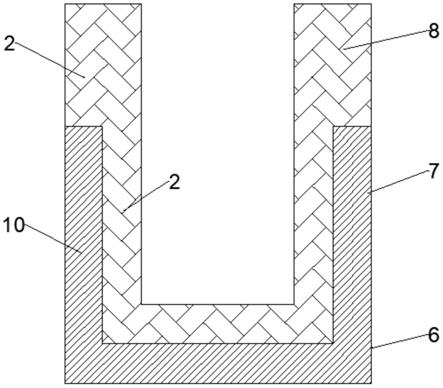
1.本实用新型涉及中间包工作衬技术领域。具体地说是用于制备复合中间包工作衬的装置及复合中间包工作衬。
背景技术:2.中间包是炼钢生产工序中钢水连铸工艺的关键部件,在对钢水储存、减压、分流、降低钢水非金属夹杂等方面发挥着重要作用。中间包工作衬主要有干式料和涂料两种类型,而中间包工作衬的材质包括镁质、硅质、镁硅质(镁橄榄石)、镁碳质、镁铬质等几种。当前,我国粗钢产量超过10亿吨,按吨钢耐火材料消耗1.5kg估算,仅中间包工作层的年需求量就在150万吨以上。伴随着现代洁净钢和特钢种冶炼技术的快速发展,越来越多的客户偏向使用mgo含量不低于80%的镁质干式料或镁质涂料。这种碱性工作衬虽然在抗熔渣侵蚀、降低钢水非金属夹杂等方面确实存在较大的优势,但由于主原料镁砂来源于菱镁矿在高温下的分解、烧制和熔融,生产过程能耗高,且co2及烟尘废气等排放量大,环境污染严重,原料成本(1500-4500元/吨)也相比硅质(500元/吨)、镁硅质(镁橄榄石,500元/吨)大幅增加(1300
‑
4000元/吨);另一方面,相比硅质、镁硅质及镁铬质等材料,镁质工作衬的导热系数大,导致钢水浇铸过程中温降快,能耗增加的同时也影响钢水连铸质量。随着今后我国对
ꢀ“
十四五”“碳达峰”、“碳中和”等战略规划等的大力推进,迫切需要研究新工艺与新技术,解决目前原料供给侧存在的各种矛盾和问题。
技术实现要素:3.为此,本实用新型所要解决的技术问题在于提供一种用于制备复合中间包工作衬的装置及复合中间包工作衬,以解决当前镁质工作衬消耗量大、成本高,以及在钢水浇铸过程中降温快而影响钢水连铸质量等问题;通过对材料结构和材质两方面同时进行优化配置,达到即能满足客户对洁净钢和特钢种冶炼的需求,又能降低生产成本、节约镁质资源、减少生产能耗及co2排放等目的。
4.为解决上述技术问题,本实用新型提供如下技术方案:
5.用于制备复合中间包工作衬的装置,包括胎模、隔板和挡渣墙安装槽成型部件,所述胎模与所述隔板之间为第一工作衬成型空间,所述隔板与永久衬之间为第二工作衬成型空间,所述挡渣墙安装槽成型部件的一侧与所述胎模贴合。本装置可以制备出包含有第一工作衬和第二工作衬的双层复合中间包工作衬,从而可以使靠近低温永久衬的一侧采用成本较低的非镁质工作衬,而靠近钢水钢渣的一侧采用综合效果较好而成本较高的镁质工作衬,从而解决了当前镁质工作衬消耗量大、成本高,以及镁质工作衬在钢水浇铸过程中降温快而影响钢水连铸质量等问题。
6.上述用于制备复合中间包工作衬的装置,所述挡渣墙安装槽成型部件的两侧分别与所述胎模和所述永久衬贴合。所述挡渣墙安装槽成型部件的作用有二:一方面对隔板起到固定作用,另一方面在使用该装置制备复合中间包工作衬的过程中形成挡渣墙安装槽,
方便在挡渣墙安装槽成型部件卸除后安装挡渣墙。
7.上述用于制备复合中间包工作衬的装置,所述隔板固定安装在所述挡渣墙安装槽成型部件上,并且所述隔板与所述挡渣墙安装槽成型部件之间可拆卸连接。可以将胎模与永久衬之间的空间分割成独立的两个空间,即第一工作衬成型空间和第二工作衬成型空间,且方便在工作衬成型过程中将隔板拆除。
8.上述用于制备复合中间包工作衬的装置,所述挡渣墙安装槽成型部件的上部设置有卡槽。
9.上述用于制备复合中间包工作衬的装置,所述隔板的下部设置有豁口,所述豁口的形状大小与所述挡渣墙安装槽成型部件下部的形状大小相吻合。隔板下部的豁口深度与挡渣墙安装槽成型部件下部的高度相等,且隔板上部的高度大于或等于挡渣墙安装槽成型部件上部的卡槽深度,从而可以使隔板和挡渣墙安装槽成型部件卡扣在一起。
10.上述用于制备复合中间包工作衬的装置,还包括环绕所述第一工作衬成型空间和所述第二工作衬成型空间的布料器,所述隔板的上端伸入到所述布料器内。隔板将布料器分割成相互独立的两个空间,方便向布料器的中添加不同的工作衬耐火材料。
11.上述用于制备复合中间包工作衬的装置,所述隔板是厚度为2
‑
6mm表面光滑的钢板,所述隔板为平板或波浪形曲面板;当隔板为波浪形曲面板时,可以增加隔板两侧不同工作衬材料的接触面积;所述隔板的顶壁高出中间包上沿300
‑
400mm;所述隔板的顶壁焊接有抽拔吊钩,方便在复合工作衬成型过程中拔除隔板;所述胎模为上宽下窄的倒梯形,以便于成型烘烤后脱模;所述内胎模上方安装有振动电机;所述胎模空腔内部安装有点火烘烤装备。所述挡渣墙安装槽成型部件的宽度略大于中间包挡渣墙的厚度,以确保挡渣墙安装槽中挡渣墙的安装。
12.上述用于制备复合中间包工作衬的装置,所述布料器为上宽下窄的倒梯形漏斗;所述布料器的底部宽度与所述复合工作衬的总厚度保持一致。
13.一种复合中间包工作衬,包括包底工作衬、包壁工作衬和渣线工作衬,所述包底工作衬成型于中间包包底上,所述包壁工作衬和所述渣线工作衬分别成型于中间包内壁上,且所述渣线工作衬位于所述包壁工作衬上方,所述包壁工作衬包括mgo含量大于80wt%的第一工作衬和mgo含量小于80wt%的第二工作衬,所述第一工作衬与所述第二工作衬之间接触面紧密贴合,至少所述第一工作衬上成型有挡渣墙安装槽。该复合中间包工作衬既可以保留镁质工作衬的工作优点,又能减少镁质工作衬的使用量,降低镁质工作衬的消耗,节约中间包耐材成本,减少环境污染。
14.第一工作衬即为镁质工作衬,第二工作衬即为非镁质工作衬;所述镁质工作衬的原料为重烧镁砂和电熔镁砂中的一种或两种;所述非镁质工作衬的主原料为石英、镁橄榄石、镁铬废砖、镁碳废碳、铝镁碳废砖、重烧镁砂、电熔镁砂中的一种或两种及两种以上的混合;所述第一工作衬靠近高温钢水,第二工作衬靠近低温永久衬,且第一工作衬和第二工作衬均可以是中间包干式振动料,也可以是中间包涂料。
15.上述复合中间包工作衬,在所述第一工作衬和所述第二工作衬的厚度方向:所述挡渣墙安装槽贯穿所述第一工作衬和所述第二工作衬。
16.上述复合中间包工作衬,所述包底工作衬包括mgo含量大于80wt%的第一工作衬和mgo含量小于80wt%的第二工作衬,所述第一工作衬与所述第二工作衬之间接触面紧密贴
合;所述渣线工作衬为mgo含量大于80wt%的工作衬。所述渣线工作衬可采用与第一工作衬相同的镁质材料,由于渣线工作衬工作环境的腐蚀性更强,为确保安全及提高工作衬的整体工作寿命,也可结合熔渣侵蚀情况布置抗侵蚀性更加优良的镁质材料。
17.本实用新型的技术方案取得了如下有益的技术效果:
18.1、使用本实用新型的装置可以制备出包含有第一工作衬和第二工作衬的双层复合中间包工作衬,从而可以使靠近低温永久衬的一侧采用成本较低的非镁质工作衬,而靠近高温钢水钢渣的一侧采用综合效果较好而成本较高的镁质工作衬,从而解决了当前镁质工作衬消耗量大、成本高,以及镁质工作衬在钢水浇铸过程中降温快而影响钢水连铸质量等问题。
19.2、本实用新型用于制备复合中间包工作衬的装置中,所述挡渣墙安装槽成型部件的作用有二:一方面对隔板起到固定作用,另一方面在使用该装置制备复合中间包工作衬的过程中形成挡渣墙安装槽,方便在挡渣墙安装槽成型部件卸除后安装挡渣墙;通过设置成可拆卸的隔板,可以将胎模与永久衬之间的空间分割成独立的两个空间,即第一工作衬成型空间和第二工作衬成型空间,且方便在工作衬成型过程中将隔板拆除。
20.3、本实用新型用于制备复合中间包工作衬的装置中,隔板下部的豁口深度与挡渣墙安装槽成型部件下部的高度相等,且隔板上部的高度大于或等于挡渣墙安装槽成型部件上部的卡槽深度,从而可以使隔板和挡渣墙安装槽成型部件卡扣在一起。隔板将布料器分割成相互独立的两个空间,方便向布料器的中添加不同的工作衬耐火材料。当隔板为波浪形曲面板时,可以增加隔板两侧不同工作衬材料的接触面积;隔板的顶壁焊接有抽拔吊钩,方便在复合工作衬成型过程中拔除隔板。
21.4、本实用新型用于制备复合中间包工作衬的装置中,胎模可设置为上宽下窄的倒梯形,以便于成型烘烤后脱模;挡渣墙安装槽成型部件的宽度略大于中间包挡渣墙的厚度,以确保挡渣墙安装槽中挡渣墙的安装。
22.5、本实用新型提供的复合中间包工作衬既可以保留镁质工作衬的工作优点,又能减少镁质工作衬的使用量,降低镁质工作衬的消耗,节约中间包耐材成本,减少环境污染。
23.6、本实用新型采用带有振动电机的内置胎模,加装槽钢、隔板和布料器等装置,根据中间包工作衬各部位的使用特点和要求,分别对包底、包壁和渣线工作衬进行复合施工、整体成型,达到既可以满足客户对中间包工作衬高mgo含量、低导热、高安全性的要求,又可以实现降低生产成本、节约镁质资源、减少生产能耗及co2排放等目的,具有很好社会经济效益和生态环境效益。
附图说明
24.图1本实用新型用于制备复合中间包工作衬的装置的结构示意图;
25.图2本实用新型用于制备复合中间包工作衬的装置的俯视图;
26.图3本实用新型用于制备复合中间包工作衬的装置的剖面图;
27.图4本实用新型图3中b处的放大图;
28.图5本实用新型实施例2复合中间包工作衬的结构示意图;
29.图6本实用新型实施例3复合中间包工作衬的结构示意图。
30.图中附图标记表示为:1
‑
胎模;2
‑
第一工作衬;3
‑
挡渣墙安装槽成型部件;4
‑
隔板;
5
‑
布料器;6
‑
包底工作衬;7
‑
包壁工作衬;8
‑
渣线工作衬;9
‑
永久衬;10
‑
第二工作衬。
具体实施方式
31.实施例1
32.如图1和图2所示,用于制备复合中间包工作衬的装置,包括胎模1、隔板4和挡渣墙安装槽成型部件3,胎模1与隔板4之间为第一工作衬成型空间,隔板4与永久衬9之间为第二工作衬成型空间,挡渣墙安装槽成型部件3的两侧分别与胎模1和永久衬9贴合;
33.该装置还包括环绕第一工作衬成型空间和第二工作衬成型空间的布料器5,隔板4的上端伸入到布料器5内;布料器5为上宽下窄的倒梯形漏斗,具体可参见图3和图4。布料器5的底部宽度与复合工作衬的总厚度保持一致。内胎模上方安装有振动电机;胎模空腔内部安装有点火烘烤装备。挡渣墙安装槽成型部件的作用有二:一方面对隔板起到固定作用,另一方面在使用该装置制备复合中间包工作衬的过程中形成挡渣墙安装槽,方便在挡渣墙安装槽成型部件卸除后安装挡渣墙。隔板将布料器分割成相互独立的两个空间,方便向布料器的中添加不同的工作衬耐火材料。
34.隔板4固定安装在挡渣墙安装槽成型部件3上,挡渣墙安装槽成型部件3的上部设置有卡槽,隔板4的下部设置有豁口,豁口的形状大小与挡渣墙安装槽成型部件3下部的形状大小相吻合;隔板下部的豁口深度与挡渣墙安装槽成型部件下部的高度相等,且隔板上部的高度大于或等于挡渣墙安装槽成型部件上部的卡槽深度,从而可以使隔板和挡渣墙安装槽成型部件卡扣在一起。
35.隔板4是厚度为2mm表面光滑的钢板,隔板4为波浪形曲面板;当隔板为波浪形曲面板时,可以增加隔板两侧不同工作衬材料的接触面积;隔板4的顶壁高出中间包上沿320mm;隔板4的顶壁焊接有抽拔吊钩,方便在复合工作衬成型过程中拔除隔板;胎模1为上宽下窄的倒梯形,以便于成型烘烤后脱模;挡渣墙安装槽成型部件3的宽度略大于中间包挡渣墙的厚度,以确保挡渣墙安装槽中挡渣墙的安装。
36.挡渣墙安装槽成型部件3为槽钢,槽钢的厚度等于中间包工作衬的总厚度100mm,槽钢的宽度为115mm,略大于中间包挡渣墙厚度105mm;槽钢的卡槽与隔板4的豁口可以呈“十”字形卡扣相互卡紧。布料器5呈上宽下窄的倒梯形,底部总宽度为100mm,与复合工作衬总厚度保持一致。
37.工作流程:
①
首先在包底涂抹一层厚度为65mm且mgo含量为67%的镁铬质涂料;
38.②
在中间包永久衬9长墙的两侧安放槽钢,每侧各对称安放两个;将胎模1平稳对称地卡入四个槽钢之间,再将隔板4分别卡入两侧槽钢,隔板4与胎模1和永久衬9之间的距离分别为34mm和64mm包括隔板厚度,确保工作衬总厚度为100mm;
39.③
在包底mgo含量为67%的镁铬质涂料表面再涂抹一层厚度为35mm且mgo含量为88%的镁质涂料;
40.④
将布料器5倒扣在胎模1和永久衬9之间,隔板4高出部分将布料器5一分为二;
41.⑤
在布料器5下方靠近永久衬9一侧布入mgo含量为67%的镁铬质涂料,靠近钢水一侧布入mgo含量为88%的镁质涂料;
42.⑥
当两侧布料高度超过渣线上方150mm左右时,启动电机开始振动,当两侧物料下沉至渣线以下50mm左右时,停止振动并将隔板4缓慢抽出;
43.⑦
再在渣线部位布入mgo含量为88%的镁质涂料,当物料布至包沿时再次开启电机振动,边振动边布料直至物料不再下沉时停止振动;
44.⑧
移除布料器5,自然养护8h后开始点火烘烤,控制胎模1内部温度在150℃下保温3h;
45.⑨
停止烘烤后,当复合工作衬与胎模1之间产生1mm左右的收缩缝时即可拔出胎模1;
46.⑩
将嵌入复合工作衬中的槽钢全部移除以备安装中间包挡渣墙。至此,复合中间包工作衬的施工完毕。
47.本实用例采用带有振动电机的内置胎模,加装槽钢、隔板和布料器等装置,根据中间包工作衬各部位的使用特点和要求,分别对包底、包壁和渣线工作衬进行复合施工、整体成型,达到既可以满足客户对中间包工作衬高mgo含量、低导热、高安全性的要求,又可以实现降低生产成本、节约镁质资源、减少生产能耗及co2排放等目的,具有很好社会经济效益和生态环境效益。
48.实施例2
49.采用实施例1的装置制备得到复合中间包工作衬,如图5所示,包括包底工作衬6、包壁工作衬7和渣线工作衬8,包底工作衬6成型于中间包包底上,包壁工作衬7和渣线工作衬8分别成型于中间包内壁上,且渣线工作衬8位于包壁工作衬7上方,包壁工作衬7包括第一工作衬2和第二工作衬10,第一工作衬2与第二工作衬10之间接触面紧密贴合。
50.在第一工作衬2和第二工作衬10的厚度方向:挡渣墙安装槽贯穿第一工作衬2和第二工作衬10。包底工作衬6也包括第一工作衬2和第二工作衬10,第一工作衬2与第二工作衬10之间接触面紧密贴合;渣线工作衬8为mgo含量为88wt%的镁质工作衬。该复合中间包工作衬既可以保留镁质工作衬的工作优点,又能减少镁质工作衬的使用量,降低镁质工作衬的消耗,节约中间包耐材成本,减少环境污染。
51.第一工作衬即为镁质工作衬,第二工作衬即为非镁质工作衬;镁质工作衬采用mgo含量为88%的镁质涂料,主原料选用95重烧镁砂;非镁质工作衬采用mgo含量为67%的镁铬质涂料,主原料选用镁铬质废砖;第一工作衬靠近高温钢水,考虑到中间包的寿命不甚长,本实施例中渣线工作衬8仍然采用上述mgo含量为88%的镁质涂料。
52.在本实施例中,复合中间包工作衬的总度厚为100mm,中间包涂料总用量在3.6吨左右,其中mgo含量为67%的镁铬质涂料用量为1.5吨,mgo含量为88%的镁质涂料用量2.1吨。本实施例的复合中间包工作衬适用于生产超低碳无间隙原子钢if钢,连浇炉数15炉11h。
53.将本实施例的复合中间包工作衬在实践中试用,结果表明,该复合中间包工作衬抗烧结性能和抗侵蚀性能优良,下线后翻包解体顺利;同时未发现中间包内钢水有明显增碳效应,钢水中非金属夹杂物也被控制在较低水平。本实施例中非镁质工作衬采用镁铬废砖为原料,促进了废物资源的循环利用,节约了优质镁砂资源,也极大幅地降低了生产成本,具有很好的社会经济效益和生态环境效益。
54.实施例3
55.如图6所示,一种复合中间包工作衬,包括包底工作衬6、包壁工作衬7和渣线工作衬8,包底工作衬6成型于中间包包底上,包壁工作衬7和渣线工作衬8分别成型于中间包内壁上,且渣线工作衬8位于包壁工作衬7上方,包壁工作衬7包括第一工作衬2和第二工作衬
10,第一工作衬2与第二工作衬10之间接触面紧密贴合。
56.在第一工作衬2和第二工作衬10的厚度方向:挡渣墙安装槽贯穿第一工作衬2和第二工作衬10。包底工作衬6也包括第一工作衬2和第二工作衬10,第一工作衬2与第二工作衬10之间接触面紧密贴合;渣线工作衬8为mgo含量为88wt%的镁质工作衬。
57.第一工作衬即为镁质工作衬,第二工作衬即为非镁质工作衬;镁质工作衬采用mgo含量为86%的镁质干式料,主原料选用91重烧镁砂;非镁质工作衬采用mgo含量为59%的镁硅质干式料,主原料选用镁橄榄石和91重烧镁砂;第一工作衬靠近高温钢水,考虑到中间包的寿命比较长,为确保安全,本实施例中渣线工作衬8采用mgo含量为92%的镁质干式料,主原料选用97电熔镁砂。
58.本实施例复合中间包工作衬的总度厚约120mm,中间包干式料总用量在5.8吨左右,其中59%的镁硅质干式料用量为2.1吨,mgo含量为86%的镁质干式料用量1.9吨,mgo含量为92%的镁质干式料用量1.8吨。本实施例适用于生产hrb400螺纹钢,可以满足钢水30h60h以上长时浇铸要求。同时,由于镁硅质工作衬的导热系数低,对钢水的保温效果更好,节约能耗的同时也有利提高浇铸钢水的质量。采用本实施例的复合中间包工作衬可以大幅降低生产成本、节约优质资源、降低生产能耗、减少co2排放等,具有很好的社会经济效益和生态环境效益。
59.显然,上述实施例仅仅是为清楚地说明所作的举例,而并非对实施方式的限定。对于所属领域的普通技术人员来说,在上述说明的基础上还可以做出其它不同形式的变化或变动。这里无需也无法对所有的实施方式予以穷举。而由此所引伸出的显而易见的变化或变动仍处于本专利申请权利要求的保护范围之中。