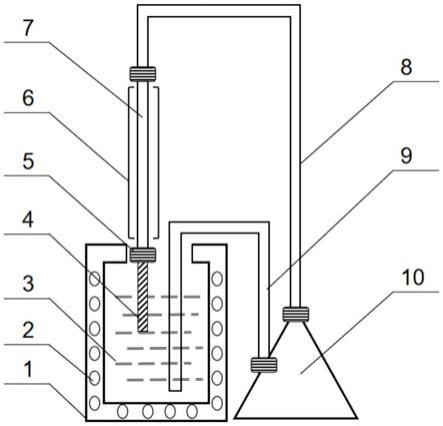
1.本发明属于管构件内表面强化领域,具体的涉及一种内表面梯度强化钢管制备装置及应用方法。
背景技术:2.钢管在日常使用中,一般需要通过内表面强化处理以满足实际工况的需求,而对于渗氮工艺,不论是传统的气体渗氮和盐浴渗氮,还是等离子体渗氮实现管内表面强化的方法如twi260954b,三类方式目前基本为将整个钢管置入化学热处理设备中,最终钢管内外基本呈现相同的强化状态。
3.同时,现行的盐浴渗氮工艺方法如cn113088868a和cn111979512a等,获得的都是整体性能均匀地强化层,在普通服役工况中,可以满足实际需求,但在部分要求两端具备不同性能特点的服役工况中,会出现一端无法较好的满足服役要求提前损坏,进而影响整管的服役寿命。
4.综上,目前尚无一种兼具性能和成本优势的,仅处理内表面且可以满足钢管两端不同性能需求的钢管制备设备及方法,现有钢管渗氮设备及方法具有下述问题:
5.(1)整体相对均匀,无法实现钢管内表面轴径向性能梯度变化;
6.(2)无法实现管内表面渗氮的同时保持外表面清洁无影响;
7.(3)大长径比钢管需要极深长的盐浴炉,造成熔盐材料和能源的浪费。
技术实现要素:8.针对上述现有技术的缺点和不足,本发明提供了一种内表面梯度强化钢管制备装置及应用方法。
9.一种内表面梯度强化钢管制备装置,包含熔盐池、前连接管、钢管、连接管、高温熔盐泵、回液管,所有构件依次连接,钢管垂直于熔盐池中熔盐水平面。
10.优选的,熔盐池的池壁具有加热系统,用于加热融化盐浴渗氮用盐,并保证熔盐处于相对稳定的温度。加热系统包含加热管、智能温控器和热电偶,可实时测量反馈熔盐温度,并根据设定温度调整加热管运行状态,保持熔盐温度稳定可控。
11.优选的,为了防止高温熔盐对接口具有高温腐蚀,造成熔盐泄露,连接管与钢管之间、连接管与高温熔盐泵之间和高温熔盐泵与回液管之间均采用耐高温密封装置密封。
12.进一步优选的,所述金属密封装置可根据钢管外形及材料等性能选择密封式金属管接头、金属面密封件(可参考skf金属面密封件hddf)、弹簧增强型金属o圈、环形密封金属垫片及紧压配件、金属套管等中的任意一种,或使用氟胶圈配合冷却系统,有效防止熔盐在连接处漏出。
13.优选的,为保证渗氮进程的实现,熔盐池中具有熔盐,熔盐熔融后产生氰酸根离子,为盐浴渗氮提供活性离子。
14.优选的,所述熔盐池和钢管之间有前连接管,前连接管伸入熔盐中,保护钢管外表
面不受熔盐影响,同时保证渗氮过程中熔盐水平面下降仍能进行熔盐循环,防止在多根钢管同时使用一个熔盐池时产生的熔盐水平面下降造成钢管下端无法吸取熔盐,进一步的,采用前连接管可以实现不同长度的钢管同时强化处理。
15.优选的,所述连接管、高温熔盐泵之间有多合一耐高温转接头,实现一个高温熔盐泵同时带动多根钢管同时强化处理。
16.优选的,钢管外围有控温装置,弥补空气冷却的温度梯度及温降速率的不足/过度。
17.进一步优选的,控温装置由2个及以上独立控温器组成,相邻独立控温器之间有隔热层,实现温度梯度的精确控制。
18.进一步优选的,所述控温装置为强制冷却装置,提供工艺所需要的温降梯度;强制冷却装置可以及时带走钢管表面热量,使熔盐从钢管一端流动到另一端的过程中缓慢产生温度下降,并根据工艺需要,灵活可控地调整钢管两端的温降幅度。
19.进一步优选的,所述的强制冷却装置可根据所需要的冷却速率选择不同的装置,如环绕式强制风冷装置、环绕式液冷装置、环绕式铝散热板乃至液氮冷阱等。
20.进一步优选的,所述控温装置为加热装置,使钢管不同区域保持不同的温度。对于较长的钢管或不希望钢管两端熔盐温降过大的情况,可采用加热装置对钢管外表面进行加热,降低钢管外部环境与熔盐的温差,从而减少热量损失,达到减小温降的目的。加热装置可根据实际工况的需要选择电阻丝加热器、暖风机、陶瓷加热器、红外线石英加热器、高反射膜保温加热器等中的任一或组合。
21.进一步优选的,所述加热装置为多个加热器组成,每个加热器单独控温,每个加热器相互之间有隔热层,使得钢管外围呈现梯度加热,可以使得温降控制更加灵活,同时,必要时也可通过梯度加热实现整管均匀强化。
22.同时,本发明提供上述装置的应用方法,包含如下步骤:
23.s1:钢管前处理;
24.s2:熔盐池、前连接管、钢管、连接管、高温熔盐泵、回液管依次连接,回液管一端置入熔盐池中;
25.s3:确认各部分密封良好,启动高温熔盐泵,设定高温熔盐泵流量,使熔盐由钢管下端经由钢管内表面、连接管内部、高温熔盐泵、回液管内部后返回熔盐池中,开始渗氮;
26.s4:渗氮完成后对渗氮后钢管进行后处理;
27.经过s1~s4后的钢管内表面强化层在轴径向均具有梯度特征。
28.优选的,钢管前使用前连接管,多钢管同时渗氮时使用钢管通过连接管之间加入多合一耐高温转接头。
29.优选的,所述前处理包括水洗、酸洗、除油、活化、干燥、喷砂、预氧化、催化层涂覆中的任意一种或几种的组合。
30.可根据钢管表面状态、组织、成分等参数灵活选择不同的前处理组合,如对于电化学抛光后的钢管可以免除酸洗、除油等步骤;对于渗氮难度较大的材料则可以适度增加10~30分钟的预氧化或1~3μm的催化层涂覆。
31.优选的,进一步优选的,所述后处理包含清洗、干燥、喷丸、喷砂、氧化中的一种或几种的组合,可根据钢管整体工艺要求灵活选取后处理工艺。如只进行水清洗干燥的方式;
若渗氮时间较长,希望去除渗氮表面疏松层,则可进行喷丸后清洗干燥。
32.优选的,无前连接管应用时,熔盐池中熔盐水平面没过钢管下端不小于10mm。
33.本发明技术关键点:
34.本技术实施例中提供的一个或多个技术方案,至少具有如下技术效果或优点:
35.(1)由于本发明的流动渗氮工艺设计,可实现轴、径向双梯度的设计,在保证了满足钢管内表面两端不同性能区别(一端具有高硬度和高耐磨性;另一端具有高韧性和高抗热冲击性能)的同时,使得钢管的内表面强化层及基体具备较好的结合力、抗热冲击性能。
36.(2)由于本发明的熔盐路径设计,可实现钢管内表面强化的同时,外表面不受熔盐影响,不会产生额外的污染和不必要的渗层。
37.(3)由于前连接管和高温转接头的设计,本发明可实现不同长度钢管同时强化,同时,结合不同的冷却或加热装置,可通过在前连接管中对熔盐进行升温或降温,实现不同工艺(不同钢管渗氮温度)钢管的同时处理。
38.(4)由于强制冷却装置和加热装置的设计,本发明可实现钢管内熔盐从恒温到不同温降的连续可调控制,适应不同工艺要求,制备具有不同轴径向性能(包括硬度、耐磨性、塑韧性、耐冲击性)梯度的钢管。
39.(5)由于流动式氮化的设计思路,可实现小炉体和少量熔盐对大型钢管的热处理(相较于原有的浸没式氮化),节省材料,绿色环保。
附图说明
40.图1为内表面梯度强化钢管制备装置示意图;
41.图中:1、熔盐池,2、熔盐池加热系统,3、熔盐,4、前连接管,5、耐高温密封装置,6、控温装置,7、钢管,8、连接管,9、回液管,10、高温熔盐泵。
具体实施方式
42.为了更好地理解上述技术方案,下面将结合具体的实施方式对上述技术方案进行详细的说明。应该指出,以下详细说明都是例示性的,旨在对本发明提供进一步的说明,并不用于限制本发明,对于本领域的技术人员来说,其依然可以对下述实施例所记载的技术方案进行修改,或者对其中部分技术特征进行等同替换。凡在本发明的精神和原则之内,所做的任何修改、等同替换、改进等,均应包含在本发明的保护范围之内。
43.实施例1
44.钢管采用h13钢,钢管长900mm,外径22mm,内径8mm。
45.具体处理步骤如下:
46.s1:钢管7内部为电化学抛光状态,前处理选用水洗、压缩空气吹干,最后预氧化20min;
47.s2:熔盐3选用520℃、cno-浓度33%的渗氮盐,熔盐池加热系统2最大加热功率25kw;将熔盐池1、100mm前连接管4、钢管7、连接管8、高温熔盐泵10、回液管9依次连接;连接管与钢管之间、连接管与高温熔盐泵之间和高温熔盐泵与回液管之间采用密封式金属管接头5密封;回液管9置入熔盐池1中,熔盐池1中熔盐3液面没过钢管下端10mm;
48.s3:确认各部分密封良好,启动高温熔盐泵10,设定高温熔盐泵0.1l/min,使熔盐3
由钢管7下端经由钢管7内表面、连接管8内部、高温熔盐泵10、回液管9内部后返回熔盐池1中,钢管7外围包覆电热膜6进行保温加热,钢管两端温降为30℃,渗氮持续180min;
49.s4:渗氮完成后停转高温熔盐泵10,将钢管50℃水洗,去除管内表面残留的渗氮熔盐,随后晾干。
50.采用线切割取得钢管两端及中间位置样品,经过200~2000目砂纸打磨后,采用1.5μm金刚石抛光剂进行抛光,采用显微维氏硬度计对内表面硬度、截面硬度进行测量,确定有效强化层深度,随后通过4%硝酸酒精腐蚀,观察强化层中化合物层厚度。钢管基体硬度487hv
0.05
,一端内表面硬度为1085hv
0.05
,有效强化层深度120μm(化合物层厚度8μm);中间位置内表面硬度为965hv
0.05
,有效强化层深度102μm(化合物层厚度3.9μm);另一端内表面硬度为840hv
0.05
(化合物层厚度2.1μm),有效强化层深度87μm。经过s1~s4后的钢管内表面强化层在轴径向均具有梯度特征。强化后钢管除浸入熔盐的10mm外,外表面保持原始组织结构与性能,无任何污染。
51.实施例2
52.钢管7采用5根20cr钢,钢管长1500mm,外径55mm,内径40mm。
53.具体处理步骤如下:
54.s1:前处理选用喷砂、清水冲洗、氮气吹干;
55.s2:熔盐3选用520℃、cno-浓度30.5%的渗氮盐,熔盐池加热系统2最大加热功率30kw;将熔盐池1、钢管7、连接管8、五转一转接头、高温熔盐泵10、回液管9依次连接;连接管8与钢管7之间、连接管8与高温熔盐泵9之间和高温熔盐泵10与回液管9之间采用金属密封垫片5密封;回液管9置入熔盐池1中,熔盐池1中熔盐3水平面没过钢管下端30mm;
56.s3:确认各部分密封良好,启动高温熔盐泵10,设定高温熔盐泵0.5l/min,使熔盐3由钢管下端经由钢管7内表面、连接管8内部、高温熔盐泵10、回液管9内部后返回熔盐池1中,钢管7外围采用环绕式热风机控温,钢管两端温降为40℃,渗氮持续180min;
57.s4:渗氮完成后停转高温熔盐泵10,将钢管水冷后采用50℃水洗,去除管内表面残留的渗氮熔盐,随后90℃烘干。
58.随机选取一根处理后钢管,采用线切割取得钢管两端及中间位置样品,经过200~2000目砂纸打磨后,采用1.5μm金刚石抛光剂进行抛光,采用显微维氏硬度计对内表面硬度、截面硬度进行测量,确定有效强化层深度,随后通过4%硝酸酒精腐蚀,观察强化层中化合物层厚度。钢管基体硬度291hv
0.05
,一端内表面硬度为633hv
0.05
,有效强化层深度165μm(化合物层厚度6.5μm);中间位置内表面硬度为611hv
0.05
,有效强化层深度132μm(化合物层厚度4.6μm);另一端内表面硬度为586hv
0.05
(化合物层厚度3.5μm),有效强化层深度90μm。强化后钢管除浸入熔盐的30mm外,外表面保持原始结构与性能,无任何污染。
59.实施例3
60.钢管7采用1根2cr13钢,钢管长5000mm,外径180mm,内径130mm。
61.具体处理步骤如下:
62.s1:钢管7前处理选用喷砂、随后压缩空气清理;
63.s2:熔盐3选用520℃、cno-浓度30.5%的渗氮盐,熔盐池加热系统2最大加热功率60kw;将熔盐池1、钢管7、连接管8、高温熔盐泵10、回液管9依次连接;连接管8与钢管7之间、连接管8与高温熔盐泵10之间和高温熔盐泵10与回液管9之间采用金属密封垫片密封;回液
管9置入熔盐池1中,熔盐池1中熔盐3水平面没过钢管下端100mm;
64.s3:确认各部分密封良好,启动高温熔盐泵10,设定高温熔盐泵6l/min,使熔盐3由钢管下端经由钢管7内表面、连接管8内部、高温熔盐泵10、回液管9内部后返回熔盐池1中,钢管7外围采用电阻加热管环绕加热,钢管两端温降为40℃,渗氮持续180min;
65.s4:渗氮完成后停转高温熔盐泵10,将钢管水冷后采用50℃水洗,去除管内表面残留的渗氮熔盐,随后通风处自然风干。
66.采用线切割取得钢管两端及中间位置样品,经过200~2000目砂纸打磨后,采用1.5μm金刚石抛光剂进行抛光,采用显微维氏硬度计对内表面硬度、截面硬度进行测量,确定有效强化层深度,随后通过4%硝酸酒精腐蚀,观察强化层中化合物层厚度。钢管基体硬度403hv
0.3
,一端内表面硬度为1302hv
0.3
,有效强化层深度65μm;中间位置内表面硬度为1145hv
0.3
,有效强化层深度51μm;另一端内表面硬度为1043hv
0.3
,有效强化层深度38μm。经过s1~s4后的钢管内表面强化层在轴径向均具有梯度特征。强化后钢管除浸入熔盐的100mm外,外表面保持原始结构与性能,无任何污染。