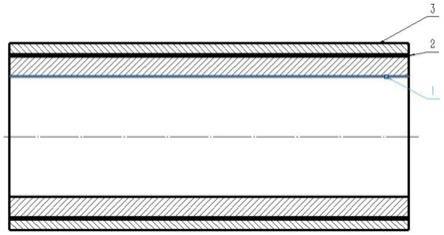
1.本发明属于锅炉管加工制造技术领域,更具体地说,涉及一种用于超临界、超超临界锅炉的复合锅炉管。
背景技术:2.超超临界燃煤发电技术备受各国重视,目前超超临界压力锅炉内的主蒸汽压力已高达30mpa,预计在今后二三十年内,燃煤电站锅炉内蒸汽温度将再提高50~100℃,因此更高性能的超超临界锅炉管研发迫在眉睫。目前锅炉管用耐热钢主要有含2%cr的t/p22、t/p23低合金铁素体钢,含9%cr的t/p91 和t/p92高cr铁素体钢、含12%cr的hcm12和hcm12a高cr铁素体钢、以及以tp347h为代表的奥氏体不锈钢等。锅炉管性能要求更高,企业面临的降成本压力不断加大,因此双金属锅炉复合管研制正受到越来越多的关注。实用新型(cn202020993279.9)提供了一种高压锅炉用内衬不锈钢复合管,为解决内衬不锈钢管的高温承受能力,本发明在内衬不锈钢复合管内部中间开设一个液氮降温空腔,然后将液氮注入空腔内部,通过液氮自身低温对内衬不锈钢复合管快速降温,进而使内部压力降低,提高本体不锈钢管的寿命。但是该发明中内衬不锈钢管本体内部液氮空腔的存在,必然会严重降低不锈钢管的综合力学性能。
3.德国、日本提出的一种双金属锅炉复合管的生产工艺,具体工艺过程如下:首先他们将两种钢管紧配合镶套在一起,然后在真空下将内外层金属通过高温原子扩散方式进行界面粘接,制得外tp304l、内gr.a-1双金属管,但该工艺制得的双金属锅炉复合管熔合界面很薄,加工效率较低且加工过程中的氧化物可能会造成界面不能完全熔合。发明(cn200910077497.6)提出了一种“锅炉用双金属无缝钢管的复合管坯及其生产方法”,利用离心浇铸方法将依次成型外层金属管、过渡层金属管和内层金属管,不同种金属管层之间属于冶金熔合,但是该方法在不同层金属管材成型时,需要频繁更换所需的表面熔融保护渣,且制备出的复合管坯还需要通过后续挤压或轧制加工才能制造成锅炉用双金属无缝钢管。这两种生产工艺制得的双金属锅炉复合管由于内部两种金属层所占比例基本相当,因此属于异种金属管,在服役过程中都很容易出现因不同金属层自身的热膨胀系数差异而导致的界面分层,即界面结合失效破环现象,往往会造成管道突发破裂。
4.为解决双金属锅炉复合管界面分层失效破坏的难题,瑞典的山德维克公司提出了利用喷射成型法,在碳钢锅炉管基体外表面复合沉积一薄层奥氏体超低碳不锈钢sanicro28,两者之间的界面同样属于冶金结合,但外表层金属厚度占比较小,复合管以内层碳钢管为主,有效克服了服役过程中的内外层金属界面的开裂风险,复合管可以较为方便的进行机械加工、弯曲变形及焊接成型等,同时复合管的耐蚀性能优异。但喷射成型法需要在真空或惰性气体保护环境下进行,喷射沉积复合管的制备严重受制于真空环境空间大小,喷射设备投入大、生产效率较低,制造成本较高。如何显著提升超临界、超超临界锅炉管的使用寿命,并降低生产成本,是业界致力追求的目标。
技术实现要素:5.本发明针对现有技术中的不足,提出了一种用于超临界、超超临界锅炉的复合锅炉管,通过具有优异抗高温氧化性、良好热导系数的特种高熵合金熔覆层与适用于超临界、超超临界的耐热钢管基体的高强高韧性相统一的结构设计,将高熵合金感应熔覆工艺用于超临界、超超临界锅炉管的制备,克服了服役过程中因内外层金属热膨胀差异引起的界面结合失效破环,本发明克服现有整体镍基合金锅炉管的高成本、现有双金属复合管所成型工艺复杂及抗高温氧化性能差的等问题,并实现了高熵合金熔覆层与基体界面界面的强冶金-化学结合,使得本发明的复合锅炉管满足了超(超)临界锅炉管的恶劣工况条件,服役寿命得到显著提升。
6.为达到上述目的,本发明采用如下技术方案:
7.一种用于超临界、超超临界锅炉的复合锅炉管,包括材料为适用于超临界、超超临界锅炉的耐热钢管内基体、通过高熵合金熔覆获得的外层以及内基体与外层间强冶金-化学结合界面。所述的高熵合金熔覆获得的外层是通过感应熔覆工艺实现的。
8.进一步,所述高熵合金熔覆层厚度为0.3~1.5mm;所述界面层厚度在 3um~20um之间,界面层是高熵合金熔覆层及锅炉管基体经感应熔覆工艺形成的以冶金-化学结合为主的过渡层。
8.进一步,所述的高熵合金熔覆层所需要的粉末是由0.6~1.5wt.%硼元素、 0.6~1.5wt.%硅元素、0.2~0.8wt.%钼元素以及等摩尔比的铁、钴、镍及铬元素组成的自熔性高熵合金粉末。
9.进一步,所述的一种用于超临界、超超临界锅炉的复合锅炉管的制作方法,主要包括以下步骤:
10.s1适用于工况条件的耐热钢管的材质及规格选型:根据超临界或超超临界锅炉管的工况条件,选用适用的耐热钢管作为锅炉管基体。
11.s2锅炉管基体表面粗糙活化处理:将所述的锅炉管基体基体外圆进行喷砂洁净粗糙化处理,除油除锈并粗糙化,达到sa3.2的要求。
12.s3高熵合金涂层预制备:将指定的粉末对的锅炉管基体基体外圆,通过火焰喷涂的优化工艺,喷涂高熵合金涂层,达到规定的涂层厚度和质量。
13.s4涂层熔覆处理:采用感应熔覆方式对高熵合金涂层进行强化处理,使涂层本身形成化学及冶金的复合合成,并与锅炉钢基体形成强界面结合。感应熔覆温度为1050~1200℃之间。至此完成超临界、超超临界锅炉管的整体制作过程。有益效果与现有技术相比,本发明的有益效果:本发明提供的一种用于超临界、超超临界锅炉的复合锅炉管,通过具有优异抗高温氧化性、良好热导系数的特种高熵合金熔覆层与适用于超临界、超超临界的耐热钢管基体的高强高韧性相统一的结构设计,将高熵合金感应熔覆工艺用于超临界、超超临界锅炉管的制备,克服了服役过程中因内外层金属热膨胀差异引起的界面结合失效破环,有效降低了内外层界面服役过程中的时效破坏风险,制备出的锅炉复合管具有优异的高温力学及耐腐蚀、抗氧化和高热导率等综合性能,服役寿命显著提升。图1为本发明的超临界、超超临界锅炉复合管结构示意图;
图2为本发明的超临界、超超临界锅炉复合管的工艺流程示意图。
具体实施方式
14.为了使本发明实现的技术手段、创作特征、达成目的与功效易于明白了解,下面结合具体图示,进一步阐述本发明。
15.实施例1一种用于超临界、超超临界锅炉的复合锅炉管,包括材料t/p23 低合金铁素体钢管内基体(1)、通过高熵合金熔覆获得的外层(2)以及内基体与外层间强冶金-化学结合界面(3)。所述的高熵合金熔覆获得的外层(2)是通过感应熔覆工艺实现的。
16.进一步,所述高熵合金熔覆层(3)厚度为0.3~1.5mm;所述界面层(2)厚度在3um~20um之间,界面层(2)是高熵合金熔覆层(3)及锅炉管基体(1)经感应熔覆工艺形成的以冶金-化学结合为主的过渡层。
17.进一步,所述的高熵合金熔覆层(3)所需要的粉末是由0.6~1.5wt.%硼元素、0.6~1.5wt.%硅元素、0.2~0.8wt.%钼元素以及等摩尔比的铁、钴、镍及铬元素组成的自熔性高熵合金粉末。
18.进一步,所述的一种用于超临界、超超临界锅炉的复合锅炉管的制作方法,主要包括以下步骤:
19.s1适用于工况条件的耐热钢管的材质及规格选型:选用t/p23低合金铁素体钢管作为锅炉管基体。
20.s2锅炉管基体表面粗糙活化处理:将所述的锅炉管基体基体(1)外圆进行喷砂洁净粗糙化处理,除油除锈并粗糙化,达到sa3.2的要求。
21.s3高熵合金涂层预制备:将指定的粉末对的锅炉管基体基体外圆,通过火焰喷涂的优化工艺,喷涂高熵合金涂层,达到规定的涂层厚度和质量。
22.s4涂层熔覆处理:采用感应熔覆方式对高熵合金涂层进行强化处理,使涂层本身形成化学及冶金的复合合成,并与锅炉钢基体形成强界面结合。感应熔覆温度为1050~1200℃之间。至此完成超临界、超超临界锅炉管的整体制作过程。
23.实施例2:一种用于超临界、超超临界锅炉的复合锅炉管,包括材料 t/p92高cr铁素体钢管内基体(1)、通过高熵合金熔覆获得的外层(2)以及内基体与外层间强冶金-化学结合界面(3)。所述的高熵合金熔覆获得的外层(2)是通过感应熔覆工艺实现的。
24.进一步,所述高熵合金熔覆层(3)厚度为0.3~1.5mm;所述界面层(2)厚度在3um~20um之间,界面层(2)是高熵合金熔覆层(3)及锅炉管基体(1)经感应熔覆工艺形成的以冶金-化学结合为主的过渡层。
25.进一步,所述的高熵合金熔覆层(3)所需要的粉末是由0.6~1.5wt.%硼元素、0.6~1.5wt.%硅元素、0.2~0.8wt.%钼元素以及等摩尔比的铁、钴、镍及铬元素组成的自熔性高熵合金粉末。
26.进一步,所述的一种用于超临界、超超临界锅炉的复合锅炉管的制作方法,主要包括以下步骤:
27.s1适用于工况条件的耐热钢管的材质及规格选型:选用t/p92高cr 铁素体钢管作为锅炉管基体。
28.s2锅炉管基体表面粗糙活化处理:将所述的锅炉管基体基体外圆进行喷砂洁净粗
糙化处理,除油除锈并粗糙化,达到sa3.2的要求。
29.s3高熵合金涂层预制备:将指定的粉末对的锅炉管基体基体外圆,通过火焰喷涂的优化工艺,喷涂高熵合金涂层,达到规定的涂层厚度和质量。
30.s4涂层熔覆处理:采用感应熔覆方式对高熵合金涂层进行强化处理,使涂层本身形成化学及冶金的复合合成,并与锅炉钢基体形成强界面结合。感应熔覆温度为1050~1200℃之间。至此完成超临界、超超临界锅炉管的整体制作过程。
31.实施例3:一种用于超临界、超超临界锅炉的复合锅炉管,包括材料 tp347h奥氏体不锈钢管内基体(1)、通过高熵合金熔覆获得的外层(2)以及内基体与外层间强冶金-化学结合界面(3)。所述的高熵合金熔覆获得的外层(2)是通过感应熔覆工艺实现的。
32.进一步,所述高熵合金熔覆层(3)厚度为0.3~1.5mm;所述界面层(2)厚度在3um~20um之间,界面层(2)是高熵合金熔覆层(3)及锅炉管基体(1)经感应熔覆工艺形成的以冶金-化学结合为主的过渡层。
33.进一步,所述的高熵合金熔覆层(3)所需要的粉末是由0.6~1.5wt.%硼元素、0.6~1.5wt.%硅元素、0.2~0.8wt.%钼元素以及等摩尔比的铁、钴、镍及铬元素组成的自熔性高熵合金粉末。
34.进一步,所述的一种用于超临界、超超临界锅炉的复合锅炉管的制作方法,主要包括以下步骤:
35.s1适用于工况条件的耐热钢管的材质及规格选型:选用tp347h奥氏体不锈钢管作为锅炉管基体。
36.s2锅炉管基体表面粗糙活化处理:将所述的锅炉管基体基体外圆进行喷砂洁净粗糙化处理,除油除锈并粗糙化,达到sa3.2的要求。
37.s3高熵合金涂层预制备:将指定的粉末对的锅炉管基体基体外圆,通过火焰喷涂的优化工艺,喷涂高熵合金涂层,达到规定的涂层厚度和质量。
38.s4涂层熔覆处理:采用感应熔覆方式对高熵合金涂层进行强化处理,使涂层本身形成化学及冶金的复合合成,并与锅炉钢基体形成强界面结合。感应熔覆温度为1050~1200℃之间。至此完成超临界、超超临界锅炉管的整体制作过程。以上公开的仅为本发明的两个具体实施例,但是,本发明并非局限于此,任何本领域的技术人员能思之的变化都应落入本发明的保护范围之内。