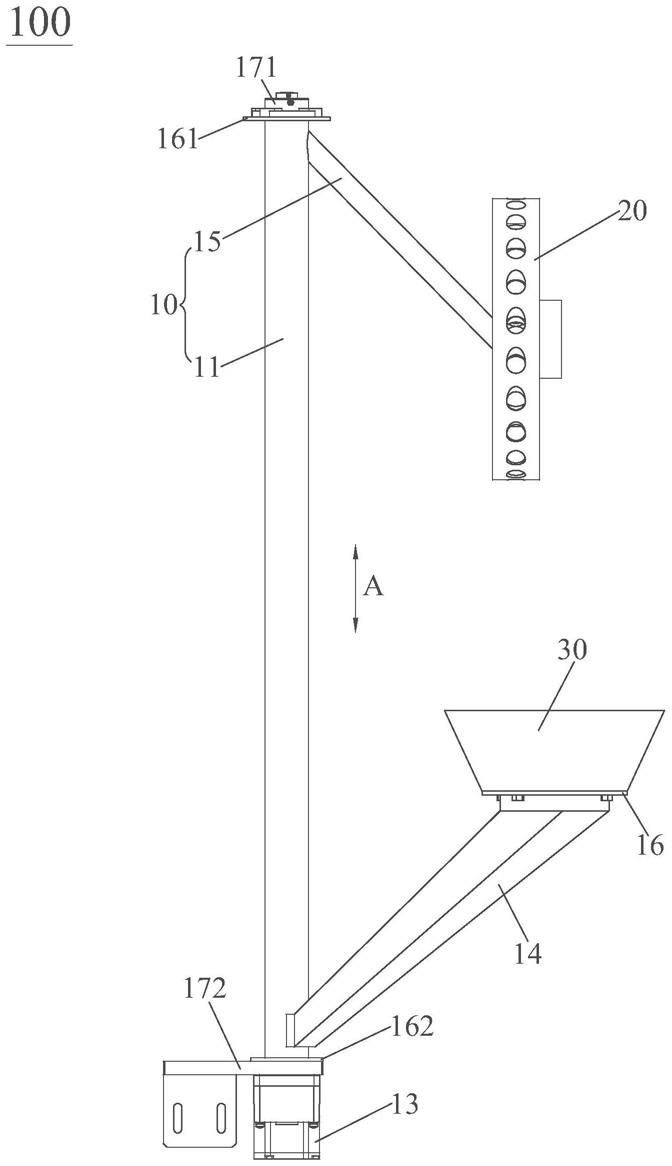
1.本发明涉及喷射抛光领域,尤其涉及一种离心式喷丸抛光机及其喷丸补料机构。
背景技术:2.众所周知,喷丸抛光机是通过高速旋转的离心抛丸盘将弹性磨粒(又称喷丸)以一定的速度甩抛在工件的表面,从而达到对工件的表面抛光以提高工件表面的硬度等性能。
3.目前,在现有的喷丸抛光机中,其离心抛丸盘的补料是靠带式输送机构完成,即是由带式输送机构将下方的料仓内的喷丸捞起并送入位于上方的离心抛丸盘中,而进入离心抛丸盘中的喷丸在离心抛丸盘的高速旋转下抛在工件的表面并最终回落到料仓中,以实现喷丸的循环利用的目的。
4.但是,在现有的喷丸抛光机中,由于它是靠带式输送机构进行补料,且带式输送机构是在上下方向做回转运动的回转带上装配有间隔一定距离排列的捞料片,故因相邻两捞料片之间存在间距而无法往离心抛丸盘进行连续不间断地补料,从而使得离心抛丸盘所抛出的喷丸时多时少而均匀性差,因而影响到抛光品质。
5.因此,亟需一种离心式喷丸抛光机及其喷丸补料机构来克服上述的一个或多个缺陷。
技术实现要素:6.本发明的一目的在于提供一种确保喷丸补料连续性和均匀性以确保抛光品质的喷丸补料机构。
7.本发明的另一目的在于提供一种确保喷丸补料连续性和均匀性以确保抛光品质的离心式抛光机。
8.为实现上述目的,本发明的喷丸补料机构适应将离心式喷丸抛光机中的料仓内喷丸送入离心式喷丸抛光机中的离心抛丸盘内,包含筒体、沿所述筒体的轴向呈间隙配合地穿置于所述筒体中的推料螺杆及位于所述筒体外并驱使所述推料螺杆在所述筒体中转动的转动驱动器。所述筒体上设有供所述料仓内的喷丸掉入所述筒体内的喷丸入料管及供所述推料螺杆所推送的喷丸送入所述离心抛丸盘内的喷丸出料管,所述喷丸出料管位于所述喷丸入料管的上方,所述喷丸入料管和喷丸出料管各呈靠近彼此的方向相对所述筒体倾斜。
9.较佳地,所述喷丸入料管为锥形管,所述锥形管沿远离所述筒体的方向呈逐渐增大的布置。
10.较佳地,所述喷丸入料管远离所述筒体的末端装配有一法兰盘。
11.较佳地,所述筒体的上末端固定有上法兰,所述筒体的下末端固定有下法兰,所述上法兰的上方装配有上轴承座结构,所述下法兰的下方装配有下轴承座结构,所述推料螺杆的上端装配于所述上轴承座结构,所述推料螺杆的下端装配于所述下轴承座结构,所述推料螺杆的下端还向下穿过所述下轴承座结构,所述转动驱动器与所述推料螺杆的下端连
接。
12.较佳地,所述喷丸出料管呈相邻地位于所述上法兰的下方,所述喷丸入料管呈相邻地位于所述下法兰的上方。
13.较佳地,所述转动驱动器直接或间接地与所述推料螺杆的下端连接。
14.较佳地,所述喷丸出料管和喷丸入料管在所述筒体的周向上彼此错位。
15.较佳地,所述筒体为圆形筒体,所述喷丸出料管为圆管。
16.为实现上述的目的,本发明的离心式喷丸抛光机包括离心抛丸盘、料仓及前述的喷丸补料机构。
17.较佳地,所述喷丸入料管位于所述料仓对应下方,所述喷丸出料管伸入所述离心抛丸盘中。
18.与现有技术相比,由于本发明的喷丸补料机构包含筒体、沿筒体的轴向呈间隙配合地穿置于筒体中的推料螺杆及位于筒体外并驱使推料螺杆在筒体中转动的转动驱动器,筒体上设有供料仓内的喷丸掉入筒体内的喷丸入料管及供推料螺杆所推送的喷丸送入离心抛丸盘内的喷丸出料管,喷丸出料管位于喷丸入料管的上方,喷丸入料管和喷丸出料管各呈靠近彼此的方向相对筒体倾斜;这样设计使得料仓内喷丸在自重作用下沿着喷丸入料管进入筒体中,被做旋转运动的推料螺杆向上连续推送,再由沿着喷丸出料管掉入离心抛丸盘中,实现喷丸往离心抛丸盘的连续补料,确保离心抛丸盘抛丸的均匀性,因而确保抛光品质。
附图说明
19.图1是本发明的离心式喷丸抛光机的平面图。
20.图2是本发明的离心式喷丸抛光机中的喷丸补料机构的立体图。
21.图3是图2所示的喷丸补料机构的分解图。
22.图4是图2所示的喷丸补料机构在隐藏转动驱动器且被中心平面剖切后的内部图。
具体实施方式
23.为了详细说明本发明的技术内容、构造特征,以下结合实施方式并配合附图作进一步说明。
24.请参阅图1,本发明的离心式喷丸抛光机100包括喷丸补料机构10、离心抛丸盘20及料仓30。料仓30一方面用于回收由离心抛丸盘20高速抛出的喷丸,另一方面用于存放操作人员所添加的喷丸;喷丸补料机构10用于将料仓30的喷丸送入离心抛丸盘20,由离心抛丸盘20将喷丸补料机构10所送入的喷丸以高速离心的方式抛向并撞击工件,从而实现喷丸对工件的抛光处理目的。
25.其中,结合图2和图3,喷丸补料机构10包含筒体11、沿筒体11的轴向(见箭头a所指的方向)呈间隙配合地穿置于筒体11中的推料螺杆12及位于筒体11外并驱使推料螺杆12在筒体11中转动的转动驱动器13。筒体11上设有供料仓30内的喷丸掉入筒体11内的喷丸入料管14及供推料螺杆12所推送的喷丸送入离心抛丸盘20内的喷丸出料管15,喷丸出料管15位于喷丸入料管14的上方,喷丸入料管14和喷丸出料管15各呈靠近彼此的方向相对筒体11倾斜。具体地,在图2和图3中,喷丸出料管15和喷丸入料管14在筒体11的周向上彼此错位,为
离心抛丸盘20和料仓30之间的布置提供充足的位置;喷丸入料管14为锥形管,锥形管沿远离筒体11的方向呈逐渐增大的布置,这样设计能进一步地确保料仓30中的喷丸沿着喷丸入料管14自动掉落到筒体11中;此外,喷丸入料管14位于料仓30对应的下方,喷丸出料管15伸入离心抛丸盘20中。更具体地,在图1至图4中,喷丸入料管14远离筒体11的末端装配有一法兰盘16,以借助法兰盘16而便于喷丸入料管14从上方装配于料仓30处,从而能进一步地确保料仓30中的喷丸在自重作用下顺畅地掉落到筒体11中,当然,根据实际需要,可将法兰盘16删除,故不以此为限。
26.如图1至图4所示,筒体11的上末端固定有上法兰161,筒体11的下末端固定有下法兰162,上法兰161的上方装配有上轴承座结构171,下法兰162的下方装配有下轴承座结构172,推料螺杆12的上端装配于上轴承座结构171,由上轴承座结构171对推料螺杆12的上端提供支撑的作用及装配的场所,推料螺杆12的下端装配于下轴承座结构172,由下轴承座结构172提供支撑的作用及装配的场所;推料螺杆12的下端还向下穿过下轴承座结构172,以便于与位于筒体11外的转动驱动器13连接,转动驱动器13与推料螺杆12的下端连接,以将转动驱动器13布置于筒体11的下方,避免将转动驱动器13布置于筒体11的上方而占用上方的空间,从而使得上方的离心抛丸盘20布置空间受到极大约束,增加了离心抛丸盘20的操作难度。具体地,如图1至图3所示,喷丸出料管15呈相邻地位于上法兰161的下方,喷丸入料管14呈相邻地位于下法兰162的上方,这样布置以最大限度地将筒体11的长度利用起来。更具体地,在图2和图3中,转动驱动器13间接地与推料螺杆12的下端连接,当然,根据实际需要可将转动驱动器13直接地与推料螺杆12的下端连接,故不以附图所示为限。举例而言,筒体11为圆形筒体,以确保推料螺杆12与筒体11之间每处的间隙保持一致,还便于筒体11的制造加工;另,喷丸出料管15为圆管,以便于喷丸出料管15加工制造,但不以此举例为限。需要说明的是,由于推料螺杆12与筒体11为间隙配合,该间隙d一方面要满足推料螺杆12做旋转的需要,另一方面要保证喷丸在被推料螺杆12向上输送过程中不能从间隙d漏走,因此,该间隙d小于喷丸的尺寸。
27.与现有技术相比,由于本发明的喷丸补料机构10包含筒体11、沿筒体11的轴向呈间隙配合地穿置于筒体11中的推料螺杆12及位于筒体11外并驱使推料螺杆12在筒体11中转动的转动驱动器13,筒体11上设有供料仓30内的喷丸掉入筒体11内的喷丸入料管14及供推料螺杆12所推送的喷丸送入离心抛丸盘20内的喷丸出料管15,喷丸出料管15位于喷丸入料管14的上方,喷丸入料管14和喷丸出料管15各呈靠近彼此的方向相对筒体11倾斜;这样设计使得料仓30内喷丸在自重作用下沿着喷丸入料管14进入筒体11中,再被做旋转运动的推料螺杆12向上连续推送,然后从喷丸出料管15掉入离心抛丸盘20中,实现喷丸往离心抛丸盘20的连续补料,确保离心抛丸盘20抛丸的均匀性,因而确保抛光品质。
28.以上所揭露的仅为本发明的较佳实例而已,不能以此来限定本发明之权利范围,因此依本发明权利要求所作的等同变化,均属于本发明所涵盖的范围。