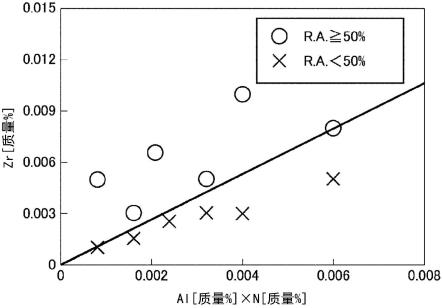
1.本发明尤其涉及大量含有al的钢的板坯及其连续铸造方法。
2.本技术基于2020年4月7日提出的日本专利申请特愿2020-069306号而主张优先权,在此引用其内容。
背景技术:3.近年来,作为薄板用高强度钢铁材料,正在大规模制造为了提高机械性能而大量含有al的合金钢。但是,越是较多地添加al,则在连续铸造中越容易在铸坯的表层生成横向裂纹,成为操作上及制品品质上的问题。
4.在弯曲型或垂直弯曲型的连续铸造机中的矫直点,对铸坯赋予矫直应力。已知横向裂纹沿着铸坯表层的原奥氏体晶界发生,矫直应力集中在沿着因aln和nbc等的析出而脆化的奥氏体晶界、或原奥氏体晶界所生成的薄膜状铁素体上,从而发生横向裂纹。此外,该横向裂纹特别容易在比从奥氏体向铁素体的相变区域稍高的温度区域发生,即便是非相变系组成,也同样发生横向裂纹。所以,通常采用在矫直点以回避延展性下降的温度区域(脆化温度区域)的方式控制铸坯的表面温度而抑制横向裂纹的发生的方法。
5.但是,如果想通过控制铸坯的表面温度来回避脆化温度区域,则操作上受到很大的制约,因此大多是困难的。于是,在专利文献1中,公开了以超过0.010质量%且0.025质量%以下添加ti,将铸坯的凝固壳厚度10mm~30mm的二次冷却带上部中的铸坯的表面温度设定为aln的析出开始温度以上的技术。
6.现有技术文献
7.专利文献
8.专利文献1:日本专利第6347164号公报
技术实现要素:9.发明所要解决的课题
10.但是,近年来,为了进一步提高机械性能,也正在进行含有0.20质量%以上的al的高铝钢的制造。如果al浓度增加,则aln从更高的温度析出,从而脆化温度区域扩大。所以,如果含有0.20质量%以上的al,则脆化温度区域显著扩大,所以通过回避脆化温度区域来进行弯曲及矫直在通常的操作上基本上是不可能的,不能回避横向裂纹。此外,如果含有0.50质量%以上的al,则脆化温度区域进一步显著扩大,所以即便是改善冷却条件的操作,回避脆化温度区域而进行弯曲及矫直基本上也是不可能的,不能回避横向裂纹。再者,发生横向裂纹的板坯除了需要采用研磨机等的修整以外,还要确认热轧后的起因于横向裂纹的缺陷,从而不能回避成品率的恶化。本发明的目的在于提供一种对于通过连续铸造而得到的板坯,不需要横向裂纹修整的制造性优异的板坯。
11.此外,在专利文献1所记载的方法中,以al浓度为0.063质量%~0.093质量%的低碳铝镇静钢为对象,在含有0.20质量%以上的al的高铝钢中,其效果并不清楚。再者,也可
以考虑随着al浓度的增加而较多地添加ti,但会招致tin的粗大化,可能导致疲劳强度的降低,因此ti的添加量也有极限。
12.本发明鉴于上述问题,其目的在于提供一种含有0.20质量%以上的al的高铝钢的铸坯,耐表面开裂敏感性优异的板坯及该板坯的连续铸造方法。
13.用于解决课题的手段
14.本发明人着眼于高铝钢的铸坯中的高温脆化的主要原因为aln的大量析出,研究了控制氮化物的析出。具体地讲,对添加了n固定能力比al更高的zr的钢的高温延展性进行了调査。其结果是,发现通过添加微量的zr而较大地改善了高温延展性。得知zr在刚凝固后生成zrn而使n固定化,因此可抑制aln向晶界的大量析出,从而能够彻底改善高铝钢的高温脆化。
15.综上,本发明如下所述。
16.(1)一种板坯,其特征在于:所述板坯为含有c:0.02质量%~0.50质量%、al:0.20质量%~2.00质量%的高铝钢的板坯,
17.zr含量满足以下的(1)式,
18.[zr]≥4/3
×
[al]
×
[n]
ꢀꢀꢀ
(1)
[0019]
其中,[zr]、[al]、[n]分别表示所述板坯中的含量(质量%)。
[0020]
(2)根据上述(1)所述的板坯,其特征在于:所述板坯的表层部中的总氮化物中的zrn的质量比率为50.0质量%以上。
[0021]
(3)根据上述(1)或(2)所述的板坯,其特征在于:所述板坯进一步含有:
[0022]
si:0.20质量%~3.00质量%、及
[0023]
mn:0.50质量%~4.00质量%。
[0024]
(4)一种铸坯的连续铸造方法,其特征在于:所述连续铸造方法是上述(1)~(3)中任一项所述的板坯的连续铸造方法,
[0025]
在矫直所述板坯时,在表面温度为800℃~1000℃的范围进行矫直。
[0026]
(5)根据上述(4)所述的板坯的连续铸造方法,其特征在于:将所述板坯的表层部中的平均冷却速度设定为60℃/min以下。
[0027]
发明的效果
[0028]
根据本发明,能够提供没有由矫直应力导致的开裂的板坯。
附图说明
[0029]
图1是表示拉伸温度为700℃~1100℃的范围时的断面收缩率的变化的图示。
[0030]
图2是表示拉伸温度为900℃下的[al]
×
[n]和[zr]的关系的图示。
具体实施方式
[0031]
以下,参照附图对本发明进行说明。再者,在本实施方式中,采用“~”表示的数值范围意味着包含“~”前后记载的数值的范围作为下限值及上限值。以“超过”或“低于”表示的数值不包含将其值作为下限值及上限值。
[0032]
为了制造含有0.20质量%以上的al的高铝钢,需要防止因连续铸造中的矫直点的矫直应力而发生横向裂纹。由于在矫直点使温度偏离脆化温度区域是困难的,因此为了在
矫直点于通常的温度区域进行铸坯的矫直,本发明人研究了添加zr的情况。
[0033]
(第1实验)
[0034]
首先,进行高温拉伸试验,以确认通过添加zr能以何种程度改善
[0035]
高温延展性。在该试验中,用表1所示的钢种a及钢种b两种钢(板5坯)而进行了实验。表1中的数值都表示质量%(mass%),如表1所
[0036]
示的那样,钢种a中不含zr,钢种b中含有zr,除此以外,为与钢种a大致相同的组成。再者,剩余部分都包含fe及杂质。再者,所谓“杂质”,指的是在工业化制造板坯时,从作为原料的矿石、废料或制造环境等混入的物质。
[0037]
表1
[0038]
钢种csimnpstizralna0.231.012.470.0110.0020.00200.700.0019b0.221.012.480.0110.0020.0020.0330.680.0020
[0039]
接着,在700℃~1100℃的范围内变更拉伸温度,用该两种钢求出了断面收缩率(r.a.:reduction area)(%)。具体地讲,基于jis g0567:2020,将25kg的通过真空熔炼而制作的各钢种拉伸锻造加工到φ15后,制成φ10的拉伸试验片(平行部90mm)。在高温拉伸试验中,采用具有冷却坩埚的高频感应加热型的高温拉伸试验装置,在将拉伸试验片熔化后以冷却速度1.0℃/s冷却到规定的拉伸温度,然后一面保持在规定的拉伸温度一面以应变速度3.3
×
10-4
(1/s)将拉伸进行到断裂。将试验后的拉伸试验片的断裂面的面积和试验前的试验片横断面积之差除以试验前的试验片横断面积,求出所得值的百分率(%)作为断面收缩率(颈缩率)。
[0040]
图1中示出了该拉伸试验的结果。图1中的白圆圈标记表示钢种a中的断面收缩率,黑圆圈标记表示钢种b中的断面收缩率。如图1所示的那样,得知如果添加zr,则尤其在800~1000℃的温度区域断面收缩率增大,高温延展性得以改善。这里,可以认为只要r.a.为50%以上,就不会因矫直应力而发生横向裂纹。得知由于以800~1000℃的范围通过矫直点在操作上是容易的,所以即使不进行回避脆化温度区域那样的温度控制,也能够通过添加zr来防止横向裂纹。
[0041]
(第2实验)
[0042]
接着,为了防止横向裂纹,进行了用于确认需要以何种程度添加zr的试验。具体地讲,将拉伸温度设定为900℃,如表2所示的那样准备al、n、zr量不同的多个样品(no.1~no.12)而进行拉伸试验,分别求出r.a.(%)。拉伸试验的具体方法与第1实验相同。表2及图2中示出了该拉伸试验的结果。
[0043]
表2
[0044][0045]
图2中,作为可以认为不发生横向裂纹的基准,将r.a.为50%以上者设为
○
、将r.a.低于50%者设为
×
。其结果是,得知zr的含量与al含量和n含量之积相关。也就是说,得知只要zr含量为al含量和n含量之积的4/3倍以上,r.a.就为50%以上,就能够防止由矫直应力造成的横向裂纹。
[0046]
基于以上的实验结果,对本发明涉及的板坯的化学组成进行说明。再者,本实施方式涉及的板坯是含有0.20质量%~2.00质量%的al的高铝钢,主要以薄板用为对象。al的优选的下限值为0.50质量%。当al的含量为0.50质量%以上时,如上所述容易发生横向裂纹,所以可更显著地得到本实施方式的效果。此外,基于上述的第2实验的结果,本实施方式涉及的板坯含有满足以下(1)式的量的zr。
[0047]
[zr]≥4/3
×
[al]
×
[n]
ꢀꢀꢀ
(1)
[0048]
这里,[zr]、[al]、[n]分别表示板坯中的含量(相对于板坯总质量的质量%)。
[0049]
此外,zr含量的上限没有特别的限定,但即使含有超过0.1质量%的zr,其效果也达到饱和,招致徒劳无益的成本上升,因此zr含量优选为0.1质量%以下。zr含量的下限也没有特别的限定,可由(1)式决定,zr含量优选为0.0010质量%以上。此外,n含量的上限及下限也没有特别的限定,但在不意图增加n含量的情况下,作为经由通常的精炼工序、连续铸造工序而含有的范围,优选将n含量设定为0.0080质量%以下。此外,基于精炼工序中的成本,优选将n含量设定为0.0010质量%以上。此外,虽以高铝钢为对象,但如果al含量超过2.00质量%,则与(1)式相比zr含量也增加,招致徒劳无益的成本上升。所以,al含量为0.20~2.00质量%,优选为0.50~2.00质量%,更优选为0.55~2.00质量%,进一步优选为0.60~2.00质量%。
[0050]
如上所述,在本实施方式涉及的板坯中,规定zr、al、n的含量的关系满足上述(1)式的条件。另一方面,其它元素的含量没有特别的限定,但优选按以下的范围含有c、si、mn,本技术中确认,只要是说明书中所示的c、si、mn等的范围,就能解决发明的课题。
[0051]
《c:0.02质量%~0.50质量%》
[0052]
c是提高钢的强度的元素,如果c含量低于0.02质量%,则不能满足作为高强度钢板的用途。此外,如果c含量超过0.50质量%,则硬度过高,不能担保必要的弯曲性。所以,将c含量设定为0.02质量%~0.50质量。
[0053]
《si:0.20质量%~3.00质量%》
[0054]
si是提高钢的强度的元素,如果si含量低于0.20质量%,则不能满足作为高强度
钢板的用途。此外,如果si含量超过3.00质量%,则对焊接性产生不良影响。所以,优选将si含量设定为0.20质量%~3.00质量%。
[0055]
《mn:0.50质量%~4.00质量%》
[0056]
mn是提高钢的强度的元素,如果mn含量低于0.50质量%,则不能满足作为高强度钢板的用途。此外,如果mn含量超过4.00质量%,则由于mn为偏析元素,因而有可能在铸坯或钢板中引起强度不均的发生。所以,优选将mn含量设定为0.50质量%~4.00质量%。上述以外的剩余部分包含铁及杂质,但也可以替代铁的一部分而含有几种成分。这里,所谓“杂质”,如上所述,指的是工业化制造板坯时,从作为原料的矿石、废料或制造环境等中混入的物质。所以,本实施方式涉及的板坯例如以质量%计,含有al:0.20~2.00%、zr:0.1%以下、n:0.0010~0.0080%、c:0.02~0.50%、si:0.20~3.00%、mn:0.50~4.00%、p:0.0005~0.1%、s:0.0001~0.05%、mo:0~0.1%、nb:0~0.1%、v:0~0.1%、b:0~0.005%、cr:0~0.1%、ni:0~0.5%、cu:0~0.5%,剩余部分包含铁及杂质,进而满足上述的(1)式。
[0057]
另外,如上所述,zr在刚凝固后生成zrn,使n固定化,因此可抑制aln向晶界的大量析出,能够彻底改善高铝钢的高温脆化,可回避板坯的横向裂纹。从这样的观点出发,板坯表面组织均匀存在的5mm的表层部中的总氮化物中的zrn的质量比率优选为50.0质量%以上,更优选为60.0质量%以上,进一步优选为75.0质量%以上。
[0058]
这里,板坯的表层部中的zrn的质量比率可通过以下方法进行测定。从制造的板坯切出铸坯表层观察用的样品(例如从铸坯宽度中央切出25mm宽25mm长25mm厚),对距铸坯表面为5mm深的位置的面进行镜面研磨,以制作观察面。接着,用sem/eds(搭载能量色散型x射线分析装置的扫描式电子显微镜)观察露出面(观察面)。由此,进行观察面中的元素面扫描,特定观察面中的尺寸200~5000nm(当量圆直径)的总氮化物。这里,作为可观察的氮化物,例如可列举zrn、aln、tin、nbn、bn、vn等。然后,根据基于特定结果而得到的总氮化物中的zrn的面积比率,根据板坯表层部中的总氮化物均匀分布的假设,可将面积比率看作为体积比率,从体积比求出总氮化物中的zrn的质量比率。再者,将zrn定义为相对于氮化物粒子的总质量含有50质量%以上的zr的氮化物。
[0059]
接着,对上述的板坯的连续铸造方法进行说明。在本实施方式中,由于不需要回避脆化温度区域,所以在连续铸造中尤其能够采用通常的方法。根据上述的第1实验的结果,在矫直铸坯时,在以铸坯的表面温度为800℃~1000℃的状态进行矫直时,效果特别显着,因此是优选的。
[0060]
这里,优选将板坯的表层部中的平均冷却速度设定为120℃/min以下,更优选设定为60℃/min以下。在此种情况下,能够使表层部中的zrn的质量比率在50.0质量%以上。特别是,通过将板坯的表层部中的平均冷却速度设定为60℃/min以下,能够使表层部中的zrn的质量比率在60.0质量%以上。板坯的表层部中的平均冷却速度可用以下方法进行测定。也就是说,用热电偶等测定板坯的宽度方向中央部的表面温度,通过二维的传热计算算出距该位置为5mm深的位置(测定位置)处的从1450到1000℃的平均冷却速度。具体地讲,将它们的温度差(450℃)除以将测定位置的温度从1450℃冷却到1000℃所需要的时间。由此,测定了板坯的表层部中的平均冷却速度。板坯的表层部中的平均冷却速度可通过二次冷却水量来调整。平均冷却速度的下限值例如可以为20℃/min。
[0061]
实施例
[0062]
接着,对本发明的实施例进行说明,但该条件为用于确认本发明的可实施性及效果的一条件例,本发明并不限定于该实施例的记载。本发明可通过不脱离本发明的主旨、且达到本发明的目的的多种手段来实施。
[0063]
准备c含量为0.3质量%、si含量为1.5质量%、mn含量为2.0质量%和al含量、n含量及zr含量分别不同的16种钢水,分别流入结晶器中,用连续铸造机进行连续铸造。再者,连续铸造机采用结晶器尺寸为250mm厚
×
1200mm宽的垂直弯曲型的连续铸造机,将铸造速度设定为1.2m/min。此外,在矫直点,都将铸坯的表面温度设定为850℃。此外,将表层部中的平均冷却速度设定为表3所示的值(60℃/min或120℃/min)。
[0064]
对按以上条件制作的各个板坯,通过上述的方法测定了板坯的表层部中的zrn的质量比率。另外,对一部分板坯,与第1实验同样地求出了900℃下的断面收缩率(r.a.)(%)。另外,关于板坯的横向裂纹,按以下的评价基准进行了评价。也就是说,在将板坯的表背面研磨0.7mm后,目视确认横向裂纹的有无。另外,在不对没能确认横向裂纹的板坯实施缺陷修整的情况下,用热轧工序的加热炉加热至1200℃而进行粗轧,然后按精轧温度880℃、板厚2.8mm的条件进行热轧,通过目视确认热轧后的起因于横向裂纹的缺陷的有无。将热轧后也没有起因于横向裂纹的缺陷的板坯评价为vg(很好)、将热轧后确认有起因于横向裂纹的缺陷的板坯评价为g(好)、将热轧前确认有横向裂纹的板坯评价为b(差)。表3中示出了实验结果。
[0065][0066]
表3中的下划线为没有满足本发明的条件的例子。如表3所示的那样,在满足(1)式的条件的情况下,与al或n的含量无关,不存在横向裂纹。另一方面,在没有满足(1)式的情况下,可以认为因zr不足,较多地残存aln而发生横向裂纹。在没有满足(1)式时,板坯的表层部中的zrn的质量比率也低于50.0质量%。
[0067]
另外,通过将板坯的表层部中的平均冷却速度设定为60℃/min以下,能够将板坯的表层部中的zrn的质量比率设定为60质量%以上。在此种情况下,热轧后也没有确认起因于横向裂纹的缺陷。另一方面,当板坯的表层部中的平均冷却速度为120℃/min时,板坯的表层部中的zrn的质量比率为50.0质量%以上且低于60.0质量%。在此种情况下,热轧前没有确认横向裂纹,但在热轧后确认有起因于横向裂纹的缺陷。
[0068]
以上,参照附图对本发明的适合的实施方式详细地进行了说明,但本发明并不限定于这些例子。很显然,只要是具有本发明所属技术领域的一般知识的人员,就可在权利要求书所记载的技术思想的范畴内,联想到各种变更例或修正例,这些当然也应理解为属于本发明的技术范围。