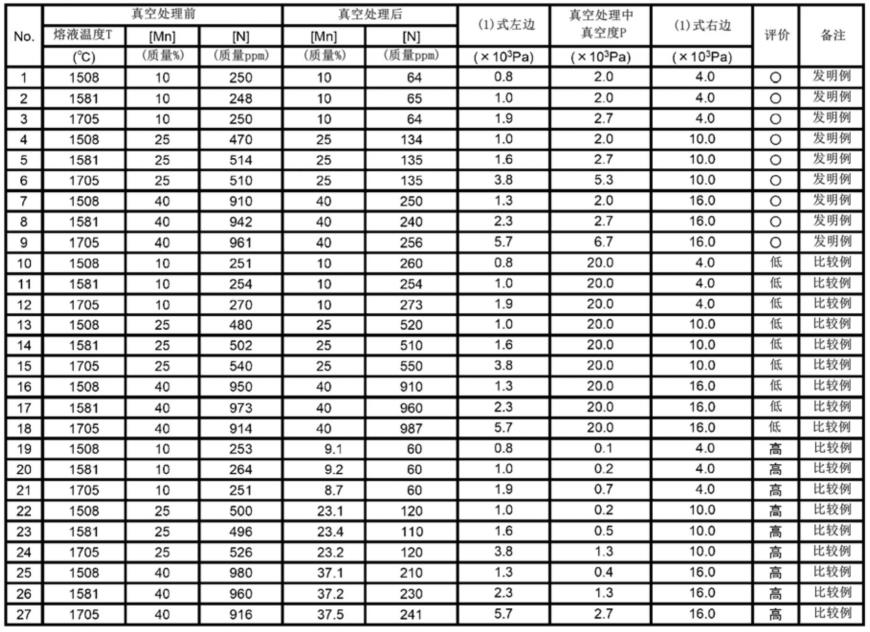
1.本发明涉及高锰钢的熔炼方法,特别涉及使氮浓度降低的高锰钢的熔炼方法。
背景技术:2.在利用一般的高炉-转炉法熔炼钢制品的工厂,熔炼含锰钢时采用在转炉吹炼中添加锰矿石的方法、在转炉出钢时或二次精炼工艺中添加锰铁等铁合金的方法。转炉出钢后,出于进一步降低碳浓度、氮浓度、减少非金属夹杂物等目的,大多进行例如使用rh式真空脱气设备的真空处理。在真空处理中,为了促进脱碳、脱氮而着眼于提高真空槽内的真空度,但是,锰与铁相比在钢水温度下蒸气压非常高,因此,对于含有锰的钢种而言,在真空处理中产生锰的挥发损失。
3.因此,例如专利文献1、专利文献2所公开的技术中提出了通过在真空处理中将脱气槽内的真空度设为2500~14000pa来抑制锰的挥发损失并且充分地降低碳浓度的方法。另外,专利文献3中提出了在锰浓度为10质量%以上的高锰钢的真空处理时在熔液温度为1500~1650℃且真空度为6000~16000pa的条件下进行处理的方法。
4.另外,专利文献4中公开了如下技术:为了不降低工厂的生产效率,利用电炉等设备将金属锰熔化,预先熔炼高锰浓度的熔液,进行与从转炉出钢的不含锰的普通钢水的联合浇注,由此得到锰含量超过10质量%的高锰熔液。
5.现有技术文献
6.专利文献
7.专利文献1:日本特开2005-60782号公报
8.专利文献2:日本特开2005-60783号公报
9.专利文献3:日本特开2010-248536号公报
10.专利文献4:日本特开平10-140227号公报
技术实现要素:11.发明所要解决的问题
12.但是,上述现有技术中还存在尚需解决的以下问题。
13.一般的钢制品的含锰钢种的锰浓度为1~2质量%,但近年来锰含量超过10质量%的钢种的需求增高。就这样的钢种而言,需要添加大量的锰源。但是,在通常利用转炉进行脱碳吹炼的情况下,由于锰的氧化损失,钢中的锰成品率变低,因此需要在利用转炉进行脱碳吹炼后添加锰源。在锰标准为mn:10质量%以上的高锰钢中,所添加的锰源的熔化热补偿量也变高。因此,转炉出钢后的二次精炼工艺中的热补偿负荷增加,生产效率显著降低。
14.在专利文献3记载的方法中,不依赖锰浓度地统一规定了处理中的温度条件和真空度条件,但锰的挥发损失随着锰浓度而大幅变化。例如,含有约10质量%的锰的熔液的真空处理与含有约40质量%的锰的熔液的真空处理相比,即使提高真空度,对挥发损失的担心也相对较小。因此,在不依赖锰浓度地在统一的条件下进行真空处理时,对于约10质量%
的相对低的锰浓度的熔液而言,由于过度降低真空度,导致脱氮速度的降低等生产率降低。
15.另外,专利文献4记载的技术中产生下述问题。由于锰与氮的亲和力大,因此,随着钢水中的锰浓度增加,熔液中的氮溶解度增加。在实施如专利文献4中记载的那样的联合浇注方式的情况下,由于大气的卷入,熔液中的氮浓度容易增加。为了达到产品标准的氮浓度,需要降低熔液中的氮浓度。作为浇包精炼中的脱氮方法,通常可以通过使用真空脱气槽在真空条件下进行回流来除去熔液中的氮。
16.在此,如前所述,随着锰浓度增加,氮在熔液中的溶解度升高,脱氮反应也变得难以发生。因此,为了促进脱氮反应,需要提高真空脱气处理中的真空度。例如,如果是含有铬的合金钢,则即使提高真空度也没有问题。但是,在锰钢的情况下,由于钢水温度下的锰的蒸气压高,因此,如果过度提高真空脱气处理中的真空度,则锰的挥发损失显著增加。因此,存在真空排气设备配管等上基体金属的附着变得显著这样的问题。因此,需要能够兼顾锰挥发损失的抑制和熔液中的氮浓度降低。
17.本发明是鉴于上述情况而完成的,目的在于提供能够兼顾锰挥发损失的抑制和熔液中的氮浓度降低的高锰钢的熔炼方法。
18.用于解决问题的方法
19.为了解决上述问题并实现上述目的而开发的本发明如下述主旨构成所示。即,本发明提出一种高锰钢的熔炼方法,其是通过进行利用转炉实施脱碳吹炼后出钢的钢水与另行熔炼的高锰熔液的联合浇注来熔炼锰浓度为10质量%以上且40质量%以下的高锰钢的方法,其特征在于,在进行联合浇注后、进行铸造之前的期间,通过实施真空处理而使联合浇注中的氮浓度降低,此时,基于真空处理前的熔液中锰浓度和熔液温度,对真空处理中的真空度进行调整。
20.需要说明的是,关于本发明的上述高锰钢的熔炼方法,认为将上述真空处理中的真空度p(pa)设为下述(1)式所表示的范围来进行真空处理是更优选的解决方法,在此,(1)式中,t为熔液温度(℃),[mn]为熔液中锰浓度(质量%),p为真空槽内的真空度(pa)。
[0021]
0.005986
×
t
2-19.07
×
t+15765.5+(0.001613
×
t
2-4.624
×
t+3319.7)
×
[mn]<p<400
×
[mn]
…
(1)
[0022]
发明效果
[0023]
如以上说明的那样,根据本发明,能够在抑制锰挥发损失的同时使熔液中的氮浓度降低,从而能够熔炼兼顾高的锰成品率和低氮含量的高锰钢。特别是,通过根据锰浓度适当地控制真空处理中的真空度,还能够抑制生产率的降低。
具体实施方式
[0024]
在高锰钢的情况下,随着锰浓度的增加,钢水(熔液)温度下的锰蒸气压升高。特别是在真空脱气处理中,如果将真空度提高到处理熔液的锰蒸气压以上,则在真空槽内锰蒸气变为剧烈沸腾的状态,存在锰的挥发损失显著增加的问题。因此,为了抑制这样的现象,可以通过降低真空度来降低风险。但是,真空槽中的氮分压越低,越促进脱氮反应。因此,在过度降低真空度的情况下,真空槽中的氮分压升高,不能使熔液中的氮浓度降低。
[0025]
为了能够兼顾锰挥发损失的抑制和氮浓度降低,本发明人进行了深入调查,结果判明,存在不产生锰挥发损失且对氮浓度降低有效的真空度。发现锰蒸气压和氮在熔液中
的溶解度均强烈依赖于锰浓度、熔液温度。
[0026]
首先,在使锰浓度和熔液温度发生各种变化的条件下,测定含锰熔液的锰的蒸气压,结果发现,锰蒸气压随着熔液温度的增加而大致以二次函数的方式增加、并且与锰浓度大致成比例地增加。因此,可以以锰浓度的一次方程的形式以及熔液温度的二次方程的形式通过回归分析求出锰的蒸气压。
[0027]
另外,对引起含锰熔液中的氮浓度降低的真空度进行了调查,结果发现,大致仅依赖于熔液中的锰浓度,与锰浓度成比例。
[0028]
基于以上的实验结果进行了回归分析,结果判明了,兼顾锰挥发损失的抑制和氮浓度降低的真空处理的真空度p(pa)可以以熔液中的锰浓度[mn](质量%)和熔液温度t(℃)的函数的形式如下述(1)式表示。
[0029]
0.005986
×
t
2-19.07
×
t+15765.5+(0.001613
×
t
2-4.624
×
t+3319.7)
×
[mn]<p<400
×
[mn]
…
(1)
[0030]
本发明的高锰钢的熔炼方法如下所述。
[0031]
(a)利用转炉实施脱碳吹炼,将普通钢的钢水出钢到浇包内(普通钢熔炼工序)。如果考虑吹炼中的氧化,则优选在转炉内不添加锰源。
[0032]
(b)利用电炉等设备将锰源熔化,预先熔炼高锰熔液。如果进行脱磷处理、脱碳处理,则由于氧化而产生锰损失,因此,优选将金属锰熔化(高锰熔液熔炼工序)。
[0033]
(c)进行从转炉出钢的普通钢的钢水与利用电炉等熔化的高锰熔液的联合浇注(联合浇注工序)。
[0034]
(d)联合浇注工序后的氮浓度变为几百质量ppm,因此,为了降低氮浓度,使用真空脱气设备、例如rh式真空脱气设备进行真空处理,使氮浓度降低(真空处理工序)。此时,根据熔液的锰浓度和熔液温度,优选按照上述(1)式适当地控制真空度。
[0035]
(e)真空处理后,在lf等浇包精炼工艺中实施成分调整等,通过连续铸造设备或铸锭作业进行铸造(铸造工序)。
[0036]
实施例
[0037]
<实施例1>
[0038]
(处理1)
[0039]
为了应用本发明方法,利用转炉进行脱碳吹炼,出钢到浇包内。作为出钢成分,得到c:0.02质量%、mn:0.01质量%的钢水200吨(普通钢熔炼工序)。另外,在电炉中,将金属锰75吨和废料25吨熔化,得到mn浓度为75质量%的高锰熔液100吨(高锰熔液熔炼工序)。进行它们的联合浇注(联合浇注工序),结果mn为25质量%、n为479质量ppm。另外,熔液温度t为1600℃。将联合浇注后的浇包运至rh式真空脱气设备,将熔液在真空度p=3333pa(25托)的条件下回流60分钟(真空处理工序),结果真空处理后的mn浓度为24.9质量%、n浓度为95质量ppm。
[0040]
(处理2)
[0041]
作为比较例,利用转炉进行脱碳吹炼,出钢到浇包内。作为出钢成分,得到c:0.02质量%、mn:0.01质量%的钢水200吨(普通钢熔炼工序)。另外,在电炉中,将金属锰75吨和废料25吨熔化,得到mn浓度为75质量%的高锰熔液100吨(高锰熔液熔炼工序)。进行它们的联合浇注(联合浇注工序),结果mn为25质量%、n为524质量ppm。另外,熔液温度t为1600℃。
将联合浇注后的浇包运至rh式真空脱气设备,在真空度p=933pa(7托)的条件下回流60分钟(真空处理工序),结果真空处理后的mn浓度下降至23.0质量%、n浓度为87质量ppm。
[0042]
(处理3)
[0043]
作为比较例,利用转炉进行脱碳吹炼,出钢到浇包内。作为出钢成分,得到c:0.02质量%、mn:0.01质量%的钢水200吨(普通钢熔炼工序)。另外,在电炉中,将金属锰75吨和废料25吨熔化,得到mn浓度为75质量%的高锰熔液100吨(高锰熔液熔炼工序)。进行它们的联合浇注(联合浇注工序),结果mn为25质量%、n为460质量ppm。另外,熔液温度t为1600℃。将联合浇注后的浇包运至rh式真空脱气设备,在真空度p=20.0
×
103pa(150托)的条件下回流60分钟(真空处理工序),结果真空处理后的mn浓度为25.0质量%、n浓度为435质量ppm。
[0044]
应用了本发明方法的处理1由于将真空处理中的真空度p适当地保持在(1)式的范围内,因此,能够在维持真空处理后的熔液中的mn浓度的状态下使n浓度降低至100质量ppm以下。就比较例的处理2而言,真空处理中的真空度p过高,真空处理后的熔液中mn浓度降低,观察到了锰损失。另一方面,就真空处理中的真空度p过低的处理3而言,熔液中的n几乎没有降低。
[0045]
<实施例2>
[0046]
使用与上述实施例1同样的设备,在各种锰浓度、熔液温度t、真空度p下熔炼高锰钢。将处理条件以及真空处理前后的mn浓度[mn](质量%)和n浓度[n](质量ppm)示于表1中。同时,表1中为了比较而示出了上述(1)式的左边、右边的值和真空处理中的真空度p(pa)。
[0047]
[表1]
[0048][0049]
就以使真空处理中的真空度p满足上述(1)式的方式适当地进行了管理的处理
no.1~9(评价栏
“○”
标记)而言,在维持钢水中的mn浓度([mn])的状态下实现了n浓度([n])的降低。另一方面,在真空度p过低、即不满足(1)式右边的不等号的处理no.10~18(评价栏“低”)中,还存在钢水中n浓度没有降低而变差的例子。另外,就真空度p过高、即不满足(1)式左边的不等号的处理no.19~27(评价栏“高”)而言,在真空处理后钢水中mn浓度降低,产生了锰损失。
[0050]
产业上的可利用性
[0051]
根据本发明,通过在适当的真空度下对联合浇注后的高锰熔液进行真空处理,能够在不使锰挥发损失的情况下降低氮浓度,因此能够高效地制造高锰钢。