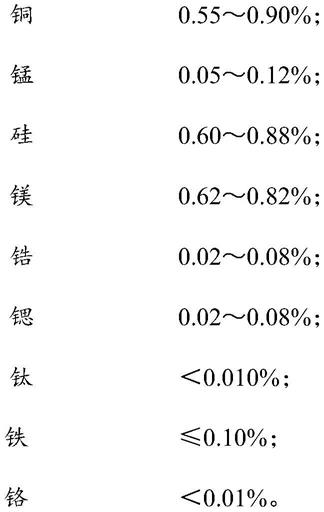
1.本发明属于铝合金技术领域,具体涉及一种铝基材料及其制备方法和应用。
背景技术:2.日常生活中,铝合金随处可见,例如电子产品的外壳以及建筑装饰用品。使用铝合金制造的电子产品外壳,通常需满足以下要求:优美的外观、优异的变形加工性能、抗跌落性能、合适的强度和优异的耐腐蚀性能。
3.其中,基于美观及耐腐蚀的要求,通常会对铝合金进行表面阳极处理,并且为手机机(外壳)进行上色处理,表面阳极处理是具体是在铝合金表面通过电流作用形成一层氧化物膜,通过着色,该氧化物膜可具有颜色丰富、色泽优美、电绝缘性好、坚硬耐磨以及抗腐蚀性极高等优点。关于变形加工性能:在铝合金外壳加工中,冲压是比较基础、常见的手段,冲压与数控加工等工艺组合可以得到各种产品的铝外壳,同时在制备过程中还会辅以拉伸、弯折等操作。因此用于电子产品外壳的铝合金需要满足优异的拉伸、弯折等变形加工性能。关于抗跌落性能和强度,是保护电子产品所需满足的基本要求。
4.但是现有的铝合金通常难以同时满足电子产品外壳要求的强度、外观、变形和耐腐蚀性能。
技术实现要素:5.本发明旨在至少解决上述现有技术中存在的技术问题之一。为此,本发明提出一种铝基材料,通过成分的配比,能够改善所得铝基材料的变形性能、耐腐蚀性能、外观性能和力学性能。
6.本发明还提出一种上述铝基材料的制备方法。
7.本发明还提出上述铝基材料的应用。
8.根据本发明的一个方面,提出了一种铝基材料,组分包括合金元素和铝;按占所述铝基材料的质量百分数计,所述合金元素包括:
[0009][0010]
根据本发明的一种优选的实施方式,至少具有以下有益效果:
[0011]
(1)所述铝基材料的组分中,合金元素锶(sr)和锆(zr)均能有效细化晶粒,改善晶界析出,提高晶间腐蚀性能,两者结合后性能更加突出。
[0012]
(2)在所述铝基材料中,钛(ti)元素主要以tib2颗粒存在,其大小在1μm左右,具体作用为细化晶粒,提升抗腐蚀性能;但是钛元素一旦过量,就会发生团聚,从而成为影响铝基材料影响氧化效果的杂质,即影响了所得铝基材料的外观;本发明通过限制其用量,平衡了其抗腐蚀性能和外观之间的关系。
[0013]
(3)铜(cu)在本发明提供的铝基材料体系中,能提高强化相的弥散度,也能起到固溶强化的效果,使铝基材料具有良好的综合性能;过量的cu不仅会恶化耐腐蚀性能,还增加焊接热裂纹倾向、挤压淬火敏感性以及挤压变形抗力,严重影响挤压性能与焊接性能,本发明在保证高强度的前提下控制了cu的添加量。
[0014]
(4)细晶有利于提升所得铝基材料的抗拉性能和弯折性能等变形性能,因此锶、锆、钛、锰等具有细化晶粒作用的合金元素,可以提升所得铝基材料的挤压、拉伸等变形性能;
[0015]
但是如果上述元素含量过高,所得铝基材料在变形、受热过程中,晶粒会融合长大,但是不能再结晶,也会导致晶粒粗大,影响所得铝基材料的外观、耐腐蚀性能以及折弯性能。
[0016]
(5)硅(si)和镁(mg)可以析出强化相,保证所得成铝基材料的力学性能。
[0017]
(6)铁(fe)在铝基材料中主要形成alfesi(mn)颗粒,经过均匀化处理后形成球状的颗粒,在后续的加工过程中能有效的细化晶粒,但是本发明为了能获得更好的氧化效果,需要尽可能减少不能固溶的相,以免导致氧化膜的不连续,导致氧化效果不佳,所以控制了fe含量的上限值。
[0018]
当所述铝基材料中含有铁(fe)和铬(cr)时,锰(mn)一方面可以促使针状fe相球化,提升所得铝基材料的挤压等变形性能,另一方面与cr发生协同作用后还可以抑制所得铝基材料在受热、变形过程中的再结晶。
[0019]
在本发明的一些实施方式中,所述锰、锶和锆的质量百分数之和≤0.20%。
[0020]
在本发明的一些实施方式中,所述锶和锆的质量百分数之和≤0.12%。
[0021]
在本发明的一些实施方式中,所述铝基材料的组分还包括杂质。
[0022]
在本发明的一些实施方式中,所述杂质包括银(ag)、钙(ca)、磷(p)、钠(na)和钴(co)等。
[0023]
在本发明的一些实施方式中,单种所述杂质的质量百分数≤0.05%。
[0024]
在本发明的一些实施方式中,所有所述杂质的质量百分数之和≤0.15%。
[0025]
在本发明的一些实施方式中,所述铝基材料t6状态下抗拉强度rm≥360mpa。
[0026]
在本发明的一些优选的实施方式中,所述铝基材料t6状态下抗拉强度rm≥370mpa。
[0027]
在本发明的一些实施方式中,所述铝基材料t6状态下屈服强度rp0.2≥340mpa。
[0028]
在本发明的一些实施方式中,所述铝基材料t6状态下屈服强度rp0.2≥350mpa。
[0029]
在本发明的一些实施方式中,所述铝基材料t6状态下断后伸长率δ≥10%。
[0030]
在本发明的一些实施方式中,所述铝基材料满足100mm跌落测试要求。
[0031]
在本发明的一些实施方式中,所述铝基材料的晶间腐蚀<0.03mm。
[0032]
根据本发明的再一个方面,提出了所述铝基材料的制备方法,包括如下步骤:
[0033]
s1.向铝熔体中添加含有所述合金元素的添加剂,得合金化熔体;
[0034]
s2.铸造所述合金化熔体,得铸锭;
[0035]
s3.对步骤s2所得铸锭进行三级均匀化处理;
[0036]
s4.对步骤s3所得铸锭进行挤压变形并进行人工时效处理。
[0037]
根据本发明的一种优选的实施方式的制备方法,至少具有以下有益效果:
[0038]
根据所述铝基材料的成分特设定三级均匀化处理,具体第一级均匀化处理使mn、cr、zr、sr等元素反应、析出弥散相,细化晶粒,进而提升耐腐蚀性能和外观性能;第二级均匀化处理析出mg2si强化相,提升强度;也避免了高温的共晶反应发生过烧,能将均匀化处理温度提高到更高的温度;第三级均匀化可以消除晶内偏析、铸造应力以及球化含fe相,提升所得铝基材料的综合性能,即可获得更好的均匀化。
[0039]
在本发明的一些实施方式中,步骤s1中,所述铝熔体的获取方法为在750-800℃熔化铝锭。
[0040]
由于zr合金的难熔性,特将熔化温度提高致750-800℃,更有助于微量元素的熔化与均匀。
[0041]
在本发明的一些实施方式中,步骤s1中,所述合金元素对应的添加剂为:
[0042]
所述硅的添加剂包括al-si中间合金;
[0043]
所述镁的添加剂包括镁锭;
[0044]
所述锶的添加剂包括al-sr中间合金;
[0045]
所述锆的添加剂包括al-zr中间合金;
[0046]
所述铜的添加剂包括紫铜;
[0047]
所述锰的添加剂包括锰剂;
[0048]
所述钛的添加剂包括al-ti-b中间合金。
[0049]
在本发明的一些实施方式中,步骤s1中,具体包括如下步骤:
[0050]
s1a.熔化铝锭;
[0051]
s1b.向步骤s1a所得熔体中添加al-si中间合金、镁锭、al-sr以及al-zr中间合金、紫铜和锰剂;
[0052]
s1c.向步骤s1b所得熔体中添加精炼剂,精炼;
[0053]
s1d.对步骤s1c所得熔体进行成分调整。
[0054]
在本发明的一些实施方式中,步骤s1c中,所述精炼剂与步骤s1b所得熔体的质量比约为2~2.5kg:1吨。
[0055]
在本发明的一些实施方式中,步骤s1c中,所述精炼的温度为730-750℃。
[0056]
在本发明的一些实施方式中,步骤s1c中,所述精炼的时长为30~40min。
[0057]
在本发明的一些实施方式中,步骤s1c中,所述精炼的过程中需从熔体的底部通入氩气,对所得熔体进行搅拌、排气和扒渣操作。
[0058]
步骤s1d中,所述成分调整的作用是确保所得熔体与所要制备的铝基材料的组分相同(除钛外)。
[0059]
在本发明的一些实施方式中,步骤s1在蓄热式火焰反射节能炉中进行。
[0060]
在本发明的一些实施方式中,步骤s1和步骤s2之间的时间间隔≤10min。
[0061]
通常在合金熔融后,需进行静置处理,以便于气渣有效分离,但是本发明的铝基材料中包括sr、zr元素,限制步骤s1和步骤s2间的时间间隔,可避免sr、zr元素和si等元素发生团聚。
[0062]
在本发明的一些实施方式中,步骤s2中,所述铸造的过程中,需向步骤s1所得熔体中添加al-ti-b合金。以达到细晶目的。
[0063]
在本发明的一些实施方式中,步骤s2中,所述铸造还包括将添加al-ti-b合金后的熔体依次进行除气与管式过滤。
[0064]
在本发明的一些实施方式中,步骤s2中,所述铸造的方法为半连续水冷铸造。
[0065]
在本发明的一些实施方式中,步骤s2中,所述铸造的温度为680~700℃。
[0066]
在本发明的一些实施方式中,步骤s3中,所述三级均匀化处理,包括依次在400~450℃、550~560℃和560~570℃进行三段恒温处理。
[0067]
在铝基材料中,锶通常形成al4sr,该物质的析出温度在300-450℃区间,mn、cr、zr等元素的析出温度也与之相仿,因此第一级均匀化处理的温度选在此温度附近。
[0068]
在本发明的一些实施方式中,所述三级均匀化处理中,400~450℃的恒温时长为2~4h。
[0069]
在本发明的一些实施方式中,所述三级均匀化处理中,550~560℃的恒温时长为2~3h。
[0070]
在本发明的一些实施方式中,所述三级均匀化处理中,560~570℃的恒温时长为6~12。
[0071]
在本发明的一些实施方式中,所述三级均匀化处理的冷却方法为水雾冷却。
[0072]
在本发明的一些实施方式中,步骤s4中,所述挤压变形的温度为530~550℃。
[0073]
在本发明的一些实施方式中,步骤s4中,所述人工时效处理的温度为165~185℃。
[0074]
在本发明的一些实施方式中,步骤s4中,所述人工时效处理的时长为6~12h。
[0075]
根据本发明的再一个方面,提出了所述铝基材料或所述制备方法制得的铝基材料
在制备电子产品中的应用。
[0076]
在本发明的一些实施方式中,所述电子产品包括智能手机,智能手表和平板电脑中的至少一种。
[0077]
根据本发明的再一个方面,提出了所述铝基材料或所述制备方法制得的铝基材料在家居装饰、工业机械和建筑领域中的应用。
具体实施方式
[0078]
以下将结合实施例对本发明的构思及产生的技术效果进行清楚、完整地描述,以充分地理解本发明的目的、特征和效果。显然,所描述的实施例只是本发明的一部分实施例,而不是全部实施例,基于本发明的实施例,本领域的技术人员在不付出创造性劳动的前提下所获得的其他实施例,均属于本发明保护的范围。
[0079]
实施例1
[0080]
本实施例制备了一种铝基材料,具体过程为:
[0081]
s1.获得熔体:
[0082]
s1a.将铝锭装入蓄热式火焰反射节能炉中加热到780-800℃进行熔化(熔化时温度不稳定,设定值为790℃,但实际上会在该值
±
10℃范围内浮动);
[0083]
s1b.待铝锭完全熔化后按表1所示比例加入al-si中间合金、镁锭、al-sr以及al-zr中间合金、紫铜、锰剂,对铝熔体进行合金化;
[0084]
s1c.按2kg精炼剂:1吨熔体的比例,向步骤s1b所得熔体中加入精炼剂(牌号为promag ri粒状精炼剂,符合标准ys/t491-2005《变形铝及铝合金用熔剂》),进行精炼,精炼温度730-750℃,精炼时间40min,在精炼的同时通过炉底透气砖向铝熔体中通入高纯氩气进行搅拌、排气,然后扒渣;
[0085]
s1d.从步骤s1c所得熔体中取样,并分析化学成分,如果其中的成分偏离了表1的设计成分,则进行成分微调;
[0086]
s2.铸造:
[0087]
在步骤s1完成10min内,对步骤s1所得熔体进行铸造;
[0088]
铸造过程中按ti占熔体0.010wt%的数量在线添加al-ti-b合金进行晶粒细化,然后采用双级除气与rd级别管式过滤所得熔体,最后在680~700℃(设定温度为690℃,实际温度在上述温度范围内浮动),采用半连续水冷铸造法获得圆铸锭;
[0089]
s3.均匀化处理:
[0090]
将步骤s2所得铸锭先升温至400℃保温4h,再升温至550℃保温2h,再升温至570℃保温8h,再水雾冷至室温(约25℃);
[0091]
s4.变形和时效:
[0092]
s4a.将步骤s3所得铸锭加热至530℃进行挤压成形,挤压比为35;
[0093]
s4b.将步骤s4a所得铸锭加热至180℃保温10h。
[0094]
实施例2
[0095]
本实施例制备了一种铝基材料,具体过程与实施例1的区别为:
[0096]
(1)成分不同,具体成分如表1所示;
[0097]
(2)步骤s1c中,精炼时间为30min;精炼剂与熔体的比例为2.5kg:1吨;
[0098]
(3)步骤s3中,均匀化处理的条件为:先升温至420℃保温3h,再升温至560℃保温3h,再升温至570℃保温10h。
[0099]
对比例1
[0100]
本对比例制备了一种铝基材料,具体过程与实施例1的区别为:
[0101]
(1)成分不同,具体成分如表1所示,其中为进行对比,添加了一定剂量的铁剂,铁剂中铁的质量百分含量为75%,余量为铝和助熔剂;
[0102]
(2)步骤s1c中,精炼时间为35min;精炼剂与熔体的比例为2.2kg:1吨。
[0103]
对比例2
[0104]
本对比例制备了一种铝基材料,具体过程与实施例1的区别为:
[0105]
(1)成分不同,具体成分如表1所示;
[0106]
(2)步骤s1b中,未添加al-sr中间合金、al-zr中间合金和锰剂。
[0107]
对比例3
[0108]
本对比例制备了一种铝基材料,具体过程与实施例1的区别为:
[0109]
(1)成分不同,具体成分如表1所示,其中,为了进行对比,添加了一定量的cr剂,cr剂中cr的质量百分含量为75%,余量为铝和助熔剂。
[0110]
(2)步骤s3中,均匀化处理的条件为:由室温(约25℃)直接升温至550℃保温2h,再升温至570℃保温8h,再水雾冷至室温(约25℃)。
[0111]
表1实施例1~2和对比例1~3所得铝基材料的成分
[0112][0113][0114]
其中铁和铬会随制备过程中引入,例如熔炼炉等引入的杂质,因此此处也进行了测试。
[0115]
试验例
[0116]
本试验例测试了实施例1~2和对比例1~3制备的铝基材料的性能。其中测试结果
如表2所示,测试方法如下:
[0117]
拉伸性能具体测试了在t6状态下(固溶处理加完全人工时效)的抗拉强度(rm)、屈服强度(rp
0.2
和断后伸长率;测试方法为:gb/t 228.1-2010金属材料拉伸试验第1部分室温试验方法。
[0118]
阳极氧化效果(外观)的测试方法为:氧化为肉眼外观检查。
[0119]
晶间腐蚀的测试方法为:gb_t 7998-2005铝合金晶间腐蚀测定方法。
[0120]
跌落测试的测试参考gbt 2423.8-1995提供的标准进行,以满足100mm跌落测试要求为通过。
[0121]
折弯性能的测试方法为:折弯90
°
,折弯角按1t(t表示测试样品厚度)测试,观察外观。
[0122]
表2实施例1~2以及对比例1~3所得铝基材料的性能
[0123][0124][0125]
根据表2结果可知,本发明提供的铝基材料具有优异的拉伸性能、弯折性能,还具有优异的外观、抗跌落性能和耐腐蚀性能。
[0126]
对比例1和实施例1的主要区别在于:对比例1中的铁、锰、锆、锶和钛的含量超标,其中铁含量超标会导致氧化过程中出现腐蚀孔洞,从而影响氧化膜品质,钛的作用主要为细化晶粒,主要以tib2颗粒存在,其大小在1μm左右,但是一旦量过多,就会发生团聚,从而成为杂质,影响氧化效果,即铁和钛超标会引起外观不良;由于含有过量的mn、sr、zr,对再结晶过程起到了抑制作用,铝基材料在步骤s4的变形、受热过程中,晶粒会融合长大,导致晶粒粗大,从而导致折弯测试时出现了橘皮。
[0127]
对比例2中没有添加锰、锶和锆元素,由于没有添加锰元素,铁无法更好的球化,导致氧化出现发麻不良;由于没有添加锶和锆元素,因此晶界未经优化,晶间腐蚀严重。
[0128]
对比例3中硅和镁的含量较低,且仅进行了两段均匀化处理;其中硅、镁成分偏低,未充分析出强化相,无法保证所得铝基材料的力学性能,按照gbt 2423.8-1995测试方法测试,也仅能满足50mm跌落测试要求;同时,虽然添加了具有细化晶粒作用的元素,但是这些元素没有在最佳的析出温度进行均匀化,而是直接进行高温均质(相当于第二段),导致锶和锆的析出相尺寸偏大,从而没有明显改善晶间腐蚀的效果,且氧化后出现了发雾不良,同时cr元素也相对较高,会导致材料发生粗晶,会导致氧化花斑。
[0129]
综上,本发明中,铝基材料组分之间,以及组分与制备方法之间,均发生了协同作用,可显著提升所得铝基材料的综合性能。
[0130]
上面对本发明实施例作了详细说明,但是本发明不限于上述实施例,在所属技术领域普通技术人员所具备的知识范围内,还可以在不脱离本发明宗旨的前提下作出各种变化。此外,在不冲突的情况下,本发明的实施例及实施例中的特征可以相互组合。