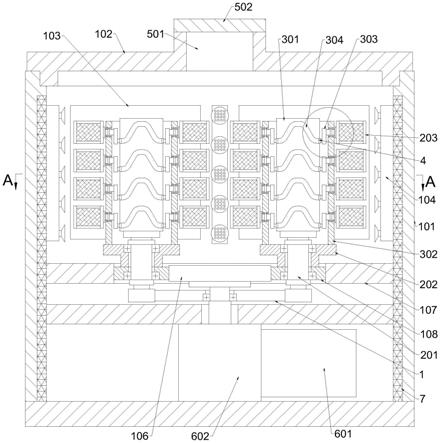
1.本发明涉及热处理设备技术领域,具体涉及一种汽车制动器摩擦片热处理装置。
背景技术:2.摩擦片是一种广泛应用于机械工程和离合器领域的机械零件,其具有较高的耐磨性。为了提升摩擦片的硬度,从而提升摩擦片的耐磨性,需要对摩擦片进行淬火等热处理。
3.现有的摩擦片热处理装置,难以使摩擦片全方位的均匀受热,也难以使加热后的摩擦片全方位与冷却液接触,从而使得摩擦片的淬火质量低下。
技术实现要素:4.本发明的目的是为了克服现有技术中的问题,提供一种汽车制动器摩擦片热处理装置,能使摩擦片全方位的均匀受热,还能使加热后的摩擦片全方位与冷却液接触,从而使得使得摩擦片的各处冷却速率相同,进而提升摩擦片的淬火质量。
5.本发明提供了一种汽车制动器摩擦片热处理装置,包括:
6.壳体,上设有壳盖;
7.多个加热片,设于所述壳体内壁,所述多个加热片电连接有控制器,所述控制器电连接有电源装置;
8.多个喷雾机构,设于所述壳体内壁,所述多个喷雾机构连通有供液装置;
9.行星齿轮系,设于所述壳体内,行星齿轮系的太阳轮连接有动力装置,所述动力装置与所述控制器电连接,行星齿轮系的齿圈固连于所述壳体内壁,行星齿轮系设有多个行星齿轮;
10.多个翻转货架,分别设于不同的行星齿轮上,所述翻转货架用于将放置于其上的摩擦片进行翻转。
11.较佳地,所述翻转货架包括连接轴、安装座、凸轮机构和夹笼,所述连接轴竖直设置,连接轴一端与所述行星齿轮系的齿轮架固连,行星齿轮与连接轴轴承连接,所述安装座的下端面与行星齿轮固连,所述凸轮机构与连接轴和安装座连接,所述夹笼连接于凸轮机构上,摩擦片放置于所述夹笼内,在凸轮机构的作用下,夹笼进行转动,夹笼的回转中心轴线与行星齿轮的回转中心轴线垂直。
12.较佳地,所述凸轮机构包括凸轮、套筒和曲拐,所述凸轮连接于连接轴顶端,套筒套设于所述凸轮外且套筒的下端面连接于所述安装座上表面,所述凸轮外侧壁设有螺旋凹槽,套筒壁上设有通孔,所述曲拐一端与与所述螺旋凹槽滑动连接,曲拐的另一端突出所述通孔且与通孔轴承连接,所述夹笼连接于曲拐远离凸轮一端。
13.较佳地,所述曲拐与所述螺旋凹槽之间设有滑套,所述滑套轴枢连接于曲拐上,滑套与所述螺旋凹槽滑动连接。
14.较佳地,所述壳盖上设有通气孔,所述通气孔上设有气盖。
15.较佳地,所述动力装置包括电机和减速器,所述电机与所述减速器的输入端连接,
所述减速器的输出端与所述太阳轮连接,电机与所述控制器电连接。
16.较佳地,所述壳体内设有保温层。
17.与现有技术相比,本发明的有益效果是:本发明的一种汽车制动器摩擦片热处理装置,能使摩擦片全方位的均匀受热,还能使加热后的摩擦片全方位与冷却液接触,从而使得使得摩擦片的各处冷却速率相同,进而提升摩擦片的淬火质量。本发明的翻转货架能够连续不断地对摩擦片进行翻转,从而使得摩擦片受热更均匀。本发明的凸轮机构能够对夹笼进行连续翻转,从而实现对摩擦片进行连续翻转,使得摩擦片受热和受冷更均匀。通过设置滑套,避免曲拐在螺旋凹槽内出现卡死现象。通过设置通气孔和气盖,在对摩擦片进行加热时,盖上气盖,使壳体迅速升温,在对摩擦片进行冷却时,使壳体内的温度迅速降低,从而提升摩擦片淬火的质量。通过设置减速器,提升电机的扭力以及提升电机驱动的平稳性。通过设置保温层,从而在对摩擦片进行加热时,降低壳体的散热速率,从而提升壳体内的升温速率。
附图说明
18.图1为本发明的结构示意图;
19.图2为本发明a-a面的结构示意图;
20.图3为本发明曲拐处的结构示意图。
21.附图标记说明:
22.101.壳体,102.壳盖,103.加热片,104.喷雾机构,105.供液装置,106.太阳轮,107.齿圈,108.行星齿轮,201.连接轴,202.安装座,203.夹笼,301.凸轮,302.套筒,303.曲拐,304.螺旋凹槽,4.滑套,501.通气孔,502.气盖,601. 电机,602.减速器7、保温层。
具体实施方式
23.下面结合附图1-3,对本发明的具体实施方式进行详细描述,但应当理解本发明的保护范围并不受具体实施方式的限制。基于本发明中的实施例,本领域普通技术人员在没有做出创造性劳动的前提下所获得的所有其他实施例,都属于本发明保护的范围。
24.实施例1:
25.如图1-3所示,本发明提供的一种汽车制动器摩擦片热处理装置,包括:壳体101、多个加热片103、多个喷雾机构104、行星齿轮系和多个翻转货架,壳体101上设有壳盖102;多个加热片103设于所述壳体101内壁,所述多个加热片103电连接有控制器,所述控制器电连接有电源装置;多个喷雾机构104 设于所述壳体101内壁,所述多个喷雾机构104连通有供液装置105;行星齿轮系设于所述壳体101内,行星齿轮系的太阳轮106连接有动力装置,所述动力装置与所述控制器电连接,行星齿轮系的齿圈107固连于所述壳体101内壁,行星齿轮系设有多个行星齿轮108;多个翻转货架分别设于不同的行星齿轮108 上,所述翻转货架用于将放置于其上的摩擦片进行翻转。
26.现简述实施例1的工作原理:
27.在进行摩擦片淬火时,将摩擦片放置在翻转货架上,盖上壳盖102。通过控制器打开加热片103和动力装置,电加热片103开始通电加热,动力装置驱动太阳轮106转动,太阳轮106驱动多个行星齿轮108转动,每个行星齿轮108 驱动驱动连接在其上的翻转货架转
动,转动的翻转货架使得放置于其上的摩擦片均匀受热,更进一步通过翻转货架将放置在其上的摩擦片进行翻转,从而对摩擦片的正反两面进行均匀加热,结合翻转货架的转动,从而使摩擦片全方位的均匀受热。在摩擦片加热完成后,利用喷雾机构104进行对翻转货架上的摩擦片进行冷却,动力装置驱动翻转货架进行转动,结合翻转货架对摩擦片进行翻转,从而使经过加热的摩擦片全方位的接触喷雾机构104喷出的冷却液,从而使摩擦片全方位与冷却液接触,使得摩擦片的各处冷却速率相同,进而提升摩擦片的淬火质量。
28.本发明的一种汽车制动器摩擦片热处理装置,能使摩擦片全方位的均匀受热,还能使加热后的摩擦片全方位与冷却液接触,从而使得使得摩擦片的各处冷却速率相同,进而提升摩擦片的淬火质量。
29.实施例2:
30.在实施例1的基础上,为了使翻转货架能够连续不断地对摩擦片进行翻转,从而使得摩擦片受热更均匀。
31.如图1和2所示,其中,所述翻转货架包括连接轴201、安装座202、凸轮301机构和夹笼203,所述连接轴201竖直设置,连接轴201一端与所述行星齿轮系的齿轮架固连,行星齿轮108与连接轴201轴承连接,所述安装座202 的下端面与行星齿轮108固连,所述凸轮301机构与连接轴201和安装座202 连接,所述夹笼203连接于凸轮301机构上,摩擦片放置于所述夹笼203内,在凸轮301机构的作用下,夹笼203进行转动,夹笼203的回转中心轴线与行星齿轮108的回转中心轴线垂直。
32.太阳轮106驱动行星齿轮108绕太阳轮106进行公转,转动的行星齿轮108 驱动连接轴201绕太阳轮106公转,由于连接轴201与齿轮架固连。因此,行星齿轮108绕连接轴201自转,连接在行星齿轮108上的安装座202进行自转,安装座202相对于连接轴201进行自转,安装座202驱动凸轮301机构进行转动。在凸轮301机构的作用下,夹笼203连续进行自转且夹笼203的回转中心轴线与行星齿轮108的回转中心轴线垂直,进而对放置于夹笼203内的摩擦片进行连续翻转,从而使得摩擦片受热更均匀。
33.实施例3:
34.在实施例2的基础上,为了能够对夹笼203进行连续翻转,从而实现对摩擦片进行连续翻转。
35.如图1和2所示,其中,所述凸轮301机构包括套筒302、凸轮301和曲拐303,所述凸轮301连接于连接轴201顶端,套筒302套设于所述凸轮301 外且套筒302的下端面连接于所述安装座202上表面,所述凸轮301外侧壁设有螺旋凹槽304,套筒302壁上设有通孔,所述曲拐303一端与与所述螺旋凹槽304滑动连接,曲拐303的另一端突出所述通孔且与通孔轴承连接,所述夹笼203连接于曲拐303远离凸轮301一端。
36.由于凸轮301连接在连接轴201上,行星齿轮108驱动安装座202绕连接轴201转动,安装座202驱动套筒302绕连接轴201转动,进而使得套筒302 绕凸轮301转动。凸轮301上的螺旋凹槽304驱动曲拐303连续转动,曲拐303 驱动夹笼203进行连续翻转,进而实现对摩擦片进行连续翻转,使得摩擦片受热和受冷更均匀。
37.作为一种优选方案,如图1和3所示,其中,所述曲拐303与所述螺旋凹槽304之间设有滑套4,所述滑套4轴枢连接于曲拐303上,滑套4与所述螺旋凹槽304滑动连接。通过设置滑套4,避免曲拐303在螺旋凹槽304内出现卡死现象。
38.作为一种优选方案,如图1所示,其中,所述壳盖102上设有通气孔501,所述通气孔501上设有气盖502。通过设置通气孔501和气盖502,在对摩擦片进行加热时,盖上气盖502,使壳体101迅速升温,在对摩擦片进行冷却时,打开气盖502,让受热蒸发的冷却液能够及时排出壳体101,使壳体101内的温度迅速降低,从而提升摩擦片淬火的质量。
39.作为一种优选方案,如图1所示,其中,所述动力装置包括电机601和减速器602,所述电机601与所述减速器602的输入端连接,所述减速器602的输出端与所述太阳轮106连接,电机601与所述控制器电连接。通过设置减速器602,提升电机601的扭力以及提升电机601驱动的平稳性。
40.作为一种优选方案,如图1所示,其中,所述壳体101内设有保温层7。通过设置保温层7,从而在对摩擦片进行加热时,降低壳体101的散热速率,从而提升壳体101内的升温速率。
41.尽管已经示出和描述了本发明的实施例,对于本领域的普通技术人员而言,可以理解在不脱离本发明的原理和精神的情况下可以对这些实施例进行多种变化、修改、替换和变型,本发明的范围由所附权利要求及其等同物限定。