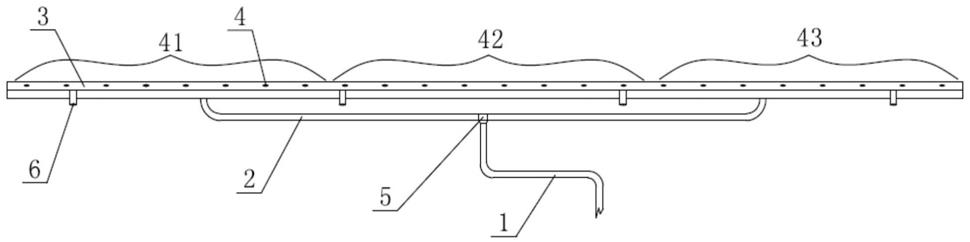
特气管路及平板式pecvd设备
技术领域
1.本技术涉及pecvd镀膜设备领域,具体涉及特气管路及平板式pecvd设备。
背景技术:2.在光伏产业中,pecvd镀膜设备将氨气和硅烷气体通过特气管路输送到反应腔室内,使气体在反应腔室发生反应并在基片上沉积出氮化硅膜。pecvd镀膜设备包括管式pecvd设备和平板式pecvd设备,相对管式pecvd设备,平板式pecvd设备因均匀性好和产量高的特点而得到广泛使用。
3.平板式pecvd设备包括向反应腔室输送气体的特气管路,特气管路包括连通反应腔室的均流管和连接均流管的进气管。在常规的平板式pecvd设备中,进气管通过至少两根分流管连接均流管,进气管通过分流管均匀为均流管供给特气,供气管通过均匀分布的特气孔往反应腔室中输送特气,使反应腔室中的基片镀膜均匀。
4.反应腔室相对于均流管两端面的侧壁上开设有排气孔,排气孔向外抽气以维持反应腔室内的气压平衡。但是,排气孔的设置会影响位于均流管两端部的特气孔,导致基片中间位置的膜厚偏高,两侧位置的膜厚偏低的问题。基片的膜厚不均匀会导致镀膜颜色的均匀性较差,同时在后期维护时会出现石英管烧黑的异常现象。
技术实现要素:5.针对上述问题,本技术提供了一种平板式pecvd设备的特气管路,通过改变分流管相对于均流管的分布位置,以降低均流管两端部的特气孔受排气孔的影响,提高膜厚的均匀性。
6.本实施例的第一方面提供了一种特气管路,包括均流管和分流管;所述均流管沿其轴向开设有特气孔;
7.所述特气孔包括位于所述均流管一端部的第一端部孔、位于所述均流管中部的中部孔以及位于所述均流管另一端部的第二端部孔;
8.所述分流管靠近所述均流管的两端面设置,所述分流管供给至所述第一端部孔和所述第二端部孔的供气量高于所述中部孔的供气量。
9.优选的,所述特气孔的数量三等分,所述分流管的数量为两根;两根所述分流管的连接位置与所述均流管相对应端面的距离为,所述均流管长度的1/8~2/7。
10.优选的,所述特气管路还包括位于所述均流管下方的进气管;所述进气管通过三通接头连接两根所述分流管的进口;所述分流管的出口连接至所述均流管的底部。
11.优选的,所述分流管与所述均流管采用焊接的方式固定连接。
12.优选的,所述均流管上还设有用于固定的螺母。
13.本实施例的第二方面提供了一种平板式pecvd设备,包括上述的特气管路。
14.本技术的技术方案改变了分流管与均流管的相对位置,通过提高分流管对第一端部孔和第二端部孔的供气量,以平衡排气孔对第一端部孔和第二端部孔的影响,从而保证
基片的膜厚均匀。本技术将分流管靠近供气管的两端面设置,分流管与均流管的连接位置离第一端部孔和第二端部孔的距离较近,离中部孔的距离较远;分流管在第一端部孔和第二端部孔处的供气量相对较高,在中部孔处的供气量相对较低,从而平衡排气孔对第一端部孔和第二端部孔的影响,改善镀膜颜色的均匀性较差的问题,避免石英管在后期维护时出现烧黑的异常现象。
附图说明
15.图1为特气管路的结构示意图。
16.图中,进气管1、分流管2、均流管3、特气孔4、第一端部孔41、中部孔42、第二端部孔43、三通接头5、螺母6。
具体实施方式
17.下面通过具体实施方式进一步详细的说明:
18.术语解释:
19.pecvd:是等离子增强型化学气相沉积(plasma enhanced chemical vapor deposition)简称。pecvd是借助微波使含有薄膜组成原子的气体电离,在局部形成等离子体,而等离子化学活性很强,很容易发生反应,在基片上沉积出所期望的薄膜。特气:pecvd中通入的sih4和nh3气体。
20.本实施例提供了一种平板式pecvd设备的特气管路,包括依次连接的进气管1、分流管2和均流管3。在本实施例中,均流管3的管壁沿其轴向开设有均匀分布的特气孔4,均流管3中的特气经特气孔4进入到反应腔室。
21.在本实施例中,特气孔4的数量三等分,包括自均流管3一端依次分布的第一端部孔41、中部孔42和第二端部孔43。第一端孔分布在均流管3的一端部,中部孔42分布在均流管3的中部,第二端部孔43分布在均流管3的第二端部。需要说明的是,本实施例中的三等分是指第一端部孔41、中部孔42和第二端部孔43具有数量相同的小孔。反应腔室是平板式pecvd设备中用于沉积氮化硅膜的部分。
22.在本实施例中,进气管1位于均流管3的下方,特气孔4开设在均流管3的顶部。进气管1的进气口连接供气设备,进气管1的出气口与分流管2的进口连接,分流管2的出口连接至均流管3的底部。
23.特气先从供气设备进入到进气管1,再经过分流管2分流到均流管3中,最后再通过均流管3上的特气孔4向反应腔室中输送特气。分流管2能够将进气管1中的特气分散供给到均流管3的不同部位,使不同部位的特气孔4具有相对均衡的供气量,进而保证基片上沉积的膜厚尽量一致,提高基片的镀膜品质。
24.由于反应腔室相对于均流管3两端的侧壁上开设有排气孔,特气孔4往反应腔室中输送特气的过程中,反应腔室需要利用排气孔向外抽气,以平衡反应腔室内部的气压。在传统的特气管路中,分流管2的设计仅考虑到各部分特气孔4的供气量,忽略了排气孔对第一端部孔41和第二端部孔43的影响,从而导致基片的膜厚不一致。排气孔将第一端部孔41和第二端部孔43输送的部分特气直接抽出,使第一端部孔41和第二端部孔43供给的部分特气无法反应并沉积在基片上,导致基片对应中部孔42的膜厚高于基片对第一端部孔41和第二
端部孔43的膜厚。
25.本实施例改变了分流管2与均流管3的相对位置,通过提高分流管2对第一端部孔41和第二端部孔43的供气量,以平衡排气孔对第一端部孔41和第二端部孔43的影响,从而保证基片的膜厚均匀。本实施例将分流管2靠近供气管的两端面设置,分流管2与均流管3的连接位置离第一端部孔41和第二端部孔43的距离较近,离中部孔42的距离较远;分流管2在第一端部孔41和第二端部孔43处的供气量相对较高,在中部孔42处的供气量相对较低,从而平衡排气孔对第一端部孔41和第二端部孔43的影响。
26.具体的,本实施例中的特气管路具有两根分流管2,进气管1的出气口通过三通接头5连接两根分流管2的进口,两根分流管2的出口采用焊接的方式与均流管3固定,以保证气密性良好,无漏气。两根分流管2的固定位置离相对应的均流管3两端面的距离为均流管3长度的1/8~2/7,例如1/7、1/6、1/5、1/4、2/9、2/11、3/11等。
27.如图1所示,均气管上均匀开设有24个特气孔4,特气孔4的间距为50mm,每个特气孔4大小一致。需要说明的是,由于最外侧的两个特气孔4离相对应的均流管3端面的距离较近,本实施例中的均流管3长度可视为最外侧两个特气孔4的距离。在本实施例中两个分流管2的出口的间距约为700mm,两根分流管2的出口离相对应的均流管3两端面的距离约为250mm。在均流管3上还设有4颗螺母6用于固定特气管路。
28.需要说明的是,分流管2的数量包括但不限于本技术提及的两根,可根据均流管3整体的供气量和排气孔的抽气量设置4根、5根等其他数量的分流管2。
29.本技术并不仅仅限于说明书和实施方式中所描述,因此对于熟悉领域的人员而言可容易地实现另外的优点和修改,故在不背离权利要求及等同范围所限定的一般概念的精神和范围的情况下,本技术并不限于特定的细节、代表性的设备和这里示出与描述的图示示例。