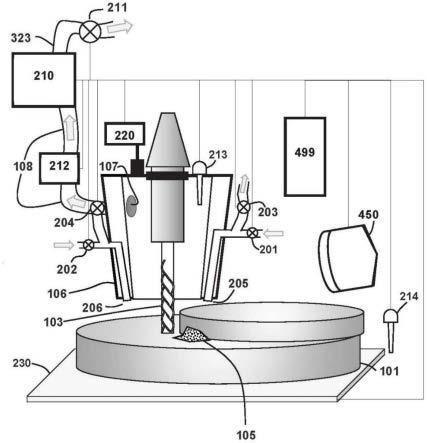
混合增材和减材制造过程中的废物收集和减排
相关申请的交叉引用
1.本技术要求2016年9月15日提交的美国专利申请us16/102,422、2019年5月20日提交的美国专利申请16/417,279和2018年9月18日提交的美国专利申请16/134,343、2016年5月13日提交的美国临时申请62/335,679、2016年9月15日提交的美国临时申请62/395,289、2016年10月12日提交的美国临时申请62/407,318和2016年11月14日提交的美国临时申请62/421,707的权益,其全部公开内容通过引用并入本文。
技术领域
2.本发明涉及用于制造由金属和其他材料制成的复杂部件的混合增材和减材制造领域。
背景技术:3.增材制造和减材制造的混合组合提供了显著的优势,同时减轻了任一技术的负面影响。例如,增材制造允许从部件设计的内部开始构建部件,这从减材技术如机械加工的外部角度来看是无法实现的。这允许新的整体部件几何形状具有内部冷却通道和中空腹板芯等特征。然而,增材制造的部件通常只能具有接近最终形状的形状,并且表现出一定程度的不希望的粗糙度,因为部件是以不连续的层构建的,这些层本质上不能粘附到的最终形状或者产生在减材制造中可能得到的期望的最终表面。在美国专利10,087,332b2中,connor等人教导减材步骤,例如在整个增材工艺中在可烧结金属糊增材步骤之间进行加工,以实现最终的净形状。由于一旦部件完成后,某些表面可能无法通过适当的减材工艺到达,因此在部件完成之前在一些增材步骤之间执行减材步骤是有利的。然而,混合制造中的减材步骤会产生废料或切屑,其形式包括碎屑、锉屑、车屑、刨花和各种细颗粒物质,如灰尘、烟雾、蒸汽和冷凝物。除了干扰加工机器并造成潜在的环境和人类健康危害外,这些切屑或废料还可能重新沉积在部件上。在增材步骤之前,不得允许颗粒材料堆积在部件上,因为它可能会改变完成部件的密度;干扰下一层的粘附;并且使得难以去除被困在需要后处理去除的已完成部件中的大量切屑。颗粒物质可能从构建区域迁移到制造设备的其他部分;此外,细颗粒物质可能会自燃或对人和环境有毒。因此,需要去除和减少减材步骤中产生的废物。
4.因此,需要在混合增材和减材制造过程中减少不需要的废料的方法和组件。
技术实现要素:5.下文给出了简化概述,以提供对本发明一个或多个实施例的一些方面的基本理解。该概述不是广泛的概述,也不是旨在标识本教导的关键或关键要素,也不是描绘本发明的范围。相反,其主要目的仅仅是以简化形式呈现一个或多个概念,作为稍后呈现的详细描述的前序。
6.公开了一种用于在混合减材和增材制造过程中控制废料的组件。用于在混合减材和增材制造过程中控制废料的组件还包括保持在支架中的加工工具或成形为也用作支架
并装配到工具致动器的加工工具。用于在混合减材和增材制造过程中控制废料的组件还包括护罩,该护罩设置在加工工具或成形为还用作支架和加工工具的一部分的加工工具的周围。用于在混合减材和增材制造过程中控制废料的组件还包括一个或多个端口,该端口被配置为在护罩内产生负压。
7.实施例可包括一个或多个以下特征。用于在混合减材和增材制造过程中控制废料的组件可包括其中一个或多个端口通过一个或多个节流阀和控制抽空速率的控制器连接到加压空气源。该组件可以包括连接到控制器的相机,以检测切屑的堆积。基于相机对切屑堆积的检测,控制器被配置成通过一个或多个端口中的选定端口调节加压空气的流量。该组件可以包括收集器,该收集器通过导管连接到一个或多个端口,并且被配置为收集、分类和释放切屑。收集器可以包括磁性质量检测室。收集器可以包括过滤切屑收集室。收集器可以包括重力切屑收集室。该组件可以包括具有一个或多个传感器的颗粒检测室,该传感器被配置为实时检测切屑的浓度、尺寸、形状和/或浓度。一个或多个传感器连接到控制器,并且控制器可配置为调节端口中的一个或多个节流阀。护罩可以包括一个或多个端口。支架可以包括一个或多个端口。护罩、工具和支架被配置为保持被增材制造的零件,可以包括可更换组件部件。该组件可以包括设置在护罩的一部分和加工工具支架的一部分之间的密封件。
8.还公开了一种用于在混合减材和增材制造期间控制废料的组件。用于控制废料的组件还包括保持在支架中的加工工具或成形为还用作支架并装配到工具致动器的加工工具。用于控制废料的组件还包括设置在加工工具或加工工具周围的护罩,该护罩的形状还用作支架和加工工具的一部分。用于控制废料的组件还包括通过一个或多个节流阀连接到加压空气源的一个或多个端口,所述节流阀被配置为在护罩内产生负压。用于控制废料的组件还包括控制器,该控制器控制护罩内的抽空速率并且配置为通过一个或多个端口中的选定端口调节加压空气流量。用于控制废料的组件还包括连接到控制器以检测切屑堆积的相机。
9.还公开了一种在部件的混合减材和增材制造过程中限制废料的方法。限制废料的方法还包括将一定量的材料添加到正在增材制造的部件中。该方法还可以包括改变添加的材料的量。该方法可以包括操纵工具来加工正在增材制造的部件的一部分并产生废料/切屑。该方法可以包括密封工具的一部分并用护罩覆盖正被增材制造的部件的一部分。该方法可包括通过护罩中的端口施加负压以产生气流以防止切屑离开护罩。
10.在混合减材和增材制造过程中限制废料的方法可以包括通过相机检测切屑的堆积。气流的调节可以基于相机检测到的切屑的堆积。该方法可以包括在收集器内确定切屑的浓度、尺寸、形状和/或浓度。收集器可以包括磁性质量检测室、重力切屑收集室、过滤收集室或它们的组合。限制废料的方法可包括通过可包括传感器的检测系统实时监测收集的切屑的速率、数量和/或类型。切屑生成模型可以基于计算和/或测量的添加到部件和/或从部件中减去的材料量。限制废料的方法可以包括使用基于预期切屑产生率、切屑产生模型、护罩的机械布置或其组合计算的一组所需空气流速来确定操作裕度。限制废料的方法可以包括基于对操作裕度之外的切屑的检测来调整气流和切屑生成模型。该方法可包括基于检测到切屑超出操作裕度而发出警报。限制废料的方法中的空气流向部件。一个或多个喷嘴、一个或多个导管或一个或多个端口可以位于护罩中。
附图简要说明
11.包含在本说明书中并构成本说明书一部分的附图示出了本发明的实施例,并且与说明书一起用于解释本发明的原理。在附图中:
12.图1示出了正在进行切屑收集的减材加工步骤的部件。
13.图2(a)示出了用于切屑提取和收集的护罩的侧视图,该护罩配有控制和减排装置。图2(b)中所示的通气口围绕护罩的周边布置。
14.图3示出了切屑收集和减排系统。
15.图4示出了切屑检测系统。
16.图5示出了在混合增材和减材制造的操作步骤期间用于控制切屑收集和去除的过程。
17.图6(a)和(b)示出了切屑提取和收集的侧视图,其中压缩空气通过各种压缩空气导管输送至凹部特征。
18.图7示出了通过两个端口从一个部件上去除切屑,该两个端口可围绕一个被工具操纵的部件定向。
19.图8示出了用于包含在混合增材和减材制造工艺的操作步骤中产生的切屑的层流。
20.应注意的是,图中的一些细节已经简化,绘制这些细节是为了便于理解本发明,而不是为了保持严格的结构精度、细节和比例。
具体实施方式
21.现将对本发明的当前实施例(示例性实施例)进行详细说明,其示例如附图所示。在可能的情况下,将在整个附图中使用相同的附图标记来指代相同或相似的部分。在下面的描述中,参考了构成其一部分的附图,并且在附图中以图示的方式示出了可以实施本发明的具体示例性实施例。这些实施例被充分详细地描述以使本领域技术人员能够实现本发明,并且应当理解,可以利用其他实施例,并且在不脱离本发明范围的情况下进行改变。因此,以下描述仅是示例性的。
22.虽然本发明已经针对一种或多种实施方式进行了说明,但是在不背离所附权利要求的精神和范围的情况下,可以对所说明的示例进行改变和/或修改。此外,虽然本发明的特定特征可能仅针对几个实施方式中的一个进行了公开,但是这种特征可以与其他实施方式的一个或多个其他特征相结合,这对于任何给定的或特定的功能来说可能是期望的和有利的。此外,就在详细描述和权利要求中使用的术语“包括”、“包括”、“具有”、“具有”、“具有”或其变体而言,这些术语旨在包含在一种类似于术语“包括”的方式。术语“至少一个”用于表示可以选择所列项目中的一个或多个。
23.尽管阐述本发明宽泛范围的数值范围和参数是近似值,但在具体实施例中阐述的数值尽可能精确地报告。然而,任何数值都固有地包含某些误差,这些误差必然是由于在它们各自的测试测量中发现的标准偏差而导致的。此外,本文公开的所有范围应理解为涵盖其中包含的任何和所有子范围。例如,“小于10”的范围可以包括(并包含)最小值0和最大值10之间的任何和所有子范围,即,具有最小值等于或大于0的最大值等于或小于10的任何和所有子范围,例如1至5。在某些情况下,所述参数的数值可能取负值。在这种情况下,表示为“小于10”的范围示例值可以采用负值,例如1、-2、-3、-10、-20、-30等。
24.在图1所示的一个实施例中,在混合增材和减材工艺中,通过机械加工对部件进行减材步骤。通过分配可烧结的金属膏添加到部件的底部101,通过干燥挥发性溶剂将其转化为致密的粘结生坯,并通过机械加工将其加工成最终形状。尽管这里描述了可烧结的金属膏,但是增材步骤可以指任何增材步骤,包括但不限于挤出、分配、沉积、印刷、喷射和放置。同样,添加的材料可以包括但不限于金属、金属合金、氧化物、硫化物、氮化物、磷化物、聚合物和各种陶瓷。该部件的顶部102已经通过分配金属膏来添加,并且通过干燥来转变,尽管干燥可以由适合于增材步骤和添加材料的转变步骤来代替,包括但不限于移除、干燥、蒸发、升华、固化、反应、氧化、涂覆、烘烤、扩散、植入、冷冻和聚合。加工工具103由主轴通过加工工具支架104驱动,以便通过加工顶部102进行操作。操作可以是适合于材料的任何操作步骤、增材步骤和转变步骤,包括但不限于铣削、切割、研磨、砂磨、抛光、磨光、蚀刻和烧蚀。在干燥的金属膏的情况下,顶部将倾向于变脆,并且切屑(也可称为废料)将典型地呈细小的金属颗粒和小颗粒簇的形式,部分倾向于变得容易悬浮在工作区域附近的空气云中,并最终在该区域附近部件的底部部分101和顶部部分102的表面上广泛和部分地沉降,如沉降簇105所示。注意,广泛沉降的颗粒和颗粒簇都不是所希望的,并且可以被有利地去除。在目前描述的实施例中,护罩106在除了邻近和靠近部件的顶部102之外的所有侧面上围绕工具103的上部和支架104的下部,从而将所有经过主轴的气流限制在护罩底部的小区域内。通过导管108在端口107处施加相对真空负压,将在护罩106内部产生负压,这继而在部件附近和周围产生气流109和110,从而随着切屑被夹带在气流中而去除切屑。因此,护罩106用于便于收集和去除在操作过程中产生的切屑。护罩106由工具支架104周围的运动密封件111密封,从而允许工具支架的旋转运动和可选的线性运动,但是不允许空气流过密封件。重要的是,密封件111不应允许切屑流出护罩并流向机器的其他部件,例如主轴。在一个实施例中,护罩106和密封件111都可以大致分成两部分打开,以允许自动工具更换,然后能够再次密封地关闭。可选地,主轴可以从护罩中升起,或者护罩可以下降以自动工具更换,并且本领域技术人员将会理解,通过护罩更换工具的其他方式也包括在本发明的范围内。在某些实施例中,加工工具103可以被保持在支架104中,或者可以包括成形为还用作支架并且装配到工具致动器的加工工具。
25.值得注意的是,如图1所示,由于正在制造的部件的可变性质,护罩106和流110穿过的部件之间的间隙小于护罩和流109穿过的部件之间的间隙,这将导致流109的较低速度和较高体积以及流110的较高速度和较低体积。这种差异将在部件边缘或悬垂部分112附近最为突出,其中大致圆柱形护罩的开口的大约一半将不与部件相邻。因此,相对于经由端口107和导管108的总流量、工具103的尺寸以及工具103超出图1中距离e给出的护罩开口的延伸,将图1中所示的护罩106的圆形开口的尺寸适当地设定为直径d是有利的。d与e之比,即d/e,当其为约0.025至约4.0时有利于捕获颗粒,而当其为约0.75至约2.0时是最佳的。在护罩开口的形状明显不同于圆形的情况下的有利和最佳范围将会不同,这对于本领域技术人员来说是显而易见的。
26.在另一个实施例中,护罩106、工具103、密封件111和支架104形成可更换组件,所有构件和尺寸均经过选择,以优化由为该组件选择的特定工具产生的切屑的类型、数量和速度的收集。以这种方式,切屑收集可以总是在最佳条件下运行,而不会受到损害。在图2所
示的一个实施例中,护罩106配备有一个或多个端口205、206、207和208,它们通过节流阀连接到加压空气源,其中两个在图2(a)中显示为201和202,或通过一个或多个分流器连通节流阀201和202排出真空和导管108,其中两个在图2(a)中显示为203和204,并由控制器499连接和控制。通过导管108的排空速度由排气节流阀211控制。如图2(b)所示,端口可以围绕护罩106中的开口的周边布置,并且可选地,基本上指向操作区域,在所展示的加工情况下,工具103正在产生切屑。连接到控制器499的相机系统450用于发现或检测潜在的切屑堆积。然后,可以调节或脉动通过为最有利地接近工作区域而选择的端口的流动,以便从潜在的故障点释放切屑,这些故障点可能倾向于捕获切屑,例如沉淀的簇105。基于相机对切屑堆积的这一检测,控制器可以调节通过一个或多个端口的加压空气的流动。可选地,一些端口可以经由节流阀和分流器被配置为排气,一些端口被配置为加压空气,以便产生横穿工作表面和工具103的横向的横流,该工具103产生切屑。在一个实施例中,致动器220连接到护罩106和端口组件并促动其运动,从而改变相对于护罩直径d的延伸e。最后,本领域技术人员将理解,许多阀、端口、导管和分流器的其他配置以实现有利于切屑去除的流动模式在本发明的范围内是显而易见的。
27.图3描绘了收集器210。在一个实施例中,收集器210包括磁性质量检测室310。来自导管108夹带切屑的气流进入磁性质量检测室310,其中定位有磁性收集器311。磁性收集器311包括磁体的单个北极或单个南极、单个磁体的北极和南极、或多极磁阵列的多个磁极。一个或多个磁体可以包括永磁体、电磁体或电永磁体。电磁体和电永磁体都可以有利地增加强度、降低强度、设置为零强度或反转极性,从而允许根据切屑颗粒的质量、形状和磁性以及通过磁性质量检测室310的流速来收集、分类和释放磁性切屑。正在制造的部件的类型、所采用的减材工艺的操作方法和速率以及增材步骤中使用的原料和转化步骤中使用的工艺将影响切屑颗粒的质量、形状和磁性。一些切屑颗粒312因此可以直接穿过磁性质量检测室310,并且一些切屑颗粒313将粘附到磁性收集器311上。如图所示,磁性收集器311在磁性质量检测室310外部或内部连接到天平314,磁性质量检测室310又通过可选的集线器399连接到控制器499。有利地,为了控制,来自天平314的多个测量值可以被组合以确定瞬时平均磁性质量捕获率为其中m
t1
和m
t2
是在随后的时间t1和t2测量的质量。
28.在另一个实施例中,收集器210包括重力切屑收集室320。来自导管108或磁性质量检测室310的夹带切屑的流进入切屑收集室320,其中,它被分流器321分流到灰尘收集室320内壁周围的气旋模式322中,并缓慢上升通过室的中部,在施加真空的端口323处离开。流动模式既减慢了速度又增加了流动的路径长度,从而增加了切屑颗粒在重力影响下落下并在重力切屑收集室的底部324收集并保持被捕获的机会。天平325测量收集的切屑324的质量或质量的增加,并将测量结果通过集线器399发送到控制器499,或直接发送到控制器499。有利地,为了控制,来自天平325的多个测量值可以被组合以确定瞬时平均重力捕获率为其中m
t1
和m
t2
是在随后的时间t1和t2测量的质量。
29.在另一个实施例中,收集器210包括过滤收集室330。来自导管108、来自磁性质量检测室310、来自重力切屑收集室或来自旁路315的夹带切屑的流进入切屑过滤收集室330,在此被细颗粒过滤器收集,例如多种高效微粒空气(hepa)过滤器中的一种或多种。天平331
测量收集在室330中的切屑的质量或质量增加,并将测量结果通过集线器399发送到控制器499,或直接发送到控制器499。有利地,为了控制,来自天平325的多个测量值被组合以确定瞬时平均过滤捕获速率为其中m
t1
和m
t2
是在随后的时间t1和t2测量的质量。旁路315由控制器499通过集线器399控制,或直接由控制器499控制,当需要低延迟或非常准确的切屑生成监控时,允许偶尔单独使用过滤收集室。这种低延迟监控可替代地称为实时的监控或实时监控。否则,收集系统210通常包括通过重力切屑收集室320的通道。
30.在一个实施例中,重力切屑收集室320可集成一个过滤器,由此有利地,通过过滤收集和重力收集收集的所有切屑可仅在天平325上称重,无论其是否已沉降在过滤器上或室底部。还应注意的是,一旦新引入的切屑进入所述组合的过滤器和重力收集系统腔室320,就没有延迟记录新引入的切屑的质量,因为所有切屑和夹带空气的质量减去被切屑置换的空气将在天平325上测量。
31.在图4所示的实施例中,通过端口107和一个或多个空气端口205、206、207和208从护罩106排入导管108的切屑被导入检测系统212,检测系统212具有近实时监控收集的切屑数量和类型以及切屑收集速率的能力。将检测系统212定位在导管108内并紧接在所述端口之后的优点是确保所有排出的切屑在流入检测系统212时都被计算在内。
32.在检测系统212的一个实施例中,夹带在流过导管108中的切屑进入感应颗粒检测室402,该感应颗粒检测室402装配有受保护的探针感应颗粒传感器403,例如可从密歇根市的dwyer,inc.获得的pms颗粒传感器。该传感器的工作原理是,在受保护的探头附近运动的颗粒通过电磁感应驱动微小的电流,从而产生可测量的电压。该感应电压可以针对其他质量的直接测量值进行校准。传感器可以由制造商预先校准,或者可以根据通过收集器210获得的质量测量值进行校准,或者可以通过从样品中研磨已知质量的材料来校准,并且对于具有足够技术的人员来说显而易见的是其他校准方法也是可能的。传感器403由控制器499控制,并且传感器信息经由集线器398传递到控制器499,或者直接由控制器499控制并传递到控制器499。此外,由于感应传感器以单调增加的方式响应增加的颗粒量,因此可以回避校准并简化控制过程,由此增加流速直到流速的进一步增加不会导致增加的颗粒检测。
33.在检测系统212的一个实施例中,气流夹带的切屑进入光学检测系统,该光学检测系统包括安装有窗口411的光学检测室410,该窗口允许检测光通过。尽管在该实施例中检测器位于窗口后面,但是在替代实施例中,检测器可以位于室壁内或室内。光源412引导光通过检测室410中的所述窗口,其中光可以与切屑颗粒405相互作用。一些被引导的光可以穿过检测室410,而基本上不会由于与切屑的相互作用而转向,并通过室410中的另一个窗口411离开。随着通过导管108夹带的切屑的浓度、尺寸、形状和成分的变化,来自光源412的或多或少的光将到达被切屑散射或吸收的光源光检测器413。因此,光检测器413通过其经由可选集线器控制器399或直接连接到控制器499,与控制器499的连接提供了一种确定由切屑引起的光衰减的方法。来自光源412的被散射而不是被切屑吸收衰减的一些光可以被位于窗口411后面的反向散射检测器414检测到。在基本向后的方向上如此散射的光有时被称为后向散射,而仅略微偏离的散射光有时被称为前向散射。由位于窗口411后面的前向散射检测器415检测的光。检测器414和415通过可选的集线器399连接到控制器499,或直接连接到控制器499,从而提供由流经导管108的流中夹带的切屑405散射的光的测量值。来自检
测器413、414和415的信号流被组合以确定颗粒计数、颗粒流速、颗粒尺寸分布和颗粒成分。光学检测系统可以相对于通过收集器210获得的质量测量值进行校准,或者可以通过从样品中研磨已知质量的材料来进行校准,并且对于本领域技术人员来说显而易见的是,其他校准方法也是可能的。如同在受保护的探针感应式颗粒传感器403的情况下,有可能回避校准并简化具有光学检测系统的控制过程,由此流速增加,直到流速的进一步增加不会导致增加的颗粒检测。
34.在一个实施例中,传感器213和214位于护罩106内和工作区域外,并分别将信号a和b收集到控制器499。传感器213和214可以是受保护的探头感应式颗粒传感器,例如在先前实施例中描述的光学检测系统403;或其他测量颗粒浓度的传感器。增加流量以增加切屑收集能力,从而增加收集的切屑量。信号a和b可以被单独地、联合地或者比率被认为是超级信号。当收集的切屑到达接近所有切屑产生的点时,信号a、a/b和b将分别增加、增加和减少,直到饱和点,在该饱和点,收集功率的进一步增加,例如流量,不会分别产生信号a、a/b和b的进一步增加、增加和减少,在此之后,流量可以被设置持续一段时间,或者收集速率可以被抖动以确定所述信号流动的变化速率,或者通过对相关领域的技术人员来说显而易见的几种其他设置和控制方法。
35.所述一个或多个节流阀201、202等,分流器203和204等,以及排气节流阀211的控制和校准可通过驻留在控制器499上并在控制器499上执行的数字软件计算机算法进行,所述控制器包括计算机系统。备选地,数字软件算法可以驻留在远程计算机系统上并在远程计算机系统上执行,该远程计算机系统是网络的一部分,控制器499与所述远程计算机系统通信,并且可以由所述远程计算机系统控制。控制器可以根据在控制器499上的计算机数控下运行的构建程序自动调节节流阀。在一个实施例中,可以通过调节节流阀201、202等,分流器203和204等调节通过在护罩开口和部件之间的大或小间隙附近操作的空气端口的流量,且排气节流阀211根据优化切屑去除和收集到护罩中所需的预期和所需气流的模型来向上或向下调节。
36.一个实施例包括如下图5所示的控制方案;一旦机器指令准备好用于混合过程中的操作步骤,就开始采集监控数据,包括流速、捕获率、颗粒检测、相机图像和部件质量损失。然后是正在构建的部件的切屑生成模型,其中包含增材步骤,例如分配,转换步骤,例如干燥,和操作步骤,例如机加工,用于计算一组预期的切屑生成率。切屑生成模型可以包括计算和测量的材料的数量或质量,例如通过分配添加的、例如通过干燥溶剂转化的、以及例如通过机械加工处理的。可以通过多种方法进行计算,例如计算层或部件的某一部分的增加的体积或质量,在转变过程中预期的质量变化,例如从增加的体积中除去的溶剂量,以及在操作过程中除去的转变材料的质量,以获得所述部件或部件的一部分的最终形式。测量可以通过多种方法进行,例如测量在增材过程中分配的材料的质量,例如测量在转化过程中去除的溶剂的量,以及例如测量在制造所述部分或部件的一部分过程中去除的材料的质量。为了测量在增材过程中获得的、在转变过程中损失或获得的以及在操作过程中损失或获得的材料的质量,被制造的部件101位于天平230上,天平230连接到控制器499,如图2所示。从所述切屑产生模型和护罩106、端口205、206、207、208和其它部件、收集器210和包括107、108的排气系统、排气节流阀211、节流阀201、202和其它部件以及分流器203、204和其它部件的特定机械布置的性能模型计算一组所需的流速。确定一个操作裕度,在该裕度内,
所需的空气流速被认为适合通过过程参数调整进行操作。操作步骤,例如开始加工过程,并将监控数据与预期的切屑产生量和设计偏差进行比较。如果检测到的切屑比预期的少,或者如果相机发现部件上的切屑堆积,则需要增加工艺流程并适当调整模型。如果可能并且认为有必要,相机系统450发现的切屑可以指示中断正常的部件加工以进行移除。如果检测到的切屑比预期的多,但在操作裕度内,则处理继续进行,而不调整工艺流程或模型,如果检测到的切屑超过预期量加上操作裕度,则流量可能过高,需要减少,并适当调整模型。此外,非常过量的切屑流可能指示显著的和意外的加工偏移,并且可以发出警报或者可以停止加工,否则加工继续进行,直到操作(例如加工)步骤指令完成。在若干实施例中,流量和模型的调整可以在预定时间连续、准连续、间歇地发生,例如在预定时间,每隔几秒钟,在预定的时间点,例如在增材、转变和操作的层或循环之间、部件到部件(例如在多件式部件制造期间)或包括上述方式的任何组合之间。
37.在一个实施例中,如图6(a)所示,工具103进入凹陷特征600(如盲沟或盲孔)进行铣削,以精加工进行混合增材和减材制造的部件顶部102的粗糙边缘601。这一动作可能产生切屑簇602,从而沉积在先前抛光的表面603上,并且由于凹陷特征600中缺乏空气循环而被截留。在该实施例中,工具103有利地配备有内部空气导管604和605,通过支架104中的密封件606的旋转馈通向内部空气导管604和605供给加压空气。当工具铣削时,加压空气在凹陷特征内流出工具,从而产生湍流气流,该湍流气流将切屑从凹陷特征提起并迫使切屑朝向护罩106的开口。由通过导管108经由端口107施加的负相对压力引起的所述护罩内的负压产生收集作用。凹部内的空气流结合所述收集动作有利地去除和防止切屑簇602的形成。
38.在另一个实施例中,如图6(b)所示,位于护罩106内的喷嘴610通过阀门611的节流供应压缩空气,并基本对准由工具103进行铣削的表面601所代表的工作区域。以与图6(a)所示的先前实施例类似的方式,空气在凹部特征600内流动,结合护罩106的收集作用,防止了切屑簇602靠着精加工表面603形成。对于本主题的具有足够技术的人员来说,显而易见的是,该实施例存在许多其他可能的配置。例如,在某些实施例中,可以在一个或多个加工步骤之后完成残留物去除。此外,替代实施例可包括本文前述实施例中描述的构造的任何组合的喷嘴。一个或多个相机可以检测是否所有的残留物都已经被去除,从而确定残留物的去除是继续还是停止。
39.在相关实施例中,在铣削步骤之后,分配下一层可烧结膏状物之前,通过端口205/206/207/208、导管604/605或喷嘴610输送的压缩空气,去除凹陷特征600中残留的切屑簇602。除了在铣削步骤中去除切屑之外,还可以进行该切屑去除步骤。可以通过在部件的整个表面上或仅在部件的基于切屑生成模型预期形成切屑簇602的区域中对护罩106进行光栅化(rastering)来执行切屑去除步骤。切屑去除步骤可以响应于由连接到控制器499的相机系统450发现的切屑簇602来执行。
40.在图7所示的实施例中,放置在构建板701上的部件102正在经历混合增材和减材制造工艺中的操纵步骤。工具103正在产生切屑,对于部件和工具的各种特定几何形状,这可能导致切屑105的聚集簇和喷出的切屑706的射流。端口705被定位成使得射流706基本流入端口705,并且端口705通向导管703,导管703通向图2的导管108,导管108分别被图3和图4的收集器210和检测系统212所包括,用于切屑收集、检测和消除的目的。通过与端口705和管道703相对的管道702从端口704供应空气,其中工具103和部件102基本上位于端口704和
705之间的线上,使得气流扫过工具103所产生并排出部件102的切屑。在一个实施例中,端口704和705可以围绕工具103的轴线707定向和旋转,这有利地允许独立于部件102的几何形状或工具103相对于部件102的定向而拦截射流706,并且还允许在某些切屑簇105可能聚集的地方优化气流。除了关于工具轴线707的定向之外,端口704和705可以在工具轴线707的方向上“向上”或“向下”平移。或者,端口704和705可以是固定的,并且构建板701可以在垂直于工具轴线707的平面内旋转和平移,并且在工具轴线707的方向上平移。在另一个替代实施例中,端口704和705以及构建板701都可以允许一些或任何上述类型的运动,以便进一步允许灵活性并优化穿过部件102的气流以促进切屑的去除。
41.在图8中描绘的实施例中,制造腔室800容纳制造系统801,该制造系统801包括排气导管108和在混合增材和减材制造的操作步骤期间产生切屑的工具103。随着空气和切屑通过导管108排出,在制造室800内建立负压或相对真空。腔室800基本上是密封的,因此负压防止切屑逸出,但是补充空气可以通过入口挡板802被吸入,该入口挡板802在腔室内具有一系列孔口,使得沿腔室的内壁建立层流800。以这种方式,有利地防止切屑逃逸到环境中,并且可以通过检测系统212和收集系统210检测、测量、收集和减少所有切屑。
42.本领域普通技术人员应清楚,除了优选实施例之外,许多其他扩展和配置也是可能的,此处这些优选实施例的示例并不排除本公开内容中的其他实施例。