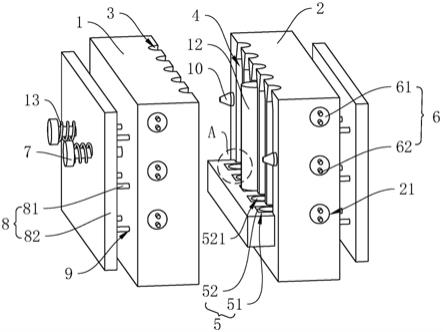
1.本技术涉及制芯机的技术领域,尤其是一种垂直分型制芯机砂芯内嵌冷铁芯盒结构。
背景技术:2.芯盒结构是采用热芯盒工艺制做覆膜砂芯的设备,由于汽车铸件产品结构不同,有的产品工艺要求砂芯内部需嵌入冷铁,以加快铸件在此处的冷却速度。
3.芯盒结构一般包括左砂盒、右砂盒以及底板,底板水平放置,左砂盒和右砂盒的下表面均与底板上表面抵接,左砂盒和右砂盒相互靠近的侧壁均开设有进砂槽;使用时,首先将冷铁放置在底板上表面,把左砂盒和右砂盒合好,合箱后注入砂土,通过对砂土进行加热成型,即可得到嵌有冷铁的砂芯。
4.针对上述中的相关技术,发明人认为存在有以下缺陷:在左砂盒与右砂盒合模过程中,冷铁位置无法固定,导致注砂后砂芯结构不均匀的现象。
技术实现要素:5.为了使砂芯结构均匀,本技术提供一种垂直分型制芯机砂芯内嵌冷铁芯盒结构。
6.本技术提供的一种垂直分型制芯机砂芯内嵌冷铁芯盒结构采用如下技术方案:一种垂直分型制芯机砂芯内嵌冷铁芯盒结构,包括左砂盒和右砂盒,左砂盒和右砂盒相互靠近的侧壁均开设有进砂槽;所述左砂盒与右砂盒之间设置有水平滑块,水平滑块上表面开设有用于放置冷铁的固定槽,左砂盒与右砂盒相互背离的一侧均设置有脱模组件。
7.通过采用上述技术方案,在左砂盒和右砂盒合模的过程中,水平滑块和固定槽对冷铁的位置进行了固定支撑的作用,从而达到了精准定位冷铁的效果,因此注砂时冷铁不易发生晃动,使得砂芯结构均匀。
8.可选的,固定槽设置有多个。
9.通过采用上述技术方案,多个固定槽的设置,制芯时冷铁置于固定槽内,可以同时对多个冷铁进行制芯,大大提高了制芯的工作效率。
10.可选的,固定槽内设置有可替换块,可替换块上表面开设有替换槽。
11.通过采用上述技术方案,当冷铁形状发生变换时,可以更换不同模型的可替换块,以满足不同形状冷铁的制芯需求,节约了材料,达到了快速制芯的效果。
12.可选的,左砂盒和右砂盒均开设有导热孔,导热孔位于左砂盒和右砂盒相互靠近一侧的内部,且导热孔的方向与左砂盒的长度方向相同,导热孔内插接有热芯加热装置,热芯加热装置包括电热棒和电线。
13.通过采用上述技术方案,热芯加热装置设置在左砂盒和右砂盒内部,减少了砂芯在加热过程中热量的消耗,节省了能量,采用电加热的方式,避免了有害气体的排放,保护了环境。
14.可选的,右砂盒靠近左砂盒的侧壁固定连接有定位销,左砂盒靠近右砂盒的侧壁
开设有销孔,定位销滑动插接于销孔内。
15.通过采用上述技术方案,使得右砂盒的定位销可以精准插入左砂盒开设的定位孔内,提高了合模的精度。
16.可选的,脱模组件包括脱模杆和垫板,垫板分别位于左砂盒和右砂盒相互背离的一侧,脱模杆与垫板垂直固定连接,脱模杆分别贯穿左砂盒和右砂盒,且脱模杆分别与左砂盒和右砂盒滑动连接;左砂盒和右砂盒相互靠近的侧壁均开设有模型槽,位于右砂盒一侧的脱模杆与水平滑块固定连接,且脱模杆位于模型槽内。
17.通过采用上述技术方案,右砂盒的脱模杆可以控制水平滑块进行左右移动;脱模杆位于模型槽内,脱模时,脱模杆可以将砂芯顶离模型槽,有利于砂芯的取出。
18.可选的,左砂盒远离右砂盒的一侧设置有螺栓;螺栓贯穿垫板并与左砂盒固定连接;螺栓周向外壁套设有弹簧,且弹簧位于垫板背离左砂盒的一侧。
19.通过采用上述技术方案,当水平滑块左侧端面与左砂盒抵接时,弹簧得到压缩,此时脱模杆与砂芯周向侧壁抵接;脱模时,处于压缩状态的弹簧得到伸展,弹簧给垫板施加靠近砂芯方向的力,砂芯和冷铁被顶离左砂盒,实现了取芯过程的自动化,提高了制芯工序的生产效率。
20.可选的,定位销背离右砂盒的一侧呈尖端状。
21.通过采用上述技术方案,尖端状的定位销便于插入定位孔内。
22.综上所述,本技术包括以下至少一种有益技术效果:
23.1.水平滑块上表面开设有用于放置冷铁的固定槽,解决了冷铁无法精准定位、注砂时易晃动的现象,达到了对冷铁精准定位、砂芯结构均匀的效果,提高了砂芯的成型质量;
24.2.脱模组件和弹簧的配合使用,开盒时,弹簧的压缩状态得到恢复,给砂芯以向右的力,砂芯被顶离左砂盒,自动脱模,实现了取芯过程的自动化,提高了制芯工序的生产效率;
25.3.固定槽内设置有可替换块,可替换块上表面开设有替换槽,该设计可以满足对不同形状的冷铁进行固定,且固定时只需更换替换槽即可满足需求,节约了材料,提高了模具的利用率。
附图说明
26.图1是本技术实施例的整体结构示意图;
27.图2是显示图1中左砂盒的剖视图;
28.图3是图1中a部分的局部放大示意图。
29.附图标记说明:1、左砂盒;2、右砂盒;21、导热孔;3、进砂槽;4、模型槽;5、水平滑块;51、固定槽;52、可替换块;521、替换槽;6、热芯加热装置;61、电热棒;62、电线;7、螺栓;8、脱模组件;81、脱模杆;82、垫板;9、通孔;10、定位销;11、销孔;12、冷铁;13、弹簧。
具体实施方式
30.以下结合附图1-3对本技术作进一步详细说明。
31.本技术实施例公开一种垂直分型制芯机砂芯内嵌冷铁芯盒结构。
32.参考图1和图2,垂直分型制芯机砂芯内嵌冷铁芯盒结构包括左砂盒1、右砂盒2,左砂盒1和右砂盒2水平放置,左砂盒1和右砂盒2相互靠近的侧壁均开设有进砂槽3,左砂盒1和右砂盒2的周向内壁均开设有模型槽4,当左砂盒1和右砂盒2合模时,进砂槽3形成了进砂孔,模型槽4形成了空腔;左砂盒1与右砂盒2之间设置有水平滑块5,水平滑块5上表面开设有用于放置冷铁12的固定槽51,左砂盒1与右砂盒2相互背离的一侧均设置有调节冷铁12与左砂盒1之间相对位置关系的脱模组件8;制芯时,将冷铁12置于水平滑块5开设的固定槽51内,将左砂盒1和右砂盒2进行合箱形成制芯盒,合箱后对制芯盒进行射砂处理,待射砂完成后,对砂土进行加热成型,即可得到嵌有冷铁的砂芯;水平滑块5和固定槽51对冷铁12起到了精准定位的效果,使得加热成型后的嵌有冷铁12的砂芯结构均匀,提高了砂芯的质量。
33.参考图1和图2,脱模组件8包括脱模杆81和垫板82,垫板82分别位于左砂盒1和右砂盒2相互背离的一侧,脱模杆81与垫板82垂直固定连接,脱模杆81分别贯穿左砂盒1和右砂盒2,脱模杆81分别与左砂盒1和右砂盒2滑动连接,且脱模杆81位于模型槽4内;脱模杆81在左砂盒1和右砂盒2上形成通孔9,通孔9的开设方向与左砂盒1和右砂盒2的宽度方向相同,通孔9均开设在模型槽4内,且通孔9的数量和脱模杆81的数量相同,本实施例中通孔9设置有15个。
34.参考图1和图2,右砂盒2靠近左砂盒1的一侧设置有定位销10,左砂盒1靠近右砂盒2的一侧开设有销孔11,定位销10滑动插接于销孔11内,且定位销10背离右砂盒2的一侧呈尖端状,便于将定位销10插进销孔11内,可以快速对齐左砂盒1和右砂盒2,提高了合模的精度。
35.参考图1和图2,左砂盒1和右砂盒2均开设有导热孔21,导热孔21位于左砂盒1和右砂盒2相互靠近的一侧,且导热孔21的方向与左砂盒1的长度方向相同,导热孔21内插接有热芯加热装置6,本实施例中热芯加热装置6包括电热棒61和电线62,提高了加热效率,减少了能源的浪费。
36.参考图1,位于右砂盒2一侧的脱模杆81与水平滑块5固定连接,左砂盒1远离右砂盒2的一侧设置有螺栓7,螺栓7贯穿垫板82并与左砂盒1固定连接,且螺栓7与垫板82滑动连接;螺栓7周向外壁套设有弹簧13,且弹簧13位于垫板82背离左砂盒1的一侧。
37.参考图1和图2,在制芯时,脱模杆81向背离左砂盒1和右砂盒2两侧移动,右砂盒2的脱模杆81带动水平滑块5进行移动,当水平滑块5与左砂盒1抵接时,弹簧13受到挤压后收缩,此时弹簧13处于压缩状态,水平滑块5停止移动,开始对制芯盒进行射砂处理,待射砂完成后,通过热芯加热装置6对砂土进行加热成型,开盒时,此时弹簧13的压缩状态得到恢复,弹簧13给垫板82施加靠近右砂盒2方向的力,即左砂盒1的脱模杆81将砂芯顶离左砂盒1,完成取芯。
38.参考图1和3,固定槽51内设置有可替换块52,可替换块52上表面开设有替换槽521,冷铁12插接在替换槽521内,固定槽51的开设对水平滑块5起到了精准定位的效果,本实施例中固定槽51开设有5个,提高了砂芯的生产效率;且固定槽51的形状可变换调整,当冷铁12形状发生变化时,只需要更换可替换块52,即可满足固定不同形状冷铁12的需求,减少了资源的浪费,提高了模具的利用率。
39.本技术实施例一种垂直分型制芯机砂芯内嵌冷铁芯盒结构的实施原理为:在保证左砂盒1、右砂盒2以及热芯加热装置6能完成正常制芯的基础上,通过在空腔内设置水平滑
块5,水平滑块5上表面开设有用于放置冷铁12的固定槽51,制芯时将冷铁12放置固定槽51内,冷铁21位置得到固定,达到了对冷铁12精准定位的效果,注砂时,冷铁不易晃动,使得嵌有冷铁12的砂芯结构均匀,提高了砂芯的质量。
40.本具体实施方式的实施例均为本技术的较佳实施例,并非依此限制本技术的保护范围,故:凡依本技术的结构、形状、原理所做的等效变化,均应涵盖于本技术的保护范围之内。