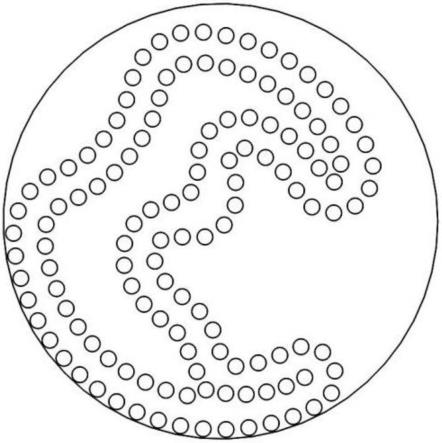
1.本实用新型涉及磁控溅射沉积薄膜,特别的,本实用新型涉及一种用于依据靶材-基片间距(tsd)等参数而设计的、产生均匀溅射、强化溅射、最大靶材利用率的磁控管。
背景技术:2.磁控溅射是物理气相沉积的一种。它是利用等离子轰击靶材,使靶材粒子脱落,沉积于基片表面形成薄膜的技术。通常,将磁控管置于靶材之后,其产生的磁场可以控制电子、离子在靶材表面的运动区域,从而提高工艺气体如ar气的在此区域的离化率,提高靶材表面等离子体浓度,进而提高薄膜沉积速率。磁控溅射技术广泛应用于半导体及微电子器件制造领域,为最常用的薄膜沉积方法。
3.如图1所示,其为典型的磁控溅射设备的示意图。该设备主要包括1、工艺腔体,其中有基片台、基片台上载有基片、工艺气体入口、靶材等;工艺腔体连接真空泵,由真空泵抽至真空;靶材连接至外部电源,电源使靶材表面产生负电场,使工艺气体离子化,并使之在电场作用下,撞击靶材,使靶材粒子溅出;2、磁控管,通常,将磁控管置于真空腔体之外,平行于靶材背面。磁控管可以是静止的,也可以是运动的。后者通常是围绕着靶材的中心线转动;磁控管上装有磁铁,通常是具有极性相反的磁铁相邻配对,其产生的磁场在靶材表面形成磁场分布,控制电子、离子在靶材表面运动的区域,提高等离子体浓度及薄膜沉积速率。
4.anderson等人在美国专利4,995,958和6,024,843中指出,为了达到对靶材的均匀腐蚀,磁控管在半径为r处的等离子体环中心的线长之和应该与半径成反比关系,即:
[0005][0006]
其中,r为该等离子体环中心线上某一点距靶材中心的距离,即此点对应的半径值;为磁控管在半径为r处的等离子体环中心的线长总和;k为与等离子强度及其他相关的常数;c为常数。e(r)为腐蚀曲线,进而他们推导出用于一固定的腐蚀曲线的微分公式具有一个标准解:
[0007][0008]
其中,θ为该等离子体轨道的最小半径,r和θ为该轨道的极坐标。
[0009]
图2为依据该理论设计出的磁控管。
[0010]
hong s.yang等人在美国专利7,186,319和中国专利cn1997768中也试图以一个公式、迭代修正程序来解决靶材径向腐蚀的不均匀性问题,他们认为如公式3:
[0011]
lr=arnꢀꢀꢀꢀꢀꢀꢀꢀꢀꢀ
(3)
[0012]
其中,a是一个常数;r为该等离子体环中心线上某一点距靶材中心的距离,即此点对应的半径值;为磁控管在半径为r处的等离子体环中心的线长总和;n为2附近的一个常数;n=2,通常对应均匀的靶材腐蚀;n《2,则对应靶材中心处有较大的靶材腐蚀;n》2,则靶材边缘处有较大的腐蚀。
[0013]
他们认为,当n=2时,,表明在一个单位径向增量内该等离子体轨道长度与半径成
正比,因此该公式与anderson等人的公式是一致的。但是,事实上,这两个公式并不一致。anderson等人的公式为公式4:
[0014][0015]
表明,dl/dr=c/k,为一个常数,并不与半径成正比。因此,hong s.yang等人基于
[0016]
lr=arnꢀꢀꢀꢀꢀꢀꢀꢀꢀꢀꢀꢀꢀ
(5)
[0017]
这一公式的迭代程序而设计磁控管是有一定局限性的。
[0018]
更重要的是,上述的磁控管专利,均只是看重靶材腐蚀的均匀性,而不顾及溅射薄膜的均匀性要求。事实上,磁控溅射过程中,如果仅仅要求靶材均匀腐蚀,并不一定能保证沉积薄膜的均匀性。
[0019]
例如,在rf(射频)溅射过程中,由于没有磁控管,靶材基本上是一个均匀腐蚀的过程。holland在vacuum deposition of thin film(chapman&hall ltd.,london,1970,p.149)一书中计算了在不同靶材-基片距离(tsd)为h的条件下,基片上沉积薄膜的厚度t,随其离源中心点的距离x的变化:
[0020][0021]
l为靶材半径。这个公式也适合溅射过程。考虑到圆形靶材、圆形基片的轴对称性,可以简化至在基片上单个直径上的薄膜厚度的分布(y=0,α=90
°
,a=h)holland获得如下的基片上沉积薄膜的厚度t,随其离中心点的距离x的变化,图形如图3所示,公式如下:
[0022][0023]
由图3可以看出,尽管rf溅射过程中,靶材的腐蚀是均匀的,但是:
[0024]
1、如果h/l较大,例如h/l=5,即tsd为靶材半径的5倍时,即使x/l=1,即基片半径与靶材半径一样的情况下,沉积薄膜的均匀性依然很好,即t/t0=0.98;
[0025]
2、如果h/l较小,例如h/l=0.5,即tsd为靶材半径的一半时,当x/l=1,即基片半径与靶材半径一样的情况下,沉积薄膜的均匀性变得很差,即t/t0=0.59;
[0026]
3.如果h/l较小,例如h/l=0.5,即tsd为靶材半径的一半时,要想获得较好的沉积薄膜的均匀性,如t/t0=0.98,则只能采用非常小的基片,如x/l=0.1,即基片半径只可以为靶材半径的十分之一。
[0027]
而沉积薄膜的均匀性要求,是磁控管设计的第一优先要求。沉积薄膜的均匀性,与具体的工艺参数、系统几何参数有关,尤其是与靶材和基片之间的距离(tsd)相关。
[0028]
而在实际的溅射过程中,通常希望利用较小的靶材、较大的基片(例如,12~14英寸靶材对应6~8英寸基片),同时也希望减少tsd(通常,tsd为1~4英寸)以增加溅射速率,这样可以一方面减少靶材费用,另一方面提高产能。因此在溅射中加入磁控管,形成磁控溅射是实现这一目标最好的方法。
[0029]
同时,磁控溅射设备,通常也会在基片台上、腔体内施加另外的电场、磁场。如施加rf偏置电压,以改善薄膜的性能,如致密度、应力等;又如,在基片周围施加磁场,以控制磁性薄膜的磁化方向。因此,我们在设计磁控管时,需要控制tsd的大小,以减少这些额外施加的电磁场与磁控管的相互干扰。
[0030]
而对于磁性材料靶材,磁控管的设计又有额外的要求。由于磁性靶材可以屏蔽磁控管产生的磁场,使其在靶材表明产生的磁场强度大大减小。因此,一方面,要增加磁控管强度;另一方面,也要减小其产生的等离子体环中心线的长度,进而提高电源施加于靶材的即时能量密度,从使磁性靶材的产生等离子体的电压减小,易于在靶材表面离化工艺气体,形成等离子体,并提高其浓度。
[0031]
因此,磁控管设计的基本原则是,满足:
[0032]
第一优先,沉积薄膜厚度的均匀性;
[0033]
第二优先,最大可能地提高靶材腐蚀率;
[0034]
第三优先,等离子体环中心线最短。
技术实现要素:[0035]
针对现有技术的不足,本实用新型提供了一种能够保证沉积薄膜厚度的均匀性,同时提高靶材腐蚀率并使等离子体环中心线较短的磁控管。
[0036]
为实现上述目的,本实用新型提供了如下技术方案:一种沉积均匀的磁控管,包括外磁极磁铁和内磁极磁铁,且外磁极磁铁和内磁极磁铁磁极性相反,外磁极磁铁和内磁极磁铁构成闭合环,此闭合环形成等离子体轨道,所述等离子体轨道接近或通过靶材中心,且其旋转扫过除靶材边缘外的大部分靶材表面。
[0037]
进一步的所述等离子体轨道旋转扫过位置距靶材边缘的距离为0-5mm。
[0038]
进一步的所述等离子体轨道中心线的长度l分布随靶材中心距离(x)的变化为l=axn,其中a是任意常数,n是变量,所述n值由公式
[0039][0040]
拟合计算获得。
[0041]
与现有技术相比,本实用新型的有益效果是:可以根据溅射工艺所需要的tsd的值来设计磁控管,以精确满足溅射工艺需求,同时,不仅可以达到沉积薄膜厚度的高均匀性,而且可以最大可能地提高靶材腐蚀率。
附图说明
[0042]
图1-图3为背景技术用附图;
[0043]
图4为将公式(8)简化的模型图;
[0044]
图5为不同tsd下沉积薄膜的厚度随距晶圆中心距离的变化图;
[0045]
图6为不同tsd下相对薄膜厚度随距晶圆中心距离的变化图;
[0046]
图7为本实用新型以14英寸靶材为例获得的磁控管结构图;
[0047]
图8为本实用新型中等离子体中心线长度与半径的关系图。
具体实施方式
[0048]
参照图4至图8对本实用新型沉积均匀的磁控管及其设计方法的实施例做进一步说明。
[0049]
在本实用新型的描述中,需要说明的是,对于方位词,如有术语“中心”,“横向(x)”、“纵向(y)”、“竖向(z)”、“长度”、“宽度”、“厚度”、“上”、“下”、“前”、“后”、“左”、“右”、“竖直”、“水平”、“顶”、“底”、“内”、“外”、“顺时针”、“逆时针”等指示方位和位置关系为基于附图所示的方位或位置关系,仅是为了便于叙述本实用新型和简化描述,而不是指示或暗示所指的装置或元件必须具有特定的方位、以特定方位构造和操作,不能理解为限制本实用新型的具体保护范围。
[0050]
此外,如有术语“第一”、“第二”仅用于描述目的,而不能理解为指示或暗示相对重要性或隐含指明技术特征的数量。由此,限定有“第一”、“第二”特征可以明示或者隐含包括一个或者多个该特征,在本实用新型描述中,“数个”、“若干”的含义是两个或两个以上,除非另有明确具体的限定。
[0051]
一种沉积均匀的磁控管,包括外磁极磁铁和内磁极磁铁,且外磁极磁铁和内磁极磁铁磁极性相反,外磁极磁铁和内磁极磁铁构成闭合环,可以在磁控溅射过程中,束缚带电粒子,提高气体离化率,形成等离子体轨道。
[0052]
如图7所示,本实用新型中的磁控管整体呈“蝙蝠”形状,该磁控管在磁控溅射设备上,围绕溅射靶材中心旋转。
[0053]
该等离子体轨道,优选地接近或通过靶材中心,且所述等离子体轨道旋转扫过位置距靶材边缘的距离为0-5mm,形成“full-face”溅射。
[0054]
该磁控管可以通过模拟,以调整内、外磁极磁铁的分布,使得等离子体轨道中心线的长度l分布随靶材中心距离(x)的变化为l=axn,其中a是任意常数,n是变量,与靶材半径、基片半径、设计的tsd均有关联。
[0055]
考虑靶材为圆形,磁控管在靶材背面、围绕靶材中心旋转;同时基片为圆形,且同轴平行与靶材的条件。由于轴对称性,可以简化为如图4所示的模型,即靶材为线状,半径为r,基片半径为r,两者的垂直距离(tsd)为h。
[0056]
如果假定,靶材上某点p,对于基片的沉积速率与作用在该点的所有磁场强度成正比,则基片上点q(k,0)的薄膜沉积厚度t可以写为:
[0057][0058]
其中,m为常数,考虑沉积薄膜均匀性的要求,即在晶圆上,各处的薄膜厚度近似相等,即可以解析上述公式。
[0059]
但是,上述公式的计算极为复杂,在实际应用中,可以进一步作以下近似,即靶材上某点p,对于基片的沉积速率仅与在该点的磁场强度成正比,这样,可以仅仅计算薄膜沉积厚度在无外加磁场的情况下随晶圆半径的变化,通过镜像,即可获得磁场强度在晶圆上分布的函数。
[0060]
以14英寸靶材,8英寸晶圆为例,解析上述公式,可以获得:
[0061][0062]
不同的(tsd)h=1,2,3,4英寸,沉积薄膜的厚度随距晶圆中心距离的变化如图5所示。
[0063]
进而,如果我们假定磁场的分布函数,其中,a是任意常数,n是变量。通过镜像,即可获得各个tsd(h)条件下磁场的分布函数h(x)=axn。
[0064]
并获得下表:
[0065]
hn12.8505922.5582932.2794440.93209
[0066]
可以归纳如下图6所示,从以上表和图6,我们注意到,
[0067]
1、随着tsd的变化,n值并不是固定的,n值可以在1到3之间变化;
[0068]
2、当h值较大时,n值接近1,表明磁控管由中心到边缘,所需磁场强度的变化为接近线性;
[0069]
3、当h值较小时,n值接近3,表明磁控管由中心到边缘,所需磁场强度在边缘急剧变强。
[0070]
一种沉积均匀的磁控管的设计方法,包括如下步骤:
[0071]
s1:确定靶材、晶圆的大小,以及所需要的理想的靶材和晶圆之间的距离(tsd)的大小;
[0072]
s2:通过公式
[0073][0074]
拟合计算,确定所需要的l=axn公式中的n值;
[0075]
s3:构建一个由内外磁极磁铁构成的闭合环;
[0076]
a.该闭合环的中心线的中心优先地接近或经过靶材中心;
[0077]
b.该闭合环的中心线在围绕靶材中心旋转时,须扫过除靶材边缘(0-5mm)外的大部分靶材表面;
[0078]
c.该闭合环的构建可以借助若干软件,将靶材分成若干(通常5-10)同心圆,并用软件自动计算相邻同心圆间等离子体轨道中心线的长度;并通过调试闭合环的分布,使得该闭合环所形成的等离子体轨道的中心线的长度l分布随靶材中心距离(x)的变化满足:l≈axn。
[0079]
如图7所示,其是以上述公式、实用新型的一个实施案例,为14英寸的“蝙蝠状”磁控管。
[0080]
1.该磁控管布局,当tsd=3.5in时,依照公式
[0081][0082]
计算获得的n值为~1.62。再依照上述步骤,
[0083]
2.将靶材分成6个等间距同心圆,其半径分别为1,2,3,4,5,6英寸;
[0084]
3.并在其上布置由内外磁极磁铁构成的闭合环,依据经验,该闭合环中心闭合环的初始形状可以设置为型,或“m”型。
[0085]
4.利用辅助软件,如solidworks,计算每一个闭合环内等离子体轨道中心线的长度,并考察是否符合:l≈axn,(n~1.62)。
[0086]
5.如果偏离,则反复调试内外磁极磁铁构成的闭合环的位置,直至满足要求。
[0087]
图7为依照此步骤完成的磁控管的结构,图8为等离子体中心线长度与半径的关系图,以图8为例等离子体中心线长度与半径的关系列于下表:
[0088]
r(in.)l(in)10.8822.1733.5846.859.27617.02
[0089]
以分布函数拟合,可以获得n值:~1.59,接近n~1.62。此条件下,沉积~100nm的nicrfe合金薄膜在8in晶圆上的薄膜的均匀性可以达到stdd%~0.50%(49pts,5mmee)。
[0090]
以上所述仅是本实用新型的优选实施方式,本实用新型的保护范围并不仅局限于上述实施例,凡属于本实用新型思路下的技术方案均属于本实用新型的保护范围。应当指出,对于本技术领域的普通技术人员来说,在不脱离本实用新型原理前提下的若干改进和润饰,这些改进和润饰也应视为本实用新型的保护范围。