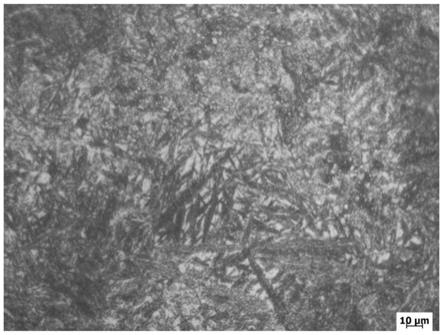
1.本发明涉及一种大型半自磨机用衬板及其制备方法,属于金属铸件制造技术领域。
背景技术:2.经济的发展离不开机械设备的运转,目前在冶金、矿山等领域常用到半自磨机,磨机衬板是一种用来保护磨机筒体,使筒体免受研磨体和物料直接冲击和摩擦,同时提升物料和研磨体,使其在磨机内部具有一定运动形态而增强研磨体对物料的粉碎和研磨作用的磨机关键零部件。在服役过程中磨机衬板会遭到强烈的冲击、磨损甚至腐蚀,对衬板的寿命及工作效率产生了一定的影响。
3.目前广泛使用的衬板材料为高锰钢系列,其屈服强度较低,在使用过程中衬板易变形,时常造成断裂,使用中易变形,导致维护拆卸困难;耐磨铸铁系列虽然具备较高的硬度,但是其脆性大、易断裂,因为不适用于冲击力强的工况条件。随着工业的发展,各类磨机的尺寸也由小变大,对衬板的性能要求也越来越严格,这就需要提出一种具有优异性能的新型衬板材料,以达到提高磨机的粉磨效率、增加产量的同时,减少金属磨损,延长使用寿命的目的。
技术实现要素:4.为了解决上述技术问题,本发明提出了一种大型半自磨机用衬板及其制备方法,该方法制备的衬板具有耐磨性能好,制备方法简单,生产成本低的特点,适合大规模工业化生产。
5.为实现上述目的,本发明提供了如下方案:
6.本发明提供了一种大型半自磨机用衬板,包括以下重量百分比的组分:c:0.60~0.80%、cr:1.80~2.20%、mo:0.30~0.60%、si:0.30~0.80%、mn:0.60~0.80%、ni:0.50~1.00%、v:0.10~0.20%、nb:0.01~0.0.03%、re:0.005~0.015%、s:≤0.025%、p:≤0.025%,余量为fe与不可避免的杂质。
7.进一步地,所述衬板单块重量>2500kg,硬度≥380hbw,冲击功≥40j,抗拉强度>1300mpa,屈服强度>1000mpa,断裂伸长率>7%,断面收缩率>12%。
8.本发明还提供了一种所述的大型半自磨机用衬板的制备方法,包括以下步骤:
9.(1)熔炼:将原料合金按照重量配比混合熔炼得到钢水,将所述钢水浇铸成型得到衬板铸件;
10.(2)热处理:将步骤(1)得到的衬板铸件依次进行正火处理和回火处理,得到所述大型半自磨机用衬板。
11.进一步地,步骤(1)中各组分在熔炼前均经过烘烤处理。
12.进一步地,步骤(1)中熔炼的温度为≥1600℃。
13.进一步地,步骤(1)中熔炼过程中喂铝线进行脱氧预处理和终脱氧,出钢时采用稀
土合金及硅钙合金进行孕育变质处理。采用炉外精炼技术,使夹杂物上浮,保证钢水纯净度。
14.进一步地,步骤(2)中所述正火处理具体包括:将步骤(1)得到的衬板胚体由250~300℃第一次升温至640~660℃,保温2h后继续第二次升温至920~940℃保温6h,之后空气冷却至200~250℃。
15.进一步地,正火处理中所述第一次升温的升温速度为≤80℃/h,第二次升温的升温速率为≤80℃/h。
16.进一步地,步骤(2)中所述回火处理具体包括:将正火处理后的衬板胚体第一次升温至340~360℃,保温2h后继续第二次升温至600~640℃保温10h,之后空气冷却至≤50℃。
17.进一步地,回火处理中所述第一次升温的升温速度为≤50℃/h,第二次升温的升温速率为≤50℃/h。
18.本发明公开了以下技术效果:
19.1)本发明的衬板调低了含碳量,但是增加了cr、ni、mo、si等的用量,从而增强衬板的强度、硬度以及耐磨性能,提高合金化衬板材料的韧性,同时起到细化晶粒的效果,v、nb元素的加入使显微组织进一步得到细化的同时提高其回火稳定性,抑制碳化物粗化,增强弥散强化作用,使衬板同时具备良好的强韧性,而s和p作为有害元素,将其含量降到了最低,安全性更高。
20.2)本发明的衬板的厚度达到了240mm,单位面积重量>2500kg,从而降低使用过程中的磨损率,并通过原料成分及配比的调整,结合热处理工艺方法,使制备得到的衬板耐磨性能优异,综合力学性能良好,其硬度达到了380hbw,冲击功达到了40j,抗拉强度达到了1300mpa,屈服强度达到了1000mpa,断裂伸长率达到了7%,断面收缩率达到了12%。
附图说明
21.为了更清楚地说明本发明实施例或现有技术中的技术方案,下面将对实施例中所需要使用的附图作简单地介绍,显而易见地,下面描述中的附图仅仅是本发明的一些实施例,对于本领域普通技术人员来讲,在不付出创造性劳动性的前提下,还可以根据这些附图获得其他的附图。
22.图1为衬板的正火处理工艺图;
23.图2为衬板的回火处理工艺图;
24.图3为实施例1制备得到的衬板的金相组织图;
25.图4为实施例2制备得到的衬板的金相组织图。
具体实施方式
26.现详细说明本发明的多种示例性实施方式,该详细说明不应认为是对本发明的限制,而应理解为是对本发明的某些方面、特性和实施方案的更详细的描述。
27.应理解本发明中所述的术语仅仅是为描述特别的实施方式,并非用于限制本发明。另外,对于本发明中的数值范围,应理解为还具体公开了该范围的上限和下限之间的每个中间值。在任何陈述值或陈述范围内的中间值以及任何其他陈述值或在所述范围内的中
间值之间的每个较小的范围也包括在本发明内。这些较小范围的上限和下限可独立地包括或排除在范围内。
28.除非另有说明,否则本文使用的所有技术和科学术语具有本发明所述领域的常规技术人员通常理解的相同含义。虽然本发明仅描述了优选的方法和材料,但是在本发明的实施或测试中也可以使用与本文所述相似或等同的任何方法和材料。本说明书中提到的所有文献通过引用并入,用以公开和描述与所述文献相关的方法和/或材料。在与任何并入的文献冲突时,以本说明书的内容为准。
29.在不背离本发明的范围或精神的情况下,可对本发明说明书的具体实施方式做多种改进和变化,这对本领域技术人员而言是显而易见的。由本发明的说明书得到的其他实施方式对技术人员而言是显而易见得的。本发明说明书和实施例仅是示例性的。
30.关于本文中所使用的“包含”、“包括”、“具有”、“含有”等等,均为开放性的用语,即意指包含但不限于。
31.本发明实施例中所用合金块铬铁、钼铁、硅铁、锰铁及废钢,合金块大小适中,并进行分批烘烤,熔炼时先加废钢,铬铁、钼铁、硅铁、锰铁等合金元素在熔炼的中后期加入,调整钢水成分至预期成分,具体成分为c:0.60~0.80%、cr:1.80~2.20%、mo:0.30~0.60%、si:0.30~0.80%、mn:0.60~0.80%、ni:0.50~1.00%、v:0.10~0.20%、nb:0.01~0.0.03%、re:0.005~0.015%、s:≤0.025%、p:≤0.025%,余量为fe与不可避免的杂质。
32.以下实施例中的合金块在熔炼前均经过烘烤处理。
33.本发明实施例正火处理工艺见图1,回火处理工艺见图2。
34.以下通过实施例对本发明的技术方案做进一步说明。
35.实施例1
36.(1)熔炼:将合金块依次加入中频炉,并将钢水成分调整至预期成分,加热至1550~1580℃时,喂铝线进行脱氧预处理,加热至1600~1650℃时,喂铝线进行终脱氧,温度在1600℃时出炉,出炉时加入钢水总质量的0.1%~0.5%的稀土合金及硅钙合金进行孕育变质处理,并采用炉外精炼技术,使夹杂物上浮,得到纯净的钢水,将钢水浇筑成型得到衬板铸件;
37.(2)热处理
38.正火处理:将加热炉预热至250~300℃后放入步骤(1)得到的衬板铸件,以60~80℃/h升温至640~660℃,保温2h后继续以30~50℃/h升温至920~940℃保温6h,随后将衬板从加热炉中取出,空气冷却至200~250℃;
39.回火处理:将加热炉预热至250~300℃后放入正火处理后的衬板,以30~50℃/h升温至340~360℃,保温2h后继续以30~50℃/h升温至600~640℃保温10h,随后将衬板从加热炉中取出,空气冷却至室温,即可得到大型半自磨机用衬板。
40.制备得到的衬板包括以下重量百分比的组分:c:0.60~0.80%、cr:1.80~2.20%、mo:0.30~0.60%、si:0.30~0.80%、mn:0.60~0.80%、ni:0.50~1.00%、v:0.10~0.20%、nb:0.01~0.0.03%、re:0.005~0.015%、s:≤0.025%、p:≤0.025%,余量为fe与不可避免的杂质。
41.制备得到的衬板厚度为241mm,单位面积重量为2533kg,采用hsb-150电动布氏硬
度仪测量硬度,压头选择5mm硬质合金球,加载力为kgf,保载时间20s硬度测得为380hbw,冲击试样采用标准无缺口冲击试样,无缺口冲击功44j,拉伸试样为圆棒状标准试样,抗拉强度达到1315mpa。
42.本实施例制备得到的大型半自磨机用衬板的金相组织图见图3,由图3可以看出组织为回火索氏体+回火马氏体+碳化物。
43.实施例2
44.(1)熔炼:将合金块依次加入中频炉,并将钢水成分调整至预期成分,加热至1550~1580℃时,喂铝线进行脱氧预处理,加热至1600~1650℃时,喂铝线进行终脱氧,温度在1600℃时出炉,出炉时加入钢水总质量的0.1%~0.5%的稀土合金及硅钙合金进行孕育变质处理,并采用炉外精炼技术,使夹杂物上浮,得到纯净的钢水,将钢水浇筑成型得到衬板铸件;
45.(2)热处理
46.正火处理:将加热炉预热至250~300℃后放入步骤(1)得到的衬板铸件,以60~80℃/h升温至640~660℃,保温2h后继续以30~50℃/h升温至920~940℃保温6h,随后将衬板从加热炉中取出,空气冷却至200~250℃;
47.回火处理:将加热炉预热至250~300℃后放入正火处理后的衬板,以30~50℃/h升温至340~360℃,保温2h后继续以30~50℃/h升温至600~640℃保温10h,随后将衬板从加热炉中取出,空气冷却至室温,即可得到大型半自磨机用衬板。
48.制备得到的衬板包括以下重量百分比的组分:c:0.60~0.80%、cr:1.80~2.20%、mo:0.30~0.60%、si:0.30~0.80%、mn:0.60~0.80%、ni:0.50~1.00%、v:0.10~0.20%、nb:0.01~0.0.03%、re:0.005~0.015%、s:≤0.025%、p:≤0.025%,余量为fe与不可避免的杂质。
49.制备得到的衬板厚度为246mm,单位面积重量为2612kg,硬度为393hbw,无缺口冲击功62j,抗拉强度达到1462mpa。
50.本实施例制备得到的大型半自磨机用衬板的金相组织图见图4,由图4可以看出组织为回火索氏体+回火马氏体+碳化物。
51.实施例3
52.(1)熔炼:将合金块依次加入中频炉,并将钢水成分调整至预期成分,加热至1550~1580℃时,喂铝线进行脱氧预处理,加热至1600~1650℃时,喂铝线进行终脱氧,温度在1600℃时出炉,出炉时加入钢水总质量的0.1%~0.5%的稀土合金及硅钙合金进行孕育变质处理,并采用炉外精炼技术,使夹杂物上浮,得到纯净的钢水,将钢水浇筑成型得到衬板铸件;
53.(2)热处理
54.正火处理:将加热炉预热至250~300℃后放入步骤(1)得到的衬板铸件,以60~80℃/h升温至640~660℃,保温2h后继续以30~50℃/h升温至920~940℃保温6h,随后将衬板从加热炉中取出,空气冷却至200~250℃;
55.回火处理:将加热炉预热至250~300℃后放入正火处理后的衬板,以30~50℃/h升温至340~360℃,保温2h后继续以30~50℃/h升温至600~640℃保温10h,随后将衬板从加热炉中取出,空气冷却至室温,即可得到大型半自磨机用衬板。
56.制备得到的衬板包括以下重量百分比的组分:c:0.60~0.80%、cr:1.80~2.20%、mo:0.30~0.60%、si:0.30~0.80%、mn:0.60~0.80%、ni:0.50~1.00%、v:0.10~0.20%、nb:0.01~0.0.03%、re:0.005~0.015%、s:≤0.025%、p:≤0.025%,余量为fe与不可避免的杂质。
57.制备得到的衬板厚度为243mm,单位面积重量为2576kg,硬度为388hbw,无缺口冲击功57j,抗拉强度达到1381mpa。
58.对比例1
59.同实施例1,其区别仅在于,不加入含v、nb的合金块使衬板中不含v和nb组分。制备得到的衬板厚度为244mm,单位面积重量为2583kg,硬度为345hbw,无缺口冲击功28j,抗拉强度达到1046mpa。
60.对比例2
61.同实施例1,其区别仅在于,未进行步骤(2)的回火处理。制备得到的衬板厚度为240mm,单位面积重量为2535kg,硬度为420hbw,无缺口冲击功14j,抗拉强度达到1150mpa。
62.对比例3
63.同实施例1,其区别仅在于,步骤(2)中的正火处理具体为:将加热炉预热至250℃后放入步骤(1)得到的衬板胚体,以90℃/h升温至850℃,保温2h后继续以80℃/h升温至940℃保温9h,随后将衬板从加热炉中取出,空气冷却至200℃。制备得到的衬板厚度为242mm,单位面积重量为2560kg,硬度为335hbw,无缺口冲击功35j,抗拉强度达到1038mpa。
64.对比例4
65.同实施例1,其区别仅在于,将加热炉预热至300℃后放入正火处理后的衬板,以50℃/h升温至500℃,保温4h后继续以50℃/h升温至640℃保温8h,随后将衬板从加热炉中取出,空气冷却至250℃,即可得到大型半自磨机用衬板。制备得到的衬板厚度为248mm,单位面积重量为2605kg,硬度为324hbw,无缺口冲击功43j,抗拉强度达到1065mpa。
66.以上所述的实施例仅是对本发明的优选方式进行描述,并非对本发明的范围进行限定,在不脱离本发明设计精神的前提下,本领域普通技术人员对本发明的技术方案做出的各种变形和改进,均应落入本发明权利要求书确定的保护范围内。