4mn中间合金中锰的重量百分比为11.4%,按照上述组分重量百分比称取原料备用。
44.步骤二,在电阻炉中,先对镁锭和mg-11.4mn中间合金在温度为300℃的条件下预热30min,然后将镁锭在温度为740℃的条件下进行熔炼,并在通入co2和sf6混合气体保护下使其完全熔化得到镁熔体,将所述镁熔体温度上升到740℃稳定之后,加入预热的mg-11.4mn中间合金,然后加入锌粒,并强力搅拌5min,打掉熔体表面浮渣,得到纯净的镁基复合材料熔体,mn以单质颗粒的形式分布于镁基复合材料熔体中。将得到的熔体直接冷却得到铸锭。
45.步骤三,机械去除铸锭的表面氧化皮,再在温度为350℃的条件下预热2h,表面涂覆润滑剂,使用挤压模具在温度为350℃的条件下对铸锭进行热挤压得到棒材,挤压比为25:1,挤压速度为0.9~1.2m/min,得到mn颗粒增强的mg-zn复合材料的棒材。
46.对得到的棒材进行sem和eds分析,结果参见图1和图2,mn颗粒弥散分布于mg-zn基体中,符合金属颗粒增强的镁基复合材料微观组织特征。
47.对得到的棒材进行力学性能检测,抗拉强度为304mpa,拉伸屈服强度为216mpa,延伸率为16%,弹性模量48.2gpa,相较于对比例一mg-4zn合金,抗拉强度、拉伸屈服强度以及弹性模量提高了21%、50%、8%,相较于对比例二mg-4zn-1.2mn合金,抗拉强度、拉伸屈服强度以及弹性模量提高了约5%、20%、9%,相较于商用镁合金az31,抗拉强度提高了约10%、拉伸屈服强度略微下降,弹性模量提高了约10%。
48.对比例一,一种mg-4zn合金,合金按重量百分比计包括如下组分:4.0%的zn,余量为mg和不可避免的杂质。该合金的制备方法包括如下步骤:
49.步骤一,以镁锭,锌粒作为原料,所述镁锭纯度在99.0%以上,锌粒纯度在99.5%以上,按照上述组分重量百分比称取原料备用。
50.步骤二,在电阻炉中,先对镁锭在温度为300℃的条件下预热30min,然后将镁锭在温度为740℃的条件下进行熔炼,并在通入co2和sf6混合气体保护下使其完全熔化得到镁熔体,将所述镁熔体温度上升到740℃稳定之后,加入加入锌粒,并强力搅拌5min,打掉熔体表面浮渣,得到纯净的镁合金熔体。将得到的熔体直接冷却得到铸锭。
51.步骤三,机械去除铸锭的表面氧化皮,再在温度为350℃的条件下预热2h,表面涂覆润滑剂,使用挤压模具在温度为350℃的条件下对铸锭进行热挤压得到棒材,挤压比为25:1,挤压速度为0.9~1.2m/min,得到mg-zn合金的棒材。
52.对得到的棒材进行力学性能检测,抗拉强度为251mpa,拉伸屈服强度为144mpa,延伸率为24%,弹性模量44.5gpa。
53.对比例二,一种mg-4zn-1.2mn合金,合金按重量百分比计包括如下组分:1.2%mn,4.0%的zn,余量为mg和不可避免的杂质。该合金的制备方法包括如下步骤:
54.步骤一,以镁锭、锌粒和mg-5.0mn中间合金作为原料,所述镁锭纯度在99.0%以上,锌粒纯度在99.5%以上,mg-5.0mn中间合金中锰的重量百分比为5.0%,按照上述组分重量百分比称取原料备用。
55.步骤二,在电阻炉中,先对镁锭和mg-5.0mn中间合金在温度为300℃的条件下预热30min,然后将镁锭在温度为740℃的条件下进行熔炼,并在通入co2和sf6混合气体保护下使其完全熔化得到镁熔体,将所述镁熔体温度上升到740℃稳定之后,加入预热的mg-5.0mn中间合金,然后加入锌粒,并强力搅拌5min,打掉熔体表面浮渣,得到纯净的镁合金熔体。将得到的熔体直接冷却得到铸锭。
56.步骤三,机械去除铸锭的表面氧化皮,再在温度为350℃的条件下预热2h,表面涂覆润滑剂,使用挤压模具在温度为350℃的条件下对铸锭进行热挤压得到棒材,挤压比为25:1,挤压速度为0.9~1.2m/min,得到mg-4zn-1.2mn合金的棒材。
57.对得到的棒材进行力学性能检测,抗拉强度为291mpa,拉伸屈服强度为180mpa,延伸率为21%,弹性模量44.4gpa。
58.对四个实施例以及两个对比例中的增强体的体积分数以及弹性模量进行统计,结果参见表1。
59.表1增强体所占体积分数及复合材料的弹性模量
60.样品实施例一实施例二实施例三实施例四对比例一对比例二体积分数(%)0.60.71.22.500弹性模量(gpa)44.944.945.648.244.544.4
61.可以看出,随着锰含量的提高,增强体所占体积分数逐渐增加,弹性模量不断提升,当增强体的体积分数增加到2.5%时,弹性模量显著提高。从而展示出本发明提出的金属锰颗粒增强的镁基复合材料弹性模量好,能够满足工程应用中对高模量镁基复合材料的需求。
62.对四个实施例以及两个对比例的常规力学性能进行统计,结果参见表2。
63.样品实施例一实施例二实施例三实施例四对比例一对比例二拉伸屈服强度(mpa)192205225216144180抗拉强度(mpa)301300319304251291延伸率(%)122421162421
64.可以看出,随着锰含量的增加,在塑性保持的情况下,材料的强度有明显提升,进一步表明本发明提出的金属锰颗粒增强的镁基复合材料性能优异,能够满足对高强度低成本镁基复合材料的需求。