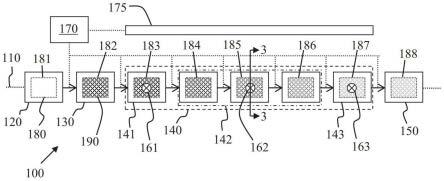
1.本发明的技术领域通常涉及用于铸造结构部件的方法和系统,其非限制性示例包括发动机缸体、气缸盖、诸如减震塔和控制臂的悬架部件、车轮和飞机门。特别地,提供了用于铸造这种结构部件的孔隙率降低的铝的方法和系统。
背景技术:2.铝铸件因其高强度重量比、良好的耐腐蚀性和相对较低的原材料成本而被广泛用于结构应用。尽管与其他制造方法相比具有成本竞争力,但与铝合金相关的铸造工艺会引入大量缺陷。
3.例如,在铸造过程中,当熔融铝冷却时,它可能收缩,导致在部件的部分内形成孔隙。铸件中的孔隙会显著降低材料的机械性能,尤其是疲劳性能。对于某些用途,多孔铸件可以通过填充孔隙来节省,通常通过使用昂贵的工艺。在其他使用中,铸件必须废弃。
4.有许多方法已经在实践中用于减少铝铸件中的铸造缺陷,例如用低压或电磁泵静态充型,用重金属冷却剂、金属模具或烧蚀工艺快速凝固,以及在凝固过程中加压,例如在高压模具压铸(high-pressure die casting,hpdc)和消失模铸造中。然而,在砂型铸造、半永久铸模铸造和永久铸模铸造工艺中,还没有使用有效的加压技术。
5.因此,希望提供适用于砂型铸造和金属型铸造工艺的方法和系统,用于连续生产铸件孔隙率降低且合金强度、疲劳性和耐腐蚀性提高的改进的铝铸件。此外,希望提供采用连续铸造工艺的这种方法和系统。此外,结合附图以及前述技术领域和背景技术,从随后的详细描述和所附权利要求中,本文实施例的其他期望特征和特性将变得显而易见。
技术实现要素:6.提供了一种连续生产铸造金属部件的方法。在一个实施例中,该方法包括在填充站将熔融金属供给到第一模具中;将加压室保持在升高的压力下;将第一模具移动到加压室中,其中熔融金属在升高的压力下在第一模具中固化;以及从加压室移除第一模具。
7.在示例性实施例中,该方法在铸造生产线中执行,并且加压室在铸造生产线中移动。
8.在示例性实施例中,加压室是固定的。
9.在示例性实施例中,该方法在旋转式铸造生产线(carousel casting line)中执行。
10.在示例性实施例中,升高的压力至少为2个大气压(atm)。
11.在示例性实施例中,该方法还包括用高传导性惰性气体填充加压室。
12.在示例性实施例中,加压室包括不同的部分,并且该方法包括在不同的部分中保持不同的气体介质。
13.在示例性实施例中,该方法还包括将第一模具从填充站移动到预加压室部分;密封预加压室部分;增加预加压室部分中的压力;打开加压室部分和预加压室部分之间的流
体连通;以及将第一模具从预加压室部分转移到加压室部分。在示例性实施例中,该方法还包括将压力释放室部分保持在升高的压力下;将第一模具从加压室部分转移到压力释放室部分;密封加压室部分;以及从压力释放室部分移除第一模具。此外,在示例性方法中,熔融金属在压力释放室部分中的升高的压力下在第一模具中固化。
14.在示例性实施例中,该方法在铸造生产线中执行,该铸造生产线依次包括模具组装站、填充站、预加压室部分、加压室部分、压力释放室部分和铸造/模具拆卸站。在这样的实施例中,该方法可以进一步包括在模具组装站组装第一模具;将第一模具移动到填充站,在那里熔融金属被供给到第一模具中,并且在模具组装站组装第二模具;将第一模具移动到预加压室部分,并将第二模具移动到填充站,在那里熔融金属被供给到第二模具中;密封预加压室部分并将预加压室部分中的压力增加到加压室部分的升高的压力;打开加压室部分和预加压室部分之间的流体连通,并将第一模具从预加压室部分转移到加压室部分;密封加压室部分;将第二模具移动到预加压室部分;密封预加压室部分并将预加压室部分中的压力增加到加压室部分的升高的压力;打开加压室部分和预加压室部分之间的流体连通,并将第二模具从预加压室部分转移到加压室部分;打开加压室部分和压力释放室部分之间的流体连通,并将第一模具从预加压室部分转移到压力释放室部分;将第一模具从压力释放室部分转移到铸造/模具拆卸站;密封压力释放室部分并将压力释放室部分中的压力增加到加压室部分的升高的压力;打开加压室部分和压力释放室部分之间的流体连通,并将第二模具从预加压室部分转移到压力释放室部分;在铸造/模具拆卸站拆卸第一模具和其中形成的第一铸件;将第二模具从压力释放室部分转移到铸造/模具拆卸站;以及在铸造/模具拆卸站拆卸第二模具和其中形成的第二铸件。
15.此外,提供了一种在线铸造系统。在一个实施例中,该系统包括用于组装模具的模具组装站;用于用熔融金属填充模具的填充站;加压站,用于在升高的压力下致密熔融和/或半固态金属;以及用于拆卸模具和其中形成的铸件的铸件/模具拆卸站。
16.在示例性实施例中,加压站包括预加压室部分、加压室部分和压力释放室部分。
17.在示例性实施例中,加压站包括预加压室部分、加压室部分和压力释放室部分,其中加压室部分处于恒定的、升高的压力。
18.在示例性实施例中,该系统还包括压力计和阀,以监测加压站中的压力,并选择性地向加压站添加介质。
19.在示例性实施例中,模具组装站、填充站、加压站和铸造/模具拆卸站布置在线性铸造生产线中。
20.在示例性实施例中,模具组装站、填充站、加压站和铸造/模具拆卸站布置在旋转式铸造生产线中。
21.在示例性实施例中,该系统还包括控制模块和传感器,其中传感器被布置成监控加压站的准备状态,并且其中当加压站准备好时,控制模块在填充站处引导填充模具。
22.在一个实施例中,在线铸造系统包括用于组装模具的模具组装站;用于用熔融金属填充模具的填充站;加压站,用于在升高的压力下致密熔融和/或半固态金属;高导热介质源,用于向加压站提供期望的介质;以及用于拆卸模具和其中形成的铸件的铸件/模具拆卸站。
23.提供该概述是为了以简化的形式介绍将在下面的详细描述中进一步描述的一些
概念。该概述不旨在标识所要求保护的主题的关键特征或必要特征,也不旨在用于帮助确定所要求保护的主题的范围。
附图说明
24.下文将结合以下附图描述示例性实施例,其中相同的附图标记表示相同的元件,并且其中:
25.图1是根据本文的实施例的用于在连续铸造过程中降低铸件孔隙率的在线铸造系统的示意图;
26.图2是根据本文的另一个实施例的用于在连续铸造过程中降低铸件孔隙率的在线铸造系统的示意图;
27.图3是沿着图1或2的系统的实施例的线3-3截取的剖视图;
28.图4是沿着图1或2的系统的另一个实施例的线3-3截取的剖视图;
29.图5是示出了根据本文的实施例的用于连续生产铸造金属部件的方法的流程图,该方法降低了连续铸造过程中的铸件孔隙率;和
30.图6是示出根据本文的另一实施例的用于连续生产铸造金属部件的方法的流程图,该方法减少了连续铸造过程中的铸件孔隙率。
具体实施方式
31.以下详细描述本质上仅仅是示例性的,并不旨在限制应用和使用。此外,不打算受前面的技术领域、背景、简要概述或下面的详细描述中呈现的任何明示或暗示的理论的约束。如这里所使用的,术语控制模块指的是专用集成电路(application specific integrated circuit,asic)、电子电路、处理器(共享的、专用的或成组的)和执行一个或多个软件或固件程序的存储器、组合逻辑电路和/或提供所述功能的其他合适的部件。
32.如这里所使用的,词语“示例性的”意味着“用作例子、实例或说明”。如本文所用,“一个”、“一”或“该”是指一个或多个,除非另有说明。术语“或”可以是连接的或分离的。诸如“包括”、“包含”、“具有”、“含有”等开放式术语表示“包含”。在某些实施例中,本说明书中指示数量、材料比例、材料物理性质和/或用途的数字可以理解为由单词“大约”修饰。结合数值和权利要求使用的术语“大约”表示本领域技术人员熟悉和可接受的精度区间。通常,这种精度区间为10%。除非另有明确说明,否则本说明书中指示数量、材料比例、材料物理性质和/或用途的所有数字都可以理解为由单词“大约”修饰。
33.如本文所用,除非另有说明,本公开中描述的“%”或“百分比”是指重量百分比。此外,如本文所用,被标识为“材料”的元素包括所述材料的至少50wt%。如本文所用,被标识为“主要材料”的元素是包括至少90wt%的所述材料。
34.此外,诸如“上”、“下”、“上方”、“在
……
上”、“下方”、“在
……
下”、“向上”、“向下”等术语用于描述附图,并不代表对由所附权利要求限定的主题范围的限制。诸如“第一”或“第二”的任何数字名称仅是说明性的,并不旨在以任何方式限制主题的范围。应当注意,尽管这里可以针对汽车应用描述实施例,但是本领域技术人员将认识到它们更广泛的适用性。
35.本文的实施例涉及用于在凝固期间使用在线加压室来减少铸件孔隙率的方法和
系统。金属铸件中的孔隙会显著降低材料的机械性能,尤其是疲劳性能。如本文所述,可通过在固化过程中施加压力来降低孔隙率。例如,在发动机缸体的精密砂型铸造中,施加大约3个大气压(amt)的绝对压力可以将孔隙率降低50%以上。这仅仅是用于特定工艺和特定铸造的加压的例子,并且可以使用任何合适的加压方案。可以计算出获得孔隙率足够低的铸件所需的最小压力。这种计算可以用任何商业上可获得的铸造过程模拟软件来完成。此外,加压的压力和持续时间可以基于铸件几何形状、模具条件和铸件质量要求来计算。对于砂型铸造工艺,砂渗透性可用于确定铸件和模具界面上的压力建立时间,即加压下的持续时间。
36.所公开的方法和系统能够根据设计要求制造具有非常薄、非常厚或非常复杂几何形状的铸件。示例性的铸件是使用最少冒口使用量(minimum riser usage)生产的高完整性无收缩铸件,因此提高了材料产量。
37.在示例性实施例中,该方法和系统可以施加大于1.5,例如大于1.75,例如大于2,例如大于2.25,例如大于2.5,例如大于2.75,例如大于3,例如大于3.25atm,例如大于2,例如大于2.25atm的升高的(绝对)压力。在示例性实施例中,该方法和系统可以施加小于4.5,例如小于4.25,例如小于4,例如小于3.75,例如小于3.5,例如小于3.25,例如小于3,例如小于2.75atm,例如小于2.5,例如小于2.25atm的升高的(绝对)压力。
38.在示例性实施例中,与在相同铸造条件下但在环境压力下制造的铸件相比,该方法和系统可以将铸件中的孔隙率降低至少20%,例如至少30%,例如至少40%,例如至少50%,例如至少60%。
39.如本文所述,使用本文所述的方法和系统可以降低铸件孔隙率、铸件废料和保修费用。此外,通过本文描述的方法和系统生产的铸件可以具有改进的机械性能和铸造性能。此外,本文描述的方法和系统可以允许减小冒口尺寸、增加金属产量和降低制造成本。
40.在示例性实施例中,用于降低铸件孔隙率的方法和系统用于连续精密砂型铸造工艺。在其他示例性实施例中,用于降低铸件孔隙率的方法和系统用于连续半永久模具(semi-permanent mold,spm)铸造工艺中。在其他示例性实施例中,用于降低铸件孔隙率的方法和系统用于连续永久铸模(permanent mold,pm)铸造工艺中。对于砂型铸造、spm铸造和pm铸造工艺中的每一种,可以使用独特的加压室。
41.此外,在示例性实施例中,加压室可以包含由空气构成的加压气体介质。在其他实施例中,加压气体介质是雾(空气和水)。在其他实施例中,加压气体介质包括惰性气体或由惰性气体组成。例如,加压气体介质可以是至少50%,例如至少60%,例如至少70%,例如至少80%,例如至少90%,例如至少92%,例如至少94%,例如至少95%,例如至少96%,例如至少97%,例如至少98%或至少99%的惰性气体或惰性气体的混合物。已经发现,使用高导热介质会降低微结构的精细度。
42.合适的惰性气体可以具有高热导率,即热导率大于空气的热导率(》0.026w/mk@300k)。例如,惰性气体可以是氦,其具有0.151w/mk@300k的热导率。在示例性实施例中,加压气体介质的热导率大于0.03,例如大于0.05,例如大于0.1,例如大于0.12,例如大于0.14或大于0.15w/mk@300k。
43.已经认识到,可以根据需要在过程中的不同时间将不同的气体介质引入加压室,以进一步提高冷却速率。例如,可以在选定的位置引入高导热介质,以增加铸件的热传递速
率,用于加速加热和/或加速冷却。
44.加压室可以是固定的,也可以在铸造线中移动。
45.在示例性实施例中,本文所述的方法和系统用于从铝合金生产铸件,所述铝合金包括但不限于铝硅基合金,例如a356、a357、319、355等;铝-铜基合金,例如206合金、242合金等;铝镁基合金,如515、535等;和铝锌基合金,例如707、710等。
46.在本文所述的方法和系统的示例性实施例中,在所述加压过程中施加的压力不超过500磅/平方英寸(psi)。在示例性实施例中,在所述加压过程中施加的压力为30磅/平方英寸(2个atm)至150磅/平方英寸(约10个atm)。压力可以在固化过程的一部分或整个过程中施加。例如,发动机缸体的完全固化可能需要600秒,气缸的完全固化可能需要400到500秒。预计在产品关键位置(如发动机缸体中的舱壁和气缸盖中的盖面)之前,不应停止加压过程。典型地,对于发动机缸体舱壁区域,凝固时间可能需要150至250秒,对于气缸盖甲板表面区域,凝固时间可能需要100至200秒。
47.在本文描述的方法和系统的示例性实施例中,铸造包括在取决于合金类型的温度下浇注液态金属。典型地,在模具填充期间,发动机缸体和气缸盖的过热(高于合金液相线的温度)为100至200℃。对于示例性的加压介质,温度可以从室温到50℃。
48.现在参考图1,示出了用于在连续铸造过程中降低铸件孔隙率的在线铸造系统100的实施例。如上所述,铸造工艺可以是砂型铸造、spm铸造或pm铸造工艺。连续铸造过程沿着图1中的线性生产线110顺序进行。如图所示,系统100包括用于组装模具的模具组装站120。此外,系统100包括填充站或浇注站130,用于用熔融材料填充模具,例如像铝这样的熔融金属,包括铝合金。
49.如图所示,系统100包括加压站140,用于在升高的压力下致密熔融和/或半固体材料。加压站140可以被认为是加压室。示例性加压站140可以相对于周围环境密封,使得在加压站140内可以有效地保持升高的压力。此外,系统100包括铸件/模具拆卸站150,用于拆卸模具和其中形成的铸件。
50.在所示实施例中,加压室140包括三个室部分:预加压室部分141、加压室部分142和压力释放室部分143。终端室部分141和143可以选择性地与周围环境密封,使得其中的压力可以根据需要升高或保持或降低。中央腔室部分142可以选择性地与终端腔室部分141和143密封,从而在腔室部分142内有效且恒定地保持期望的、升高的压力。
51.如图1所示,压力计和阀161、162和163分别设置在每个腔室部分141、142和143中,以监控和保持其中的期望压力。根据模具材料,可以从每个压力计和阀161-163向铸造浇口入口、开口冒口和/或铸造模具施加压力。对于非金属模具,压力可以施加到浇口入口、开口冒口和铸造模具上。对于金属型铸造,例如半永久型铸造,压力可以直接施加到浇口入口和开口冒口。
52.如图所示,系统100还包括用于控制连续铸造过程操作的控制模块170。此外,该系统包括传感器175,用于感测加压站140的准备状态。具体而言,传感器175可以确定加压站140何时准备好额外的模具,或者即将准备好额外的模具,例如在准备好额外的模具的30秒、20秒、10秒或5秒内。
53.如图1所示,提供位置180,包括181、182、183、184、185、186、187和188,用于在加工过程中定位模具单元190。虽然每个站120、130、140和150可以设置有任何期望的实际数量
的位置180,但是在所示实施例中,站120、130和150每个都具有一个位置180,并且站140具有多个位置。具体地,预加压室部分141包括一个位置183,加压室部分142包括三个位置184-186,压力释放室部分143包括一个位置187。设置在每个腔室部分141、142和143中的位置180的数量可以被优化,以在压力下为正在制造的铸件提供适当的持续时间。
54.现在参考图2,在线铸造系统100被示出与连续铸造过程中的转盘或旋转铸造生产线一起使用。同样,铸造工艺可以是砂型铸造、spm铸造或pm铸造工艺。连续铸造过程沿着图2中的旋转生产线210顺序进行。如图所示,系统100包括用于组装模具的模具组装站120。此外,系统100包括填充站或浇注站130,用于用熔融材料填充模具,例如像铝这样的熔融金属,包括铝合金。
55.如图所示,系统100包括加压站140,用于在升高的压力下致密熔融和/或半固体材料。加压站140可以被认为是加压室。示例性加压站140可以相对于周围环境密封,使得加压站140内可以有效地保持升高的压力。此外,系统100包括铸件/模具拆卸站150,用于拆卸模具和其中形成的铸件。
56.在所示实施例中,加压室140包括三个室部分:预加压室部分141、加压室部分142和压力释放室部分143。终端室部分141和143可以选择性地相对于周围环境密封,使得其中的压力可以根据需要升高或保持或降低。中央腔室部分142可以选择性地相对于终端腔室部分141和143密封,从而在腔室部分142内有效且恒定地保持期望的高压。
57.如图2所示,压力计和阀161、162和163分别设置在每个腔室部分141、142和143中,以监控和保持其中的期望压力。根据模具材料,可以从每个压力计和阀161、162和163向铸造浇口入口、开口冒口和/或铸造模具施加压力。对于非金属模具,压力可以施加到浇口入口、开口冒口和铸造模具上。对于金属型铸造,例如半永久型铸造,压力可以直接施加到浇口入口和开口冒口。
58.如图所示,系统100还包括用于控制连续铸造过程操作的控制模块170。此外,该系统包括传感器175,用于感测加压站140的准备状态。具体而言,传感器175可以确定加压站140何时准备好额外的模具,或者即将准备好额外的模具,例如在准备好额外的模具的30秒、20秒、10秒或5秒内。
59.如图2所示,提供位置80,包括181、182、183、184、185、186、187和188,用于在过程中定位模具单元190。虽然每个站120、130、140和150可以设置有任何期望的实际数量的位置180,但是在所示实施例中,站120、130和150每个都具有一个位置180,并且站140具有多个位置。具体地,预加压室部分141包括一个位置180,加压室部分142包括三个位置180,压力释放室部分143包括一个站。设置在每个腔室部分141、142和143中的位置180的数量可以被优化,以在压力下为正在制造的铸件提供适当的持续时间。
60.在图1和图2的每个实施例中,加压站140位于铸造生产线中的填充站130之后,使得一旦填充过程完成,浇注的铸件就可以被置于加压下。在某些实施例中,控制浇注铸件的引入时间,以避免铸件尺寸公差和表面质量问题。
61.注意,对于spm或pm铸造工艺,可通过将密封盖放置在相应模具单元190的开放冒口或浇注系统的顶部上来实现加压。
62.现在参考图3,提供了图1或图2沿任一图中的线3-3截取的截面图,以示出示例性实施例。如图所示,模具单元190包含在其中经历固化的铸件192和模具191。模具190直接由
铸造线110或210的传送输送机195支撑。
63.现在参考图4,提供了图1或图2沿任一图中的线3-3截取的截面图,以示出另一实施例。如图所示,模具单元190包含模具191、在其中经历固化的铸件192和支撑模具191的支撑件193。如图所示,模具单元190悬挂在铸造线110或210的传送输送机195上方。
64.这里的实施例还提供了在加压站140内,特别是在加压室部分142内进行冷却或插入物抽取。
65.图3-4示出了计量器和阀162与介质源165流体连通,用于向加压站提供所需介质,例如空气、雾、高热导率气体或其混合物。虽然图3-4仅示出了计量器和阀162,但是应当注意,每个计量器和阀161-163可以与介质源165流体连通,用于向加压站提供期望的介质,对于一个或多个计量器和阀,可以是相同的介质或者不同的介质。
66.参考图5,交叉参考图1和图2,示出了用于连续生产铸造金属部件的方法500,该方法减少了连续铸造过程中的铸件孔隙率。如图所示,方法500包括在动作框510,在填充站130将熔融材料,例如像铝合金的熔融金属,供给到模具中。此外,方法500包括在动作框520将加压室保持在升高的压力。在将熔融材料供给到模具中之后,该方法包括在动作框530将模具移动到加压室中。熔融金属在升高的压力下在模具中凝固。方法500还包括在动作框540处从加压室移除模具。
67.在示例性实施例中,方法500在移动的铸造生产线中执行,并且加压室在铸造生产线中移动。在另一个示例性实施例中,加压室是固定的。
68.如上所述,方法500可以在线性铸造生产线或旋转式铸造生产线中执行。此外,如上所述,该方法可以包括保持升高的(绝对)压力大于1.5,例如大于1.75,例如大于2,例如大于2.25,例如大于2.5,例如大于2.75,例如大于3,例如大于3.25atm,例如大于2,例如大于2.25atm。在示例性实施例中,该方法和系统可以施加小于4.5,例如小于4.25,例如小于4,例如小于3.75,例如小于3.5,例如小于3.25,例如小于3,例如小于2.75atm,例如小于2.5,例如小于2.25atm的升高的(绝对)压力。
69.如上所述,该方法可以包括用具有选定成分的加压气体介质填充和保持加压室。例如,加压气体介质可以由空气组成或包含空气,可以由雾(空气和水)组成或包含雾,或者可以由惰性气体组成或包含惰性气体,例如氦气。此外,方法500可包括在加压室中铸件的凝固过程期间改变加压气体介质。例如,方法500可以包括在加压室的选定位置引入不同的加压气体介质。
70.交叉参考图1和2,图6示出了用于连续生产铸造金属部件的方法600的实施例,该方法减少了连续铸造过程中的铸件孔隙率。
71.在一个示例性实施例中,方法600可以包括在动作框602,为期望的铸造过程和期望的铸造部件设计、建造和测试腔室部分141、142和143。此外,在动作框604,方法600可包括模拟铸造部件的铸造,以根据要使用的一种或多种气体介质来定制和优化压力分布和要在加压站140中施加的最大压力,并且具体地在部分141、142和143中施加。
72.方法600还可以包括在动作框606在模具组装站120组装模具。此外,方法600可以包括在动作框608将组装好的模具移动到填充站。
73.在某些实施例中,该方法包括在动作框612监控加压站140。例如,方法600可以监控加压站140的准备状态,并且具体监控腔室部分141、142和143的准备状态,关于压力分布
和介质是否是期望的。
74.在询问614,控制模块确定加压站140是否准备好接收额外的模具和铸件,如果否,则重复动作框612。如果加压站140准备接收额外的模具和铸件,则该方法继续在动作框616处将熔融材料,例如像铝合金的熔融金属,供给到填充站130处的模具中。因此,查询614一般基于加压站140的准备状态,具体地基于腔室部分141、142和143的准备状态来控制动作框616的执行时间。
75.方法600还包括在动作框618打开加压站140的预加压室部分141。方法600还包括在动作框622处,将填充的模具,即模具和其中的铸件,从填充站130移动到加压站140的打开的预加压室部分141。该方法还包括在动作框624密封预加压室部分141。
76.在示例性实施例中,方法600包括在动作框626用期望的加压气体介质增加和保持预加压室部分141中的压力,例如到加压室部分142的升高的压力。
77.此后,方法600包括在动作框628打开加压室部分142和预加压室部分141之间的流体连通。此外,方法600包括在动作框632将模具从预加压室部分141转移到加压室部分142。方法600还包括在动作框634密封加压室部分142。
78.在示例性实施例中,方法600包括在动作框636处,用期望的加压气体介质将加压室部分142保持在升高的压力下。此外,方法600包括在动作框638处,在加压室部分142中的升高的压力下固化模具中的熔融金属铸件。在示例性实施例中,铸件的大部分在加压室部分142中固化,例如铸件的80%以上,例如90%以上,例如约95%。
79.在示例性实施例中,方法600包括在动作框642处,用期望的加压气体介质将压力释放室部分143保持在升高的压力。
80.方法600包括在动作框644打开加压室部分142和压力释放室部分143之间的流体连通。此外,方法600包括在动作框646将模具从加压室部分142转移到压力释放室部分143。虽然铸件可以在加压室部分142中完全固化,但是在示例性实施例中,当转移到压力释放室部分143时,模具中的铸件接近完全固化,例如超过80%,例如超过90%,例如大约95%固化。方法600还包括在动作框648密封加压室部分142。
81.在示例性实施例中,方法600包括在动作框652处,用期望的加压气体介质将压力释放室部分143保持在升高的压力。
82.方法600可包括在动作框654,在升高的压力下,在压力释放室部分143中完成铸件的凝固。此外,在动作框656,方法600包括打开压力释放室部分143,并从压力释放室部分143移除完全固化的铸件和模具。此外,方法600包括在动作框658冷却铸件和模具。方法600还包括在动作框662,在铸件/模具拆卸站150拆卸模具和其中形成的铸件。
83.为了在每个腔室部分中施加压力,根据模具材料,压力可以施加到铸造浇口入口、开口冒口和/或铸造模具。对于非金属模具,压力施加在浇口入口、开口冒口和铸造模具上。对于金属型铸造,例如半永久型铸造,压力可以直接施加到浇口入口和开口冒口。
84.方法600预期连续生产铸件。因此,当第一模具,即下游模具,从当前站移动到下一站时,第二模具,即上游模具,在当前站进行替换移动。在加压站内,第二模具或附加模具可以移动到加压室部分中,并伴随下游模具,直到下游模具被从加压室部分移除。
85.使用预加压室部分141和压力释放室部分143允许打开加压室部分142以引入上游模具和移除下游模具,而不会损失加压室部分142中的压力。
86.在示例性实施例中,在动作框602和604,使用集成计算材料工程,针对被铸造的材料和模具以及铸造过程来定制和优化腔室部分的压力分布。
87.动作框626、636、642和652中的每一个可以包括引入不同的气体介质以提供期望的热传递速率,和/或执行冷却或插入抽取。
88.通过监控加压站140的准备状态,方法600提供了在连续过程中对后续铸件的自动和数字控制处理。
89.虽然在前面的详细描述中已经呈现了至少一个示例性实施例,但是应当理解,存在大量的变化。还应当理解,一个或多个示例性实施例仅是示例,并不旨在以任何方式限制本公开的范围、适用性或配置。相反,前述详细描述将为本领域技术人员提供用于实现一个或多个示例性实施例的便利路线图。应当理解,在不脱离所附权利要求及其法律等同物中阐述的本公开的范围的情况下,可以对元件的功能和布置进行各种改变。