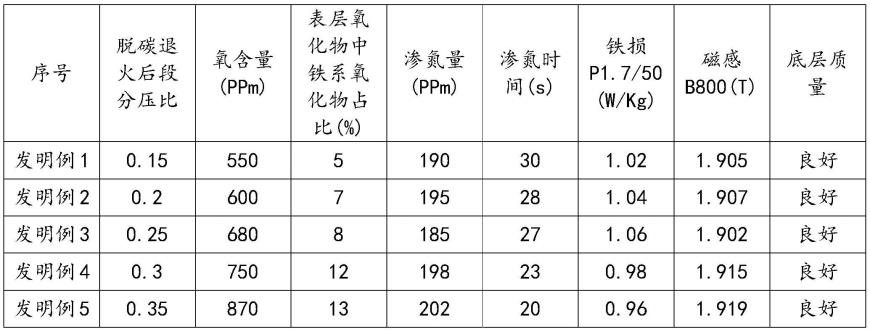
1.本技术涉及高磁感取向硅钢渗氮处理技术领域,具体而言,涉及一种提高高磁感取向硅钢渗氮效率的方法。
背景技术:2.高磁感取向硅钢由于具有低的铁损值,以及高的磁感值,因而主要应用于制造大型电力变压器、输配电变压器和节能配电变压器的铁芯材料。高磁感取向硅钢的制造技术目前主要有先天抑制剂法和后天抑制剂法。相对于前者,采用后天抑制剂法生产的高磁感取向硅钢由于具有高磁性、低成本的优势,从而其生产技术为当前广大取向硅钢生产厂家所青睐。采用后天抑制剂法生产高磁感取向硅钢的最重要的技术特点是作为发展二次再结晶所必需的aln颗粒第二相是通过脱碳后的渗氮进一步获得。因此,渗氮成为了采用这一技术生产高磁感取向硅钢产品必须经过的一道重要环节,其渗氮效果(渗氮总量、渗氮量的厚度分布及渗氮后形成的氮化物状况)对于成品质量有着至关重要的影响。生产实践表明,渗氮效率(s,同等单位氨气浓度下渗氮量一定时所需的时间)高低一定程度上影响了渗氮效果,从而对成品磁性能和底层质量产生影响,与此同时,渗氮效率的高低直接影响了产线的产能和生产成本。
3.现有对渗氮效率的提高,需要进行相应的设备改进,或者实现气氛的精细控制,或者是增加一定工序,这将造成生产成本上升,或者工艺控制难度增加,同时渗氮效率不理想。
技术实现要素:4.为了弥补以上不足,本技术提供了一种提高高磁感取向硅钢渗氮效率的方法,旨在改善高磁感取向硅钢渗氮效率不理想的问题。
5.本技术是这样实现的:本技术提供一种提高高磁感取向硅钢渗氮效率的方法,所述高磁感取向硅钢按重量百分比包括:si:2.8~3.4%、 c:0.040~0.070%、als:0.015~0.045%、mn:0.06~0.14%、s: 0.003~0.020%、n:0.003~0.010%、cu:0.01~0.025%、sn:0.03%~ 0.07%、cr及ni,cr和ni的总含量小于0.5%,其余为fe和不可避免杂质物;通过控制脱碳退火后钢带表层氧化物中铁系氧化物的比例。
6.在本技术的一种实施例中,所述表层氧化物中铁系氧化物比例: 5%-20%。
7.在本技术的一种实施例中,提高脱碳退火后钢板的氧含量,其中,所述氧含量:500ppm-1300ppm。
8.在本技术的一种实施例中,所述表层铁系氧化物主要组成为 fesio3、fe2sio4、feo和fe3o4中的一种氧化物或几种氧化物的混合物。
9.在本技术的一种实施例中,所述氧含量与所述表层氧化物中铁系氧化物所占比例成正比关系,随着所述氧含量的增加,所述表层氧化物中铁系氧化物所占比例随之增加。
10.在本技术的一种实施例中,所述氧含量调整主要通过改变脱碳退火后段保护气氛
的分压比来实现,其中,所述分压比:0.15-0.50。
11.本技术的有益效果是:本技术通过上述设计得到的一种提高高磁感取向硅钢渗氮效率的方法,使用时,通过增加脱碳退火后钢带表面氧化层中铁系氧化物占整个氧化层重量的比例,从而在获得同等渗氮量的情况下实现了快速渗氮,缩短渗氮时间,提高渗氮效率,同时获得了同样的成品磁性,并且产品底层质量良好。
具体实施方式
12.为使本技术实施方式的目的、技术方案和优点更加清楚,下面将对本技术实施方式中的技术方案进行清楚、完整地描述,显然,所描述的实施方式是本技术一部分实施方式,而不是全部的实施方式。基于本技术中的实施方式,本领域普通技术人员在没有作出创造性劳动前提下所获得的所有其他实施方式,都属于本技术保护的范围。
13.因此,以下提供本技术的实施方式的详细描述并非旨在限制要求保护的本技术的范围,而是仅仅表示本技术的选定实施方式。基于本技术中的实施方式,本领域普通技术人员在没有作出创造性劳动前提下所获得的所有其他实施方式,都属于本技术保护的范围。
14.在本技术的描述中,需要理解的是,术语“中心”、“纵向”、“横向”、“长度”、“宽度”、“厚度”、“上”、“下”、“前”、“后”、“左”、“右”、“竖直”、“水平”、“顶”、“底”、“内”、“外”、“顺时针”、“逆时针”等指示的方位或位置关系仅是为了便于描述本技术和简化描述,而不是指示或暗示所指的设备或元件必须具有特定的方位、以特定的方位构造和操作,因此不能理解为对本技术的限制。
15.此外,术语“第一”、“第二”仅用于描述目的,而不能理解为指示或暗示相对重要性或者隐含指明所指示的技术特征的数量。由此,限定有“第一”、“第二”的特征可以明示或者隐含地包括一个或者更多个该特征。在本技术的描述中,“多个”的含义是两个或两个以上,除非另有明确具体的限定。
16.在本技术中,除非另有明确的规定和限定,术语“安装”、“相连”、“连接”、“固定”等术语应做广义理解,例如,可以是固定连接,也可以是可拆卸连接,或成一体;可以是直接相连,也可以通过中间媒介间接相连,可以是两个元件内部的连通或两个元件的相互作用关系。对于本领域的普通技术人员而言,可以根据具体情况理解上述术语在本技术中的具体含义。
17.在本技术中,除非另有明确的规定和限定,第一特征在第二特征之“上”或之“下”可以包括第一和第二特征直接接触,也可以包括第一和第二特征不是直接接触而是通过它们之间的另外的特征接触。而且,第一特征在第二特征“之上”、“上方”和“上面”包括第一特征在第二特征正上方和斜上方,或仅仅表示第一特征水平高度高于第二特征。第一特征在第二特征“之下”、“下方”和“下面”包括第一特征在第二特征正下方和斜下方,或仅仅表示第一特征水平高度小于第二特征。
18.实施例
19.其实影响高磁感取向硅钢渗氮效率的因素很多,有脱碳后钢带的表面氧化层状况,有渗氮区域保护气体中的氨气浓度,有渗氮区域保护气体的组成,有渗氮区域保护气体的露点,有渗氮区域的温度,有渗氮区域保护气管道的构造等。查询相关专利可知,专利公开号 cn110438439a主要讲述了设计了一种新型装置,可以避免氨气在高温段过早分解导
致的渗氮效率下降,同时避免试样温度与渗氮炉内温度不匹配时导致的欠渗氮或过渗氮问题。专利公开号cn110055489a 主要讲述了按照某一特定的炼钢成分,通过调整渗氮区域的保护气体状况,可以提高渗氮效率,并且保持磁性能的稳定。专利公开号 cn106480281a主要讲述了依据不同的成品规格,控制不同的冷轧成品道次的表面光整度,可提高取向硅钢的渗氮效率。专利 ep0339474b1和cn102041440a主要讲述了通过脱碳退火板进一步还原,然后降低渗氮温度,从而提高渗氮效率。专利公开号 cn208485937主要讲述了通过设计新型氨气喷管结构,使得喷孔出气方向与带钢运行方向呈一定夹角,喷出的氨气与钢带的接触时间更长,提供了更多地氨气量,提高了氨气的使用效率和渗氮质量。
20.从上述专利内容来看,针对渗氮效率的提高,需要进行相应的设备改进,或者实现气氛的精细控制,或者是增加一定工序,这将造成生产成本上升,或者工艺控制难度增加。
21.针对上述不足,本技术提供一种技术方案:一种提高高磁感取向硅钢渗氮效率的方法,所述高磁感取向硅钢按重量百分比包括:si: 2.8~3.4%、c:0.040~0.070%、als:0.015~0.045%、mn:0.06~ 0.14%、s:0.003~0.020%、n:0.003~0.010%、cu:0.01~0.025%、 sn:0.03%~0.07%、cr及ni,cr和ni的总含量小于0.5%,其余为fe和不可避免杂质物;通过控制脱碳退火后钢带表层氧化物中铁系氧化物的比例,其中,脱碳退火板钢带表层氧化物主要组成为si 和fe系氧化物的混合物。具体的,表层铁系氧化物主要组成为 fesio3、fe2sio4、feo和fe3o4中的一种氧化物或几种氧化物的混合物,且该表层氧化物中铁系氧化物比例需控制在5%-20%之间。在具体设置时,需要说明的是,当表层氧化物中铁系氧化物比例低于 5%,渗氮效率显著降低,同时成品底层附着性差,高于20%时,渗氮效率明显,然而成品玻璃膜出现亮点,底层质量下降。
22.示例性的,通过提高脱碳退火后钢带表层氧化物中铁系氧化物的比例,增加了渗氮反应的触媒,加快了钢带的渗氮速度,缩短了渗氮时间,提升渗氮效率。在同等渗氮条件下,脱碳退火后钢带表层氧化物中铁系氧化物的比例由5%提高至20%,在获得150-250ppm同等渗氮量情况下,渗氮时间由40s缩短为15s,渗氮时间缩短了近三分之一,从而为进一步提升产线速度创造了条件,减少了能源消耗,降低了生产成本。
23.在一些具体的实施方案中,还需要控制脱碳退火后钢板的氧含量,其中,氧含量主要指脱碳退火后钢带表层氧化物中氧元素在钢板中所占的重量比例,且该氧含量的浓度需控制在500ppm-1300ppm范围之间。在具体设置时,需要说明的是,当氧含量低于500ppm,渗氮效率显著降低,同时成品底层附着性差,高于1300ppm,渗氮效率明显,然而成品玻璃膜出现亮点,底层质量下降。
24.可以理解,在上述实施例中,所述氧含量与所述表层氧化物中铁系氧化物所占比例成正比关系,随着所述氧含量的增加,所述表层氧化物中铁系氧化物所占比例随之增加。
25.在一些具体的实施方案中,氧含量调整主要通过改变脱碳退火后段保护气氛的分压比来实现,为保证这一氧含量数值,脱碳退火后段分压比应控制在0.15-0.50范围,分压比低于0.15,脱碳退火板的氧含量太低,降低了渗氮效率,分压比高于0.50,脱碳退火板的氧含量偏高,尽管提升了渗氮效率,然而底层质量出现问题。
26.通过上述实施例,热轧板经常化冷轧至0.26mm成品厚度,再经脱碳渗氮退火后,进行高温和拉伸退火。脱碳退火后段分压比、脱碳退火板氧含量和铁系氧化物占比、渗氮时间和渗氮量,以及对应成品的磁性和底层情况如下表1所示。其中,实施工艺中,1-8例为发明
例,9-10例为比较例。
27.表1:
[0028][0029][0030]
从表1可知,采用本专利提高脱碳退火后钢带表层氧化物中铁系氧化物占比的方法,可以在保证同等渗氮量情况下,缩短渗氮时间,提高渗氮效率,同时获得了同样的成品磁性,并且产品底层质量良好。
[0031]
具体的,该提高高磁感取向硅钢渗氮效率的方法的工作原理:通过改变脱碳退火后段保护气氛的分压比来调整脱碳退火板中氧含量的浓度,以及通过增加脱碳退火后钢带表层氧化物中铁系氧化物的比例,增加了渗氮反应的触媒,加快了钢带的渗氮速度,缩短了渗氮时间,提升渗氮效率。在同等渗氮条件下,脱碳退火后钢带表层氧化物中铁系氧化物的比例由5%提高至20%,在获得150-250ppm同等渗氮量情况下,渗氮时间由40s缩短为15s,渗氮时间缩短了近三分之一,从而为进一步提升产线速度创造了条件,减少了能源消耗,降低了生产成本。
[0032]
以上所述仅为本技术的优选实施方式而已,并不用于限制本技术,对于本领域的技术人员来说,本技术可以有各种更改和变化。凡在本技术的精神和原则之内,所作的任何修改、等同替换、改进等,均应包含在本技术的保护范围之内。