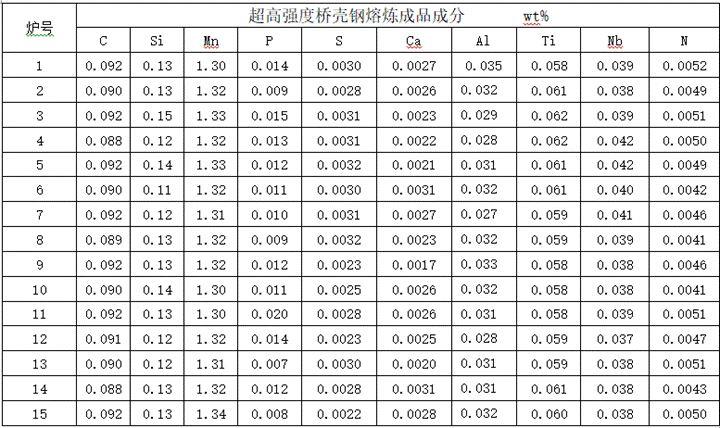
1.本发明涉及一种超高强度低屈强比桥壳钢的制备方法,属于汽车用钢材技术领域。
背景技术:2.汽车驱动桥是汽车承载的重要结构,广泛应用于重卡、半挂牵引车、客车、工程机械等领域。其通过悬架总成与车架相连接,两端安装车轮,传递车架与车轮之间的各种作用力,支撑着汽车载荷。因此对材料的强度、刚度、疲劳寿命等性能指标提出了极高的要求。驱动桥壳应具有高强度、高刚度、高质量,并便于主减速器的拆装和调整。热冲压桥壳用钢凭借高温变形抗力小、残余应力低、疲劳寿命高等显著优点,牢牢占据着重卡桥壳生产的主导地位。高强度的汽车桥壳通常采用热冲压成型,然而,热冲压桥壳用钢因热冲压后强度显著降低成为业内的最大难题,限制了桥壳的轻量化与整车承载能力提升,严重制约了重卡汽车行业技术进步和低碳绿色发展。
3.文献检索:(1) 攀钢研制了490 mpa级汽车桥壳用钢热轧高强钢板,采用铌、钛复合强化,开发出了屈服强度405~453 mpa,抗拉强度495~531 mpa,断后延伸率为30~31%,屈强比为0.82~0.86,钢材组织为大量的铁素体和极少量的珠光体,晶粒度为11级的汽车桥壳用钢。见《柳钢科技》中南
·
泛珠三角地区第五届轧钢学术交流会论文专辑,2009,p57~61。
4.(2)北京钢铁研究总院的张楠等人研究了《600 mpa 级冷压桥壳钢 cghaz 组织性能及抗疲劳特征》,该钢主要化学成分 (质量分数,%) 为:c:0.08~0.09%, si:0.14 ~0.16%,mn:1.58~1.62%,s+p ≤0.001%。通过钛微合金化(钛含量为0.08%),铌、钛复合微合金化(铌含量为0.04%,钛含量为0.02%),铌、钒复合微合金化(铌含量为0.04%,钒含量为0.05%)三种成分体系进行了实验室试验,对材料的拉伸性能和抗疲劳特征进行了对比,经过对比试验,提出了应优先选用nb-v 微合金化成分体系生产600mpa 级冷压桥壳钢的建议,见《焊接学报》,2020年11期,p38~46。
5.(3) 新疆八一钢铁采用铌、钒、钛三种元素复合强化开发了较低级别的热轧桥壳580qk钢板。屈服强度达到了512 mpa,抗拉强度达到了628mpa,断后伸长率为23.5~26%,强屈比小于0.86。见《新疆钢铁》2017年第3期。
6.(4)河北普阳钢铁采用铌钛复合强化模式生产了600 mpa级汽车桥壳钢,屈服强度在485~520mpa,抗拉强度620~641mpa,屈强比0.78~0.83,《轧钢》2017.3。
技术实现要素:7.本发明的目的在于提供一种超高强度低屈强比桥壳钢的制备方法,能够提高钢材冷冲压成形性能,解决材料拉伸性能提高后冷冲压开裂,避免热冲压成形材料的强度降低的难题。
8.本发明采用的技术方案是,一种超高强度低屈强比桥壳钢的制备方法,1).成分设
计质量百分数组成为c:0.090~0.12wt%,si:0.05~0.15%,mn:1.25~1.35wt%,p:≤0.018wt%,s:≤0.004wt%,ti:0.055~0.065wt%,al:0.020~0.045wt%,n:≤0.050wt%,余量为铁和不可避免的杂质;2).制备方法,采用铁水脱硫预处理、120t顶底复吹转炉冶炼,lf精炼处理、板坯连铸、1750热连轧工艺生产:[1]转炉冶炼,出钢控制:[c]:0.065-0.085%,[p]:≤0.012%、[s]:≤0.007%,转炉出钢采用电石预脱氧,把萤石、电石、活性石灰按1:2:5的质量比进行混合,原料的粒度10~20mm,在转炉出钢过程中按时间顺序依次加入混合脱氧剂,加入目标值500kg/炉,转炉出钢过程的钢渣混冲,提高预脱氧效率,然后加入铝铁深脱氧,同时进行渣洗,渣洗料为预熔渣,成分为cao含量约40%,al2o3含量约45%,sio2含量≤5%;[2]lf精炼处理前定氧,按残氧每10ppm喂入铝线1.5kg/炉钢,铝的回收率按45%计算,喂入铝线后钢包底吹氩强搅拌5分钟,促使夹杂物上浮去除,钢包钢液到lf补加铝铁,铝的回收率按65%加入,lf精炼过程控制氮含量的方法是造泡沫渣埋弧精炼,方法是为提高渣的粘度配入高三氧化二铝含量和金属铝的炉渣促进剂,成分al含量30%,al2o3含量40~42%,sio2含量≤5%,caf2含量5-8%,caco3含量20%,碳化硅1.5%,lf精炼末期,钢中钙和钛除外的其它成分符合钢的熔炼成品成分后,加入钛铁,钛回收率大于70%,钛铁配入后钢包底吹氩气搅拌,熔化、均匀成分,钢水快速深脱硫,硫含量小于0.0035%;然后钙处理,钢包底软吹氩搅拌,喂入钙铁线进行夹杂物的变性处理,软吹时间控制在8~10分钟,钢水上连铸温度控制在1585~1590℃;[3]连铸,每炉钢连铸板坯拉速恒定,并采用板坯动态压下,压下量约6mm,钢水过热度控制在10~25℃,目标拉速1.1m/min,铸坯设计厚度250mm,板坯拉速控制:宽度1360mm板坯,板坯连铸拉速控制在1.1~1.20m/min,目标值1.15m/min;宽度1500mm板坯,板坯连铸拉速控制在0.85~0.95m/min,目标值0.90m/min;板坯凝固末端压下量大于6mm,板坯中心偏析不大于1.8级,曼内斯曼标准,下线板坯必须堆垛保温;[4]轧制,板坯加热温度1210~1230℃,板坯入加热炉温度避开裂纹敏感区,热装温度在400~620℃,避免轧后钢卷边部出现翘皮缺陷;[5]采用1750热连轧轧机轧制厚度为8.0mm~10mm的热轧卷,板坯加热温度1210~1230℃,粗轧出口温度为1030~1070℃,粗轧中间坯厚度42~45mm,精轧终轧温度840~860℃,钢卷厚度为8~10mm的卷取温度590~610℃。
[0009]
钢材力学性能:钢材力学性能(横向)检测显示,屈服强度550~581mpa,抗拉强度680~713mpa,断后伸长率22.0~27.0%,材料的屈强比为0.79~0.82,钢材-20℃冲击功值153-199j,钢材-0℃冲击功值为176-233j,显示材料具有很低的耐低温脆性转变温度。由于锰含量的大幅度降低,由偏析导致的钢材的带状组织显著减轻,材料的带状组织不大于1.5级。
[0010]
熔炼成品成分和板坯质量:采用本方法生产15炉,生产245mm
×
1510mm
×
10500mm,,熔炼成品成分见表1。板坯中心偏析抽检最小值为1级,最大值为1.8级(曼内斯曼标准)。
[0011]
表1采用本发明方法生产的超高强度桥壳钢熔炼成品成分
轧后钢材力学性能表2采用本发明方法生产的超高强度桥壳钢材性能试验检测显示,采用本发明生产的钢卷,在拉伸强度大幅度提高的同时,钢材拉伸性能极其稳定,不同材料号(不同炉号)的屈服强度波动的的最大值31mpa,抗拉强度波动的最大值33mpa,由于采用相对较高的碳含量和较低的铌含量的成分设计模式钢材的屈强比不大于0.82,对于冷冲压桥壳的制作及其有利。
[0012]
钢材的组织和纯净度:6炉钢轧后钢材抽检,组织为铁素体+珠光体,晶粒度在10级至11级之间。非金属夹杂物最大为b类细1.0级,铌钛的碳、氮物夹杂小于20μm,满足纯净钢
要求,有效防止了钢材的冷冲压开裂,钢材的带状组织不大于1.5级。
[0013]
表3 采用本发明方法生产的超高强度桥壳钢钢材的组织及纯净度检测结果本方法制备的材料,采用锰合金减量化成分设计,节约了合金,降低了钢材的带状组织,解决了冷冲压开裂难题,提高了钢材的性能稳定性。本方法制备的材料,采用锰含量减量化,铌钛复合强化的成分设计,严格控制铌含量和碳含量,使材料抗拉强度显著提高的同时,控制了屈服强度的快速提升,获得了低屈强比的高强度材料,冷冲压制造桥壳时具有良好的加工成形性能,具备大批量工业化生产。
具体实施方式
[0014]
一种超高强度低屈强比桥壳钢的制备方法,1).成分设计质量百分数组成为c:0.090~0.12wt%,si:0.05~0.15%,mn:1.25~1.35wt%,p:≤0.018wt%,s:≤0.004wt%,ti:0.055~0.065wt%,al:0.020~0.045wt%,n:≤0.050wt%,余量为铁和不可避免的杂质;2).制备方法,采用铁水脱硫预处理、120t顶底复吹转炉冶炼,lf精炼处理、板坯连铸、1750热连轧工艺生产。
[0015]
[1]转炉冶炼,出钢控制:[c]:0.065-0.085%,[p]:≤0.012% 、[s]:≤0.007%。转炉出钢采用电石预脱氧,为防止电石和钢水剧烈反应导致包内钢水翻腾和爆炸,把萤石、电石、活性石灰按1:2:5的质量比进行混合,原料的粒度10~20mm,在转炉出钢过程中按时间顺序依次加入混合脱氧剂,加入目标值500kg/炉,转炉出钢过程的钢渣混冲,提高预脱氧效率,然后加入铝铁深脱氧,同时进行渣洗(渣洗料为预熔渣,成分为cao含量约40%,al2o3含量约45%,sio2含量≤5%)。
[0016]
[2]lf精炼处理前定氧,根据钢中的残氧量和要求的成分铝含量,不足时可喂入铝线,按残氧每10 ppm喂入铝线1.5kg/炉钢,铝的回收率按45%计算,喂入铝线后钢包底吹氩强搅拌5分钟,促使夹杂物上浮去除。钢包钢液到lf补加铝铁,铝的回收率按65%加入。lf精炼过程控制氮含量的方法是造泡沫渣埋弧精炼,方法是为提高渣的粘度配入高三氧化二铝含量和金属铝的炉渣促进剂,成分al含量30%,al2o3含量40~42%,sio2含量≤5%,caf
2 含量5-8%,caco3含量20%,碳化硅1.5%),lf精炼末期,钢中其它成分(钙和钛除外)符合钢的熔炼成品成分后,加入钛铁,钛回收率大于70%(否则将有大量的钛的氧化物夹杂生成)。钛铁配入后钢包底吹氩气搅拌,熔化、均匀成分,严禁加入钛铁后送电提温再处理或大氩气流量强搅拌,造成钢水增氮和裸露氧化,生成大颗粒钛的氧化物夹杂和铌钛的氮化物夹杂。lf精炼
形成的泡沫渣覆盖钢水利于底吹氩搅拌脱硫,钢水快速深脱硫,硫含量小于0.0035%;然后钙处理,钢包底软吹氩搅拌,喂入钙铁线进行夹杂物的变性处理,软吹时间控制在8~10分钟。钢水上连铸温度控制在1585~1590℃。
[0017]
[3]连铸,连铸钢水温度的保障措施,钢包顶渣上面必须加覆盖剂,连钢水经过的各连接部位全部采用氩气封闭,保护浇铸,每炉钢连铸板坯拉速恒定,并采用板坯动态压下,压下量约6mm,钢水过热度控制在10~25℃,目标拉速1.1 m/min。通过低硫钢水,低过热度,恒拉速连铸,解决了板坯中心偏析,消除了偏析带中的硫化锰夹杂。铸坯设计厚度250mm,板坯拉速控制:宽度1360mm板坯,板坯连铸拉速控制在1.1~1.20m/min,目标值1.15 m/min;宽度1500mm板坯,板坯连铸拉速控制在0.85~0.95m/min,目标值0.90m/min;板坯凝固末端压下量大于6mm,板坯中心偏析不大于1.8级(曼内斯曼标准),板坯实现了灵活轧制(可热装轧制和冷装轧制)。下线板坯必须堆垛保温。
[0018]
[4]轧制,板坯加热温度1210~1230℃,板坯入加热炉温度避开裂纹敏感区,热装温度在400~620℃,避免轧后钢卷边部出现翘皮缺陷。
[0019]
[5]采用1750热连轧轧机轧制厚度为8.0mm~10mm的热轧卷,板坯加热温度1210~1230℃,粗轧出口温度为1030~1070℃,粗轧中间坯厚度42~45mm,精轧终轧温度840~860℃(设计目标终轧温度850℃),钢卷厚度为8~10mm的卷取温度590~610℃(设计卷取温度600℃)。