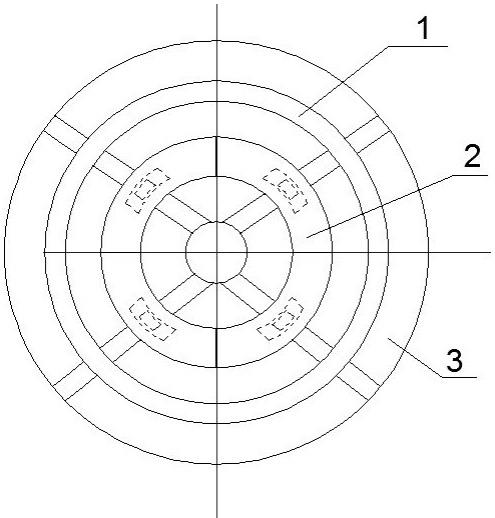
1.本发明涉及渗碳轴承套圈淬火处理后可控抗变形方法,属于热处理技术领域。
背景技术:2.渗碳轴承套圈在热处理过程中,存在几个难以解决的工艺技术问题,一个是加热后在淬火后的变形问题,第二是变形量超过渗碳厚度,在后续加工过程中,产生渗碳层被磨削掉,造成套圈磨削表面有软点。轻者降低轴承使用寿命,严重的会造成轴承使用磨损事故,给钢厂带来严重损失。
3.目前,采用的方式是将经过渗碳处理后的轴承套圈,放到加热炉中加热到830度,停止加热,并在加热炉中冷却至280度;这种在加热炉中冷却至280度再放上轴承套圈,让轴承套圈进行收缩,这种方式冷却时间较长,效率较低,操作复杂。
技术实现要素:4.鉴于上述所述的技术问题,本发明的目的是提供了轴承套圈淬火后可控变形方法,该控制方法采用与现有技术不同的处理方式并利用相应模具对轴承套圈采用内径进行装夹,解决现有技术的处理方式存在的轴承套圈局部淬火缺陷的问题,并且淬火后轴承套圈圆度好,防止因变形造成批次性报废,提高工效和产品质量。
5.为了实现上述目的,本发明所采用的技术方案是:轴承套圈淬火后可控变形方法,设计一套淬火胎具,该淬火胎具对轴承套圈的内径全弧度接触,在线自动按收缩量调节;具体的工艺步骤如下:(1)将经过渗碳处理后的轴承套圈,轴承套圈温度为室温,放到加热炉中加热到830度;(2)将轴承套圈从加热炉中取出,将轴承套圈放入淬火胎具中,然后将承载轴承套圈的淬火胎具置于淬火油中进行油淬处理;(3)淬火工序结束后,待轴承套圈温度冷却至淬火结束温度时,将轴承套圈从淬火胎具中取下。
6.上述轴承套圈的油淬的起始温度为830度,即,轴承套圈从830度时开始降温进行收缩;所述淬火胎具在与轴承套圈放入油淬时,淬火胎具的外径与轴承套圈的内径设置间隙,间隙量可进行调节,使淬火胎具与轴承套圈不接触,保证轴承套圈内径实现完全淬火,不会在轴承套圈内径上出现软点;轴承套圈油淬起始时,淬火胎具呈收缩状态放置,然后把轴承套圈放在淬火胎具外部,轴承套圈随油温下降而进行收缩;等待3-5min后,此时轴承套圈内径硬度形成,已经达到加工要求;然后调整淬火胎具进行外撑,至到淬火胎具的外径与轴承套圈的内径接触;后续,通过控制淬火胎具的自动调节收缩变形量,直至收缩到正常工艺磨削尺寸,最终限制轴承套圈的持续收缩,使多余的变形量向外径膨胀,外径是非工作表面,从而保证了轴承套
圈内径工作表面的圆度和均匀淬火硬度;进一步的,所述的淬火胎具是通过设置于无心卡盘上,淬火胎具通过无心卡盘的作用与轴承套圈进行自动调心。
7.上述控制方法所使用的淬火胎具采用收缩调整结构,包括:胎具本体和无心卡盘,所述胎具本体包括至少2个弧形卡爪,2个弧形卡爪组合构成一个整体组合单元,两个弧形卡爪活动连接于无心卡盘上端面;进一步的,所述的胎具本体的弧形卡爪的数量设置为3-4瓣弧形卡爪结构;优选的,所述的胎具本体设置为4瓣弧形卡爪,4瓣弧形卡爪底部分别对应设置滑块,4瓣弧形卡爪通过各自的滑块与设置在无心卡盘上的滑道进行配合,4瓣弧形卡爪能够通过无心卡盘进行自动调心,使4瓣弧形卡爪在无心卡盘上进行同步收缩或撑开,保证胎具本体与轴承套圈同心;本发明的所述的淬火胎具的多个弧形卡爪作用是在轴承套圈内径硬度形成后抑制轴承套圈的收缩;进一步的,所述的4瓣弧形卡爪的规格相同;无心卡盘上滑道的数量及角度通过弧形卡爪的数量及角度所需而设置。
8.进一步的,所述的无心卡盘为电磁无心卡盘;轴承套圈随着淬火的逐渐收缩,淬火胎具的外径全弧面装夹轴承套圈的内径;使淬火胎具的全弧面外径与轴承套圈内径接触;待轴承套圈温度冷却至淬火结束温度时,胎具本体收缩,移除淬火胎具,有效的控制轴承套圈完全淬火后的全收缩过程的变形。
9.本发明的关键点是在线控制轴承套圈收缩率,是控制淬火后的全收缩过程,淬火过程的淬火胎具与轴承套圈实现无接触,保证轴承套圈内径全淬火到,实现均匀淬火;本发明所采用轴承套圈淬火后可控变形方法与现有技术相比,加热后的轴承套圈(温度为830℃)放入所述发明胎具中,调整好胎具外圆弧与轴承套圈内径的接触间隙,不能存在高温套圈与低温胎具相接触的问题,再将胎具与套圈同时放入淬火油中进行淬火,待轴承套圈温度冷却至淬火结束温度时,从淬火油中将承载套圈的胎具取出;淬火模具的外径全弧面装夹轴承套圈的内径;使淬火模具的全弧面外径与轴承套圈内径接触。接触间隙可以调节,接触中心可以自动调节;待轴承套圈的温度降至室温后,调节淬火模具全弧面大小,顺利将轴承套圈上取下,此时轴承套圈淬火完成,解决现有技术的处理方式存在的轴承套圈为了保证不变形而出现局部淬火缺陷的问题,并且淬火后轴承套圈圆度好,防止因变形造成批次性报废,提高工效和产品质量。
附图说明
10.图1为本发明淬火胎具与轴承套圈装配过程中胎具本体呈收缩状态(保证轴承套圈内径完全淬火)的结构图。
11.图2为本发明淬火胎具与轴承套圈装配过程中胎具本体撑开状态结构图。
12.图中,1、轴承套圈、2、胎具本体、3、无心卡盘。
具体实施方式
13.下面结合附图及实施例对本发明进行进一步说明。显然,所描述的实施例仅仅是本发明一部分实施例,而不是全部的实施例。
14.本实施例以轴承外圈为例,其淬火处理后可控变形方法,设计一套淬火胎具,该淬火胎具对轴承套圈1的内径全弧度接触,在线自动按收缩量调节;具体的工艺步骤如下:(1)将经过渗碳处理后的轴承套圈1,轴承套圈1温度为室温,放到加热炉中加热到830度;(2)将轴承套圈1从加热炉中取出,将轴承套圈1放入淬火胎具中,然后将承载轴承套1圈的淬火胎具置于淬火油中进行油淬处理;(3)淬火工序结束后,待轴承套圈1温度冷却至淬火结束温度时,将轴承套圈1从淬火胎具中取下。
15.上述轴承套圈1的油淬的起始温度为830度,即,轴承套圈1从830度时开始降温进行收缩;所述淬火胎具在与轴承套圈1放入油淬时,淬火胎具的外径与轴承套圈1的内径设置间隙,间隙量可进行调节,使淬火胎具与轴承套圈1不接触,保证轴承套圈1内径实现完全淬火,不会在轴承套圈1内径上出现软点;轴承套圈1油淬起始时,淬火胎具呈收缩状态放置,然后把轴承套圈1放在淬火胎具外部,轴承套圈1随油温下降而进行收缩;等待3-5min后,此时轴承套圈1内径硬度形成,已经达到加工要求;然后调整淬火胎具进行外撑,至到淬火胎具的外径与轴承套圈1的内径接触;后续,通过控制淬火胎具的自动调节收缩变形量,直至收缩到正常工艺磨削尺寸,最终限制轴承套圈的持续收缩,使多余的变形量向外径膨胀,外径是非工作表面,从而保证了轴承套圈内径工作表面的圆度和均匀淬火硬度;进一步的,所述的淬火胎具是通过设置于无心卡盘3上,淬火胎具通过无心卡盘3的作用与轴承套圈1进行自动调心。
16.上述控制方法所使用的淬火胎具采用收缩调整结构,包括:胎具本体2和无心卡盘3,所述胎具本体2包括至少2个弧形卡爪,2个弧形卡爪组合构成一个整体组合单元,两个弧形卡爪活动连接于无心卡盘上3端面;进一步的,所述的胎具本体2的弧形卡爪的数量设置为3-4瓣弧形卡爪结构;优选的,所述的胎具本体2设置为4瓣弧形卡爪,4瓣弧形卡爪底部分别对应设置滑块,4瓣弧形卡爪通过各自的滑块与设置在无心卡盘3上的滑道进行配合,4瓣弧形卡爪能够通过无心卡盘3进行自动调心,使4瓣弧形卡爪在无心卡盘3上进行同步收缩或撑开,保证胎具本体2与轴承套圈1同心;轴承套圈1随着淬火的逐渐收缩,淬火胎具的外径全弧面装夹轴承套圈1的内径;使淬火胎具的全弧面外径与轴承套圈1内径接触;待轴承套圈1温度冷却至淬火结束温度时,胎具本体2收缩,移除淬火胎具,有效的控制轴承套圈完全淬火后的全收缩过程的变形。
17.本发明的关键点是在线控制轴承套圈1收缩率,是控制淬火后的全收缩过程,淬火过程的淬火胎具与轴承套圈1实现无接触,保证轴承套圈1内径全淬火到,实现均匀淬火。
18.以上所述,仅为本发明较佳的具体实施方式,但本发明的保护范围并不局限于此,任何熟悉本技术领域的技术人员在本发明揭露的技术范围内,根据本发明的技术方案及其发明构思加以等同替换或改变,都应涵盖在本发明的保护范围之内。