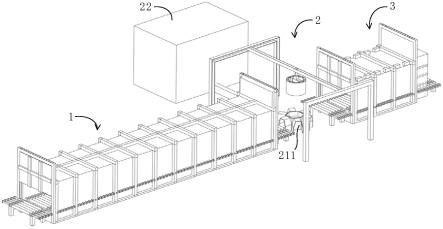
1.本发明涉及热处理技术领域,特别是指一种钢车轮热处理系统。
背景技术:2.汽车轻量化背景下,第三代先进高强钢(advanced high strength steel,简称ahss)替换传统汽车用钢可减重约20%。同时基于汽车结构件的安全性,要求汽车用ahss具有优异的综合力学性能,良好的碰撞吸能特性,强塑积需达到20.0gpa
·
%以上的水平。这要求材料保持高强度的同时还应具有良好的塑形和韧性。基于奥氏体trip效应和α/γ复相组织理论的q&p(quenching and partitioning,淬火-再分配)热处理工艺,可使传统热成形用超高强度钢拥有良好的强塑性匹配。
3.目前q&p热处理工艺在工业上应用较为困难,工业上多采用盐浴、淬火油,控温模具等方法实现淬火与保温,但盐浴、淬火油危险系数较高,工业应用会产生大量污染,从而增加后续处理工序及成本,控温模具制造成本高,对零件形状要求较高,以上方法均不利于钢车轮等复杂结构件大批量生产,同时由于钢车轮特殊结构,常规淬火方式在轮辐与轮辋连接处往往会产生淬火死角,导致该区域性能较差,对钢车轮服役性能造成不利影响。或焊缝淬火不均匀,由于焊缝处存在较大残余应力,可能会导致焊缝开裂,车轮变形。同时盐浴、淬火油对外界环境较为敏感,长期使用会对淬火介质产生污染影响淬火及保温效果,更换淬火介质较为困难等。
4.因此,亟需一种钢车轮热处理系统及方法,以能安全、环保地采用q&p热处理工艺对钢车轮进行处理,降低生产成本及生产难度,使钢车轮的q&p热处理适于大规模生产。
技术实现要素:5.有鉴于此,本发明的主要目的在于提供一种钢车轮热处理系统,以能安全、环保地采用q&p热处理工艺对钢车轮进行处理,减少淬火死角,使钢车轮的q&p热处理适于大规模生产。
6.本发明提供的钢车轮热处理系统,包括:第一加热炉,对钢车轮进行加热,使钢车轮完全奥氏体化;射流冷却机,可对钢车轮的表面喷射冷却介质,使钢车轮以≥5℃/s的冷速快速冷却至100-400℃;第二加热炉,对钢车轮进行加热,使钢车轮的温度保持在250-400℃。
7.采用如上系统,通过向钢车轮的表面喷射冷却介质的方式对钢车轮进行淬火。对钢车轮淬火后的冷却介质不会污染、影响新喷射出的冷却介质,便于对冷却介质进行更换。由此,降低了生产成本,使钢车轮的q&p热处理适于大规模生产。
8.本发明优选,所述射流冷却机包括:上淬火罩,下部具有开口,内部形状与钢车轮外周面相适配,内表面设置有多个第一喷射口;下淬火罩,外部形状与钢车轮的内周面相适配,外表面设置有多个第二喷射口;其中,第一喷射口及第二喷射口可向钢车轮喷射冷却介质。
9.采用如上结构,通过与钢车轮相适配的上淬火罩及下淬火罩,使布设的第一喷射口及第二喷射口更为均匀合理,从而使冷却更加均匀,减少了淬火死角,提高了淬火的效果。
10.本发明优选,所述射流冷却机还包括用于放置钢车轮的旋转台,旋转台可带动钢车轮旋转。
11.采用如上系统,在对钢车轮喷射冷却介质淬火过程中,通过旋转台驱动钢车轮旋转,可以使冷却更加均匀,提高了淬火的效果。
12.本发明优选,所述冷却介质为干燥空气、n2、h2或co2。
13.采用如上系统,通过干燥空气n2、h2或co2等介质冷却,安全系数高,且在淬火过程中不会产生大量污染,无须设置后续处理工序及成本,降低了生产成本。
14.本发明优选,所述冷却介质中添加有干冰颗粒或水雾。
15.采用如上系统,可以在冷却介质中添加有干冰颗粒或水雾,从而提高了冷却介质的冷却性能,从而使钢车轮更快地降温,提高了淬火效率。
16.另外,本技术还提供了一种钢车轮热处理方法,包括:对钢车轮进行加热处理,使钢车轮完全奥氏体化;向钢车轮的表面均匀喷射冷却介质,使钢车轮以≥5℃/s的冷速快速冷却至100-400℃;对钢车轮进行加热保温,使钢车轮的温度保持在250-400℃;最后,使钢车轮缓慢冷却到室温。
17.采用如上方法,通过向钢车轮的表面喷射冷却介质的方式对钢车轮进行淬火。对钢车轮淬火后的冷却介质不会污染、影响新喷射出的冷却介质,便于对冷却介质进行更换。由此,降低了生产成本,使钢车轮的q&p热处理适于大规模生产。
18.本发明优选,所述对钢车轮加热处理的温度为820-920℃,加热处理的时间为5-40min。
19.本发明优选,所述对钢车轮进行加热保温的时间为1-15min。
20.采用如上方法,提供了使钢车轮完全奥氏体化的温度及时间,以及保温的时间,提高了生产效率。
21.本发明优选,所述对钢车轮进行加热保温的温度部低于钢轮快速冷却后的温度。
22.采用如上方法,使钢车轮满足一步法或二步法碳配分工艺,以提高生产效率。
23.本发明优选,所述向钢车轮的表面均匀喷射冷却介质时,钢车轮以轴心为轴旋转。
24.采用如上方法,可以使钢车轮冷却时各部位都可以与喷射出的冷却介质接触,从而使冷区更加均匀。从而提高了淬火效果。
附图说明
25.图1为本技术钢车轮热处理系统的分布示意图;
26.图2为射流冷却机工作时的结构示意图;
27.图3为图2中上淬火罩、下淬火罩分离时的结构示意图;
28.图4为本技术钢车轮热处理方法的流程图。
29.附图标记说明
30.第一加热炉1;冷却装置2;射流冷却机21;旋转台211;下淬火罩212;第一冷却管212a;第一喷射口212b;上淬火罩213;第二冷却管213a;第二喷射口213b;风机房22;第二加
热炉3。
具体实施方式
31.下面,结合附图,对本技术的钢车轮热处理系统的具体结构及布置形式进行详细的描述。
32.图1为本技术钢车轮热处理系统的分布示意图。如图1所示,本技术的钢车轮热处理系统包括:第一加热炉1(图中为辊底式加热炉,还可采用步进式加热炉等形式)、冷却装置2、第二加热炉3(图中为辊底式加热炉,还可采用步进式加热炉等形式)三部分。其中,第一加热炉1用于对钢车轮进行加热,使钢车轮内部组织完全转化为奥氏体;冷却装置2包括射流冷却机21、风机房22,用于对完全奥氏体化后的钢车轮通过可控射流的方式进行均匀冷却,使钢车轮各部位的冷却速度大于马氏体转变临界冷却速度,当钢车轮冷却至ms-mf温度区间(初淬温度)后,将钢车轮转移至第二加热炉3中;第二加热炉3对钢车轮进行保温,使钢车轮保持在初淬温度或高于初淬温度一段时间,使得碳原子由马氏体向未转变残余奥氏体中配分,此时碳从过饱和的马氏体扩散到未发生马氏体转变的残余奥氏体中,使残余奥氏体中的碳含量增加,这样可以提高钢中残余奥氏体稳定性,并使其能在室温条件下稳定存在,最终室温下的微观组织为马氏体与残余奥氏体复相组织。
33.图2为射流冷却机21工作时的结构示意图;图3为图2中上淬火罩213、下淬火罩212分离时的结构示意图。如图1、图2、图3所示,射流冷却机21包括旋转台211,旋转台211用于放置经第一加热炉1加热完成后的钢车轮。钢车轮放置在旋转台211的上表面,可带动钢车轮以钢车轮的轴心为轴旋转。旋转台211的中间位置具有供下淬火罩212活动的空间。下淬火罩212设置在旋转台211内中间位置,可沿垂直方向上下移动。下淬火罩212的外周面形状与钢车轮的内周面相适配,下淬火罩212上均匀布设有若干第一冷却管212a,第一冷却管212a上均匀设置有多个朝向外侧的第一喷射口212b。旋转台211的上部位置设置有可上下移动的上淬火罩213,上淬火罩213的下部开口,上淬火罩213的内周面形状与钢车轮的外周面相适配。上淬火罩213上均匀布设有若干第二冷却管213a,第二冷却管213a上均匀设置有多个朝向轴心的第二喷射口213b。钢车轮转运至旋转台211上后,下淬火罩212上升位于钢车轮的内部,上淬火罩213下降位于钢车轮的外周位置,对钢车轮的内外表面进行包夹。
34.风机房22内部设置有风机,风机与射流冷却机21管道连接,可为射流冷却机21提供冷却气体。其中,冷却气体可采用干燥空气、n2、h2、co2等中添加有干冰颗粒或水雾等,可以根据实际情况选择合适的冷却气体介质。
35.由上,当钢车轮在第一加热炉1中加热到完全奥氏体化后,由辊道、步进梁等转运装置将钢车轮由第一加热炉1的出口输出,并将钢车轮转运至旋转台211上。钢车轮放置在预定位置后,下淬火罩212上升到钢车轮内部,上淬火罩213下降到钢车轮的外周面。第一喷射口212b及第二喷射口213b向钢车轮的内外表面喷射出冷却气体。旋转台211带动钢车轮以轴心为轴旋转,使钢车轮以≥5℃/s的冷速快速冷却至100-400℃的初淬温度。然后旋转台211停止旋转,上淬火罩213上升,下淬火罩212下降,对钢车轮的淬火冷却完成。将钢车轮转运至第二加热炉,对钢车轮进行保温,使钢车轮保持在配分温度一定时间,进行碳配分处理,配分温度与初淬温度相等或低于初淬温度。碳配分处理完成后,通过转运装置将钢车轮由第二加热炉3的出口输出,空冷到室温,钢车轮完成热处理。
36.进一步地,由第二加热炉3输出的钢车轮还可以通过水冷或风冷的方式冷却到室温,以加快冷却效率,提高生产节奏。
37.本技术还提供一种钢车轮热处理的方法。图4为本技术钢车轮热处理方法的流程图,如图4所示,钢车轮热处理方法的具体流程为:
38.1.钢车轮加热工序:将钢车轮转运至第一加热炉1加热,设置均热段温度为820-920℃,均热段加热时间约5-40min,至钢车轮完全奥氏体化;
39.2.冷却工序:奥氏体化完成后,将钢车轮转运至射流冷却机21中,通过设置在上淬火罩213与下淬火罩212上的第一喷射口212b及第二喷射口213b,采取可控射流方法(控制冷却介质的喷射速度,从而控制冷却速度),将冷却介质喷射到钢车轮的内外表面,旋转台211带动钢车轮以钢车轮的轴心为轴旋转,对钢车轮各部位进行均匀冷却。冷却介质可采用干燥空气、n2、h2、co2等中添加有干冰颗粒或水雾等,使钢车轮不同形状特征、不同厚度、焊缝等特殊性能要求区域部位以≥5℃/s的冷速均匀快速冷却至100-400℃的初淬温度;
40.3.配分工序:将冷却至100-400℃的钢车轮快速转移至第二加热炉31中加热保温,进行碳配分处理,可采取一步法或二步法碳配分工艺,即初淬温度等于配分温度,或初淬温度低于配分温度。第二加热炉3温度为250-400℃,加热时间约为1-15min;
41.4.二次冷却工序:将配分完成的钢车轮缓慢冷却至室温即得到本发明的强韧化钢车轮。
42.以上所述仅为本发明的较佳实施例而已,并不用以限制本发明,凡在本发明的精神和原则之内,所作的任何修改、等同替换、改进等,均应包含在本发明的保护范围之内。