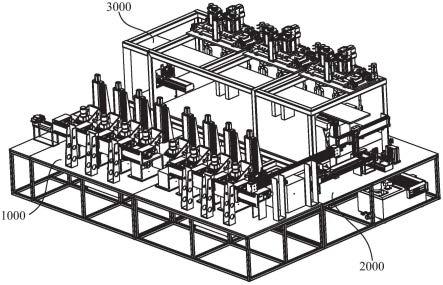
1.本实用新型涉及抛光技术领域,具体涉及一种自动抛光生产线。
背景技术:2.抛光是指利用机械、化学或电化学的作用,使工件表面粗糙度降低,以获得光亮、平整表面的加工方法。
3.现有工件在对不同侧面或部位进行抛光时需要在不同的设备上分别进行,如图1所示,现有手机后盖板在抛光时需要首先对手机后盖板上安装摄像头的通孔进行抛光,然后利用人工将完成通孔抛光的手机后盖板转运至周抛设备上,以对手机后盖板的侧面进行抛光,从而导致现有手机后盖板抛光的方式效率较低,且在人工转运过程中也容易出现手机后盖板损伤的现象。上述方案仅便于理解本技术中的方案,并不是对现有技术的限定。
技术实现要素:4.本实用新型的主要目的在于提供一种自动抛光生产线,以解决背景技术中提出的技术问题。
5.为实现上述目的,本实用新型提出的自动抛光生产线包括抛孔设备、中转设备和周抛设备,所述抛孔设备包括第一机架以及设置在所述第一机架上的上料平台、第一中转平台、第一转运装置、第二转运装置、至少一个粗抛孔装置和至少一个精抛孔装置,所述上料平台用于放置工件,所述第一转运装置用于在所述上料平台、粗抛孔装置、精抛孔装置以及第一中转平台之间依次运输工件,所述第二转运装置用于将所述第一中转平台上的工件放置在所述中转设备上;所述中转设备包括与所述第一机架相邻布置的第二机架以及设置在所述第二机架上的第二中转平台、定位装置和第三转运装置,所述第二中转平台用于接收所述第二转运装置上的工件,所述第三转运装置用于将所述第二中转平台上的工件抓取至所述定位装置上;所述周抛设备包括与所述第二机架相邻布置的第三机架以及设置在所述第三机架上的第四转运装置和至少一个周抛装置,所述第四转运装置用于将所述定位装置上的工件抓取至所述周抛装置上。
6.优选地,所述第一机架上还设有清洗装置,所述第二转运装置用于在所述第一中转平台、清洗装置和第二中转平台之间依次运输工件。
7.优选地,所述自动抛光生产线还包括用于叠层放置工件的治具以及设置在所述第一机架上的回流线体,所述上料平台上设有用于放置所述治具的第一放置位,所述第一转运装置用于在所述上料平台、粗抛孔装置、精抛孔装置以及第一中转平台之间依次运输所述治具,所述第二转运装置用于将所述第一中转平台上的所述治具放置在所述第二中转平台上以及将所述第二中转平台上空的所述治具放置在所述回流线体上。
8.优选地,所述治具包括底座、盖设在所述底座顶部的盖板以及设置在所述底座上的卡持件,所述底座顶部设有向下凹陷的收纳腔,所述盖板的一侧边设有第二转轴,所述盖板通过所述第二转轴与所述底座铰接,且所述第二转轴上套设有与所述底座连接的第一扭
簧,所述卡持件包括安装块、卡头和第二扭簧,所述安装块设置在所述底座的一侧面,所述卡头通过第一转轴与所述安装块铰接并可压持在所述盖板顶部,所述第二扭簧套设在所述第一转轴上并与所述安装块连接;所述第二中转平台上设有用于放置所述治具的第二放置位以及推动机构,所述推动机构用于推动所述卡头转动、以使得所述盖板在所述第一扭簧的驱动下翻转并打开所述收纳腔。
9.优选地,所述粗抛孔装置和所述精抛孔装置均为四个,四个所述粗抛孔装置和四个所述精抛孔装置依次沿直线间隔布置在所述第一机架上;所述第一转运装置包括设置在所述第一机架上的第一机械手和第二机械手,所述第一机械手用于在所述上料平台、四个所述粗抛孔装置以及靠近所述粗抛孔装置布置的一个所述精抛孔装置之间运输工件,所述第二机械手用于在四个所述精抛孔装置和第一中转平台之间运输工件。
10.优选地,所述粗抛孔装置包括设置在所述第一机架上的第一载具和粗抛模组,所述第一载具上设有用于放置工件的第三放置位,所述粗抛模组位于所述第三放置位的正上方;所述精抛孔装置包括设置在所述第一机架上的第二载具和精抛模组,所述第二载具上设有用于放置工件的第四放置位,所述精抛模组位于所述第四放置位的正上方。
11.优选地,所述第一载具包括设置在所述第一机架上的第一安装座、转动设置在所述第一安装座顶部的第一转盘以及驱动所述第一转盘移动的第一驱动机构,所述第三放置位位于所述第一转盘的顶部;所述第二载具包括设置在所述第一机架上的第二安装座、转动设置在所述第二安装座顶部的第二转盘以及驱动所述第二转盘移动的第二驱动机构,所述第四放置位位于所述第二转盘的顶部。
12.优选地,所述定位装置包括第一底板、第一挡板、驱动至少一个所述第一挡板移动的第三驱动机构和驱动所述第一底板移动的第四驱动机构,多个所述第一挡板围设在所述第一底板的周侧以构成收纳工件的定位腔,所述第三驱动机构驱动至少一个所述第一挡板朝向或远离所述定位腔移动,所述第四驱动机构驱动所述第一底板在所述第三转运装置的下料点与所述第四转运装置的上料点之间往复移动。
13.优选地,所述中转设备还包括设置在所述第二机架上并用于放置工件的第三中转平台,所述第三中转平台包括第二底板、第二挡板和第五驱动机构,所述第二挡板围设在所述第二底板的周侧以构成存储腔,所述第五驱动机构驱动所述底板沿竖直方向移动,所述第三转运装置用于将所述第二转运平台上的工件抓取至所述存储腔内以及用于将所述存储腔内的工件抓取至所述定位装置上。
14.优选地,所述周抛装置为三个,三个所述周抛装置沿直线依次布置,所述周抛设备还包括设置在所述第三机架上的下料平台,所述第四转运装置还用于将所述周抛装置上完成加工的工件放置在所述下料平台上。
15.本实用新型实施例提供的自动抛光生产线,通过第一转运装置将上料平台上的工件依次抓取至粗抛孔装置和精抛孔装置上进行孔抛光,并将完成抛光的工件放置在第一中转平台上,然后利用第二转运装置将第一中转平台上的工件放置在第二中转平台上,再利用第三转运装置将第二中转平台上的工件放置在定位装置上进行定位,最后利用第四转运装置将定位装置上存储的若干个工件一次性放置在周抛装置上进行周侧抛光,以此实现了自动完成工件的抛光工序,有利于提升抛光效率以及避免出现人工转运工件时损伤工件的情况。
附图说明
16.图1为现有手机后盖板的结构示意图;
17.图2为本实用新型中自动抛光生产线一实施例的结构示意图;
18.图3为图2中所示抛孔设备的结构示意图;
19.图4为图2中所示中转设备的结构示意图;
20.图5为图2中所示周抛设备的结构示意图;
21.图6为图3中所示上料平台的结构示意图;
22.图7为图3中所示清洗装置的结构示意图;
23.图8为本实用新型中治具一实施例的结构示意图;
24.图9为图3中所示第二转运装置的结构示意图;
25.图10为图4中所示第二中转平台的结构示意图;
26.图11为图3中所示第一机械手的结构示意图;
27.图12为图3中所示粗抛孔装置的结构示意图;
28.图13为图12中所示第一载具的结构示意图;
29.图14为图4中所示定位装置的结构示意图;
30.图15为图4中所示第三中转平台的结构示意图;
31.图16为图4中所示第三转运装置的结构示意图;
32.图17为图5中所示周抛装置的结构示意图;
33.图18为图5中所示下料装置的结构示意图;
34.图19为图5中所示第四转运装置的结构示意图。
具体实施方式
35.下面将结合本实用新型实施例中的附图,对本实用新型实施例中的技术方案进行清楚、完整地描述,显然,所描述的实施例仅仅是本实用新型的一部分实施例,而不是全部的实施例。基于本实用新型中的实施例,本领域普通技术人员在没有作出创造性劳动前提下所获得的所有其他实施例,都属于本实用新型保护的范围。
36.需要说明,本实用新型实施例中所有方向性指示(诸如上、下、左、右、前、后......)仅用于解释在某一特定姿态(如附图所示)下各部件之间的相对位置关系、运动情况等,如果该特定姿态发生改变时,则该方向性指示也相应地随之改变。
37.还需要说明的是,当元件被称为“固定于”或“设置于”另一个元件上时,它可以直接在另一个元件上或者可能同时存在居中元件。当一个元件被称为是“连接”另一个元件,它可以是直接连接另一个元件或者可能同时存在居中元件。
38.另外,在本实用新型中涉及“第一”、“第二”等的描述仅用于描述目的,而不能理解为指示或暗示其相对重要性或者隐含指明所指示的技术特征的数量。由此,限定有“第一”、“第二”的特征可以明示或者隐含地包括至少一个该特征。另外,各个实施例之间的技术方案可以相互结合,但是必须是以本领域普通技术人员能够实现为基础,当技术方案的结合出现相互矛盾或无法实现时应当认为这种技术方案的结合不存在,也不在本实用新型要求的保护范围之内。
39.本实用新型提出一种自动抛光生产线,特别适用于对具有通孔的工件进行抛光,
如手机后盖板4200,如图2至图6所示,该自动抛光生产线包括抛孔设备1000、中转设备2000和周抛设备3000,抛孔设备1000包括第一机架1100以及设置在第一机架1100上的上料平台1200、第一中转平台1300、第一转运装置1400、第二转运装置1500、至少一个粗抛孔装置1600和至少一个精抛孔装置1700,上料平台1200用于放置工件,第一转运装置1400用于在上料平台1200、粗抛孔装置1600、精抛孔装置1700以及第一中转平台1300之间依次运输工件,第二转运装置1500用于将第一中转平台1300上的工件放置在中转设备2000上;中转设备2000包括与第一机架1100相邻布置的第二机架2100以及设置在第二机架2100上的第二中转平台2200、定位装置2300和第三转运装置2400,第二中转平台2200用于接收第二转运装置1500上的工件,第三转运装置2400用于将第二中转平台2200上的工件抓取至定位装置2300上;周抛设备3000包括与第二机架2100相邻布置的第三机架3100以及设置在第三机架3100上的第四转运装置3200和至少一个周抛装置3300,第四转运装置3200用于将定位装置2300上的工件抓取至周抛装置3300上。
40.其中,第一机架1100、第二机架2100和第三机架3100均优选采用框架结构,至于第一机架1100、第二机架2100和第三机架3100的摆放方式是可以是沿直线布置呈一字形,也可以呈u字形布置。上料平台1200可以是固定设置在第一机架1100上的架体以用于放置工件,如图6所示,也可以是上料平台1200包括用于放置工件的第一载物板1210和驱动第一载物板1210移动的第六驱动机构1220,从而便于利用第六驱动机构1220驱动第一载物板1210在工件上料点(可以人工上料或通过机械手自动上料)与第一转运装置1400的上料点之间往复移动。第一转运装置1400和第二转运装置1500可以是采用机械手的形式运输工件,粗抛孔装置1600和精抛孔装置1700参照现有形式进行设置即可,即将抛光头插入工件上的通孔内后利用抛光头的自转进行抛光,具体结构在此不作具体说明。第一中转平台1300可以是参照上料平台1200进行设置,以便于暂时放置工件。第二中转平台2200也可以是参照上料平台1200进行设置,以便于暂时存放工件,定位装置2300用于对工件进行定位,以便于第四转运装置3200将工件精准放置在周抛装置3300上,具体结构可参照现有形式进行布置,第三转运装置2400可以是采用机械手的形式运输工件。第四转运装置3200可以是采用机械手的形式运输工件,周抛装置3300具体的原理则是驱动堆叠的手机后盖板4200自转,并利用在其周侧设置的抛光件对手机后盖板4200的侧面进行抛光,此时抛光件也需自转以及水平移动,具体的结构参照现有周抛设备3000进行设置。本方案具体工作原理为:首先将工件放置在上料平台1200上(此时上料平台1200上可堆叠存放多干工件),然后利用第一转运装置1400将上料平台1200上的工件放置在粗抛孔装置1600上进行粗抛孔(此时第一转运装置1400一次性可只抓取一个工件),再利用第一转运装置1400将完成粗抛孔的工件放置在精抛孔装置1700上进行精抛孔,在利用第一转运装置1400将完成精抛孔的工件放置在第一中转平台1300上,在利用第二转运装置1500将第一中转平台1300上的工件放置在第二中转平台2200上,再利用第三转运装置2400将第二中转平台2200上的工件放置在定位装置2300上,最后利用第四转运装置3200将定位装置2300上存储的若干工件一次性抓取至周抛装置3300上进行周侧抛光即可。本实施例中,通过第一转运装置1400将上料平台1200上的工件依次抓取至粗抛孔装置1600和精抛孔装置1700上进行孔抛光,并将完成抛光的工件放置在第一中转平台1300上,然后利用第二转运装置1500将第一中转平台1300上的工件放置在第二中转平台2200上,再利用第三转运装置2400将第二中转平台2200上的工件放置在定位装
置2300上进行定位,最后利用第四转运装置3200将定位装置2300上存储的若干个工件一次性放置在周抛装置3300上进行周侧抛光,以此实现了自动完成了工件所有抛光工序,有利于提升抛光效率以及避免出现人工转运工件时损伤工件的情况。
41.在一较佳实施例中,如图3和图7所示,优选第一机架1100上还设有清洗装置1800,第二转运装置1500用于在第一中转平台1300、清洗装置1800和第二中转平台2200之间依次运输工件。其中,优选清洗装置1800包括第一收集盒1810、设置在第一收集盒1810内的第七驱动机构1820、与第七驱动机构1820的输出端连接的第二载物板1830以及喷淋风干系统1840,第一收集盒1810的顶部的一端具有一用于取放料的取放料缺口,第七驱动机构1820优选为电机+丝杠机构,第二载物板1830上具有一用于放置工件的第五放置位,喷淋风干系统1840的出液嘴和风干系统的出气嘴位于第一收集盒1810内。本实施例中,第七驱动机构1820驱动第二载物板1830移动至取放料缺口的正下方,从而便于第二转运装置1500将工件放置在第五放置位上,然后第七驱动机构1820驱动第二载物板1830远离取放料缺口移动,并使得工件位于出液嘴和出气嘴的正下方进行清洗以及风干,在完成清洗和风干后由第七驱动机构1820驱动第二载物板1830朝向取放料缺口移动,以此便于第二转运装置1500抓取清洗完成后的工件并将其放置在第二中转平台2200上。
42.在一较佳实施例中,如图3和图8所示,优选自动抛光生产线还包括用于叠层放置工件的治具4000以及设置在第一机架1100上的回流线体1110,上料平台1200上设有用于放置治具4000的第一放置位1211,第一转运装置1400用于在上料平台1200、粗抛孔装置1600、精抛孔装置1700以及第一中转平台1300之间依次运输治具4000,第二转运装置1500用于将第一中转平台1300上的治具4000放置在第二中转平台2200上以及将第二中转平台2200上空的治具4000放置在回流线体1110上。其中,优选治具4000上具有一个腔体,以用于叠层放置多个工件,从而便于第一转运装置1400只需抓取治具4000即可一次性运输多个工件,而粗抛孔装置1600和精抛孔装置1700也可一次性对多个工件进行孔抛光,提升了抛光效率。当然,也可以是不采用治具4000的形式放置工件,还可以是第一转运装置1400直接抓取多个工件,而粗抛孔装置1600和精抛孔装置1700上设有固定结构固定多个工件,也可提升抛光效率。此时,优选治具4000内放置工件的形式为隔板和工件交替放置,从而有利于避免相邻两个工件摩擦出现损伤,而第一放置位1211位于上述第一载物板1210上。具体工作时,在第二转运装置1500将治具4000从清洗装置1800抓取至第二中转平台2200上后,利用第三转运装置2400将治具4000内的工件抓取至定位装置2300上以及利用第二转运装置1500将隔板以及空的治具4000放置在回流线体1110上,优选回流线体1110的输出端位于上料平台1200的一侧,从而便于治具4000以及隔板的回收。如图9所示,此时,优选第二转运装置1500上具有两个第二抓取头1510,其中一个第二抓取头1510用于抓取治具4000,另一个第二抓取头1510用于抓取隔板。
43.在一较佳实施例中,如图8和图10所示,优选治具4000包括底座4100、盖设在底座4100顶部的盖板4200以及设置在底座4100上的卡持件4300,底座4100顶部设有向下凹陷的收纳腔4110,盖板4200的一侧边设有第二转轴,盖板4200通过第二转轴与底座4100铰接,且第二转轴上套设有与底座4100连接的第一扭簧,卡持件4300包括安装块4310、卡头4320和第二扭簧,安装块4310设置在底座4100的一侧面,卡头4320通过第一转轴与安装块4310铰接并可压持在盖板4200顶部,第二扭簧套设在第一转轴上并与安装块4310连接;第二中转
平台2200上设有用于放置治具4000的第二放置位2221以及推动机构2210,推动机构2210用于推动卡头4320转动、以使得盖板4200在第一扭簧的驱动下翻转并打开收纳腔4110。
44.其中,优选收纳腔4110为与工件形状相适配的腔体,盖板4200只遮盖收纳腔4110开口端的部分区域,即使得工件上的通孔部位露出,以便于进行抛孔工序。推动机构2210可以是直线气缸等部件,以便于驱动治具4000中的卡头4320转动,从而释放盖板4200以使得盖板4200可在第一扭簧的驱动下翻转,以便于第二转运装置1500抓取收纳腔4110内的隔板以及空的治具4000以及便于第三转运装置2400抓取收纳腔4110内的工件。本实施例中,在将预设数量的工件放置在收纳腔4110内后,通过翻转隔板并使得盖板4200的底面与最顶面的隔板接触,最后利用卡头4320抵接在盖板4200的顶部以完成工件的放置工序,从而有利于避免出现工件在加工或运输时在收纳腔4110内移动的情况。
45.在一较佳实施例中,如图3和图11所示,优选粗抛孔装置1600和精抛孔装置1700均为四个,四个粗抛孔装置1600和四个精抛孔装置1700依次沿直线间隔布置在第一机架1100上;第一转运装置1400包括设置在第一机架1100上的第一机械手1410和第二机械手1420,第一机械手1410用于在上料平台1200、四个粗抛孔装置1600以及靠近粗抛孔装置1600布置的一个精抛孔装置1700之间运输工件,第二机械手1420用于在四个精抛孔装置1700和第一中转平台1300之间运输工件。
46.其中,粗抛孔装置1600和精抛孔装置1700的数量与工件上通孔的数量一致,由于进行说明的工件为手机后盖板4200,且该手机后盖板4200上具有四个通孔,即粗抛孔装置1600和精抛孔装置1700均为四个,即每一个粗抛孔装置1600和精抛孔装置1700只针对工件上的同一个通孔进行抛光,且优选上料平台1200、四个粗抛孔装置1600、四个精抛孔装置1700以及第一中转平台1300沿直线布置,且相邻两个部件的间距相等。优选第一机械手1410与第二机械手1420结构一致,现以第一机械手1410作具体说明,第一机械手1410上设有五个第一抓取头1411,在只抓取一个工件的情况下可采用真空吸附的方式,在抓取上述治具4000的情况没有选采用夹持的方式,第一机械手1410具有驱动第一抓取头1411沿直线移动以及沿竖直方向移动的功能,从而便于第一机械手1410驱动第一抓取头1411运输工件。当然,也可以是采用一个粗抛孔装置1600和一个精抛孔装置1700对工件上所有的通孔进行抛光的形式。
47.在一较佳实施例中,如图12和图13所示,优选粗抛孔装置1600包括设置在第一机架1100上的第一载具1610和粗抛模组1620,第一载具1610上设有用于放置工件的第三放置位1614,粗抛模组1620位于第三放置位1614的正上方;精抛孔装置1700包括设置在第一机架1100上的第二载具和精抛模组,第二载具上设有用于放置工件的第四放置位,精抛模组位于第四放置位的正上方。其中,粗抛孔装置1600和精抛孔装置1700的结构一致,现以粗抛装置进行具体说明,第一载具1610包括设置在第一机架1100上的第一安装座1611、转动设置在第一安装座1611顶部的第一转盘1612以及驱动第一转盘1612移动的第一驱动机构1613,第三放置位1614位于第一转盘1612的顶部。此时,第三放置位1614的形式可以是设置在第一转盘1612上的两个定位柱,而上述治具4000的底部设有与之对应的定位孔,通过将定位柱插装在定位孔内以实现治具4000的固定。优选粗抛模组1620包括第八驱动机构1621和粗抛头1622,第八驱动机构1621优选采用直线模组的形式,以便于驱动粗抛头1622沿竖直方向移动,以便于将粗抛头1622插装在工件上的待抛光的通孔内,然后利用粗抛头1622
的自转实现对通孔的抛光,粗抛头1622采用毛刷棒,而精抛模组则采用磨皮棒。本实施例中,第一驱动机构1613用于驱动治具4000以工件上进行抛光的通孔的轴向方向为旋转进行旋转,从而便于粗抛模组1620对该通孔进行抛光时通过工件自转来提升抛光效率。
48.此时,第一中转平台1300也可参照第一载具1610进行设置,以便于带动治具4000转换方向(如转换90
°
)后供第二转运装置抓取治具4000。
49.在一较佳实施例中,如图4和图14所示,优选定位装置2300包括第一底板2310、第一挡板2320、驱动至少一个第一挡板2320移动的第三驱动机构2330和驱动第一底板2310移动的第四驱动机构2340,多个第一挡板2320围设在第一底板2310的周侧以构成收纳工件的定位腔,第三驱动机构2330驱动至少一个第一挡板2320朝向或远离定位腔移动,第四驱动机构2340驱动第一底板2310在第三转运装置2400的下料点与第四转运装置3200的上料点之间往复移动。
50.其中,优选第一底板2310为矩形,第一挡板2320的数量至少为四个并分别位于第一底板2310的四个侧面,以便于围合构成与工件相适配的定位腔。此时,优选第三驱动机构2330为两个,均采用直线气缸,以驱动相邻两个第一挡板2320移动,优选其中一个第三驱动机构2330设置在第一底板2310上,而另一个第三驱动机构2330设置在第二机架2100上且位于第三转运装置2400的下料处,从而便于第四驱动机构2340驱动位于定位腔内的工件移动至第四转运装置3200的上料点时,有利于第四转运装置3200从定位腔一侧面伸入内部并抓取定位腔内的全部工件,第四驱动机构2340优选采用直线模组的形式,以便于驱动定位腔内的工件移动至第四转运装置3200的上料点。本实施例中,通过第三转运装置2400将工件放置在定位腔内,然后利用两个第三驱动机构2330分别驱动两个相邻的围板朝向定位腔移动,从而便于调整定位腔内的工件的位置,以此实现了工件的定位。
51.在一较佳实施例中,如图4和图15所示,优选中转设备2000还包括设置在第二机架2100上并用于放置工件的第三中转平台2500,第三中转平台2500包括第二底板2510、第二挡板2520和第五驱动机构2530,第二挡板2520围设在第二底板2510的周侧以构成存储腔,第五驱动机构2530驱动底板沿竖直方向移动,第三转运装置2400用于将第二转运平台上的工件抓取至存储腔内以及用于将存储腔内的工件抓取至定位装置2300上。其中,优选第二底板2510为矩形板,第二挡板2520为四个l形条,且四个l形条分别布置在第二底板2510的四个边角处,以此围合构成与工件(即手机后盖板4200)相适配的存储腔,第五驱动机构2530用于驱动第二底板2510沿竖直方向运动,以便于第三转运装置2400将工件放置在存储腔内或将存储腔内的工件放置在上述定位腔内。此时,如图16所示,优选第三转运装置2400上具有两个独立工作的第三抓取头2410,从而便于利用其中一个第三抓取头2410将第二中转平台2200上的治具4000内的隔板放置在下述第七放置位3411上以及利用另一个第三抓取头2410将第二中转平台2200上的治具4000内的工件放置在存储腔内或将存储腔内的工件放置在定位腔内,优选两个第三抓取头2410均采用真空吸附的方式抓取隔板和工件。当然,其中抓取工件的第三抓取头2410也可以是直接将工件从治具4000抓取至定位腔内。
52.同时,如图10所示,优选第二中转平台2200包括第三载物板2220和驱动第三载物板2220移动的第九驱动机构2230。其中,上述第二放置位2221位于第三载物板2220上,且第三载物板2220上还设有第六放置位2222,第六放置位2222用于放置隔板,以便于第六放置位2222上的隔板存储至一定数量后利用第二转运装置1500中的一个第二抓取头1510抓取
至回流线体1110上,至于第九驱动机构2230优选采用直线模组,以便于驱动第三载物板2220在第二转运装置1500的下料点以及第三转运装置2400的上料点之间往复移动。具体的,优选第二转运装置1500将治具4000放置在二放置位上后,第九驱动机构2230驱动第三载物板2220移动至第三转运装置2400的上料点处,从而便于两个第三抓取头2410交替抓取隔板和工件。
53.在一较佳实施例中,如图5所示,优选周抛装置3300为三个,三个周抛装置3300沿直线依次布置,周抛设备3000还包括设置在第三机架3100上的下料平台3400,第四转运装置3200还用于将周抛装置3300上完成加工的工件放置在下料平台3400上。其中,如图17所示,周抛装置3300包括:
54.转座3310,转座3310转动设置在第三机架3100上;
55.第十驱动机构3320,第十驱动机构3320设置在第三机架3100上并与转座3310连接;
56.压头3330,压头3330位于转座3310的正上方并可朝向或背离转座3310移动;
57.第十一驱动机构,第十一驱动机构设置在第三机架3100上并与压头3330转动连接;
58.两个抛光筒3340,两个抛光筒3340相对设置在转座3310的周向上;
59.第十二驱动机构3350,第十二驱动机构3350的输出端与两个抛光筒3340连接。
60.其中,转座3310用于放置工件,此时优选转座3310上设有避位缺口,以便于第四转运装置3200将手机后盖板4200放置在转座3310上,第十驱动机构3320优选采用电机+减速器的形式,以驱动转座3310转动。第十一驱动机构优选采用直线气缸,以驱动压头3330朝向转座3310移动,从而与转座3310配合以对转座3310上的手机后盖板4200形成夹持,且压头3330与直线气缸的输出端转动连接,从而便于压头3330跟随转座3310转动。两个抛光筒3340分别为地毯筒和猪毛筒,以便于利用抛光筒3340的自转对手机后盖板4200的侧面进行抛光。此时,第十二驱动机构3350包括两个第一驱动组件、两个第二驱动组件和一个第三驱动组件,两个第一驱动组件优选采用电机+减速器的形式,以分别驱动两个抛光筒3340自转,两个第二驱动组件优选采用电机+丝杠的形式,以便于分别驱动两个抛光筒3340相对或相背移动,第三驱动组件优选采用电机+凸轮结构的形式,以便于驱动两个抛光筒3340整体上下往复移动,从而有利于增加抛光效率。
61.同时,如图18所示,下料平台3400优选包括用于放置工件的第四载物板3410和驱动第四载物板3410移动的第十三驱动机构3420,从而便于利用第十三驱动机构3420驱动第四载物板3410在工件下料点(可以人工下料或通过机械手自动下料)与第四转运装置3200的下料点之间往复移动,以便于第四转运装置3200将周抛装置3300上完成周抛工序的工件抓取至下料平台3400上后供人工或机械手下料。此时,优选第四载物板3410上设有用于放置工件的第七放置位3411,具体第七放置位3411可为腔体的形式,从而便于避免出现第四载物板3410移动的过程中工件移出的情况。
62.进一步,如图19所示,优选第四转运装置3200上具有至少一个第四抓取头3210,第四抓取头3210优选采用沿竖直方向夹持的方式夹持工件,从而便于将定位装置2300上若干叠层布置的一次性抓取至周抛装置3300上以及将周抛装置3300上完成周抛的工件的一次性抓取至上述下料平台3400上。具体的,如第四抓取头3210为两个,其中一个第四抓取头
3210用于将定位装置2300上的工件抓取至周抛装置3300上进行周抛工序,而另一个第四抓取头3210则用于将周抛装置3300上完成周抛的工件抓取至下料平台3400上。
63.在一较佳实施例中,优选第一机架1100上设有第二收集盒以及第三机架3100上设有第三收集盒,上述第一载具1610和第二载具均位于第二收集盒内,转座3310位于第三收集盒内,从而便于收集抛光液。当然,为了防止抛光液飞溅,还可在第一机架1100上设置第一密封罩、在第二机架2100上设置第二密封罩以及在第三机架3100上设置第三密封罩。
64.以上的仅为本实用新型的部分或优选实施例,无论是文字还是附图都不能因此限制本实用新型保护的范围,凡是在与本实用新型一个整体的构思下,利用本实用新型说明书及附图内容所作的等效结构变换,或直接/间接运用在其他相关的技术领域均包括在本实用新型保护的范围内。