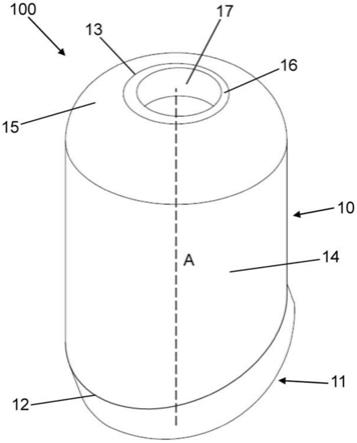
1.本技术涉及一种利用铸造模具在金属铸造操作中使用的供料器系统,以及在该供料器系统中使用的供料器套筒和缩颈砂芯。
背景技术:2.在典型的铸造过程中,熔融金属被浇注到限定铸件形状的预成型模具空腔中。通常通过压实在砂箱内的第一模具铸型周围的砂和粘合剂的混合物、使砂混合物凝结并硬化,然后移除铸型以留下模具空腔的一半来制造铸造模具。通过限定模具空腔的第二个一半的第二模具铸型来重复该过程,然后将模具的两个半部(称为上型箱和下型箱)组装在一起以形成在其中限定完整的模具空腔的整个模具。尽管以这种方式形成的模具可以使用多次,但是模具最终会失效或者铸型形状可能被侵蚀,此时模具被破坏并且砂被回收和修复以在新模具中重新使用。然而,对于这种类型的模具,在模具的使用寿命结束时难以回收砂并将砂与粘合剂材料分离。
3.在另一种称为真空模具铸造过程或“v过程”的铸造过程中,使用不含任何粘合剂的干砂制造模具,并且由于真空施加的力保持模具的形状。在v过程中,模具铸型包括微孔以便能够进行真空抽吸。第一塑料膜被拉到模具铸型上并通过抽吸粘附到模具铸型上。将还装备有抽吸系统的特殊砂箱围绕模具铸型放置,并用干砂填充,然后压实干砂。砂箱的顶侧被第二塑料密封膜覆盖,并且通过砂箱施加抽吸,这使得第一塑料膜和第二塑料膜(分别在底部和顶部)粘附到型砂上,将型砂密封在砂箱内。然后关闭通过铸型的真空并释放铸型,同时通过砂箱连续地施加真空以保持砂紧实并保持由铸型留下的模具空腔的形状。以这种方式形成的上型箱和下型箱被组装以形成完整的模具空腔,同时仍然施加抽吸以保持砂的形状,并且熔融金属被浇注到该空腔中。一旦金属铸件冷却并凝固,型砂可以容易地恢复到其原始的松散的状态,并通过简单地关闭真空而恢复以备将来使用。
4.在大多数的金属铸造过程中,金属在凝固时会收缩,从而导致缩孔,缩孔又在最终铸件中导致不可接受的缺陷。这是铸造工业中众所周知的问题,并且通过使用一体成型到模具中的供料器套筒或冒口来解决。每个供料器套筒提供与模具空腔连通的附加的(通常封闭的)容积或空腔,以便熔融金属在铸造期间从模具空腔进入供料器套筒内。在铸件凝固期间,供料器套筒内的熔融金属回流到模具空腔内以补偿铸件的收缩。在铸件凝固和型砂去除之后,供料器套筒空腔内的不需要的残余金属保持附着于铸件且必须被去除。为了便于去除残余金属,在通常被称为颈缩套筒的设计中,供料器套筒空腔可以朝向其基部(即供料器套筒最靠近模具空腔的端部)成锥形。当对残余金属施加急剧的冲击时,残余金属在最弱点处、靠近模具的地方(通常称为“敲落”的过程)分离。在铸件上的较小的覆盖区域也是期望的,以允许将供料器套筒定位在铸件的进入可能受到相邻特征限制的区域内。
5.尽管供料器套筒可以直接应用到铸造模具空腔的表面上,但供料器套筒通常与缩颈砂芯结合使用。传统的缩颈砂芯仅仅是具有贯穿该缩颈砂芯的孔的耐火材料的板或盘(通常是树脂粘结砂芯、陶瓷砂芯或供料器套筒材料的砂芯),该贯穿该缩颈砂芯的孔位于
模具空腔与供料器套筒之间。穿过缩颈砂芯的孔的直径被设计成小于供料器套筒的内部空腔(其不必是成锥形的)的直径,以便在接近铸造表面的缩颈砂芯处发生敲落。最近研发的缩颈砂芯(例如在foseco pct申请案no.wo2016/034872、no.wo2017/025702和no.wo2016/166497中描述的缩颈砂芯)可以是具有贯穿该缩颈砂芯的孔的金属管状形式。
6.在v过程中,在第一塑料膜施加到铸型之前,供料器放置在模具铸型上的凸台或销上。通常,供料器作为预成型系统放置在模具铸型上,其中,缩颈砂芯例如通过粘合剂附接到供料器套筒的基部。然而,可能有时在相邻的供料器套筒之间生成膜桥。此外,当塑料膜被拉到铸型和供料器套筒上时,在供料器套筒的顶部部分处的任何尖锐边缘都可能潜在地撕裂塑料膜。
7.本技术在考虑这些问题的情况下而发明。
技术实现要素:8.根据本技术的第一方面,提供一种用于金属铸造的供料器系统,该供料器系统包括安装在缩颈砂芯上的供料器套筒。供料器套筒具有第一端和相反的第二端、在第一端和第二端之间延伸的纵向轴线以及在第一端和第二端之间大致围绕纵向轴线延伸的连续的侧壁。供料器套筒的侧壁限定用于在铸造期间接纳熔融金属的空腔,且缩颈砂芯限定贯穿该缩颈砂芯的开孔,用于将空腔连接到铸件上。供料器套筒的第一端包括安装在缩颈砂芯上的基部部分。供料器套筒的第二端包括平坦的顶部部分和围绕顶部部分的周边延伸的弯曲部分或倒角部分,该弯曲或倒角部分用于连接供料器套筒的侧壁和顶部部分。
9.传统的供料器套筒倾向于在顶部被做成方形,在套筒的侧壁和顶部部分之间具有大致90
°
的拐角,从而导致在套筒的顶部处的相对尖锐的边缘。在本技术的供料器系统中,弯曲部分或倒角部分改善传统供料器套筒的顶部处的尖锐边缘,并且降低在v过程模具的形成期间在铸型上拉动塑料膜时撕裂塑料膜的风险。在供料器套筒包括倒角部分的实施例中,这通过在套筒的侧壁与顶部部分之间有效地生成两个边缘来实现,每个边缘均具有显著小于90
°
的拐角角度,该两个边缘没有具有90
°
的拐角角度的常规单个边缘那么尖锐。在供料器套筒包括弯曲部分的实施例中,完全消除了套筒的侧壁与顶部部分之间的任何坚硬的边缘。
10.在实施例中,供料器套筒的侧壁为圆筒形。圆筒的横截面形状大致可以是圆形、椭圆形或长圆形。在一些实施例中,圆筒的直径从第一端到第二端是大致恒定的。在其它实施例中,供料器套筒在第一端处的直径可以大于在第二端处的直径,供料器套筒在第二端处的直径可以大于在第一端处的直径。在一些实施例中,供料器套筒的侧壁大体呈圆筒形,其中截头圆锥形部分朝向供料器套筒的第一端定位,该截头圆锥形部分朝向缩颈砂芯成锥形。
11.在实施例中,在供料器套筒第一端处的基部部分大体上垂直于供料器套筒的纵向轴线(即,相对于供料器套筒的纵向轴线成约90
°
的角度)延伸。替代地,基部部分可以相对于供料器套筒的纵向轴线以一定角度倾斜,以使得供料器套筒一侧上的侧壁比供料器套筒相对侧上的侧壁短。在实施例中,基部部分相对于供料器套筒的纵向轴线以至少30
°
、35
°
、40
°
、50
°
、60
°
、70
°
、80
°
或85
°
的倾斜角度延伸。在实施例中,基部部分相对于供料器套筒的纵向轴线以不大于88
°
、85
°
、80
°
、70
°
、60
°
、50
°
、40
°
或35
°
的倾斜角度延伸。在实施例中,基
部部分相对于供料器套筒的纵向轴线以30
°
至88
°
、40
°
至85
°
或50
°
至80
°
的倾斜角度延伸。可以理解,其上安装有供料器套筒的缩颈砂芯将沿着与供料器套筒的基座部分相同的方向或以与供料器套筒的基座部分相同的倾斜角度延伸。在供料器系统位于铸件的成角度的部分上的情况下,倾斜的基部部分和缩颈砂芯是期望的。
12.在实施例中,缩颈砂芯是传统的板状缩颈砂芯或盘状缩颈砂芯。替代地,缩颈砂芯可包括限定出贯穿该缩颈砂芯的孔的平坦的基部以及围绕基部的外周延伸的环形的凸起的侧壁。在实施例中,凸起的侧壁具有下表面和与下表面相反的上表面,该下表面附接到平坦的基部或与平坦的基部一体地形成,其中,内边缘和相反设置的外边缘在上表面与下表面之间延伸。在实施例中,凸起的侧壁的高度是供料器套筒的最大高度的至少1%、2%、5%、10%或15%,其中,凸起的侧壁的高度是从下表面到上表面测得的,且供料器套筒的最大高度是从第一端到第二端测得的。在实施例中,凸起的侧壁的高度不大于供料器套筒的最大高度的15%、10%、5%、2%或1%。在实施例中,凸起的侧壁的高度是供料器套筒的最大高度的1%
‑
15%、2%
‑
10%或5
‑
10%。应当理解,在供料器套筒的基座部分相对于纵向轴线倾斜的实施例中,供料器套筒的最大高度为第一端与第二端之间的最大距离,即,在供料器套筒的侧壁的高度为最大的位置。
13.提供具有凸起的侧壁的缩颈砂芯使得供料器系统能够在需要时以两个部件应用于模具铸型。在这种两个部件的应用过程中,缩颈砂芯首先被定位在模具铸型上,然后第一塑料膜被拉到模具铸型和缩颈砂芯上,然后供料器套筒与缩颈砂芯在塑料膜上一起被组装。这防止塑料膜在供料器套筒之间桥接,因为该膜没有被拉到套筒本身上。在铸造期间,缩颈砂芯和供料器套筒之间的塑料膜易于被熔融金属烧掉且不干扰铸造。
14.在实施例中,缩颈砂芯还包括朝向远离平坦的基部的方向从凸起的侧壁的上表面突出的脊部或凸台。该凸台允许在供料器系统的组装过程中,供料器套筒被正确地对准并牢固地安装在缩颈砂芯上。在实施例中,凸台围绕凸起的侧壁的内边缘的外周完全或部分地延伸。凸台可以围绕内边缘的外周的至少5%、10%、20%、30%、40%、50%、60%、70%、80%或90%延伸。凸台可以围绕内边缘的外周的不超过100%、90%、80%、70%、60%、50%、40%、30%、20%或10%延伸。在实施例中,凸台围绕内边缘的外周的大约25%
‑
100%或25%
‑
50%延伸。
15.应当理解,供料器套筒的第一端被适当地构造成在供料器系统的组装期间被安装到缩颈砂芯上。例如,在缩颈砂芯包括凸起的侧壁和围绕凸起的侧壁的内边缘延伸的凸台的实施例中,供料器套筒的侧壁可以具有与凸起的侧壁的上表面的除凸台的宽度之外的剩余宽度相对应的厚度,以使得供料器套筒的侧壁紧密地配合到凸台。替代地,在供料器套筒的第一端处的侧壁可以包括被构造成接纳缩颈砂芯上的凸台的切口或凹槽。
16.在实施例中,平坦的顶部部分在第二端处位于中心。优选地,顶部部分垂直于供料器套筒的纵向轴线延伸。
17.通常,顶部部分的形状可以对应于供料器套筒的侧壁的横截面形状。例如,在供料器套筒的侧壁具有大体圆形横截面形状的实施例中,顶部部分可以为大体圆形,或者在侧壁具有大体长圆形横截面形状的实施例中,顶部部分可以为大体长圆形。在实施例中,顶部部分具有为供料器套筒的侧壁的最小直径的至少25%、30%、40%、50%、60%、70%、80%或85%的最小直径。在实施例中,顶部部分具有不大于侧壁的最小直径的90%、85%、80%、
70%、60%、50%、40%或30%的最小直径。在实施例中,顶部部分具有为供料器套筒的侧壁的最小直径的25%
‑
90%、30%
‑
80%或40%
‑
70%的最小直径。
18.在实施例中,供料器套筒的顶部部分包括贯穿该顶部部分的开孔。该孔可以位于顶部部分的中心。或者,孔可以偏离顶部部分的中心。在顶部部分中的孔的形状可以对应于顶部部分的形状。例如,在顶部部分是圆形的情况下,孔也可以是圆形的,或者在顶部部分是长圆形的情况下,孔也可以是长圆形的。然而,孔的形状可以不必与顶部部分的形状相对应(例如,在顶部部分为长圆形的情况下,孔可以是圆形的)。该孔相对于顶部部分的面积可以是任何尺寸。在实施例中,孔具有为顶部部分的最小直径的至少20%、30%、40%、50%、60%、70%、80%、90%或95%的最小直径。在实施例中,孔具有不大于顶部部分的最小直径的95%、90%、80%、70%、60%、50%、40%或30%的最小直径。在实施例中,孔的最小直径是顶部部分的最小直径的20%
‑
100%或40%
‑
90%。优选地,孔的直径小于顶部部分的直径,使得为了制造的目的,存在围绕孔的整个周边的一定量的顶部部分。然而,应当理解,在一些实施例中,孔的最小直径可以是顶部部分的最小直径的100%,使得顶部部分完全由孔构成。
19.在供料器套筒的第二端包括倒角部分的实施例中,倒角部分可以相对于供料器套筒的纵向轴线以至少10
°
、20
°
、30
°
、40
°
、50
°
或60
°
的角度从侧壁延伸。倒角部分可以相对于供料器套筒的纵向轴线以不大于70
°
、60
°
、50
°
、40
°
、30
°
或20
°
的角度从侧壁延伸。在实施例中,倒角部分相对于供料器套筒的纵向轴线以10%
‑
70
°
、20%
‑
60
°
或30%
‑
50
°
的角度从侧壁延伸。倒角部分可以延伸在侧壁和顶部部分之间测量的最小距离,该最小距离是侧壁的最小直径的至少10%、20%、30%、50%、75%、100%或125%。
20.倒角部分可以延伸不超过侧壁的最小直径的150%、125%、100%、75%、50%、30%或20%的最小距离。在实施例中,倒角部分延伸侧壁的最小直径的10%
‑
150%、20%
‑
100%或20
‑
50%的最小距离。
21.在供料器套筒的第二端包括弯曲部分的实施例中,弯曲部分的曲率半径可以为至少2mm、5mm、10mm、20mm、30mm、50mm、75mm或90mm。弯曲部分的曲率半径可不大于100mm、90mm、75mm、50mm、30mm、20mm、10mm或5mm。在实施例中,弯曲部分的曲率半径为2
‑
100mm、5
‑
75mm或10
‑
50mm。应当理解,精确的曲率半径将取决于供料器套筒的总尺寸,且如果供料器格外大,则精确的曲率半径可以大于这些值。
22.在实施例中,供料器套筒可以包括通过任何合适的机构(例如粘合剂、榫槽等)装配在一起的两个或更多部件。部件中的一个可以包括顶部部分和弯曲部分或倒角部分,而部件中的另一个可以包括供料器套筒的基部部分。
23.根据本技术的第二方面,提供一种用于金属铸造的供料器系统,该供料器系统包括安装在缩颈砂芯上的供料器套筒。供料器套筒具有第一端和相反的第二端、在第一端和第二端之间延伸的纵向轴线以及在第一端和第二端之间大致围绕纵向轴线延伸的连续的侧壁。供料器套筒的侧壁限定用于在铸造期间接纳熔融金属的空腔。供料器套筒的第一端包括安装在缩颈砂芯上的基部部分。缩颈砂芯包括限定贯穿该缩颈砂芯的孔的平坦的基部以及围绕平坦的基部的外周延伸的环形的凸起的侧壁。该凸起的侧壁具有下表面和与该下表面相反的上表面,该下表面连接到该平坦的基部或与该平坦的基部一体地形成。缩颈砂芯还包括朝向远离平坦的基部的方向从凸起的侧壁的上表面突出的脊部或凸台,脊部或凸
台被构造成与供料器套筒的基部部分接合。
24.如上文关于第一方面所讨论的,提供具有凸起的侧壁的缩颈砂芯使得供料器套筒能够在第一塑料膜已被拉到模具铸型上之后被组装到缩颈砂芯上,从而防止在相邻的供料器套筒之间产生塑料膜桥接。
25.在实施例中,供料器套筒的第二端包括平坦的顶部部分和围绕顶部部分的周边延伸的弯曲部分或倒角部分,弯曲部分或倒角部分用于连接供料器套筒的侧壁和顶部部分。替代地,供料器套筒的第二端可以仅包括以90
°
角度直接连接到侧壁上的平坦的顶部部分。
26.本技术还在于一种在根据第一方面和第二方面的实施例的供料器系统中使用的供料器套筒和缩颈砂芯。
27.根据本技术的第三方面,提供一种用于金属铸造的供料器套筒,供料器套筒包括第一端和相反的第二端、在第一端与第二端之间延伸的纵向轴线以及大体围绕纵向轴线在第一端与第二端之间延伸的连续的侧壁,该侧壁限定在铸造期间用于接纳熔融金属的空腔,供料器套筒的第一端被构造用于安装在缩颈砂芯上,且供料器套筒的第二端包括平坦的顶部部分和围绕顶部部分的周边延伸的弯曲部分或倒角部分,弯曲部分或倒角部分用于连接供料器套筒的侧壁与顶部部分。
28.根据本技术的第四方面,提供一种用于金属铸造的缩颈砂芯,缩颈砂芯包括限定贯穿该缩颈砂芯的孔的平坦的基部和围绕平坦的基部的外周延伸的环形的凸起的侧壁,该凸起的侧壁包括附接到平坦的基部或者与平坦的基部一体地形成的下表面以及与下表面相反的上表面,缩颈砂芯还包括朝向远离平坦的基部的方向从凸起的侧壁的上表面突出的脊部或凸台,该脊部或凸台被构造成与供料器套筒的基部部分接合。
29.上面关于第一方面的实施例描述的特征可以同样地应用于第二方面、第三方面和第四方面的实施例。除非存在任何技术不相容性,否则考虑本技术的各方面的所有组合。
附图说明
30.现在仅通过参考附图以示例的方式来描述本技术的实施例,其中:
31.图1至图3是根据本技术的实施例的供料器系统的示意图;
32.图4是图1至图3所示的供料器系统的剖视图;
33.图5至图7是根据本技术的不同实施例的供料器系统的示意图;
34.图8是图5至图7所示的供料器系统的剖视图;
35.图9是根据本技术的另一实施例的供料器系统的示意图;
36.图10是图9所示的供料器系统的平面图;
37.图11是与本技术的供料器系统的实施例一起使用的缩颈砂芯的实施例的示意图;以及
38.图12是与本技术的供料器系统的实施例一起使用的缩颈砂芯的另一实施例的示意图。
具体实施方式
39.参照图1至图4,示出一种供料器系统100,该供料器系统包括安装在缩颈砂芯11上的供料器套筒10,供料器套筒10具有第一端12和相反的第二端13,其中纵向轴线a在第一端
12与第二端13之间延伸。连续的侧壁14大致围绕纵向轴线a以圆筒的形状延伸,从而在其中限定用于接纳熔融金属的空腔。侧壁14的直径d1从供料器套筒10的第一端12到第二端13是恒定的。
40.供料器套筒10的第二端13包括垂直于纵向轴线a延伸的位于中心的平坦的顶部部分16。第二端13还包括连接供料器套筒的侧壁14和顶部部分16的弯曲部分15。弯曲部分15的曲率半径为28.5mm。顶部部分16是圆形的,并且具有延伸贯穿该顶部部分的位于中心的孔17,该孔的横截面通常也是圆形的。顶部部分16的直径d2是供料器套筒的侧壁的直径d1的50%,且孔17的直径d3小于顶部部分16的直径d2,从而使得顶部部分16的一部分围绕孔17的整个周边延伸。
41.供料器套筒10的第一端12安装在缩颈砂芯11上,并相对于纵向轴线以70
°
的角度α倾斜,使得侧壁14在供料器套筒10的一侧上比在相反侧上更短。缩颈砂芯11包括平坦的基部110和围绕平坦的基部110的外周延伸的凸起的侧壁111(在图4中最佳示出)。平坦的基部110通常是圆形的,并包括延伸贯穿该基部的位于中心的孔112。凸起的侧壁111具有与平坦的基部110连通并一体地形成的下表面113以及与平坦的基部110相反的上表面114,其中内边缘115和相反设置的外边缘116在下表面113和上表面114之间延伸。从下表面113到上表面114测量的凸起的侧壁111的高度h2是在从第一端12到第二端13测量的侧壁14的高度最大处的供料器套筒10的最大高度h1的6.25%。
42.缩颈砂芯11还包括从凸起的侧壁111的上表面114的内边缘侧突出的凸台117。凸台117延伸内边缘115的外周的大约25%。供料器套筒10的侧壁14的基部具有厚度t1,使得侧壁14的基部抵靠住凸台117,该厚度t1对应于凸起的侧壁111的上表面114的除凸台117以外的剩余区域。
43.参照图5至图8,示出根据本技术的供料器系统200的另一实施例。供料器系统200包括安装在缩颈砂芯21上的供料器套筒20。供料器套筒20具有第一端22和相反的第二端23,其中纵向轴线b在第一端22和第二端23之间延伸。连续的侧壁24大致围绕纵向轴线b延伸,大致呈圆筒形,从而在其中限定用于接纳熔融金属的空腔。侧壁24在供料器套筒20的第二端23处的直径略小于在第一端22处的直径,以使得侧壁24在供料器套筒的第二端23处具有最小直径d4。
44.供料器套筒20的第二端23包括垂直于纵向轴线b延伸的位于中心的平坦的顶部部分26。第二端23还包括连接供料器套筒的侧壁24和顶部部分26的倒角部分25。倒角部分25相对于纵向轴线b以50
°
的角度β倾斜,并延伸等于侧壁24的最小直径d4的24%的距离w1。顶部部分26是圆形的,并具有延伸贯穿该顶部部分的位于中心的孔27,该孔的横截面大致也是圆形的。顶部部分26的直径d5是供料器套筒的侧壁的最小直径d4的63%,且孔27的直径d6小于顶部部分26的直径d5,从而使得顶部部分26的一部分围绕孔27的整个周边延伸。
45.供料器套筒20的第一端22安装在缩颈砂芯21上。供料器套筒20的第一端22垂直于纵向轴线b延伸,以使得侧壁24具有均匀的高度。缩颈砂芯21包括平坦的基部210和围绕平坦的基部210的外周延伸的凸起的侧壁211(在图8中最佳示出)。平坦的基部210通常是圆形的,并且包括延伸贯穿该基部的位于中心的孔212。凸起的侧壁211具有与平坦的基部210连通并一体地形成的下表面213以及与平坦的基部210相反的上表面214,其中内边缘215和相反设置的外边缘216在下表面213和上表面214之间延伸。从下表面213到上表面214测量的
凸起的侧壁211的高度h4是从第一端22到第二端23测量的供料器套筒20的高度h3的6%。
46.缩颈砂芯21还包括从凸起的侧壁211的上表面214的内边缘侧突出的凸台217。凸起217围绕内边缘215的整个外周延伸。供料器套筒20的侧壁24的基部具有厚度t2,使得侧壁24的基部抵靠住凸台217,该厚度t2对应于凸起的侧壁211的上表面214的除凸台217以外的剩余区域。
47.参照图9至图10,示出根据本技术的供料器系统300的另一实施例。供料器系统300包括安装在缩颈砂芯31上的供料器套筒30。供料器套筒30具有第一端32和相反的第二端33,其中纵向轴线(未示出)在第一端32和第二端33之间延伸。连续的侧壁34以长圆形的横截面形状大致围绕纵向轴线延伸,从而在其中限定用于接纳熔融金属的空腔。
48.供料器套筒30的第一端32安装在缩颈砂芯31上。供料器套筒30的第一端32垂直于纵向轴线延伸,使得侧壁34具有均匀的高度。缩颈砂芯31包括平坦的基部(未示出)和围绕平坦的基部的外周延伸的凸起的侧壁311。平坦的基部通常为长圆形,并包括延伸贯穿该基部的位于中心的孔(未示出)。
49.供料器套筒30的第二端33包括垂直于纵向轴线延伸的位于中心的平坦的顶部部分36。第二端33还包括连接供料器套筒30的侧壁34和顶部部分36的弯曲部分35。顶部部分36为长圆形且具有延伸贯穿该顶部部分的位于中心的孔37,该孔的横截面也为长圆形。
50.如图10所示,侧壁34具有在长圆形的横截面的长边之间的最小直径d7和在长圆形的横截面的短边之间的最大直径d8。长圆形的顶部部分36还具有在长边之间的最小直径d9和在短边之间的最大直径d
10
。顶部部分36的最小直径d9大约是侧壁34的最小直径d7的40%。孔37的直径小于顶部部分36的直径,使得顶部部分36的一部分围绕孔37的整个周边延伸。
51.参照图11,示出根据本技术实施例的在供料器系统中使用的缩颈砂芯400的实施例。缩颈砂芯400包括平坦的基部410和围绕平坦的基部410的外周延伸的凸起的侧壁411。平坦的基部410通常是圆形的,并且包括延伸贯穿该基部的位于中心的孔412。凸起的侧壁411具有与平坦的基部410连通并一体地形成的下表面(未示出)和与平坦的基部410相反的上表面414,其中内边缘415和相反设置的外边缘416在下表面413和上表面414之间延伸。缩颈砂芯400还包括从凸起的侧壁411的上表面414的内边缘侧突出的凸台417。凸台417围绕内边缘215的外周的大约25%延伸。
52.参照图12,示出根据本技术实施例的在供料器系统中使用的缩颈砂芯500的另一实施例。缩颈砂芯500包括与图11中所示缩颈砂芯400基本相同的特征,除了平面基部510是长圆形而不是圆形的并且凸台517围绕上表面514的内边缘侧的整个周边延伸之外。延伸穿过平坦的基部510的孔512的横截面也是长圆形的。