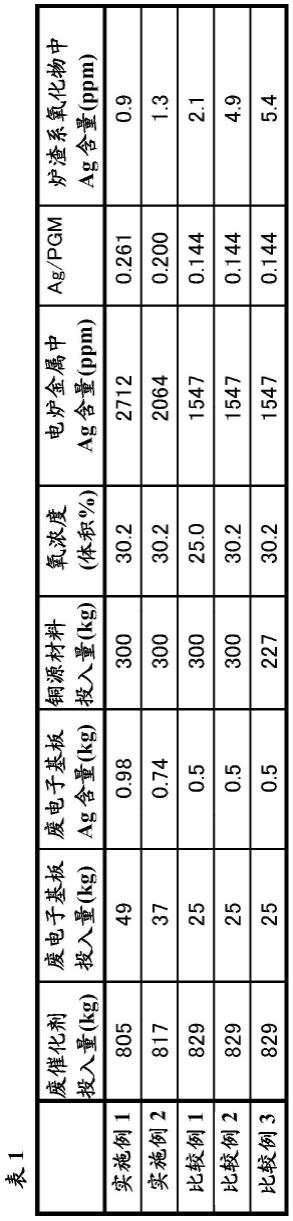
1.本发明涉及从含有铂族元素的物质、例如使用过的石油化学系催化剂、汽车废气净化用废催化剂、使用过的电子基板、引线框等中回收铂族元素(platinum group metals,以下有时简称为pgm)、金的方法。
背景技术:2.以往,作为从使用过的汽车催化剂等含有铂族元素的物质中回收铂族元素的方法,已知有湿式法、干式法,湿式法在回收率、成本方面存在问题,未实用化。
3.另一方面,本技术人提出了一种高收率、低成本的铂族元素的回收方法,其代替湿式法,将含有铂族元素的汽车废气净化用废催化剂等与金属铜一起进行氧化处理,将废催化剂的载体等作为炉渣(slag)系氧化物分离,使熔融铜吸收铂族元素,从而浓缩铂族元素(专利文献1)。
4.但是,在专利文献1公开的铂族元素的回收方法的情况下,根据通过氧化处理而生成的炉渣系氧化物的性状,有时铂族元素的一部分转移到该炉渣系氧化物中。关于该问题,本技术人发现,通过将金属熔液和炉渣系氧化物在适当的温度下在炉内充分地静置,能够减少转移到炉渣系氧化物的铂族元素的量。
5.但是,即使延长氧化处理后的金属熔液和炉渣系氧化物的静置时间,有时转移到炉渣系氧化物的铂族元素的量也没有降低。根据申请人的研究,判明其原因在于,供于氧化处理的含有铂族元素的被处理原料的组成因批次(lot)而大幅变动,如果在电炉中的加热处理中生成高粘性的炉渣,则铂族元素难以被吸收至金属熔液中。
6.因此,申请人发现:通过预先分析并掌握含有铂族元素的被处理原料中的炉渣形成成分中的至少al、si和fe的氧化物的含量,根据这些氧化物的含量,调整投入至炉内的助焊剂成分的组成,由此能够稳定地降低转移到炉渣系氧化物的铂族元素的量(专利文献2)。
7.现有技术文献
8.专利文献
9.专利文献1:日本特开2000-248322号公报
10.专利文献2:日本特开2004-277792号公报
技术实现要素:11.发明所要解决的课题
12.但是,即使在进行了专利文献2中记载的改良的情况下,根据生成的炉渣系氧化物的性状,有时转移到炉渣系氧化物中的铂族元素的量增多到无法忽视的程度。关于这一点,本发明人反复进行了深入研究,结果判明:对含有铂族元素的被处理原料进行加热熔融而得到的金属熔液中的成分与转移到炉渣系氧化物中的铂族元素量之间存在相关关系,特别是,转移到炉渣系氧化物中的铂族元素的量受到该金属熔液中包含的银的含量的影响。
13.本发明的目的在于提供一种铂族元素的回收方法,其在将含有铂族元素的被处理
原料与包含金属铜或氧化铜的至少1种的铜源材料、助焊剂成分和还原剂一起进行加热处理从而回收铂族元素的方法中,抑制铂族元素向炉渣系氧化物中转移,从而进一步提高铂族元素的回收率。
14.用于解决课题的手段
15.本发明人发现,在上述铂族元素的回收方法中,通过控制金属熔液中的银浓度,能够抑制铂族元素向炉渣系氧化物中转移,由此完成了以下所述的本发明。
16.即,为了实现上述的课题,在本发明中,
17.[1]本发明提供铂族元素的回收方法,将含有铂族元素的被处理原料和包含金属铜或氧化铜中的至少1种的铜源材料与助焊剂成分和还原剂一起在炉内加热熔融,利用比重差将吸收铂族元素的金属熔液与炉渣系氧化物分离后,对吸收了所述铂族元素的金属熔液进行氧化处理,利用比重差分离为以氧化铜为主成分的氧化物层和铂族元素被浓缩了的以金属铜为主成分的金属熔液,其中,将通过所述加热熔融而分离的金属熔液中的银的含量调整为2000ppm以上且8000ppm以下。
[0018]
[2]在所述[1]项的铂族元素的回收方法中,在将通过加热熔融而分离的金属熔液中的银含量相对于铂族元素含量的质量比表示为ag/pgm时,ag/pgm优选为0.2以上且0.8以下。
[0019]
[3]在所述[1]项或[2]项的铂族元素的回收方法中,优选一边供给氧浓度27体积%以上且100体积%以下的含氧气体或者供给氧,一边进行所述氧化处理。
[0020]
[4]在所述[1]项~[3]项的铂族元素的回收方法中,优选将含有所述铂族元素的被处理原料在插入炉内之前粉碎,使最大粒径小于400μm。
[0021]
[5]在所述[1]项~[4]项的铂族元素的回收方法中,相对于含有所述铂族元素的被处理原料,以质量比计,优选添加0.3以上且0.9以下的所述的铜源材料。
[0022]
[6]在所述[1]项~[5]项的铂族元素的回收方法中,能够将所述分离的以氧化铜为主成分的氧化物作为所述铜源材料进行再利用。
[0023]
发明效果
[0024]
根据本发明,通过调整对含有铂族元素的被处理原料进行加热处理而得到的金属熔液中的银含量,能够抑制铂族元素向炉渣系氧化物中转移,进一步提高铂族元素的回收率。
具体实施方式
[0025]
[被处理原料]
[0026]
铂族元素(pgm)是指钌(ru)、铑(rh)、钯(pd)、锇(os)、铱(ir)和铂(pt)这六种元素,在记为pgm的情况下,不仅表示这些金属元素的单质,有时也表示两种以上的金属的组合。本发明为pgm的回收方法,但除了pgm以外,也能够应用于金(au)的回收。
[0027]
在本发明的铂族元素的回收方法中,作为含有pgm的被处理原料,例如可列举出含有铂、钯等的使用过的石油化学系催化剂,含有铂、钯、进而铑等的使用过的汽车废气净化用催化剂,对于从这些催化剂的制造工序中得到的批量次品、废料等,以及含有钯等的使用过的电子基板、数码构件、引线框等也可以使用。
[0028]
对上述含有铂族元素的被处理原料在电炉内实施加热熔融处理,为了提高加热熔
融处理时发生的反应的速度,优选在插入电炉前进行破碎
·
粉碎
·
混合,制成细粒状物质。予以说明,在投入电炉时,若将原料制为细粒状物质,则反应速度变快,并且pgm容易被吸收到金属熔液中。在该情况下,优选将细粒状物质的最大粒径设为50mm左右。为了将被处理原料破碎,例如可以使用颚式破碎机作为一次破碎机、使用双辊破碎机作为二次破碎机。在原料中存在铁屑等异物的情况下,破碎前后可配置磁力分选器。
[0029]
另外,如后所述,将被处理原料制成细粒状物质后,优选预先测定该细粒状物质的平均银含量,此时,对于供于分析的细粒状物质的最大粒径而言,优选用磨粉机(
パルベライザー
)等进一步微粉化至400μm以下,更优选使用粉碎至最大粒径为350μm以下的细粒状物质。
[0030]
该情况下,供于分析的细粒状物优选用振动磨机等进一步微粉化至平均粒径10μm以下,更优选使用粉碎至平均粒径为5μm以下的细粒状物质。予以说明,使用振动磨机等进行微粉化的情况下,即使延长粉碎时间等而使平均粒径小于1μm,分析结果中也看不出差异,因此将平均粒径设为1μm以上。
[0031]
[铜源材料]
[0032]
在本发明的铂族元素的回收方法中,作为铜源材料,使用金属铜或氧化铜中的一种或两种。这些铜源材料不需要是特别高的纯度。将含有铂族元素的被处理原料、助焊剂成分和还原剂一起在炉内加热熔融时,金属铜熔解,并且氧化铜的一部分或全部还原而熔融为金属铜,形成熔入铂族元素的金属熔液。另外,对得到的金属熔液实施后述的氧化处理时,构成金属熔液的金属铜的一部分被氧化而成为氧化铜,能够回收该氧化铜,作为铜源材料再利用。予以说明,铜源材料的直径优选为0.1mm以上且小于10mm。
[0033]
对于投入到电炉的上述铜源材料的添加量,优选将金属铜、氧化铜或它们两者设为以与被处理原料的质量比计0.3以上。进一步优选添加0.5以上。在此,通过添加大量的氧化铜,金属熔液内的pgm与铜源材料的接触机会增加,因此能够降低pgm向炉渣系氧化物的转移。另外,通过添加大量的氧化铜,还原炉内的金属熔液中的pgm的含量降低,因此,相对地pgm向炉渣系氧化物中的转移量容易减少。铜源材料添加的上限值以与被处理原料的重量比计优选为0.9以下。即使使添加量进一步增加,pgm向炉渣系氧化物中的转移量也不会降低,工序内的铜循环量增加,容易变得不经济。
[0034]
[助焊剂成分]
[0035]
在本发明的铂族元素的回收方法中,作为助焊剂成分,可以使用选自al2o3、sio2、cao、caco3和feo中的至少1种。就助焊剂的添加量而言,优选以下述方式进行调节:预先测定含有pgm的被处理原料中包含的至少al、si和fe的量,使反应生成的炉渣系氧化物的组成成为以下的范围。
[0036]
在炉渣系氧化物的成分组成为al2o3:20~30质量%、sio2:25~40质量%、cao:20~35质量%、feo:0~35质量%(包含0%)的情况下,炉渣系氧化物具有适当的粘度和良好的分散性、流动性,因此在比重分离的过程中,被处理原料中混合存在的铂族元素容易被熔融金属铜吸收。在该情况下,与金属熔液分离的炉渣系氧化物可以为下述成分组成的炉渣系氧化物:包含al:10~22质量%、si:10~16质量%、ca:14~22质量%、fe:27质量%以下(包含0%)、pt:10ppm以下,余量基本上由氧构成。
[0037]
若在电炉中生成的炉渣系氧化物不在上述范围,例如al2o3超过30质量%,则炉渣
的粘度急剧增大,其结果,从氧化铜还原的熔融金属铜与pgm的接触速度变慢,吸收了pgm的熔融金属铜容易在炉渣中浮游,pgm向金属熔液的吸收率降低。
[0038]
[还原剂]
[0039]
在本发明的铂族元素的回收方法中,使用还原剂的主要目的在于将氧化铜还原为金属铜。作为还原剂,代表性地使用焦炭、sic,也可以使用含有金、铂族元素的贱金属类,在该情况下,能够同时回收贱金属中的金、铂族元素。用于电子基板的树脂、活性炭等也可以用作还原剂。
[0040]
[银成分]
[0041]
本发明的铂族元素的回收方法的技术特征之一在于,将上述含有pgm的被处理原料、铜源材料、助焊剂成分和还原剂混合并在加热炉内加热熔融,使吸收了pgm的金属熔液与炉渣系氧化物分离时,控制金属熔液中的银(ag)的含量。
[0042]
通过增加金属熔液中的ag含量,转移到炉渣系氧化物中的pgm的量减少的理由在目前尚不明确,本发明人认为其机理如下。
[0043]
即,认为由于金属熔液中的ag含量增加,fe、ni、pb等向炉渣的分配率降低,与它们亲和性高的pgm向炉渣的分配率也降低。
[0044]
在本发明的铂族元素的回收方法中,通过上述的加热熔融处理,利用比重差将炉渣系氧化物与金属熔液分离时,将金属熔液中的ag含量调整为2000ppm以上且8000ppm以下。金属熔液中的ag含量低于2000ppm时,抑制转移到炉渣系氧化物中的pgm的量的效果弱。另外,若ag含量超过8000ppm,则抑制转移到炉渣系氧化物中的pgm的量的效果饱和,并且制造成本增大,因此不优选。
[0045]
为了将金属熔液中的ag含量调整为上述范围,优选将上述含有pgm的被处理原料中的ag含量相对于pgm含量的质量比(ag/pgm)调整为0.2以上且0.8以下。
[0046]
通过进行该调整,能够将金属熔液中的ag含量调整为上述期望的范围。含有pgm的被处理原料中的ag/pgm小于0.2时,固溶于ag中的pgm的量减少,pgm的回收率降低,因此不优选。另外,若含有pgm的被处理原料中的ag/pgm超过0.8,则有时相比于转移到炉渣氧化物中的pgm的减少量,ag的成本更高。
[0047]
上述含有pgm的被处理原料中的ag含量的调整可以如下进行。以往的废气净化用催化剂等中存在包含少量的ag的催化剂,但使用其得到的金属熔液中的ag含量最大为1600ppm以下。因此,在本发明的铂族元素的回收方法中,需要在上述含有pgm的被处理原料中进一步追加ag。作为ag,可以将ag原料金属粉碎进行添加,从降低制造成本的观点出发,优选粉碎混合上述含有pgm的被处理原料时,将包含大量ag的废电子基板、含有ag的废料品、淤渣(sludge)等加入到被处理原料中,进行粉碎处理。此时,优选预先测定含ag废电子基板的ag含量,在投入到电炉前对含有pgm的被处理原料中的ag含量进行调整。
[0048]
[加热熔融处理]
[0049]
在本发明的铂族元素的回收方法中,向含有pgm的被处理原料中加入铜源材料、助焊剂成分和还原剂,实施在炉内进行加热熔融以利用比重差将吸收了pgm的金属熔液与炉渣系氧化物分离的加热熔融处理。此时,优选在投入到加热炉之前,预先将含有pgm的被处理原料、铜源材料粉碎,与粉粒状的助焊剂成分和还原剂混合。作为加热炉,使用通常的电炉即可,加热的气氛可以为大气气氛。进行加热熔融处理时,含有pgm的被处理原料中包含
的铬(cr)、铝(al)等易氧化性的金属的一部分被氧化,与被处理原料中原本包含的氧化物和助焊剂成分一起形成玻璃状的熔融炉渣系氧化物,比重小的炉渣系氧化物上浮至金属熔液上方。另一方面,氧化铜被还原而变成金属铜,熔融的金属铜由于比重差而在熔融炉渣系氧化物中沉降,在熔融炉渣系氧化物层的下层形成金属熔液。其结果,投入原料分离为主要由铜构成、包含pgm、ag和au等贵金属的金属熔液、和炉渣系氧化物。
[0050]
将上述经混合的投入原料加热熔融(熔化,meltdown)的温度优选为1100℃以上且1600℃以下。熔化的温度低于1100℃时,生成的炉渣系氧化物的熔融容易变得不彻底,熔融炉渣的粘度也变高,因此pgm的回收率降低,因此不优选。若熔化的温度超过1600℃,则能量成本增大,且成为导致电炉的炉体破损的主要原因,因此不优选。熔化的温度更优选为1200℃~1500℃。在加热熔融处理中,优选在投入原料熔融后设置至少保持5小时以上、优选保持10小时以内的静置工序。
[0051]
在上述加热熔融和静置之后,对于上浮到金属熔液上方的炉渣系氧化物,通过倾动操作(倾倒操作)等进行排渣,使吸收了pgm的金属熔液出汤(出湯),供于下一工序的氧化处理。
[0052]
[氧化处理]
[0053]
在本发明的铂族元素的回收方法中,对通过上述加热熔融处理工序而得到的吸收了pgm的金属熔液实施氧化处理,利用比重差分离为以氧化铜为主成分的氧化物层、和进一步浓缩了pgm的以金属铜为主成分的金属熔液,由此进行熔入金属熔液中的pgm的浓缩。进行氧化处理时,金属熔液中的铜被氧化而变成氧化铜,并且金属熔液中微量包含的铁(fe)、镍(ni)等也被氧化而形成氧化物层,金属熔液成为在接近纯铜的熔液中包含浓缩了的pgm、ag和au等贵金属的金属熔液。另外,当然,通过实施氧化处理,金属熔液的量减少,在全部的铜氧化之前结束处理。
[0054]
上述氧化处理是一边将炉内的金属熔液的温度维持在1100℃以上且1600℃以下、优选1200℃以上且1500℃以下的温度,一边向炉内导入氧气或富氧气体来进行的。金属熔液的温度低于1100℃时,氧化速度容易降低,相反,若超过1600℃,则容易产生炉体的破损,因此不优选。
[0055]
例如在氧化炉中通过重油燃烧器对前工序中得到的金属熔液进行加热的情况下,如果仅加热气氛则金属熔液的温度难以上升。另外,氧化炉中最初生成的铁氧化物和镍氧化物的含量高的炉渣系氧化物的熔点高,与金属熔液的分离性差,因此使用富氧气体进行氧化处理,使金属熔液的温度上升。若金属熔液的温度上升,则铁和镍含量高的炉渣系氧化物的流动性变好,炉渣与金属系氧化物的分离性提高。
[0056]
作为上述富氧气体,优选使用氧浓度为27体积%以上且100体积%以下的气体。予以说明,氧浓度为100体积%是指纯氧气。富氧气体的氧浓度低于27体积%时,与利用大气时相比,有时氧化速度等没有明显的变化,因此不优选。
[0057]
氧化处理中可以使用纯氧气,但氧浓度超过40体积%时,例如氧化炉的喷枪的消耗容易变快,因此氧浓度更优选为27体积%以上且40体积%以下。通过设为这样的氧浓度,能够提高氧化速度以及减少氧化炉中的铂族向炉渣的转移。
[0058]
关于上述富氧气体的吹入量,作为氧化处理前的每1吨金属熔液的吹入量(nm3/吨-金属),可设为30nm3/吨-金属以上且70nm3/吨-金属以下。
[0059]
氧化处理结束后,使氧化炉倾动(倾斜),使上层的主要由铜的氧化物构成的氧化物层流出到炉外,与金属熔液分离。接着,将pgm浓缩后的下层的金属熔液排出(出汤),供于本发明的范围外的下一工序的pgm回收工序。此时,优选不是通过一次氧化处理就直接使pgm浓缩后的金属熔液出汤,而是将由上述加热熔融处理的工序而得到的吸收了pgm的金属熔液进一步投入到氧化炉内,反复进行氧化处理,从而在金属熔液中的pgm的含量成为10~75质量%的时刻使金属熔液出汤,在下一工序中回收pgm。
[0060]
从氧化炉流出的氧化物层如上所述主要由氧化铜构成,因此能够在使其从氧化炉流出并冷却固化后,作为加热熔融处理的铜源材料再利用。由此,也能够回收伴随氧化物层的微量的pgm。
[0061]
予以说明,在使氧化物层从氧化炉流出时,如果从熔融状态进行急水冷从而进行水淬化(水砕化),则可以使主要由氧化铜构成的氧化物成为最大直径0.1mm以上且10mm以下的粒状物,由此能够制成适合作为加热熔融处理的铜源材料的材料。
[0062]
[实施例]
[0063]
[实施例1]
[0064]
依次使用辊磨机、磨粉机(
パルぺライザー
)这两种机器将使用过的块状的蜂窝状汽车废气净化用催化剂(转换器的碎片)粉碎至最大直径400μm以下,作为投入用原料。使用振动磨机将投入用原料的一部分粉碎至平均粒径5μm,从而作为组成分析用的试样,使用荧光x射线分析装置(型号:rigaku zsx primusii)预先测定被处理原料的组成。另外,对于含有ag的废电子基板,也同样地测定其组成和ag含量。上述投入用原料的质量和上述废电子基板的质量的合计值为被处理原料的投入质量。
[0065]
称量上述的投入原料805kg、废电子基板49kg(ag含量0.98kg)、296kg作为助焊剂成分的cao,称量作为还原剂的焦炭30kg和氧化铜(含有约80质量%的0.1mm以上且10mm以下的粉粒状物)300kg,将它们投入到电炉中,在1350℃下加热熔融。使其熔化后,将熔融物在1250~1300℃的温度下静置约5小时,接着使上层的炉渣系氧化物从电炉的侧面流出,使其冷却固化。
[0066]
使电炉内的吸收了pgm的金属熔液从电炉下部出汤(排出),将其导入经加热的氧化炉内。该金属熔液中的ag含量为2712ppm。另外,该金属熔液中的ag的质量相对于铂族元素(pt、pd、rh)的总质量的比ag/pgm为0.261。
[0067]
接着,对氧化炉内的含有pgm的金属熔液吹入氧浓度为30.2体积%的富氧气体,然后将该富氧气体喷吹到熔液表面进行氧化处理。在熔液表面生成的氧化物的层成为约1cm的厚度时,使炉倾斜,使该氧化物流出到炉外,将流出的氧化物投入到水槽内,用大量的流水进行水冷。
[0068]
将除去氧化物层而得到的金属熔液全部从氧化炉出汤(排出),进行冷却固化,作为pgm的浓缩物进行回收。对其进行分析,金属铜=5.3kg,就pgm的含量而言,pt=18.5质量%、pd=35.9质量%、rh=4.9质量%。另外,从电炉的上层除去的炉渣系氧化物中包含的pgm为0.9ppm。该值为例如后述的比较例1的1.94ppm的一半以下,可知通过使用本发明的铂族元素的回收方法,能够减少转移到炉渣系氧化物中的pgm的量。
[0069]
表1中示出本实施例的操作条件和操作结果。予以说明,表1中也一并示出其他实施例和比较例的结果。
[0070]
表1
[0071][0072]
[实施例2]
[0073]
将废催化剂817kg和废电子基板37kg(ag含量0.74kg)投入到电炉中,进行与实施例1相同的操作,金属熔液中的ag含量为2064ppm,金属熔液中的ag的质量相对于pgm的总质量的比ag/pgm为0.200。在与实施例1相同的条件下对该金属熔液实施氧化处理,就pgm的浓缩物而言,金属铜=5.6kg,pgm的含量为pt=19.9质量%、pd=34.4质量%、rh=4.5质
量%,炉渣系氧化物中包含的pgm为1.3ppm。
[0074]
[比较例1]
[0075]
将废催化剂829kg和废电子基板25kg(ag含量0.50kg)投入电炉中进行加热熔融,电炉的金属熔液中的ag含量为1547ppm,ag/pgm为0.144。
[0076]
在与实施例1相同的条件下对该金属熔液实施氧化处理,金属铜=5.3kg,就pgm的含量而言,pt=20.0质量%、pd=34.2质量%、rh=4.9质量%。另外,从电炉的上层去除的炉渣系氧化物中包含的pgm的含量为2.1ppm,与实施例相比为较高的值。
[0077]
[比较例2]
[0078]
对于氧化炉内的金属熔液,初期将氧浓度25.0体积%的富氧气体吹入熔液中,然后将该富氧气体喷吹到熔液表面进行氧化处理,除此以外,重复与比较例1同样的操作,回收本比较例的pgm的浓缩物。对其进行分析,金属铜=5.7kg,就pgm的含量而言,pt=17.9质量%、pd=37.1质量%、rh=4.5质量%。另外,从电炉的上层去除的炉渣系氧化物中所含的pgm的含量为4.9ppm。
[0079]
[比较例3]
[0080]
除了使用227kg氧化铜作为铜源材料以外,重复与比较例1同样的操作,回收本比较例的pgm的浓缩物。对其进行分析,金属铜=4.8kg,就pgm的含量而言,pt=20.8质量%、pd=34.1质量%、rh=4.8质量%。另外,从电炉的上层去除的炉渣系氧化物中所含的pgm的含量为5.4ppm。
[0081]
由以上的结果可知,使用本发明的铂族元素的回收方法时,能够减少转移到炉渣系氧化物中而未被回收的铂族元素的量,进一步提高铂族元素的回收率地进行回收。