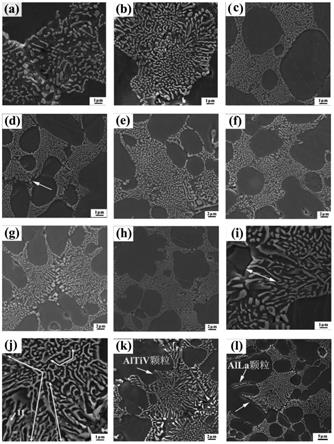
1.本发明涉及金属材料技术领域,具体涉及一种非热处理强化高强高韧压铸铝硅合金及其制备方法。
背景技术:2.在“双碳”目标下,国家对环保要求越来越高,《节能与新能源汽车技术路线图》的发布,新能源汽车轻量化成为高度关注的发展方向。铝合金作为车身常用的金属结构材料,密度小,比强度高,减震效果好,应用到汽车减震塔、汽车后纵梁等部件,其减重优势明显,可实现良好的强度和刚度,耐疲劳性高,集成化设计、一体化压铸成型有利于减少加工过程,可以减少对环境的重复污染,同时铸件结构设计灵活,可满足不同产品需求。
3.新能源汽车车身结构件常用压铸铝合金应用主要以silafont-36合金(专利公开号:us6364970b1)为代表的热处理型高强高韧压铸铝合金材料。该材料采用“高真空压铸+热处理”的使铸件达到屈服强度100-120mpa,抗拉强度180-220mpa,延伸率10-15%。但是对于薄壁压铸件而言,使用该技术存在两个方面的缺点:(1)高真空压铸大幅度增加工艺难度和制造成本;(2)采用热处理工艺铸件会发生一定量的变形和鼓泡,产品的合格率受到影响,成本提高。因此,各国研究机构积极开发非热处理高强高韧压铸铝合金材料,从而适用于大型复杂压铸结构件的批量化生产。特别的,以特斯拉为代表的新能源汽车厂家采用免热处理合金制备大型一体化车身结构件,且已使用的合金主体成分为al7simgmn合金(专利公开号:us20050167012a1)。该合金配合高真空甚至超高真空压铸进行零件的制备,采用该技术路线可缓解原有热处理合金带来的零件变形问题。但仍存在两个主要问题:(1)合金种si含量较低(~7wt.%),可以提高材料的延伸率,达到10-15%。但低si限制了非热处理合金的流动性,对于大型铸件存在填充不足的风险。(2)现有al7simgmn合金强度较低(典型屈服强度110-120mpa,抗拉强度180-220mpa),使大型铸件在结构设计整体壁厚较大且存在较多壁厚区域。因此如能在不改变或者略微降低材料延伸率情况下(保证延伸率》10%,满足车身结构件铆接要求),通过提升合金中si含量提升材料流动性,同时提升材料的强度,对于优化大型车身铸件结构具有重要意义。
4.因此,开发一种非热处理高强高韧压铸铝硅合金,并研究其制备与压铸工艺,以满足汽车行业日益提高的优质高性能铝合金压铸件的实际使用要求,成为压铸领域追求的目标之一。
技术实现要素:5.本发明的目的是在上述现有技术的背景下,提供一种非热处理强化高强高韧压铸铝硅合金及其制备方法。在保证合金具备良好铸造性能的前提下,非热处理态铸件就具有优异的综合力学性能,从而满足车身结构件的性能要求,特别是大型薄壁车身结构件。
6.为了达到这一目的,本发明在长期压铸铝合金研究中发现,压铸铝硅合金中si含量对合金的铸造性能、强度、塑性有着显著的影响。一般情况下,随着si含量的增加,合金的
强度增加,流动性增加,塑性降低。sr元素虽然能够对合金中共晶si起到变质细化作用,但是随着si含量的增加,其塑性仍呈现降低趋势,从而难以达到10%的塑性。本发明主要就是为了解决si含量增加后对压铸条件下对al-si合金塑性降低的问题。随着合金中si含量的增加,组织中共晶si含量增加,共晶si尺寸和形貌也随之改变,并成为影响合金塑性的关键因素。为解决合金中si含量增加造成的材料塑性的降低,本发明创造性的引入v元素,对共晶si相进行细化,从而获得细小的共晶si组织。此外,通过前期大量的实验验证发现稀土元素中la、er、ce等稀土元素可与v元素复合作用,进一步细化合金中的共晶si组织,从而使共晶si尺寸以及形状发生改变。v+re的复合添加使铸态组织中生成了细小的共晶si颗粒,从而确保si含量较多的压铸铝合金材料仍具有较高的塑性。一方面,较高含量的si添加使合金具有优异的强度和流动性。另一方面,v+re的复合添加使共晶si保持细小弥散的状态,从而提高合金的塑性。进而使得本发明在保证优良的铸造性能的前提下,能够极大地提高压铸铝硅合金的机械性能,获得强度与塑形兼顾的高强度、高韧性的综合力学性能。
7.据此,本发明的目的是通过以下技术方案来实现的:
8.本发明提供一种非热处理强化高强高韧压铸铝镁铜合金,所述压铸铝镁铜合金中各组分的重量百分比为si 8.0-10.0%、mg 0.1-0.5、mn 0.5-0.8%、cu 0.05-0.5%、ti 0.05-0.2%、sr 0.01-0.05wt.%、v 0.01-0.1%、re 0.01-0.15%、fe《0.2wt.%;其他杂质总量和≤0.4wt.%,余量为al。
9.作为本发明的一个实施方案,所述re元素包括la、ce、er元素中的一种或几种。
10.本发明还涉及一种非热处理强化高强高韧压铸铝硅合金的制备方法,所述制备方法包括以下步骤:
11.s1、烘干:将备好的原料纯al、纯si、纯mg、al-mn中间合金、al-ti中间合金、al-cu中间合金、al-re中间合金、al-v中间合金预热,进行烘干处理;
12.s2、熔炼:初次升温将纯al熔化后添加al-ti中间合金、al-cu中间合金、al-mn中间合金、al-v中间合金、纯si,待中间合金熔化后降温;将纯mg压入熔体底部熔化,完全熔化后合金熔体第二次升温精炼;再将al-re中间合金压入熔体底部熔化,完全熔化后静置,即得所述非热处理强化高强高韧压铸铝硅合金。
13.作为本发明的一个实施方案,步骤s1中预热的温度为190-210℃。
14.作为本发明的一个实施方案,步骤s2中初次升温的温度为750℃-760℃。
15.作为本发明的一个实施方案,步骤s2中降温的温度为680-700℃。
16.作为本发明的一个实施方案,步骤s2中纯mg、al-re中间合金压入熔体后搅拌3-5分钟至完全熔化。
17.作为本发明的一个实施方案,步骤s2中第二次升温的温度为720-730℃。re为变质元素,在铝合金熔炼过程,变质元素最后添加。
18.作为本发明的一个实施方案,步骤s2中精炼具体为:采用旋转喷吹装置在熔体中通入带有精炼剂粉末的氮气进行喷粉精炼,除渣、除气处理,随后静置10-15分钟,并完成扒渣处理,得到精炼后的熔体。
19.作为本发明的一个实施方案,旋转喷吹装置工艺参数为除气转数:300-350r/min,除气时间:5-10min,除气时气源压力:0.35
±
0.05mpa,气体流量:0.2-0.8sccm。
20.作为本发明的一个实施方案,所采用的精炼剂包括氯化镁、氯化钙中的一种;精炼
5v、纯si合金,待中间合金熔化后降温至690℃,采用钟罩将纯mg压入坩埚底部区域进行熔化,随后搅拌5分钟。随后熔体升温至720℃,在熔体中通入压力为0.4mpa的氮气,带入熔体总重量0.4%的精炼剂粉末,以300r/min、气体流量0.5通气10min除渣除气。随后静置12分钟,并完成扒渣处理,并进行炉前成分分析测试。成分合格后在690℃进行高压铸造。压射速度为3m/s,铸造压力80mpa,脱模剂比例1:100,模具温度230℃。生产过程中使用的模具为压铸试棒模,获得铸件记为a1。
36.实施例2
37.本实施例涉及一种非热处理强化高强韧压铸铝硅合金的各组分重量百分比为:si:8.0wt.%;mg:0.25wt.%;mn:0.6wt.%;ti:0.15wt.%;cu:0.15wt.%;er:0.05wt.%,sr:0.025wt.%,fe:0.12wt.%,其他杂质总量和为0.3wt.%,余量为al。
38.本实施例的一种非热处理强化高强韧压铸铝硅合金的制备及其压铸工艺包括以下步骤:
39.1)烘干:将备好的原料纯铝、纯si、纯mg、al-10mn中间合金、al-10ti中间合金、al-50cu中间合金、al-10er中间合金预热至200℃,进行烘干处理;
40.2)熔炼:炉子升温至755℃将纯铝熔化,随后添加al-10ti、al-50cu、al-10mn、纯si合金,待中间合金熔化后降温至690℃,采用钟罩将纯mg压入坩埚底部区域进行熔化,随后搅拌5分钟。随后熔体升温至720℃,在熔体中通入压力为0.4mpa的氮气,带入熔体总重量0.4%的精炼剂粉末,以300r/min、气体流量0.5通气10min除渣除气。随后静置12分钟,并完成扒渣处理;精炼完成后,采用钟罩将al-10er中间合金压入坩埚底部区域进行熔化,并搅拌5分钟至完全熔化,随后静置12分钟,并进行炉前成分分析测试。成分合格后在690℃进行高压铸造。压射速度为3m/s,铸造压力80mpa,脱模剂比例1:100,模具温度230℃。生产过程中使用的模具为压铸试棒模,获得铸件记为a2。
41.实施例3
42.本实施例涉及一种非热处理强化高强韧压铸铝硅合金的各组分重量百分比为:si:8.0wt.%;mg:0.25wt.%;mn:0.6wt.%;ti:0.15wt.%;cu:0.15wt.%;v:0.02wt.%,er:0.05wt.%,sr:0.025wt.%,fe:0.12wt.%,其他杂质总量和为0.3wt.%,余量为al。
43.本实施例的一种非热处理强化高强韧压铸铝硅合金的制备及其压铸工艺包括以下步骤:
44.1)烘干:将备好的原料纯铝、纯si、纯mg、al-10mn中间合金、al-10ti中间合金、al-50cu中间合金、al-10er中间合金、al-5v中间合金预热至200℃,进行烘干处理;
45.2)熔炼:炉子升温至755℃将纯铝熔化,随后添加al-10ti、al-50cu、al-10mn、al-5v、纯si合金,待中间合金熔化后降温至690℃,采用钟罩将纯mg压入坩埚底部区域进行熔化,随后搅拌5分钟。随后熔体升温至720℃,在熔体中通入压力为0.4mpa的氮气,带入熔体总重量0.4%的精炼剂粉末,以300r/min、气体流量0.5通气10min除渣除气。随后静置12分钟,并完成扒渣处理;精炼完成后,采用钟罩将al-10er中间合金压入坩埚底部区域进行熔化,并搅拌5分钟至完全熔化,随后静置12分钟,并进行炉前成分分析测试。成分合格后在690℃进行高压铸造。压射速度为3m/s,铸造压力80mpa,脱模剂比例1:100,模具温度230℃。生产过程中使用的模具为压铸试棒模,获得铸件记为a3。
46.实施例4
47.本实施例涉及一种非热处理强化高强韧压铸铝硅合金的各组分重量百分比为:si:9.5wt.%;mg:0.25wt.%;mn:0.6wt.%;ti:0.15wt.%;cu:0.15wt.%;v:0.02wt.%,er:0.05wt.%,sr:0.025wt.%,fe:0.12wt.%,其他杂质总量和为0.3wt.%,余量为al。
48.本实施例的一种非热处理强化高强韧压铸铝硅合金的制备及其压铸工艺包括以下步骤:
49.1)烘干:将备好的原料纯铝、纯si、纯mg、al-10mn中间合金、al-10ti中间合金、al-50cu中间合金、al-10er中间合金、al-5v中间合金预热至200℃,进行烘干处理;
50.2)熔炼:炉子升温至755℃将纯铝熔化,随后添加al-10ti、al-50cu、al-10mn、al-5v、纯si合金,待中间合金熔化后降温至690℃,采用钟罩将纯mg压入坩埚底部区域进行熔化,随后搅拌5分钟。随后熔体升温至720℃,在熔体中通入压力为0.4mpa的氮气,带入熔体总重量0.4%的精炼剂粉末,以300r/min、气体流量0.5通气10min除渣除气。随后静置12分钟,并完成扒渣处理;精炼完成后,采用钟罩将al-10er中间合金压入坩埚底部区域进行熔化,并搅拌5分钟至完全熔化,随后静置12分钟,并进行炉前成分分析测试。成分合格后在690℃进行高压铸造。压射速度为3m/s,铸造压力80mpa,脱模剂比例1:100,模具温度230℃。生产过程中使用的模具为压铸试棒模,获得铸件记为a4。
51.实施例5
52.本实施例涉及一种非热处理强化高强韧压铸铝硅合金的各组分重量百分比为:si:9.5wt.%;mg:0.25wt.%;mn:0.6wt.%;ti:0.15wt.%;cu:0.15wt.%;v:0.02wt.%,la:0.05wt.%,sr:0.025wt.%,fe:0.12wt.%,其他杂质总量和为0.3wt.%,余量为al。
53.本实施例的一种非热处理强化高强韧压铸铝硅合金的制备及其压铸工艺包括以下步骤:
54.1)烘干:将备好的原料纯铝、纯si、纯mg、al-10mn中间合金、al-10ti中间合金、al-50cu中间合金、al-10la中间合金、al-5v中间合金预热至200℃,进行烘干处理;
55.2)熔炼:炉子升温至720℃将纯铝熔化,随后升温至755℃添加al-10ti、al-50cu、al-10mn、al-5v、纯si合金,待中间合金熔化后降温至690℃,采用钟罩将纯mg压入坩埚底部区域进行熔化,随后搅拌5分钟。随后熔体升温至720℃,在熔体中通入压力为0.4mpa的氮气,带入熔体总重量0.4%的精炼剂粉末,以300r/min、气体流量0.5通气10min除渣除气。随后静置12分钟,并完成扒渣处理;精炼完成后,采用钟罩将al-10la中间合金压入坩埚底部区域进行熔化,并搅拌5分钟至完全熔化,随后静置12分钟,并进行炉前成分分析测试。成分合格后在690℃进行高压铸造。压射速度为3m/s,铸造压力80mpa,脱模剂比例1:100,模具温度230℃。生产过程中使用的模具为压铸试棒模,获得铸件记为a5。
56.实施例6
57.本实施例涉及一种非热处理强化高强韧压铸铝硅合金的各组分重量百分比为:si:9.5wt.%;mg:0.25wt.%;mn:0.6wt.%;ti:0.15wt.%;cu:0.15wt.%;v:0.02wt.%,ce:0.05wt.%,sr:0.025wt.%,fe:0.12wt.%,其他杂质总量为0.3wt.%,余量为al。
58.本实施例的一种非热处理强化高强韧压铸铝硅合金的制备及其压铸工艺包括以下步骤:
59.1)烘干:将备好的原料纯铝、纯si、纯mg、al-10mn中间合金、al-10ti中间合金、al-50cu中间合金、al-10ce中间合金、al-5v中间合金预热至200℃,进行烘干处理;
60.2)熔炼:炉子升温至720℃将纯铝熔化,随后升温至755℃添加al-10ti、al-50cu、al-10mn、al-5v、纯si合金,待中间合金熔化后降温至690℃,采用钟罩将纯mg压入坩埚底部区域进行熔化,随后搅拌5分钟。随后熔体升温至720℃,在熔体中通入压力为0.4mpa的氮气,带入熔体总重量0.4%的精炼剂粉末,以300r/min、气体流量0.5通气10min除渣除气。随后静置12分钟,并完成扒渣处理;精炼完成后,采用钟罩将al-10ce中间合金压入坩埚底部区域进行熔化,并搅拌5分钟至完全熔化,随后静置12分钟,并进行炉前成分分析测试。成分合格后在690℃进行高压铸造。压射速度为3m/s,铸造压力80mpa,脱模剂比例1:100,模具温度230℃。生产过程中使用的模具为压铸试棒模,获得铸件记为a6。
61.实施例7
62.本实施例涉及一种非热处理强化高强韧压铸铝硅合金的各组分重量百分比为:si:10wt.%;mg:0.5wt.%;mn:0.8wt.%;ti:0.2wt.%;cu:0.5wt.%;v:0.1wt.%,la:0.15wt.%,sr:0.05,fe:0.12,其他杂质总量为0.3wt.%,余量为al。
63.本实施例的一种非热处理强化高强韧压铸铝硅合金的制备及其压铸工艺包括以下步骤:
64.1)烘干:将备好的原料纯铝、纯si、纯mg、al-10mn中间合金、al-10ti中间合金、al-50cu中间合金、al-10la中间合金、al-5v中间合金预热至200℃,进行烘干处理;
65.2)熔炼:炉子升温至755℃将纯铝熔化,随后添加al-10ti、al-50cu、al-10mn、al-5v、纯si合金,待中间合金熔化后降温至690℃,采用钟罩将纯mg压入坩埚底部区域进行熔化,随后搅拌5分钟。随后熔体升温至720℃,在熔体中通入压力为0.4mpa的氮气,带入熔体总重量0.4%的精炼剂粉末,以300r/min、气体流量0.5通气10min除渣除气。随后静置12分钟,并完成扒渣处理;精炼完成后,采用钟罩将al-10la中间合金压入坩埚底部区域进行熔化,并搅拌5分钟至完全熔化,随后静置12分钟,并进行炉前成分分析测试。成分合格后在690℃进行高压铸造。压射速度为3m/s,铸造压力80mpa,脱模剂比例1:100,模具温度230℃。生产过程中使用的模具为压铸试棒模,获得铸件记为a7。
66.实施例8
67.本实施例涉及一种非热处理强化高强韧压铸铝硅合金的各组分重量百分比为:si:8wt.%;mg:0.1wt.%;mn:0.5wt.%;ti:0.05wt.%;cu:0:05wt.%;v:0.01wt.%,la:0.01wt.%,sr:0.01,fe:0.12,其他杂质总量为0.3wt.%,余量为al。
68.本实施例的一种非热处理强化高强韧压铸铝硅合金的制备及其压铸工艺包括以下步骤:
69.1)烘干:将备好的原料纯铝、纯si、纯mg、al-10mn中间合金、al-10ti中间合金、al-50cu中间合金、al-10la中间合金、al-5v中间合金预热至200℃,进行烘干处理;
70.2)熔炼:炉子升温至755℃将纯铝熔化,随后添加al-10ti、al-50cu、al-10mn、al-5v、纯si合金,待中间合金熔化后降温至690℃,采用钟罩将纯mg压入坩埚底部区域进行熔化,随后搅拌5分钟。随后熔体升温至720℃,在熔体中通入压力为0.4mpa的氮气,带入熔体总重量0.4%的精炼剂粉末,以300r/min、气体流量0.5通气10min除渣除气。随后静置12分钟,并完成扒渣处理;精炼完成后,采用钟罩将al-10la中间合金压入坩埚底部区域进行熔化,并搅拌5分钟至完全熔化,随后静置12分钟,并进行炉前成分分析测试。成分合格后在690℃进行高压铸造。压射速度为3m/s,铸造压力80mpa,脱模剂比例1:100,模具温度230℃。
生产过程中使用的模具为压铸试棒模,获得铸件记为a8。
71.对比例1
72.本对比例涉及一种非热处理强化高强韧压铸铝硅合金的各组分重量百分比为:si:8.0wt.%;mg:0.25wt.%;mn:0.6wt.%;ti:0.15wt.%;cu:0.15wt.%,sr:0.025wt.%,fe:0.12wt.%,其他杂质总量和为0.3wt.%,余量为al。
73.本对比例的一种非热处理强化高强韧压铸铝硅合金的制备及其压铸工艺包括以下步骤:
74.1)烘干:将备好的原料纯铝、纯si、纯mg、al-10mn中间合金、al-10ti中间合金、al-50cu中间合金预热至200℃,进行烘干处理;
75.2)熔炼:炉子升温至755℃将纯铝熔化,随后添加al-10ti、al-50cu、al-10mn、纯si合金,待中间合金熔化后降温至690℃,采用钟罩将纯mg压入坩埚底部区域进行熔化,随后搅拌5分钟。随后熔体升温至720℃,在熔体中通入压力为0.4mpa的氮气,带入熔体总重量0.4%的精炼剂粉末,以300r/min、气体流量0.5,通气10min除渣除气。随后静置12分钟,并完成扒渣处理,并进行炉前成分分析测试。成分合格后在690℃进行高压铸造。压铸工艺参数与压铸使用模具与实施例1中相同,获得铸件a9。
76.对比例2
77.本对比例涉及一种非热处理强化高强韧压铸铝硅合金的各组分重量百分比为:si:9.5wt.%;mg:0.25wt.%;mn:0.6wt.%;ti:0.15wt.%;cu:0.15wt.%,sr:0.025wt.%,fe:0.12wt.%,其他杂质总量和为0.3wt.%,余量为al。
78.本对比例的一种非热处理强化高强韧压铸铝硅合金的制备及其压铸工艺包括以下步骤:
79.1)烘干:将备好的原料纯铝、纯si、纯mg、al-10mn中间合金、al-10ti中间合金、al-50cu中间合金预热至200℃,进行烘干处理;
80.2)熔炼:炉子升温至755℃将纯铝熔化,随后添加al-10ti、al-50cu、al-10mn、纯si合金,待中间合金熔化后降温至690℃,采用钟罩将纯mg压入坩埚底部区域进行熔化,随后搅拌5分钟。随后熔体升温至720℃,在熔体中通入压力为0.4mpa的氮气,带入熔体总重量0.4%的精炼剂粉末,以300r/min、气体流量0.5通气10min除渣除气。随后静置12分钟,并完成扒渣处理,并进行炉前成分分析测试。成分合格后在690℃进行高压铸造。压铸工艺参数与压铸使用模具与实施例1中相同,获得铸件a10。
81.对比例3
82.本实施例涉及一种非热处理强化高强韧压铸铝硅合金的各组分重量百分比为:si:9.5wt.%;mg:0.25wt.%;mn:0.6wt.%;ti:0.15wt.%;cu:0.15wt.%;v:0.15wt.%,la:0.05wt.%,sr:0.025wt.%,fe:0.12wt.%,其他杂质总量和为0.3wt.%,余量为al。
83.本实施例的一种非热处理强化高强韧压铸铝硅合金的制备及其压铸工艺包括以下步骤:
84.1)烘干:将备好的原料纯铝、纯si、纯mg、al-10mn中间合金、al-10ti中间合金、al-50cu中间合金、al-10la中间合金、al-5v中间合金预热至200℃,进行烘干处理;
85.2)熔炼:炉子升温至755℃将纯铝熔化,随后添加al-10ti、al-50cu、al-10mn、al-5v、纯si合金,待中间合金熔化后降温至690℃,采用钟罩将纯mg压入坩埚底部区域进行熔
化,随后搅拌5分钟。随后熔体升温至720℃,在熔体中通入压力为0.4mpa的氮气,带入熔体总重量0.4%的精炼剂粉末,以300r/min、气体流量0.5通气10min除渣除气。随后静置12分钟,并完成扒渣处理;精炼完成后,采用钟罩将al-10la中间合金压入坩埚底部区域进行熔化,并搅拌5分钟至完全熔化,随后静置12分钟,并进行炉前成分分析测试。成分合格后在690℃进行高压铸造。压铸工艺参数与压铸使用模具与实施例1中相同,获得铸件a11。
86.对比例4
87.本对比例涉及一种非热处理强化高强韧压铸铝硅合金的各组分重量百分比为:si:9.5wt.%;mg:0.25wt.%;mn:0.6wt.%;ti:0.15wt.%;cu:0.15wt.%,v:0.02wt.%,la:0.2wt.%,sr:0.025,fe:0.12,其他杂质总量和为0.3wt.%,余量为al。
88.本对比例的一种非热处理强化高强韧压铸铝硅合金的制备及其压铸工艺包括以下步骤:
89.1)烘干:将备好的原料纯铝、纯si、纯mg、al-10mn中间合金、al-10ti中间合金、al-50cu中间合金、al-10la中间合金、al-5v预热至200℃,进行烘干处理;
90.2)熔炼:炉子升温至755℃将纯铝熔化,随后添加al-10ti、al-50cu、al-10mn、al-5v、纯si合金,待中间合金熔化后降温至690℃,采用钟罩将纯mg压入坩埚底部区域进行熔化,随后搅拌5分钟。随后熔体升温至720℃,在熔体中通入压力为0.4mpa的氮气,带入熔体总重量0.4%的精炼剂粉末,以300r/min、气体流量0.5通气10min除渣除气。随后静置12分钟,并完成扒渣处理;精炼完成后,采用钟罩将al-10la中间合金压入坩埚底部区域进行熔化,并搅拌5分钟至完全熔化,随后静置12分钟,并进行炉前成分分析测试。成分合格后在690℃进行高压铸造。压铸工艺参数与压铸使用模具与实施例1中相同,获得铸件a12。
91.将上述实施例1、2、3、4、5、6、7、8与对比例1、2、3、4分别制备的铸件a1、a2、a3、a4、a5、a6、a7、a8、9、a10、a11、a12进行力学性能测试,测试结果如表1所示。对比a1、a2、a3、a9铸件的力学性能可以发现,单独添加v元素或者稀土er元素,合金的强度和延伸率明显提高,抗拉强度最高提升27mpa,延伸率提升幅度达24.1%。而同时添加v和er元素对合金的塑性提升更为明显,铸件延伸率由8.7%(a9)显著提升至14.9%(a3),增幅为71.2%。对比a4、a10铸件力学性能同样可以发现以上规律,复合添加v和er元素可使高si含量(9.5wt.%)的压铸铝合金的塑性显著提高,从而由延伸率6.5(a10铸件)达到12.9%(a4铸件),满足合金高强高韧的特性。对比a4、a5、a6、a10铸件力学性能发现,复合添加v与er、la、ce稀土元素均可使压铸铝合金的塑性和抗拉强度显著提高。其中a4-a6铸件的抗拉强度~281mpa,延伸率~12.8%,较a10铸件的抗拉强度和延伸率分别提高了16.5%和97%。这样也说明了本专利中包含的三种re稀土对合金均有显著的作用。对比a5、a7、a8、a11、a12铸件力学性能可知,在本专利合金成分范围内,通过复合添加v与稀土元素均可使压铸铝合金的屈服强度大于120mpa,抗拉强度大于260mpa,延伸率大于10%(a5、a7、a8铸件),体现了本专利成分范围内合金优异的力学性能。而当合金中v达到0.15(铸件a11)或者稀土元素达到0.2(铸件a12)超出专利范围后,合金的延伸率与抗拉强度显著降低,特别是延伸率降低至8%以下,无法获得高强高韧压铸铝合金材料。综上,本发明中涉及到的合金成分范围中,通过添加v元素以及re元素(la、er、ce)使压铸al-si合金在非热处理状态下具有高强高韧的特点。
92.表1.a1-a12铸件拉伸力学性能
93.组别主要成分屈服强度/mpa抗拉强度/mpa延伸率/%
a1al8si0.02v12126510.5a2al8si0.05er12527910.8a3al8si0.02v0.05er12928114.9a4al9.5si0.02v0.05er13528312.9a5al9.5si0.02v0.05la13128212.7a6al9.5si0.02v0.05ce13628113.0a7al10si0.1v0.15la15531510.5a8al8si0.01v0.01la12326713.2a9al8si1212528.7a10al9.5si1362416.5a11al9.5si0.15v0.05la1342517.9a12al9.5si0.02v0.2la1452657.5
94.将上述实施例1-8与对比例1-4分别制备的铸件a1、a2、a3、a4、a5、a6、a7、a8、a9、a10、a11、a12进行微观组织观察,微观组织如图1所示a1(a)、a2(b)、a3(c)、a9(i)组织对比发现,随着v和稀土元素er的引入,共晶si组织得到了明显的细化。当合金中不含v和er时,铸件组织中共晶si如图1(i)中呈现层片状结构,颗粒尺寸约4μm。而随着v或者er元素的引入,共晶si组织由呈片状向颗粒状转变,且颗粒尺寸显著降低至1μm,如图1(a)和(b)所示。而随着v和er的复合添加,组织中共晶si的尺寸进一步降低,且共晶si呈现更为细小的蠕虫状组织,如图1(c)。组织特征的变化与机械性能的变化密切相关,显然,通过引入v和er元素可显著细化共晶si组织,并改变其形貌,使合金的性能发生显著的变化。通过a4与a10组织对比可以发现,v和er元素的复合作用对高si含量的合金组织同样有效。当si含量为9.5wt.%,且合金中不添加v和er元素时,组织中共晶si组织呈现粗大的折线状,折线状组织尺寸最大可达到10μm(如图1(j))。而随着合金中引入v和er元素,合金中共晶si组织显著细化为蠕虫状(图1(d)所示),但局部存在方块状共晶si组织,对合金塑性有一定影响。因此,a3合金塑性优于a4合金塑性。对比a4、a5、a6、a7、a8、a10铸件组织发现,在本专利合金范围内,通过复合添加v与er、la、ce稀土元素均可使压铸铝合金中的粗大折线状组织消失,从而保证合金的性能。对比a5、a11、a12铸件组织可知,过多的v元素添加可使合金组织中出现alv第二相,过多的稀土元素添加使合金中出现alla第二相,而这些第二相会造成合金塑性极大的降低。总的来说,本专利合金中引入v和re元素的复合作用,使组织中共晶si颗粒更加细小弥散,形貌也获得极大改善,正是这一组织特征使合金具有优异的力学性能。
95.以上所述仅为本发明的实施例,并非限制本发明的专利范围,凡是利用本发明说明书所做的等效结构或等效流程变换,或直接或间接运用在其他相关的技术领域,均同理包括在本发明的专利保护范围之内。