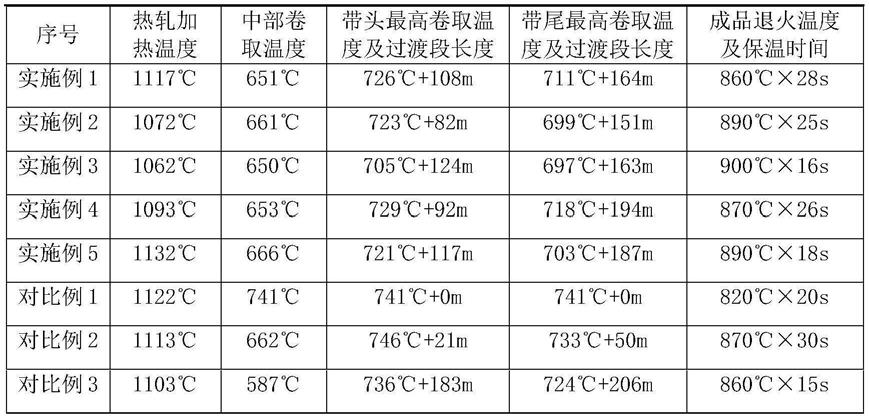
1.本发明属于无取向硅钢技术领域,具体涉及中低牌号无取向硅钢的生产方法,确切地为一种在常规流程下能提升中低牌号无取向硅钢性能均匀性的方法。
背景技术:2.中低牌号无取向硅钢不经过常化工序,在热轧时需要利用高温卷取来提高磁性能。与短流程相比,常规流程在铸坯切割后进入加热炉过程中存在较高的温降,且常规流程加热炉中铸坯一般通过步进梁移动,而短流程通过炉辊运输,导致常规流程中铸坯在加热炉中温度分布不均匀,铸坯上下表面存在温差,且受加热炉烧嘴分布影响,铸坯头尾温度高,中部温度低,夹杂物更容易在头尾固溶。而在轧制过程中,头尾温降快,且卷取后头尾与空气接触导致散热快,保温时间短,造成冷轧前的组织与夹杂物分布不均,表现为头尾夹杂物更多,且头尾以变形组织为主,中部再结晶比例较高,导致热轧板通板的组织及力学性能存在差异,冷轧过程中将表现出轧制力头尾高、中间低的现象,不利于板型及厚度控制,且成品退火后头尾晶粒小,铁损高,中部晶粒大,铁损低,使用连续在线铁损检测设备检测带钢每米的铁损值并绘制成曲线,呈现出铁损头尾高中间低的特点。整卷在线铁损p
1.5/50
极差相差0.3~1.0w/kg,方差大于0.03,rp0.2相差20~40mpa,严重影响成品整体性能,用户使用过程中生产出的铁芯一致性较差。为了降低性能波动的影响,对发给用户的钢卷进行了分卷,损失成材率也降低了生产效率。
3.中国专利公布号为cn 107983784a的文献,公开了一种提高热轧钢板性能均匀性的方法,在采用超快速冷却系统对热轧钢板进行冷却时,控制钢板分段冷却、分段头尾遮蔽,使钢板头尾部与中部温差≤20℃,该工艺主要针对中厚板,由于其卷取温度<600℃,且头尾与中部温差太小,不适用于硅钢的生产。
4.中国专利公布号为cn 107824619a的文献,公开了一种提高带钢性能均匀性的方法,在带钢的同一宽度方向上采用阶梯冷却方式,从距带钢边部120~200mm处开始向边部梯度减少层流水流量,每间隔30~60mm层流水流量递减2~6%,实现在同一宽度上带钢力学性能均匀的方法,适用于低碳钢、超低碳钢、低合金高强钢、双相钢等,该文献针对的是带钢宽度方向上的性能均匀性,未提及提升带钢长度方向上的性能均匀性。由于硅钢较其他钢种更容易氧化,当边部温度较高时,氧化层更厚,不利于后工序酸洗。
5.中国专利公布号为cn 104307891a的文献,公开了一种阶梯式热轧带钢产线层流冷却控制方法,保证薄带钢在层流冷却辊道上稳定运行、防止带钢头部在辊道上翻起、避免钢卷内圈出现折叠和松卷,该文献主要针对对热轧带钢板型进行控制及调整,并未涉及对带钢性能的提升。中国专利公布号为cn 103031419a的文献,公开了一种提高ti微合金化高强机械用钢通卷性能均匀性的方法,申请公布号为cn 102851474a的中国专利,公开了一种提高带钢通卷力学性能均匀性的生产方法,改善了最终产品沿轧制方向的性能均匀性,提高了综合成材率,但其保护的钢种均未涉及硅钢领域。
6.中国专利公布号为cn 102102141a的文献,公开了一种改善取向硅钢板组织均匀
性的热轧工艺,通过改变轧制厚度,降低中间坯头尾的温度差别,提高了热轧工序的生产效率,使头尾温差缩小到17~40℃,该文献对中间坯厚度以及精轧压下率进行了较大的调整,要求出炉温度大于1200℃,对于无取向硅钢而言,该温度下将会出现大量的夹杂物固溶,导致磁性能严重恶化。
7.中国专利公布号为cn 101879529a的中国专利,公开了一种提高无取向硅钢头尾性能的热轧加热方法,通过调整炉内烧嘴,降低靠近钢坯头尾部的加热炉温度,提高头尾性能,该文献仅解决炉内板坯温度均匀性问题,无法解决出炉后板坯头尾的温降带来的影响。同时,该方法要求加热温度1200~1400℃,该温度下将会出现大量的夹杂物固溶,导致磁性能严重恶化。
技术实现要素:8.本发明的目的在于克服现有技术存在的不足,提供一种通过采取不同温度卷取,使单卷在线铁损p
1.5/50
的极差小于0.1w/kg,标准方差小于0.015,且成品退火后整卷性能均一的提升中低牌号无取向硅钢性能均匀性的方法。
9.实现上述目的的技术措施
10.一种提升常规流程中低牌号无取向硅钢性能均匀性的方法,其步骤:
11.1)经转炉冶炼并浇注成坯;冶炼采取洁净钢的方式,使c≤0.0025%,n≤0.0030%,p≤0.030%,s≤0.0050%,ti≤0.0030%且应满足al+si-mn/2≤2.0%;
12.2)对铸坯加热,控制其出炉温度在1046~1142℃;
13.3)经常规粗轧、精轧后层流冷却至卷取温度;精轧采用常规升速轧制;层流冷却采用后段冷却方式;
14.4)进行卷取,并控制带钢中部卷取温度在640~680℃;卷取按照以下方式进行:
15.a、当铸坯出炉温度-1046-mn/s》0时,钢带头部及钢带尾部的卷取温度按照以下公式控制:
16.钢带头部卷取最高温度按照:ct+铸坯出炉温度-1046-mn/s+(s/2+n/3+ti/4)
×
106+20~40℃进行控制;并控制钢带头部卷取最高温度与钢带中部卷取温度即ct之间温差不超过100℃;并在过渡段长度为在80~120m内使卷取温度逐步降低到ct温度;
17.当卷取距离钢带尾部在160~200m时,开始对钢带逐步升温,直至钢带尾部达到其卷取最高温度;钢带尾部卷取最高温度按照:ct+铸坯出炉温度-1046-mn/s+(s/2+n/3+ti/4)
×
106+0~20℃进行控制;
18.b、当铸坯出炉温度-1046-mn/s<0时,钢带头部及钢带尾部的卷取温度按照以下公式控制:
19.钢带头部卷取最高温度按照:ct+(s/2+n/3+ti/4)
×
106+10~30℃进行控制;并控制钢带头部卷取最高温度与钢带中部卷取温度即ct之间温差不超过100℃;并在过渡段长度为80~120m内使卷取温度逐步降低到ct温度;
20.当卷取距离钢带尾部在160~200m时,开始对钢带升温,直至钢带尾部达到其卷取最高温度;钢带尾部卷取最高温度按照:ct+(s/2+n/3+ti/4)
×
106+0~20℃进行控制;
21.上述的ct为带钢中部卷取温度,单位为℃;
22.关于钢带头部及钢带尾部的计算公式中,所涉及到的金属元素的取值均为重量百
分比含量数;
23.5)经酸洗、冷轧至成品厚度后进行成品退火,成品退火温度控制在860~940℃,保温控制在15~30s;硅、铝含量与退火温度及保温时间成正相关关系;
24.6)通过在线连续铁损曲线评估整卷铁损波动情况。
25.优选地:铸坯出炉温度控制在1056~1135℃。
26.优选地:控制带钢中部卷取温度在648~670℃。
27.本发明中主要工艺的作用
28.控制c≤0.0025%主要是为了避免时效,也省去了成品退火机组使用湿气脱碳,减少生产成本。控制n≤0.0030%,p≤0.030%,s≤0.0050%,ti≤0.0030%主要是为了控制钢中的夹杂物,避免因夹杂元素过多影响磁性能。控制al+si-mn/2≤2.0,主要是为了在热轧过程中有两相区轧制,避免出现瓦楞缺陷,同时也可省去连铸过程中的电磁搅拌。
29.本发明之所以控制铸坯出炉温度在1046~1142℃,优选地铸坯出炉温度控制在1056~1135℃,是便于后续轧机减小负荷,顺利轧制,避免过高产生内氧化层,减少不良夹杂物析出。出炉温度与热轧机轧制能力和卷取温度限制有关,如果轧机能力不足或者卷取温度无法满足权利要求,可以适当提高出炉温度,但加热温度最大不应超过1160℃。温度过高会导致夹杂物析出,影响磁性能,且2feo
·
sio2氧化铁皮熔化,热轧时不易脱落,热轧带表面缺陷增多。温度过低则轧制负荷大,铸坯塑性差,轧制板型难以控制。优选的铸坯出炉温度为1056~1135℃。
30.从mns溶解度曲线来看,加热温度越高mns在铸坯中的溶解度越大,扩大mn/s可以在一定程度上减少夹杂物,在本发明规定出炉温度范围内,当铸坯出炉温度-1046-mn/s>0时,mns即会开始溶解,当铸坯出炉温度-1046-mn/s<0,mns在铸坯中的溶解量减少。铸坯中另外的夹杂物主要为n、ti的化合物,此类化合物在本发明出炉温度范围内的溶解度也随着加热温度的升高而增大,在成品退火时,均会阻碍晶粒长大从而影响磁性能。
31.本发明之所以控制带钢中部卷取温度在640~680℃,优选地控制带钢中部卷取温度在648~670℃。是为了提升后工序生产效率,采用酸洗连轧机组进行生产。带钢中部卷取温度如果过高,则将不利于氧化铁皮的控制,所以将卷取温度控制在640~680℃。随着硅、铝含量的增加,带钢中部卷取温度可以适当降低,但也不应低于640℃。控制中部卷取温度大于640℃,主要是为了能够利用卷取后的余热让热轧板进行再结晶,控制带钢中部卷取温度小于680℃,是为了避免引起晶界氧化和内氧化层,降低酸洗难度。因为晶界氧化,晶界处易发生过酸洗而形成坑状表面,冷轧时易形成小裂纹和产生脱皮及铁粉。
32.本发明之所以使卷取按照以下方式进行:
33.a、当铸坯出炉温度-1046-mn/s》0时,钢带头部及钢带尾部的卷取温度按照以下公式控制:
34.钢带头部卷取最高温度按照:ct+铸坯出炉温度-1046-mn/s+(s/2+n/3+ti/4)
×
106+20~40℃进行控制;并控制钢带头部卷取最高温度与钢带中部卷取温度即ct之间温差不超过100℃;并在过渡段长度为80~120m内使卷取温度逐步降低到ct温度;
35.当卷取距离钢带尾部在160~200m时,开始对钢带逐步升温,直至钢带尾部达到其卷取最高温度;钢带尾部卷取最高温度按照:ct+铸坯出炉温度-1046-mn/s+(s/2+n/3+ti/4)
×
106+0~20℃进行控制;
36.b、当铸坯出炉温度-1046-mn/s<0时,钢带头部及钢带尾部的卷取温度按照以下公式控制:
37.钢带头部卷取最高温度按照:ct+(s/2+n/3+ti/4)
×
106+10~30℃进行控制;并控制钢带头部卷取最高温度与钢带中部卷取温度即ct之间温差不超过100℃;并在过渡段长度为80~120m内使卷取温度逐步降低到ct温度;当卷取距离钢带尾部在160~200m时,开始对钢带逐步升温,直至钢带尾部达到其卷取最高温度;钢带尾部卷取最高温度按照:ct+(s/2+n/3+ti/4)
×
106+0~20℃进行控制;控制头尾不同卷取温度,是因为在加热炉中板坯头尾温度高,中部温度低,s、n、ti等夹杂物更容易在头尾固溶,根据杂质成分的含量不同,固溶比例也不同,头尾夹杂物固溶量多,中部夹杂物固溶量少,使得在相同卷取温度下头尾晶粒长大更加困难,造成头尾晶粒细小,中部晶粒大的情况;在卷取后的冷却过程中,钢卷的外圈与内圈和外界接触,钢卷头尾部位的冷却速度大于钢卷中部的冷却速度,造成热轧卷头尾保温时间比中部短,进一步导致钢卷头部和尾部与中部的晶粒大小不一致,中部晶粒尺寸大于头尾。
38.钢带头部由于内圈和卷取机卷筒接触,温降更快,故钢带头部卷取温度比带尾高20℃左右。由于热轧卷性能对冷轧卷具有遗传性,最终导致成品退火的单卷成品磁性能与力学性能存在差异,通过控制不同的卷取温度,让冷却后的热轧板组织均一性更好,使成品磁性能更加稳定。控制温差最大不超过100℃,是为了减少冷却速率不同造成的应力分布不均,避免冷轧时轧制不稳定。
39.即:常规热轧工艺下的钢带头部及钢带尾部夹杂物多且保温时间短,热轧带头与卷筒接触进一步降低了带头的温度,造成热轧卷长度方向上的晶粒尺寸不均:中部晶粒最大,带尾次之,带头晶粒最小。
40.由于热轧卷内圈卷径小,所以过渡段长度仅需80~120m即可,带尾卷径较大,按照单卷卷重25t进行计算,过渡段长度需要160~200m,以达到在冷却至再结晶温度以下时,获得整卷一致的组织。过渡段长度根据卷径和环境温度可以进行适当调整。
41.本发明之所以控制成品退火温度在860~940℃,是根据合金量不同,选取不同的成品退火温度,随着合金量的提高,成品退火温度应当相应提高,降低铁损。为了提高生产效率,保温时间可以控制在30s以内,由于采用了头中尾不同的卷取温度,不需要进一步延长保温时间即可保持晶粒大小基本相当。退火温度低,成品晶粒细小,铁损高;退火温度过高,达到两相区温度时,晶粒大小不均,磁性能不稳定。
42.本发明与现有技术相比,通过采取不同温度卷取,使热轧板的头、尾冷却至常温时两者温差波动很小,即获得的性能一致性较高,使单卷在线铁损p
1.5/50
的极差小于0.1w/kg,标准方差小于0.015,且成品退火后整卷性能均一。
具体实施方式
43.下面对本发明做详细具体的说明:
44.本发明各实施例均按以下步骤生产:
45.一种提升常规流程中低牌号无取向硅钢性能均匀性的方法,其步骤:
46.1)经转炉冶炼并浇注成坯;冶炼采取洁净钢的方式,使c≤0.0025%,n≤0.0030%,p≤0.030%,s≤0.0050%,ti≤0.0030%且应满足al+si-mn/2≤2.0%;
47.2)对铸坯加热,控制其出炉温度在1046~1142℃;
48.3)经常规粗轧、精轧后层流冷却至卷取温度;精轧采用常规升速轧制;层流冷却采用后段冷却方式;
49.4)进行卷取,并控制带钢中部卷取温度在640~680℃;卷取按照以下方式进行:
50.a、当铸坯出炉温度-1046-mn/s》0时,钢带头部及钢带尾部的卷取温度按照以下公式控制:
51.钢带头部卷取最高温度按照:ct+铸坯出炉温度-1046-mn/s+(s/2+n/3+ti/4)
×
106+20~40℃进行控制;并控制钢带头部卷取最高温度与钢带中部卷取温度即ct之间温差不超过100℃;并在过渡段长度为在80~120m内使卷取温度逐步降低到ct温度;
52.当卷取距离钢带尾部在160~200m时,开始对钢带逐步升温,直至钢带尾部达到其卷取最高温度;钢带尾部卷取最高温度按照:ct+铸坯出炉温度-1046-mn/s+(s/2+n/3+ti/4)
×
106+0~20℃进行控制;
53.b、当铸坯出炉温度-1046-mn/s<0时,钢带头部及钢带尾部的卷取温度按照以下公式控制:
54.钢带头部卷取最高温度按照:ct+(s/2+n/3+ti/4)
×
106+10~30℃进行控制;并控制钢带头部卷取最高温度与钢带中部卷取温度即ct之间温差不超过100℃;并在过渡段长度为80~120m内使卷取温度逐步降低到ct温度;
55.当卷取距离钢带尾部在160~200m时,开始对钢带升温,直至钢带尾部达到其卷取最高温度;钢带尾部卷取最高温度按照:ct+(s/2+n/3+ti/4)
×
106+0~20℃进行控制;
56.上述的ct为带钢中部卷取温度,单位为℃;
57.关于钢带头部及钢带尾部的计算公式中,所涉及到的金属元素的取值均为重量百分比含量数;
58.5)经酸洗、冷轧至成品厚度后进行成品退火,成品退火温度控制在860~940℃,保温控制在15~30s;硅、铝含量与退火温度及保温时间成正相关关系;
59.6)通过在线连续铁损曲线评估整卷铁损波动情况。
60.本发明在实验阶段,选取了三种不同合金量中低牌号无取向硅钢进行对比说明,分别对应50w1300、50w800及50w600三种不同牌号。
61.使用p
1.5/50
作为实测铁损测量值(反映试样实际水平),在线铁损使用p
1.5/50
进行检测(工艺变化波动性更加明显)
62.按照成分1实施情况:
63.生产的为50w1300电工钢:
64.成分1的化学组分及wt%含量为:c:0.0025%,si:0.45%,mn:0.20%,als:0.25%,s:0.0038%,n:0.0025%,ti:0.0020%;
65.表1在成分1下的实施例及对比例的工艺取值情况
[0066][0067]
表2在成分1下的实施例及对比例的钢板性能检测结果
[0068][0069]
按照成分2实施情况:
[0070]
生产的为50w800电工钢:
[0071]
成分2的化学组分及wt%含量为:c:0.0022%,si:1.05%,mn:0.22%,als:0.28%,s:0.0035%,n:0.0020%,ti:0.0018%;
[0072]
表3在成分2下的实施例及对比例的工艺取值情况
[0073][0074]
[0075]
表4在成分2下的实施例及对比例的钢板性能检测结果
[0076][0077]
按照成分3实施情况:
[0078]
生产的为50w600电工钢:
[0079]
成分3的化学成分及wt%含量为:c:0.0018%,si:1.45%,mn:0.25%,als:0.30%,s:0.0032%,n:0.0018%,ti:0.0015%;
[0080]
表5在成分3下的实施例及对比例的工艺取值情况
[0081][0082]
表6在成分3下的实施及对比例的钢板性能检测结果
[0083][0084]
从以上实验情况看,采用u型冷却策略之后,按照给定的工艺设计热轧工艺,在线铁损平直度大幅度提升,在满足对应牌号磁性能的同时,单卷在线铁损p
1.5/50
的极差小于0.1w/kg,标准方差小于0.015。
[0085]
以上实施例仅为最佳例举,并非对本发明的保护范围限定。