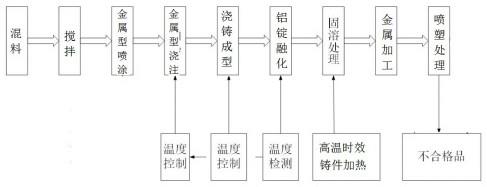
1.本发明涉及一种铝合金铸造领域,尤其涉及到一种液压盘式制动器铸件铝合金热处理工艺。
背景技术:2.液压盘式制动器在浇铸过程中强度和刚性有差异,单纯的al-si合金不可强化,申请号:201711141252.6一种铝合金铸件表面的热处理方法,其特征在于,包括以下步骤:s1:选取将铸造完成的铝合金铸件,直接将其置入25-35摄氏度的水中进行淬火,待其 温度降低至100-150摄氏度,取出备用;s2:将s1中处理后的铝合金铸件放置在电解槽内,并向电解槽内添加电解液,且需保证 电解液漫过压铸件,在80-100摄氏度的条件下对压铸件进行表面电解预处理,且电解时间为5-8min;s3:上述完成后,将铝合金铸件取出,并在常温下自然降温度降低至35-45摄氏度,然后 在240-260摄氏度的条件下再次进行回火,且回火时间120-150min,然后将置于冷却风机下进行冷却,待温度降低至50-80摄氏度,再次将铝合金铸件在140-160摄氏度的条件下再次进行回火,且回火时间为30-50min,完成后,将其在空气中冷却至室温,即完成铝合金铸件的热处理,但是铝合金处理后强度会降低,抗拉强度不够,变形量不恒定。
技术实现要素:3.本发明要解决的问题是提出了一种通过调整材料成分和固溶处理改进,提升卡钳关键部位抗拉强度、硬度和刚性,提高切削性能,减少热裂且制动钳进油孔加液压卡钳变形量变小的液压盘式制动器铸件铝合金热处理工艺。
4.为实现上述目的,本发明提供了一种液压盘式制动器铸件铝合金热处理工艺,工艺包括以下步骤:步骤一:材料成分选择,铸件以重量百分比计,铸件铝合金的材料成分包括:硅si 9~10%;铜cu 1.6~1.8%;锰mn 0.2~0.30%;镁mg 0.3~0.4%;锌zn 0.3~0.4%;铁fe 0~0.2%;余量的锡、铅和杂质,其中杂质总和≤1.0;步骤二:首先将上述原材料混合并进行充分搅拌,然后将水加热到50~60℃后再将搅拌均匀的原材料加入搅拌桶内充分搅拌,待搅拌均匀后评估涂料稀稠浓度,停止搅拌,放置1~2小时进行充分溶解,再采用400目筛网进行过滤,然后将涂料装入喷枪备用,金属型腔喷砂工作;步骤三:金属型喷涂处理;
将金属型预热到150~250℃,经过预热的金属型型腔、金属型芯及浇冒口部位的型面喷刷涂料;步骤四:金属型浇注处理:将浇包内加热到150~250℃后进行,涂料涂刷后再次烘干处理,金属型的预热温度为150~250℃;步骤五:模具浇铸成型:浇铸成型工序中利用坩埚和熔炼工具,保温炉采用温度控制电炉,将熔化温度控制为690~720度,将硅充分熔化;步骤六:铝锭融化工艺:高温人工时效处理利用坩埚和熔炼工具,将铝锭熔化,熔化温度设定为690~720度,清除搅拌和坩埚的铁锈和氧化物,将硅充分熔化;步骤七:固溶热处理:包括固溶处理和高温人工时效处理,其中,固溶处理将铸件溶解到固溶体中快速冷却,铸件加热温度为515~525度;加热保温过程中,30~40min缓慢加热至500~515度,保温30~45分钟,经过二次加热保温,10~20min缓慢加热到525~540度,保温5~7小时,60~100度水淬火20~30分钟,高温时效为160~170度;步骤八:金属加工处理;旋压、弯曲、剪切和冲压成型,对铸件外形进行加工;步骤九:喷塑处理将涂料喷涂到铸件的表面,粉末均匀地吸附在铸件表面形成粉状涂层;将粉状涂层经过高温烘烤后流平固化形成保护涂层,附于铸件表面。
5.优选地,步骤四中,涂料涂刷原材料为石墨。
6.优选地,步骤四中,先将金属型合好后用夹口夹紧,舀取铝液时先用浇包底将铝液表面的氧化皮推开,再用浇包一侧舀取铝液,并将氧化皮和其它杂物去除干净,将金属型倾斜80度,用浇包嘴贴紧金属型的浇冒口边进行浇注,浇注时铝液进入型腔的流速采用先慢、中快、后慢的工序,金属型浇注完毕后铝液和氧化皮倒入容器内。
7.优选地,步骤五中,保温炉内铝液温度控制在690~720℃,铝液经过精炼处理,铝液需在30~40分钟内完成。
8.与现有技术相比,本发明的具有下列优点:首先将上述原材料混合并进行充分搅拌,金属型喷涂处理,金属型浇注处理,模具浇铸成型,铝锭融化工艺,固溶热处理,材料成分选择,铸件以重量百分比计,铸件铝合金的材料成分,硅si9~10%;铜cu 1.6~1.8%;锰mn 0.2~0.30%;镁mg 0.3~0.4%;锌zn 0.3~0.4%;铁fe 0~0.2%;余量的锡、铅和杂质,其中杂质总和≤1.0,参照qc/t655标准,通过调整材料成分和固溶处理改进,提升卡钳关键部位强度,提高切削性能,减少热裂,抗拉强度σb从315mpa提升到350mpa,硬度hb从105
±
5提升到115-125,卡钳关键部位变形量,动钳进油孔加液压从7mpa提升到10-11mpa,卡钳变形量小于0.35mm。
9.另外,通过实验测试,加压7mpa,保持5s,卸压后制动盘转动第一圈时的托滞扭矩不大于3n/m,制动盘转动第10圈时的托滞不大于2n/m。
10.液压刚性方面,在制动钳进油孔处加液压7mpa时,制动钳钳口相应活塞中心处的变形量大于0.35ram,耐压强度方面,在制动钳进油孔处加液压24.5mpa。
附图说明
11.图1为本发明的压盘式制动器铸件铝合金热处理工艺流程图。
12.图2为本发明热处理后性能检测表格。
具体实施方式
13.本发明实施例的一种液压盘式制动器铸件铝合金热处理工艺,工艺包括以下步骤:步骤一:材料成分选择,铸件以重量百分比计,铸件铝合金的材料成分包括:硅si 9~10%;铜cu 1.6~1.8%;锰mn 0.2~0.30%;镁mg 0.3~0.4%;锌zn 0.3~0.4%;铁fe 0~0.2%;余量的锡、铅和杂质,其中杂质总和≤1.0;步骤二:首先将上述原材料混合并进行充分搅拌,然后将水加热到50~60℃后再将搅拌均匀的原材料加入搅拌桶内充分搅拌,待搅拌均匀后目测或手感涂料的稀稠浓度,认为符合使用要求时停止搅拌,放置1-2小时让其各种原材料进行充分溶解,涂料使用前的再处理:将配置好的涂料再次进行充分搅拌,待搅拌均匀后用,400目的筛网进行过滤,然后把经过过滤的涂料装入喷枪待用,金属型腔喷砂工作,金属型喷砂清理时必须对型腔内的各个部位认真清理,特别要注意型腔的各个角落部位,清理过的金属型型腔不得有残留的涂料存在,喷砂完成后,检查金属型的合模情况、顶杆和弹簧的使用情况、金属型型腔和分型面是否完好;步骤三:金属型喷涂处理;将金属型预热到150~250℃,经过预热的金属型型腔、金属型芯及浇冒口部位的型面喷刷涂料;为了保证铸件的光洁度,金属型型腔的涂料层不允许有麻点,如出现个别麻点可用铅笔抹去,如大面积出现麻点金属型应重新清理再次喷涂料,直到满足要求为止,铸件壁越厚,涂料层应减薄;反之,铸件壁越薄,涂料层应增厚,但浇冒口部位的涂料一定要厚,以利于冒口的充分补缩,在浇注过程中如发现涂料脱落应及时补喷,经过喷涂的金属型使用周期不得超过12小时,步骤四:金属型浇注处理:浇注前的准备(1)首先将浇包清理干净,去除粘在其表面的氧化皮和杂物,然后加热到150~250℃后进行涂料涂刷(涂料原材料是石墨),涂料涂刷后再次烘干处理,确保浇包表面干燥后才能使用。
14.(2)金属型的预热温度为150~250℃之间,在实际生产过程中金属型的温度并不是均匀一致的。
15.浇注工艺与步骤(1)先将金属型合好,并用夹口夹紧,保证铝液进入型腔后不会从分型面流出来。
16.(2)浇注工在舀取铝液时必须先用浇包底将铝液表面的氧化皮推开,然后再用浇包不带嘴的一侧舀取铝液,并将在舀取铝液过程中所形成的氧化皮和其它杂物去除干净,避免在浇注时夹杂物进入型腔内形成铸造缺陷。
17.(3)在将铝液浇入金属型之前,首先将金属型倾斜80度左右,然后用浇包嘴贴紧金属型的浇冒口边进行浇注,浇注时铝液进入型腔的流速应遵循先慢
→
中快
→
后慢的原则,金属型倾斜的角度也要平稳缓慢的返回到水平状态,并必须将金属型浇冒口充满为止。
18.(4)金属型浇注完毕后,必须将浇包中剩余的铝液和氧化皮倒入没有精炼的坩埚内或指定的容器内;步骤五:模具浇铸成型:浇铸成型工序中利用坩埚和熔炼工具,保温炉采用温度控制电炉,将熔化温度控制为690~720度,将硅充分熔化;保温炉内铝液温度控制在690~720℃,铝液经过精炼处理,铝液需在30~40分钟内完成;保温炉内铝液温度和质量的控制,现在使用的保温炉是温度控制电炉,温度控制在690~720℃之间,浇注工使用的铝液经过精炼处理合格的铝液,精炼好的铝液应在30~40分钟用完,若出现其它情况铝液放置的时间超过工艺要求时,必须对铝液再次精炼;精炼合格的铝液。
19.步骤六:铝锭融化工艺:高温人工时效处理利用坩埚和熔炼工具,将铝锭熔化,熔化温度设定为690~720度,清除搅拌和坩埚的铁锈和氧化物,将硅充分熔化;步骤七:固溶热处理:包括固溶处理和高温人工时效处理,其中,固溶处理将铸件溶解到固溶体中快速冷却,铸件加热温度为515~525度;加热保温过程中,30~40min缓慢加热至500~515度,保温30~45分钟,经过二次加热保温,10~20min缓慢加热到525~540度,保温5~7小时,60~100度水淬火20~30分钟,高温时效为160~170度;步骤八:金属加工处理;旋压、弯曲、剪切和冲压成型,对铸件外形进行加工;步骤九:喷塑处理将涂料喷涂到铸件的表面,粉末均匀地吸附在铸件表面形成粉状涂层;将粉状涂层经过高温烘烤后流平固化形成保护涂层,附于铸件表面。
20.以上所述仅为本发明的较佳实施例而已,并不用以限制本发明,凡在本发明的精神和原则之内所作的任何修改、等同替换和改进等,均应包含在本发明的保护范围之内。