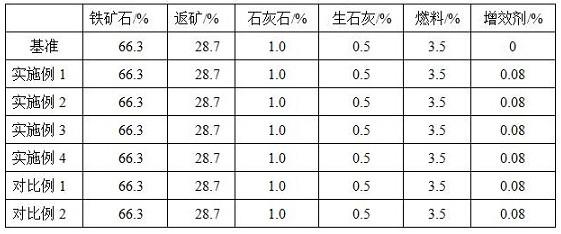
1.本发明属于冶金烧结技术领域,具体涉及一种冶金烧结增效剂及其制备方法和应用。
背景技术:2.在炼钢生产中,高炉炼铁首先要通过烧结机把混合矿通过烧结机烧成烧结矿。因此,烧结机承担着向高炉提供优质烧结矿的主要任务。由于采购矿石多样化,进口矿配比不稳定,国内矿来源复杂和细粉级料含量增多等因素影响,高炉返矿增加(25%-30%),粉末污染严重,矿源损失较大,问题比较突出,这成为钢铁企业,前系统工序优化的主要矛盾之一。根据国内部分钢铁企业添加bm增效剂获得提质增效的实践经验。宝武钢铁集团,原昆钢股份三家直属钢铁厂进行了相关的烧结杯实验及已生产使用了9年的情况,取得了烧结矿转鼓强度提高,平均有用粒度增加,烧结矿小于5mm粒度含量降低明显。上述实际生产数据表明,增效剂确实能提高烧结矿强度和改善烧结矿粒度组成。
3.现有技术中,已有一些针对烧结增效剂的研究。如专利文献cn110527824a报道了一种多金属组成的添加剂,使用成本高;专利文献cn105907951a报道了一种以矿石为主的烧结添加剂,但是未充分考虑烧结过程中烧结矿的还原性;专利文献cn101245411a报道了一种烧结复合添加剂,使用了硝酸铈这一稀土金属,成本高,同时含有大量的碱性元素。可以看到,现有技术中,增效剂的使用存在着成本高、未充分考虑烧结过程与烧结矿性能同时改善等不足。
技术实现要素:4.针对现有技术的不足,本发明的目的在于一种冶金烧结增效剂及其制备方法和应用。增效剂以炼钢厂常见的钢渣为主要原料,烧结矿强度好、粒度分布好,烧结矿的还原度好,能够极大地降低燃耗。
5.为实现上述目的,本发明提供如下技术方案:一种冶金烧结增效剂,以质量百分比计,由以下原料制得:钢渣35~65%,聚乙二醇0.1~2%,萤石2~8%,高锰酸钾0.05~2.5%,过氧化氢0.5~8%,偏钒酸铵1~5%,废弃活性炭0.5~2%,余量为水。
6.优选的,以质量百分比计,所述增效剂由以下原料制得:钢渣40~60%,聚乙二醇0.5~1.5%,萤石3~5%,高锰酸钾0.2~2%,过氧化氢1~6%,偏钒酸铵2~4%,废弃活性炭0.8~1.5%,余量为水。
7.优选的,所述钢渣包含以下组分:氧化钙34.63%,tfe 18.15%,二氧化硅13.55%,氧化镁11.36%,三氧化二铝5.93%,mno 1.35%。
8.优选的,所述废弃活性炭为烧结烟气脱硫脱硝过程产生的活性炭。
9.优选的,所述废弃活性炭的固定碳含量为80%wt。
10.本发明还提供一种上述增效剂的制备方法,包括如下步骤;
(1)将钢渣烘干后进行破碎;(2)按比例称取聚乙二醇、萤石、高锰酸钾、过氧化氢、偏钒酸铵、废弃活性炭,随后将上述物质与步骤(1)所得钢渣一起与水混合均匀,即得增效剂。
11.优选的,步骤(1)中破碎后的钢渣粒度为:-1mm粒度的钢渣占95%,-0.1mm粒度的钢渣占65%。
12.同时,本发明还要求保护由上述方法制备得到的增效剂在强化烧结矿烧结中的应用。
13.优选的,所述增效剂的用量为烧结原料的0.05~0.2%wt。
14.优选的,在一混时,将增效剂加入到烧结原料中,经制粒后即可进行烧结。
15.与现有技术相比,本发明具有如下的有益效果:(1)钢渣是炼钢厂的副产物,其数量可以占到钢产量的20%左右,对钢渣资源的再利用具有重要的经济和生态意义。本技术结合某钢厂副产的钢渣的成分,创造性地将其用于制备增效剂中。其中,氧化镁的存在有利于抑制铁酸钙和赤铁矿的生成,降低烧结矿的粉化,改善烧结矿的粒度;同时,钢渣中还含有氧化钙和二氧化硅,二氧化硅和氧化镁还能够与氧化钙作用形成低熔点的矿物质,优化烧结过程中的渣系,提高烧结过程中液相的生成量,改善烧结体系中液相的流动性,达到改善烧结矿强度的目的。
16.(2)本发明中使用聚乙二醇作为分散剂,能够使烧结料具有良好的制粒效果,改善料层透气性。本发明使用到的过氧化氢能够在高锰酸钾的作用下产生氧气,使得烧结原料表面的四氧化三铁氧化,降低亚铁的量,低亚铁量有利于改善和提高烧结矿的还原性能;高锰酸钾的阳离子在烧结矿还原的过程中迁移形成硅铝酸盐,最终形成微晶集合体,并会随之还原晶化。当随着温度的升高时,晶体就越来越强,而烧结矿的整体结构就会疏松,在一定程度上也会使烧结矿还原性得到改善。同时,本发明中还使用了少量的萤石,萤石的主要成分是caf,caf具有降低烧结料熔点的作用,使得烧结料更容易燃烧,达到节能降耗的作用。同时,本发明中使用到的少量偏钒酸铵,能够促进氧化铁生成铁酸盐,降低烧结原料以及钢渣中的氧化铁的含量,抑制fe2o3向fe3o4转化,减弱了晶型转变引起的粉化现象,使得烧结矿的低温还原粉化指数好。
17.(3)本发明中使用到了少量的钢厂副产物废弃活性炭,其具有比表面积大、活性高、固定碳含量等特性,在烧结原料烧结过程中能够充分燃烧,降低燃料的消耗;同时,废弃活性炭在燃烧过程中能够优化燃烧过程,提高烧结过程中温度,促进烧结原料中各个矿物质间的反应,促进液相的形成,达到降耗和提高烧结矿强度的目的。
18.总之,本发明通过优化复配物质,增效剂的使用能够提高烧结矿转鼓质量,提高垂直烧结速度,改善烧结矿的粒度组成,改善rdi
+3.15
,改善还原度和熔滴性能,降低能耗。
具体实施方式
19.下面将结合具体实施方式对本发明中的技术方案进行清楚、完整地描述,显然,所描述的实施例仅仅是本发明一部分实施例,而不是全部的实施例。基于本发明中的实施例,本领域普通技术人员在没有做出创造性劳动前提下所获得的所有其他实施例,都属于本发明保护的范围。所有原料均可通过钢厂或市售获得。
20.实施例1
一种冶金烧结增效剂,以质量百分比计,由以下原料制得:钢渣55%,聚乙二醇1%,萤石3%,高锰酸钾1%,过氧化氢1.5%,偏钒酸铵2%,废弃活性炭1%,余量为水。
21.其中,所述钢渣包含以下组分:氧化钙34.63%,tfe 18.15%,二氧化硅13.55%,氧化镁11.36%,三氧化二铝5.93%,mno 1.35%。
22.其中,所述废弃活性炭为烧结烟气脱硫脱硝过程产生的活性炭。
23.其中,所述废弃活性炭的固定碳含量为80%wt。
24.本实施例中,上述增效剂的制备方法包括以下步骤:(1)将钢渣烘干后进行破碎,破碎后的钢渣粒度为:-1mm粒度的钢渣占95%,-0.1mm粒度的钢渣占65%;(2)按比例称取聚乙二醇、萤石、高锰酸钾、过氧化氢、偏钒酸铵、废弃活性炭,随后将上述物质与步骤(1)所得钢渣一起与水混合均匀,即得增效剂。
25.本实施例中,还提供一种上述增效剂在强化烧结矿烧结中的应用,应用方法如下:按照烧结原料质量0.08%wt的用量,在一混时,将增效剂加入到烧结原料中,经制粒后即可进行烧结。
26.实施例2一种冶金烧结增效剂,以质量百分比计,由以下原料制得:钢渣58%,聚乙二醇1%,萤石3.5%,高锰酸钾1%,过氧化氢2%,偏钒酸铵2.5%,废弃活性炭1.2%,余量为水。
27.所述钢渣包含以下组分:氧化钙34.63%,tfe 18.15%,二氧化硅13.55%,氧化镁11.36%,三氧化二铝5.93%,mno 1.35%。
28.其中,所述废弃活性炭为烧结烟气脱硫脱硝过程产生的活性炭。
29.其中,所述废弃活性炭的固定碳含量为80%wt。
30.本实施例中,上述增效剂的制备方法包括以下步骤:(1)将钢渣烘干后进行破碎,破碎后的钢渣粒度为:-1mm粒度的钢渣占95%,-0.1mm粒度的钢渣占65%;(2)按比例称取聚乙二醇、萤石、高锰酸钾、过氧化氢、偏钒酸铵、废弃活性炭,随后将上述物质与步骤(1)所得钢渣一起与水混合均匀,即得增效剂。
31.本实施例中,还提供一种上述增效剂在强化烧结矿烧结中的应用,应用方法如下:按照烧结原料质量0.08%wt的用量,在一混时,将增效剂加入到烧结原料中,经制粒后即可进行烧结。
32.实施例3一种冶金烧结增效剂,以质量百分比计,由以下原料制得:钢渣59%,聚乙二醇1.1%,萤石3.5%,高锰酸钾1.1%,过氧化氢2%,偏钒酸铵2.7%,废弃活性炭1.3%,余量为水。
33.所述钢渣包含以下组分:氧化钙34.63%,tfe 18.15%,二氧化硅13.55%,氧化镁11.36%,三氧化二铝5.93%,mno 1.35%。
34.其中,所述废弃活性炭为烧结烟气脱硫脱硝过程产生的活性炭。
35.其中,所述废弃活性炭的固定碳含量为80%wt。
36.本实施例中,上述增效剂的制备方法包括以下步骤:(1)将钢渣烘干后进行破碎,破碎后的钢渣粒度为:-1mm粒度的钢渣占95%,-0.1mm粒度的钢渣占65%;
(2)按比例称取聚乙二醇、萤石、高锰酸钾、过氧化氢、偏钒酸铵、废弃活性炭,随后将上述物质与步骤(1)所得钢渣一起与水混合均匀,即得增效剂。
37.本实施例中,还提供一种上述增效剂在强化烧结矿烧结中的应用,应用方法如下:按照烧结原料质量0.08%wt的用量,在一混时,将增效剂加入到烧结原料中,经制粒后即可进行烧结。
38.实施例4一种冶金烧结增效剂,以质量百分比计,由以下原料制得:钢渣60%,聚乙二醇1.3%,萤石3.5%,高锰酸钾1%,过氧化氢2%,偏钒酸铵2.5%,废弃活性炭1.4%,余量为水。
39.所述钢渣包含以下组分:氧化钙34.63%,tfe 18.15%,二氧化硅13.55%,氧化镁11.36%,三氧化二铝5.93%,mno 1.35%。
40.其中,所述废弃活性炭为烧结烟气脱硫脱硝过程产生的活性炭。
41.其中,所述废弃活性炭的固定碳含量为80%wt。
42.本实施例中,上述增效剂的制备方法包括以下步骤:(1)将钢渣烘干后进行破碎,破碎后的钢渣粒度为:-1mm粒度的钢渣占95%,-0.1mm粒度的钢渣占65%;(2)按比例称取聚乙二醇、萤石、高锰酸钾、过氧化氢、偏钒酸铵、废弃活性炭,随后将上述物质与步骤(1)所得钢渣一起与水混合均匀,即得增效剂。
43.本实施例中,还提供一种上述增效剂在强化烧结矿烧结中的应用,应用方法如下:按照烧结原料质量0.08%wt的用量,在一混时,将增效剂加入到烧结原料中,经制粒后即可进行烧结。
44.对比例1一种冶金烧结增效剂,以质量百分比计,由以下原料制得:钢渣55%,聚乙二醇1%,萤石3%,高锰酸钾1%,过氧化氢1.5%,偏钒酸铵2%,余量为水。
45.其中,所述钢渣包含以下组分:氧化钙34.63%,tfe 18.15%,二氧化硅13.55%,氧化镁11.36%,三氧化二铝5.93%,mno 1.35%。
46.本实施例中,上述增效剂的制备方法包括以下步骤:(1)将钢渣烘干后进行破碎,破碎后的钢渣粒度为:-1mm粒度的钢渣占95%,-0.1mm粒度的钢渣占65%;(2)按比例称取聚乙二醇、萤石、高锰酸钾、过氧化氢、偏钒酸铵,随后将上述物质与步骤(1)所得钢渣一起与水混合均匀,即得增效剂。
47.本实施例中,还提供一种上述增效剂在强化烧结矿烧结中的应用,应用方法如下:按照烧结原料质量0.08%wt的用量,在一混时,将增效剂加入到烧结原料中,经制粒后即可进行烧结。
48.对比例2一种冶金烧结增效剂,以质量百分比计,由以下原料制得:钢渣55%,聚乙二醇1%,萤石3%,高锰酸钾1%,过氧化氢1.5%,废弃活性炭1%,余量为水。
49.其中,所述钢渣包含以下组分:氧化钙34.63%,tfe 18.15%,二氧化硅13.55%,氧化镁11.36%,三氧化二铝5.93%,mno 1.35%。
50.其中,所述废弃活性炭为烧结烟气脱硫脱硝过程产生的活性炭。
51.其中,所述废弃活性炭的固定碳含量为80%wt。
52.本实施例中,上述增效剂的制备方法包括以下步骤:(1)将钢渣烘干后进行破碎,破碎后的钢渣粒度为:-1mm粒度的钢渣占95%,-0.1mm粒度的钢渣占65%;(2)按比例称取聚乙二醇、萤石、高锰酸钾、过氧化氢、废弃活性炭,随后将上述物质与步骤(1)所得钢渣一起与水混合均匀,即得增效剂。
53.本实施例中,还提供一种上述增效剂在强化烧结矿烧结中的应用,应用方法如下:按照烧结原料质量0.08%wt的用量,在一混时,将增效剂加入到烧结原料中,经制粒后即可进行烧结。
54.将上述实施例1~4及对比例1~2制备得到的增效剂进行性能测试,包括烧结杯试验以及烧结矿的冶金性能测试。其中,冶金性能测试测试包括低温还原粉化率、还原度及熔滴性能三个方面。
55.(1)烧结杯试验烧结杯试验包括以下步骤:a)一混:将按比例称好的烧结原料、增效剂置于2.5m
×
2m的铁板上,在铁板上来回折翻8次,得烧结混合料;其中,增效剂的用量为烧结原料的0.08%wt;需要说明的是,在实际混合过程中,为了保证混料的质量,可以适量加水以调整水分含量在7.5%左右;b)二混:在圆筒制粒机内对烧结混合料进行制粒;圆筒制粒机直径为0.6m,高为1.0m,圆筒制粒机转速为17r/min,制粒时间为3min;c)烧结:将制粒后的烧结原料装入烧结杯中进行烧结;烧结过程中,用3kg烧结矿作为铺底料;烧结工艺参数为:点火温度1070
±
20℃,点火时间1.5min,点火负压8000
±
200pa,烧结负压11000
±
500pa;在尾气温度达到最高温度并下降到100℃后,停机进行烧结矿粒度、转鼓检测;d)烧结杯过程检测:在烧结后首先经过四次2m高的落入强度检测;经过落下强度处理后的烧结矿用25mm、10mm、5mm的筛子进行筛分,筛分后称量各粒度的质量确定烧结矿的粒度组成;随后,取1.5kg大于25mm,1.5kg大于10mm小于25mm的成品烧结矿做转鼓实验,同时取样大于10mm的烧结矿若干留待做其他性能测试,留出铺底料3kg;并检测烧结矿的成品率,计算烧损率、烧结垂直烧结速度、利用系数、转鼓指数以及燃耗等。
56.(2)冶金性能测试a)还原粉化实验:参照gb/t 13242-2017进行还原粉化实验;b)还原度测试:参照gb/t 13241-2017进行还原度测试;c)熔滴测试:参照gb/t 34211-2017进行熔滴测试。
57.烧结配比见表1,测试结果汇总见2~表6。
58.表1 原料配比
表2 烧结杯测试结果表3 粒度分布结果
表4 低温还原粉化结果表5 还原度测试结果表6 熔滴测试结果
从表2中可以看到,增效剂的使用,转鼓增加,提高了垂直烧结速度和烧结利用率,达到了提高烧结产量的效果。
59.从表3中可以看到,增效剂的使用。极大地改善了烧结矿粒度的组成分布,10~25mm这一粒度区间的占比显著增加。
60.从表4中可以看到,增效剂的使用,低温还原粉化率rdi
+3.15
改善明显。
61.从表5中可以看到,增效剂的使用,还原度提高。
62.从表6中可以看到,增效剂的使用,软熔带开始温度下降,滴落带终了温度增加,有利于强化冶炼。从总特性值s来看,100~150范围内为最佳值,显然增效剂的使用量在0.08%较为合适。
63.尽管已经示出和描述了本发明的实施例,对于本领域的普通技术人员而言,可以理解在不脱离本发明的原理和精神的情况下可以对这些实施例进行多种变化、修改、替换和变型,本发明的范围由所附权利要求及其等同物限定。