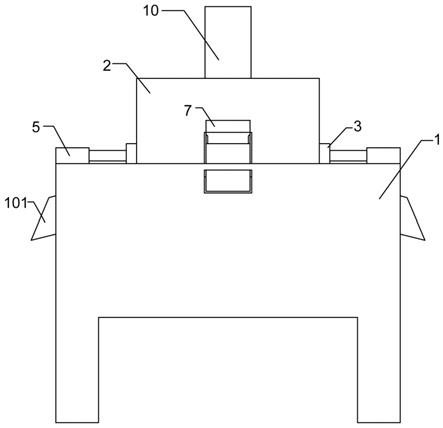
1.本实用新型属于金刚石复合片技术领域,具体涉及一种标准化的金刚石复合片自动化压取装置。
背景技术:2.金刚石复合片多在高温、高应力条件下工作,由于作为金刚石烧结助剂的钴与金刚石的热膨胀系数差别很大,在工作过程中容易造成金刚石层内金刚石晶粒脱落,因此会降低pcd的使用性能,另外,当温度高于700℃时,烧结助剂金属钴、铁等会催化金刚石向石墨发生逆转变,使pcd的硬度和耐磨性急剧下降,因此,除去pcd金刚石层中的金属烧结助剂,可大幅提高pcd的使用性能。
3.国内外去除金属烧结助剂的方式多采用腐蚀性极强的一种或几种强酸的混合溶液作为脱钴试剂,这就需要有耐腐蚀的防护禁锢装置来保护金刚石复合片的合金基座,为了降低员工的操作难度,而采用了可以通过机器压入的防护禁锢装置,该防护禁锢装置采用双层结构,复合片需要先内衬一层聚丙烯材料,然后再压入高分子防腐材料制成的防护禁锢装置中。
4.上述的防护禁锢装置在完成去钴后,再将复合片取出时较为繁琐,需要先将复合片连同聚丙烯层一起压出,再换机器将复合片从聚丙烯层中压出,由于复合片防护禁锢装置的压力较大,这两部工序不仅慢,员工操作也非常吃力,因此需要开发一套半自动化设备,可以快速取出复合片的同时,还能够将夹具和内衬层有效的分开。
5.基于此,研究一种标准化的金刚石复合片自动化压取装置是必要的。
技术实现要素:6.针对现有设备存在的缺陷和问题,本实用新型提供一种标准化的金刚石复合片自动化压取装置,有效的解决了现有复合片从防护工件中取出时较为繁琐,需要先将复合片连同聚丙烯层一起压出,再换机器将复合片从聚丙烯层中压出,由于复合片防护禁锢装置的压力较大,这两部工序不仅慢,员工操作也非常吃力的问题。
7.本实用新型解决其技术问题所采用的方案是:一种标准化的金刚石复合片自动化压取装置,包括桌架、上层夹持机构、下层开合机构和压取机构; 所述桌架的中部设置有落料孔,桌架内部设置有倾斜向下设置的压取物通道,压取物通道的上部与落料孔连通;所述下层开合机构包括两相对设置的定位块、分别位于两定位块后侧的第一同步驱动结构和定位块,两开合块的内侧均呈对应设置的台阶状结构,从而当两开合块合并时,形成上部的限位台和下部的下料孔,其中下料孔与落料孔连通,限位台的上部设置工件放置区;所述定位块设置在开合块的后侧,第一同步驱动机构设置在定位块的后侧;所述上层夹持机构包括第二同步驱动结构和夹环;所述第二同步驱动结构设置在定位块上,并驱动夹环向左或向右运动;所述工件放置区的后侧设置有顶推块,顶推块的后侧设置有第三驱动结构;所述压取机构包括压取气缸,所述桌架的上部设置有安全罩,压取气缸设置在安全罩上,其驱动杆
连接有压取块,所述压取块与所述下料孔对应。
8.进一步的,所述第一同步驱动结构包括电动推杆,其输出杆与定位块的后侧固定。
9.进一步的,所述压取气缸的压取块内设置有将复合片本体和pp层分离的微型气缸,所述安全罩前侧对应工件放置区设置有出入口,其外侧延伸有倾斜设置的导料板。
10.进一步的,所述第二同步驱动结构包括同步气缸,所述同步气缸的输出杆与夹环固定。
11.进一步的,所述第三驱动结构包括顶推气缸,所述顶推气缸的输出杆与顶推块相固定,且顶推气缸底部设置有支撑座。
12.本实用新型的有益效果:本实用新型针对现有复合片取出时较为繁琐,员工操作非常吃力的问题,提供了一种能够代替人工,降低操作难度,提高了生产效率,能够满足生产需求的标准化的金刚石复合片自动化压取装置。
13.本实用新型为了能够实现代替人工对防护工件内的金刚石复合片进行压取的效果,在安全罩上设置了压取气缸,通过压取气缸的压取块将固定好位置的防护工件中的金刚石复合片压取出来,从而降低工作强度,提高工作效率。
14.本实用新型为了保证压取气缸能够准确且稳定的对防护工件内的金刚石复合片进行压取,设置了能够对防护工件位置进行固定的第二同步驱动结构,即通过同步气缸驱动夹环向左或向右运动,对防护工件进行夹持和释放,并且在对防护工件位置固定后,能够保证防护工件与压取气缸的压取块位置准确对应,顺利完成金刚石复合片的压取作业。
15.本实用新型为了给金刚石复合片提供下落的空间,设置了下层开合机构,通过在两开合块的内侧对应设置台阶状结构,能够限制金刚石复合片外侧pp层的台阶,目的是实现金刚石复合片与其外侧pp保护层的快速分离工作,分离后的金刚石复合片穿过下料孔落入压取物通道内自动排出,而停留在台阶上的pp保护层则会通过两个对应的开合块进行相互远离,从而自动落入压取物通道内排出。
16.本实用新型为了降低操作难度,设置了第一同步驱动结构、第二同步驱动结构和第三同步驱动结构,依次控制两开合块的距离调节、夹环对防护工件的夹持和顶推块推动复合片防护工件的工作。
17.本实用新型为了便于对复合片防护工件的取出和放入,在安全罩上设置了出入口,且将第三同步驱动结构设置在了对应出入口的位置,通过顶推气缸控制顶推块向防护工件移动,使顶推块能够将工件放置区的防护工件从出入口处推出来,无需工作人员再手动将防护工件取出,给工作人员提供了极大的便利,也进一步降低了操作难度。
18.本实用新型为了避免压取气缸的压取块难与限位台以及下料孔大小匹配的情况,在压取块内又设置了微型气缸,通过微型气缸的输出杆来进行金刚石复合片与pp保护层的分离工作,保证了压取工作的稳定性。
附图说明
19.图1为本实用新型主视图。
20.图2为本实用新型剖视图。
21.图3为本实用新型桌架结构的俯视图。
22.图4为本实用新型开合块结构的俯视图。
23.图中:1、桌架;101、压取物通道;2、安全罩;3、定位块;4、顶推块;5、电动推杆;6、开合块;601、限位台;602、下料孔;7、出入口;8、夹环;9、同步气缸;10、压取气缸;11、微型气缸;12、压取块。
具体实施方式
24.下面结合附图和实施例对本实用新型进一步说明。
25.实施例1:本实施例旨在提供一种标准化的金刚石复合片自动化压取装置,主要用于代替人工将金刚石复合片从防护工件中压取出来,降低操作难度,提高工作效率。
26.如图2所示,包括桌架1、上层夹持机构、下层开合机构和压取机构,桌架的中部设置有落料孔,桌架内部设置有倾斜向下设置的压取物通道101,压取物通道101的上部与落料孔连通,便于压取后的金刚石复合片自动从压取物通道101滑出,减小劳动力,加快工作效率。
27.如图1、图2和图4所示,下层开合机构包括两相对设置的定位块3、分别位于两定位块3后侧的第一同步驱动结构和定位块3,第一同步驱动结构包括电动推杆5,其输出杆与定位块3的后侧固定,两开合块6的内侧均呈对应设置的台阶状结构,从而当两开合块6合并时,形成上部的限位台601和下部的下料孔602,其中下料孔602与落料孔连通,限位台601的上部设置工件放置区;定位块3设置在开合块6的后侧,第一同步驱动机构设置在定位块3的后侧,为了给金刚石复合片提供下落的空间,设置了下层开合机构,通过在两开合块6的内侧对应设置台阶状结构,能够限制金刚石复合片外侧pp层的台阶,目的是实现金刚石复合片与其外侧pp保护层的快速分离工作,分离后的金刚石复合片穿过下料孔602落入压取物通道101内自动排出,而停留在台阶上的pp保护层则会通过两个对应的开合块6进行相互远离,从而自动落入压取物通道101内排出,极大地降低了操作难度,代替人工作业,大幅度提高生产效率。
28.如图1图2和图3所示,上层夹持机构包括第二同步驱动结构和夹环8;第二同步驱动结构设置在定位块3上,并驱动夹环8向左或向右运动;第二同步驱动结构包括同步气缸9,同步气缸的输出杆与夹环8固定,工件放置区的后侧设置有顶推块4,顶推块4的后侧设置有第三驱动结构;压取机构包括压取气缸10,桌架1的上部设置有安全罩2,压取气缸10设置在安全罩2上,其驱动杆连接有压取块12,压取块12与下料孔对应,为了保证压取气缸10能够准确且稳定的对防护工件内的金刚石复合片进行压取,设置了能够对防护工件位置进行固定的第二同步驱动结构,即通过同步气缸9驱动夹环8向左或向右运动,对防护工件进行夹持和释放,并且在对防护工件位置固定后,能够保证防护工件与压取气缸10的压取块12位置准确对应,顺利完成金刚石复合片的压取作业。
29.本实施例中,为了降低操作难度,设置了第一同步驱动结构、第二同步驱动结构和第三同步驱动结构,依次控制两开合块6的距离调节、夹环8对防护工件的夹持和顶推块4推动复合片防护工件的工作。
30.实施例2,如图1和图3所示,安全罩2前侧对应工件放置区设置有出入口7,其外侧延伸有倾斜设置的导料板,为了便于对复合片防护工件的取出和放入,在安全罩2上设置了出入口201,且将第三同步驱动结构设置在了对应出入口201的位置,第三驱动结构包括顶推气缸,顶推气缸的输出杆与顶推块4相固定,且顶推气缸底部设置有支撑座,通过顶推气
缸控制顶推块4向防护工件移动,使顶推块4能够将工件放置区的防护工件从出入口201处推出来,无需工作人员再手动将防护工件取出,给工作人员提供了极大的便利,也进一步降低了操作难度。
31.实施例3,如图2所示,压取气缸10的压取块12内设置有将复合片本体和pp层分离的微型气缸11,为了避免压取气缸10的压取块12难与限位台601以及下料孔602大小匹配的情况,在压取块12内又设置了微型气缸11,通过微型气缸11的输出杆来进行金刚石复合片与pp保护层的分离工作,保证了压取工作的稳定性。