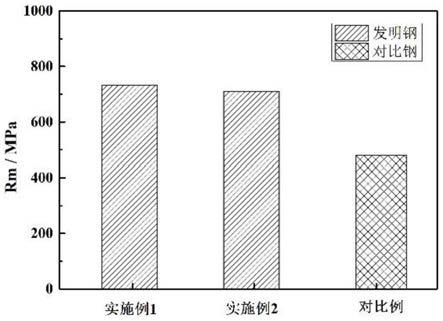
1.本发明属于低合金结构钢技术领域,特别是提供了一种可烧结摩擦层的高强心板用钢,适用于制造耐磨板、摩擦片、制动器等机械或车辆零部件。
背景技术:2.中碳的cr-mn-si系低合金结构钢在经淬、回火调质处理后,具有良好的综合性能,抗拉强度高达1500mpa甚至更高,但在经800℃左右温度的烧结处理时,由于组织和原奥氏体晶粒在高温下不断长大,且烧结后获得摩擦烧结层,后续无法再进行淬、回火调质处理,导致该类低合金钢材料强度急剧降低,在使用过程中无法发挥材料高强韧性特点。
3.对于带摩擦层的零部件,由于服役时摩擦层容易受到磨损,属于磨损主要受力部分,目前研究多数还是以摩擦层材料研究为主,对于心板材料的研究相对较少。中国专利cn102878232b提出了一种陶瓷纤维基摩擦片及其制作方法,其采用陶瓷纤维、碳纤维、芳纶浆、长纤维绵纸等制作摩擦片基体材料,但其未提到高温烧结的问题,以及心板材料强度的问题。中国专利cn 106190024b提出了一种摩擦片材料及其制备方法,其骨架材料为碳化硅增强铝基复合材料。而钢作为心板材料的相关报道很少,也鲜有相关成分的报道。
技术实现要素:4.本发明的目的在于提供一种可烧结摩擦层的高强心板用钢,通过控制钢中各成分含量生产制造可用于烧结摩擦层的高强心板用钢,在经烧结处理后,仍然具备高强度性能,从而提升摩擦件的抗疲劳性能。
5.本发明钢化学成分重量为:c:0.28~0.33%,si:0.90~1.20%,mn:0.95~1.09%,cr:0.95~1.09%,b:0.001~0.004%,al:0.025~0.050%,n:0.011~0.025%,其余为fe及不可避免的杂质,同时需要保证al:n的值在1.80~3.20。
6.该成分钢通过0.28~0.33%碳含量控制,可以促进形成碳化物,保证足够的强度。
7.该成分钢通过较高si含量控制,尽量降低钢在高温烧结时的软化行为,而si太高时,容易导致钢在烧结温度下表面氧化程度增加,因此,将si含量控制在0.90~1.20%。
8.mn、cr、b等是提升淬透性的元素,通过本发明mn、cr、b的含量配比,可以极大的提高钢在冷却时形成强化组织的几率,即使在冷却速度较慢的条件下,仍然可以获得较好的强度,同时可避免因烧结时可能产生的表面氧化弱化材料性能,另外,本发明中的b含量控制,可与c、n形成b(c,n)等析出相,起到析出强化的作用,进一步提升材料强度。
9.本发明钢中al和n的控制,可以实现在烧结前形成足够量的aln析出相,在钢800℃左右烧结温度下长时间保温时起到钉扎晶界的作用,细化晶粒和组织,使钢具有足够的细晶强化作用。
10.发明钢的冶炼工艺路线:bof转炉或eaf电炉+lf精炼+rh或vd精炼+cc连铸+轧制开坯+热轧+冷轧;冶炼时合金化方法:在lf精炼过程中分2~3批次加入sife合金、mnfe合金、si-mn合金、crfe合金进行微合化,添加量按mn、cr成分上线控制,在lf精炼末期,添加硼铁
合金,达到b含量控制目标。在rh或vd真空处理结束后通过喂线机将含al合金(或al线)加入钢液中,线速0.5~2.5m/s,并通过软吹氮及添加含氮合金调整氮含量。在所有成分调整到目标含量范围内后,进行厚板坯浇铸获得连铸坯。
11.在通过冶炼获得发明钢连铸坯后,需要对连铸坯进行轧制开坯,轧制前将连铸坯加热到1200~1220℃,保温180~280分钟,保证b、al、n在钢中的溶解及均匀化,随后轧制开坯以及热连轧轧制,终轧温度保持在880~980℃,促进b(c,n)和aln的析出,热轧钢板厚度控制在6~10mm,热轧后及时进行高温退火处理,对组织进行一定均匀化,最后在冷轧线上对获得的热轧板进行冷轧获得高强心板用钢,钢强度达到700mpa以上。
12.通过以上成分和工艺控制,获得的低合金结构钢,可以提升烧结摩擦层后钢板材料强度,在800℃左右烧结时,由于钢中高si成分控制,使钢的组织在高温下具有较好的稳定性,并且轧制时钢中析出的大量aln,在烧结温度下可以稳定存在,起到钉扎组织和晶界的作用,经烧结处理后,钢板和摩擦层整体随炉降温至320~450℃后进行空冷/风冷处理,冷却后,钢板强度可达到700mpa以上水平,与原有常规钢板强度仅仅只有350~500mpa相比,强度水平大幅度提升。
附图说明
13.图1为本发明钢、对比钢经烧结处理后强度结果图。
具体实施方式
14.下面通过具体实施例,对本发明的具体实施方法进行进一步的说明。
15.实施例1:
16.高强心板用钢化学成分重量为:c:0.32%,si:1.12%,mn:1.04%,cr:1.07%,b:0.0028%,al:0.032%,n:0.015%,余量为fe及不可避免的杂质,同时al:n为2.13。
17.制造工艺路线:eaf电炉+lf精炼+vd真空脱气+cc连铸+轧制开坯+热轧+冷轧;
18.冶炼时合金化方法:在lf精炼过程中分3批次加入sife合金、mnfe合金、si-mn合金、crfe合金进行微合化,添加量按mn、cr成分上线控制,在lf精炼末期,添加硼铁合金,lf结束后b含量控制为0.0031%。在vd真空处理结束后通过喂线机将含al合金加入钢液中,线速1.6m/s,并通过软吹氮及添加含氮合金调整氮含量,之后进行浇铸获得连铸坯;
19.轧制方法:连铸坯经1210℃加热保温250分钟后进行轧制开坯,并进行热连轧获得6.5mm热轧板,终轧温度保持在880~900℃,之后及时进行高温退火处理,随后进行冷轧获得高强心板用钢。
20.切割冷轧板,获得试样,参照烧结温度进行热处理,热处理后随炉冷却至350~360℃,出炉空冷。对热处理后试样进行力学性能测试,抗拉强度达到733mpa。
21.实施例2
22.高强心板用钢化学成分重量为:c:0.30%,si:0.99%,mn:1.01%,cr:1.03%,b:0.0025%,al:0.041%,n:0.014%,其余为fe及不可避免的杂质,al:n为2.93。
23.制造工艺路线:bof电炉+lf精炼+rh真空脱气+cc连铸+轧制开坯+热轧+冷轧;
24.冶炼时合金化方法:在lf精炼过程中分3批次加入sife合金、mnfe合金、si-mn合金、crfe合金进行微合化,添加量按mn、cr成分上线控制,在lf精炼末期,添加硼铁合金,lf
结束后b含量控制为0.0026%。在rh真空处理结束后通过喂线机将al线加入钢液中,线速2.0m/s,并通过软吹氮及添加含氮合金调整氮含量,之后进行浇铸获得连铸坯;
25.轧制方法:连铸坯经1210℃加热保温200分钟后进行轧制开坯,并进行热连轧获得7.5mm热轧板,终轧温度保持在910~930℃,之后及时进行高温退火处理,随后进行冷轧获得高强心板用钢。
26.切割冷轧板,获得试样,参照烧结温度进行热处理,热处理后随炉冷却至330~340℃,出炉空冷。对热处理后试样进行力学性能测试,抗拉强度为710mpa。
27.对比例:
28.对比钢化学成分重量为:c:0.31%,si:0.95%,mn:0.91%,cr:0.93%,al:0.020%,n:0.006%,其余为fe及不可避免的杂质,al:n为3.33。
29.制造工艺路线:eaf电炉+lf精炼+vd真空脱气+cc连铸+轧制开坯+热轧+冷轧;
30.冶炼时合金化方法:在lf精炼过程中一次性加入sife合金、mnfe合金、crfe合金进行微合化。在vd真空处理结束后通过喂线机将含al合金加入钢液中,线速0.8m/s,之后进行浇铸获得连铸坯;;
31.轧制方法:连铸坯经1230℃加热保温160分钟后进行轧制开坯,并进行热连轧获得6.5mm热轧板,终轧温度保持在850~870℃,之后进行高温退火处理,随后进行冷轧获得对比钢。
32.切割获得对比冷轧板试样,参照烧结温度进行热处理,热处理后随炉冷却。对热处理后试样进行力学性能测试,抗拉强度仅480mpa。