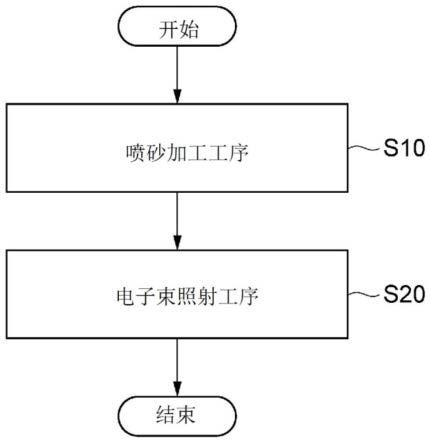
1.本公开涉及表面处理方法以及表面处理系统。
背景技术:2.专利文献1公开有通过电子束的照射使模具表面平滑的表面处理方法。
3.专利文献1:日本特开2004-001086号公报
4.在专利文献1的方法中,认为通过电子束使工件的表面熔融,从而使工件的表面平滑化。因此,若能够将工件的表面状态控制为容易通过电子束熔融的形状,则存在能够高效地去除工件的粗糙度的可能性。该公开提供一种能够通过电子束的照射高效地使工件平滑的技术。
技术实现要素:5.本发明人着眼于喷砂加工能够以与熔融不同的原理控制表面状态这一点,发现若在照射电子束之前进行喷砂加工,则与仅进行电子束的照射的情况相比,工件的表面粗糙度的降低率变大。即,发现在电子束照射前后的工件的粗糙度的降低比例变大。
6.即,本公开的一个方面所涉及的表面处理方法是处理工件的表面处理方法,该表面处理方法具备:喷砂加工工序,其对工件的表面进行喷砂加工;和电子束照射工序,其对工件的喷砂加工完成的表面照射电子束。根据该表面处理方法,与仅进行电子束的照射的情况相比,工件的表面粗糙度的降低率变大,因此能够通过电子束的照射高效地使工件平滑。
7.在一个实施方式中,也可以为,工件为金属粉末的烧结品。在一个实施方式中,工件也可以为层叠造型品。烧结品或层叠造型品的表面的粗糙度处于变得比较大的趋势。该表面处理方法即使是烧结品或层叠造型品的表面也能够高效地使其平坦。
8.在一个实施方式中,也可以为,工件的喷砂加工完成的表面的粗糙度曲线要素的平均长度不足770.80μm。在该情况下,表面处理方法能够使工件的表面粗糙度的降低率为20%以上。
9.本实施方式的另一个方面所涉及的表面处理系统具备:喷砂加工装置,其对工件进行喷砂加工;电子束照射装置,其对工件照射电子束;以及控制部,其控制喷砂加工装置以及电子束照射装置。而且,控制部控制喷砂加工装而对工件的表面进行喷砂加工,另外控制电子束照射装置而对喷砂加工完成的工件的表面照射电子束。该表面处理系统与上述的表面处理装置同样地,与仅进行电子束的照射的情况下相比,能够通过电子束的照射高效地使工件平滑。
10.根据本公开,能够通过电子束的照射高效地使工件平滑。
附图说明
11.图1是表示实施方式所涉及的表面处理方法的一个例子的流程图。
12.图2是表示喷砂加工装置的一个例子的示意图。
13.图3是表示电子束照射装置的一个例子的示意图。
14.图4是表示实施方式所涉及的表面处理系统的一个例子的框图。
15.图5是对工件进行的电子束的照射的一个例子。
16.图6是表示表面粗糙度的评价结果的表。
17.图7是表示rsm(粗糙度曲线要素的平均长度)与rz(最大高度粗糙度)降低率的相关性的分布图。
18.图8是电子束照射的前后的工件的截面观察结果。
19.附图标记说明
20.10...喷砂加工装置;40...电子束照射装置;80...控制部;90...表面处理系统;eb...电子束;w...工件。
具体实施方式
21.以下,参照附图,对本公开的实施方式进行说明。此外,在以下说明中,对相同或相当的要素标注相同的附图标记,不反复进行重复的说明。附图的尺寸比率未必与说明的一致。“上”、“下”、“左”、“右”的用语是基于图示的状态的用语,是为了方便说明的。
22.[表面处理方法]
[0023]
图1是表示实施方式所涉及的表面处理方法的一个例子的流程图。图1所示的表面处理方法是使工件的表面平滑化的方法。工件是进行表面处理的对象物。工件例如由铁、铝、钛、不锈钢、铜合金或碳钢等金属形成。工件也可以为金属粉末的烧结品。烧结品是通过粉末冶金对金属粉末进行烧结而制造的。工件也可以为层叠造型品。层叠造型品是对金属粉末反复照射激光而制造的。工件也可以为铸造品。工件也可以为切削加工品。工件也可以为锻造品。
[0024]
如图1所示,表面处理方法具备喷砂加工工序(步骤s10)以及电子束照射工序(步骤s20)。喷砂加工工序通过喷砂加工装置进行。电子束照射工序通过电子束照射装置进行。首先,对在各工序中使用的装置例的概要进行说明。
[0025]
[喷砂加工装置]
[0026]
图2是表示喷砂加工装置的一个例子的示意图。喷砂加工是通过投射研磨材料来磨削工件的表面的加工方法。研磨材料的材质从金属、陶瓷、玻璃、树脂、植物来源物等各种材质中选择。所谓金属,例如为铁、锌、不锈钢等。所谓陶瓷,例如为氧化铝、碳化硅、锆石等。所谓树脂,例如为尼龙树脂、三聚氰胺树脂、尿素树脂等。所谓植物来源物,例如为核桃、桃子等。研磨材料的形状从球状、多边形状、圆柱状等各种形状中选择。例如,在金属的粒子的情况下,能够选择弹丸、砂粒、或者切断丝。弹丸是球状粒子。砂粒是具有锐角部的多边形状粒子。切断丝是圆柱形状的粒子或者是角部变圆的圆柱形状的粒子。
[0027]
图2所示的喷砂加工装置10为直压式的喷砂加工装置。所谓直压式的喷砂加工装置,即为加压式的喷砂加工装置。如图2所示那样,喷砂加工装置10包含贮存容器20以及喷嘴30。贮存容器20在内部对贮存研磨材料的空间进行划分,并贮存研磨材料。从外部向贮存容器20供给研磨材料。例如,作业者也可以向贮存容器20供给研磨材料。贮存容器20也可以再使用用于喷砂加工的研磨材料的一部分。在该情况下,贮存容器20由后述的分级机构14
供给用于喷砂加工的研磨材料。贮存容器20经由定量供给部21以及配管13与喷嘴30连接。定量供给部21是将贮存于贮存容器20的研磨材料向配管13送出的装置,作为一个例子,为螺旋送料器。
[0028]
在配管13连接有供给气体的气体供给源12。气体供给源12例如存在供给中压力的气体的压缩机或气瓶罐、供给低压力的气体的风扇或鼓风机等送风机等。所谓中压力,例如为0.1mpa~0.6mpa的范围的压力。所谓低压力,例如为0.01mpa~0.1mpa的范围的压力。在本实施方式中,作为一个例子,由压缩机供给压缩空气。从气体供给源12向配管13供给的气体将由定量供给部21送出的研磨材料输送到喷嘴30。
[0029]
喷嘴30将从贮存容器20供给的研磨材料与气体一起喷射。喷嘴30收容于处理室31内,经由配管13被供给从贮存容器20供给的研磨材料与气体混合而成的固气两相流。喷嘴30将研磨材料与气体一起朝向内置于处理室31内的工件w喷射。由此,对工件w进行喷砂加工。工件w也可以支承于未图示的工作台,通过工作台驱动机构来调整位置。
[0030]
处理室31的下部经由分级机构14与贮存容器20连接。落到处理室31的下部的研磨材料以及工件w的切屑被未图示的集尘器吸引而通过分级机构14。分级机构14将这些分级成可再使用的研磨材料、和破碎的研磨材料以及工件w的切屑等其他微粉。其他微粉被回收到集尘器。分级机构14的下部与贮存容器20的上部连接。可再使用的研磨材料从分级机构14向贮存容器20供给。在不再使用研磨材料的情况下,喷砂加工装置10也可以不具备分级机构14。
[0031]
喷砂加工装置10由控制装置11控制。控制装置11例如构成为plc(programmable logic controller,可编程逻辑控制器)。控制装置11也可以构成为包括cpu(central processing unit,中央处理单元)等处理器、ram(random access memory,随机存储器)以及rom(read only memory,只读存储器)等存储器、触摸面板、鼠标、键盘以及显示器等输入输出装置、网卡等通信装置在内的计算机系统。控制装置11通过在基于存储于存储器中的计算机程序的处理器的控制下使各硬件动作,从而实现控制装置11的功能。
[0032]
[电子束照射装置的结构]
[0033]
图3是表示电子束照射装置的一个例子的示意图。图3所示的电子束照射装置40是将电子束eb照射到工件w,而进行工件w的表面处理的装置。如图3所示那样,电子束照射装置40包含真空室41、阴极50、阳极51、一对螺线管60以及工作台70。
[0034]
真空室41将被照射电子束eb的工件w以及电子束eb的产生源储存于内部。照射电子束的工件w载置于真空室41内的工作台70。作为电子束eb的产生源的阴极50以与工作台70对置的方式配置于真空室41的内部。在工作台70与阴极50之间配置有环状的阳极51。工作台70、阴极50以及阳极51在真空室41的内部中,以在一个轴上排列的方式配置。一对螺线管60分别为环状的部件。第1螺线管以包围阴极50的方式配置于真空室41的外部,第2螺线管以包围阳极51的方式配置于真空室41的外部。
[0035]
在真空室41连接有旋转泵以及涡轮泵等未图示的真空泵。真空室41在进行电子束eb的照射时预先被抽真空。从外部向被抽真空的真空室41导入ar(氩)气体等非活性气体,真空室41内被保持为5~15
×
10-2
pa左右的非活性气体气氛。
[0036]
在储存于真空室41内的阴极50以及阳极51连接有施加脉冲电压的未图示的电源。在螺线管60连接有未图示的电源,该未图示的电源不同于与阴极50以及阳极51连接的电
源。
[0037]
若对螺线管60施加电压,则螺线管60使真空室41的内部的阳极51附近产生磁场。在阳极51附近产生的磁场成为最大时,对阳极51施加脉冲电压。真空室41内的电子朝向被施加了电压的阳极51移动。此时,由于通过螺线管60在阳极51附近产生了磁场,因此电子通过洛伦兹力,边描绘螺旋边移动。该电子反复进行与气体分子的碰撞,与电子碰撞的气体分子电离成阳离子和电子。阳离子以及电子与气体进一步反复进行碰撞。在阴极50以及阳极51的附近分别形成等离子体。
[0038]
在形成于阳极51附近的等离子体成为最大时,向阴极50施加脉冲电压。此时,阴极50与阴极50附近的等离子体之间的电位差成为最大。由此,从阴极50放出的电子通过阴极50以及阴极50附近的等离子体所产生的电场,向阳极51的方向加速,而生成电子束eb。电子束eb通过环状的阳极51,向载置于工作台70的工件w照射。
[0039]
以下,再次参照图1,对表面处理方法进行说明。首先,作为喷砂加工工序(步骤s10),通过喷砂加工装置10对工件的表面进行喷砂加工。由此,工件表面被物理切削。
[0040]
接下来,作为电子束照射工序(步骤s20),通过电子束照射装置40,对工件的喷砂加工完成的表面照射电子束。工件的表面的微小的凹凸通过电子束的照射而熔融,并变得平滑。具体而言,微小的凸部通过电子束而熔融,熔融后的金属流入微小的凹部,由此工件的表面变得平滑。
[0041]
[表面处理系统]
[0042]
图1所示的表面处理方法也可以由表面处理系统执行。图4是表示实施方式所涉及的表面处理系统的一个例子的框图。如图4所示那样,表面处理系统90具备喷砂加工装置10、电子束照射装置40以及控制部80。作为一个例子,控制部80构成为plc,与喷砂加工装置10以及电子束照射装置40以可通信的方式连接。控制部80也可以构成为上述的计算机系统。控制部80控制喷砂加工装置10以及电子束照射装置40。喷砂加工装置10通过控制部80的控制对工件w进行喷砂加工,电子束照射装置40对通过控制部80的控制进行喷砂加工后的工件w进行电子束的照射。这样,表面处理系统90分别控制喷砂加工装置10以及电子束照射装置40,能够执行图1所示的表面处理方法。
[0043]
[实施方式的总结]
[0044]
在本实施方式所涉及的表面处理方法中,对工件w的喷砂加工完成的表面照射电子束。工件w的喷砂加工完成的表面具有容易通过电子束熔融的形状。作为一个例子,工件w的喷砂加工完成的表面可能被物理切削100μm以上的凹凸。100μm以上的凹凸与不足100μm的凹凸相比,存在基于电子束的照射进行的熔融速度变慢的趋势,因此可以说工件w的喷砂加工完成的表面具有容易通过电子束熔融的形状。即,本实施方式所涉及的表面处理方法通过进行喷砂加工,能够将工件w的表面控制为容易通过电子束熔融的形状。由此,与仅进行电子束的照射的情况相比,工件的表面粗糙度的降低率变大。因此,本实施方式所涉及的表面处理方法能够通过电子束的照射高效地使工件平滑。
[0045]
另外,本实施方式所涉及的表面处理方法即使在将表面粗糙度比较高的烧结品或层叠造型品作为工件w的情况下,与仅进行电子束的照射的情况相比,也能够缩短电子束照射工序的时间。并且,本实施方式所涉及的表面处理方法也能够通过电子束去除因喷砂加工而形成于工件w的表面的瑕疵。
[0046]
以上,虽然对各种例示的实施方式进行了说明,但并不限定于上述例示的实施方式,也可以进行各种省略、置换以及变更。例如,喷砂加工装置10并不限定于直压式的喷砂加工装置,也可以是重力式的喷气装置或离心式的喷砂装置。所谓重力式的喷气装置,即吸引式的喷气装置。
[0047]
实施例
[0048]
以下,为了说明上述效果,对本发明人所实施的实施例进行说明。本公开并不限定于这些实施例。
[0049]
[工件的制作]
[0050]
作为工件w,准备一边为50mm的大致立方体的层叠造型品。工件w是将arcam公司制的金属粉末ti6al4v eli powder层叠造型而得到的。层叠造型使用arcam公司制的层叠造型装置arcam a2x。准备16个相同的工件w。
[0051]
接下来,对16个工件w中的15个工件w,使用图2所示的喷砂加工装置10,以分别设定的喷砂条件来进行喷砂加工。喷砂条件如下这样设置:投射材料的种类为钢砂或钢丸、投射材料的硬度的下限值为450hv~800hv、以及粒度为0.2mm~2.5mm。由此,得到喷砂加工完成的15个工件w和未经喷砂处理的一个工件。
[0052]
接下来,使用图3所示的电子束照射装置40,对16个所有的工件w的表面照射电子束eb。图5是表示对工件进行的电子束的照射的一个例子。如图5所示那样,为了比较电子束eb的照射前后的表面状态,使用掩模材料m。掩模材料m是具有25mm见方的开口s的铜制的掩模。对由掩模材料m覆盖的状态的工件w照射电子束eb。电子束eb的照射条件如下这样设置:脉冲宽度为2μs、脉冲频率为0.125hz、能量密度为15j/cm2、以及脉冲照射次数为50次。
[0053]
[表面粗糙度的确认]
[0054]
针对实施例的喷砂加工完成的15个工件w、和比较例的未经喷砂处理的工件w,确认电子束照射前后的表面粗糙度。表面粗糙度使用(jis b0601:2001)中规定的最大高度粗糙度rz(μm)以及粗糙度曲线要素的平均长度rsm(μm)来进行评价。最大高度粗糙度rz(μm)是在工件w的表面的粗糙度曲线中,最高的点与最低的点的差值。粗糙度曲线要素的平均长度rsm(μm)是工件w的表面的粗糙度曲线的基准长度中的轮廓曲线要素的长度的平均值。并且,使用电子束eb的照射前后的最大高度粗糙度rz(μm),来计算最大高度粗糙度rz降低率(%)。最大高度粗糙度rz降低率(%)是电子束eb的照射使工件w的表面平滑化的比例,用以下式子计算。
[0055]
最大高度粗糙度rz降低率(%)=(1-电子束的照射后的最大高度粗糙度rz/电子束的照射前的最大高度粗糙度rz)
×
100
[0056]
在图6中示出表面粗糙度的评价结果。图6是表示表面粗糙度的评价结果的表。图6所示的喷砂条件“1”是关于比较例的未经喷砂处理的工件w的表面粗糙度的评价结果(比较例)。图6所示的喷砂条件“2”~“16”是实施例的喷砂加工完成的工件w的表面粗糙度的评价结果。
[0057]
如喷砂条件“1”所示那样,未经喷砂处理的工件w的rz在电子束eb的照射前为174.51μm,在电子束eb的照射后降低至139.75μm。在该情况下,rz的降低率为20%。rsm在电子束eb的照射前为367.35μm,在电子束eb的照射后增加至752.66μm。
[0058]
在喷砂条件“2”中,用维氏硬度为450hv,粒度为1.4mm的钢砂对工件w进行了喷砂
加工。喷砂加工完成的工件w的rz在电子束eb的照射前为53.19μm,在电子束eb的照射后降低至45.68μm。在该情况下,rz的降低率为14%。另一方面,rsm在电子束eb的照射前为1091.55μm,在电子束eb的照射后增加至1322.48μm。
[0059]
在喷砂条件“3”中,用维氏硬度大于800hv,粒度为0.7mm的钢砂对工件w进行了喷砂加工。喷砂加工完成的工件w的rz在电子束eb的照射前为54.66μm,在电子束eb的照射后降低至24.65μm。在该情况下,rz的降低率为55%。另一方面,rsm在电子束eb的照射前为391.86μm,在电子束eb的照射后增加至1291.25μm。
[0060]
在喷砂条件“4”中,用维氏硬度大于800hv,粒度为0.7mm的钢砂对工件w进行了喷砂加工。喷砂加工完成的工件w的rz在电子束eb的照射前为65.99μm,在电子束eb的照射后降低至27.98μm。在该情况下,rz的降低率为58%。另一方面,rsm在电子束eb的照射前为433.89μm,在电子束eb的照射后增加至1098.82μm。
[0061]
在喷砂条件“5”,用维氏硬度为450hv,粒度为1.0mm的钢丸对工件w进行了喷砂加工。喷砂加工完成的工件w的rz在电子束eb的照射前为45.43μm,在电子束eb的照射后降低至34.36μm。在该情况下,rz的降低率为24%。另一方面,rsm在电子束eb的照射前为860.99μm,在电子束eb的照射后增加至1180.18μm。
[0062]
在喷砂条件“6”中,用维氏硬度为450hv,粒度为2.5mm的钢丸对工件w进行了喷砂加工。喷砂加工完成的工件w的rz在电子束eb的照射前为45.36μm,在电子束eb的照射后降低至32.19μm。在该情况下,rz的降低率为29%。另一方面,rsm在电子束eb的照射前为922.88μm,在电子束eb的照射后增加至937.18μm。
[0063]
在喷砂条件“7”中,用维氏硬度为450hv,粒度为1.4mm的钢丸对工件w进行了喷砂加工。喷砂加工完成的工件w的rz在电子束eb的照射前为45.45μm,在电子束eb的照射后降低至35.67μm。在该情况下,rz的降低率为22%。另一方面,rsm在电子束eb的照射前为1009.34μm,在电子束eb的照射后降低至956.43μm。
[0064]
在喷砂条件“8”中,用维氏硬度为450hv,粒度为0.6mm的钢丸对工件w进行了喷砂加工。喷砂加工完成的工件w的rz在电子束eb的照射前为47.04μm,在电子束eb的照射后降低至38.62μm。在该情况下,rz的降低率为18%。另一方面,rsm在电子束eb的照射前为959.69μm,在电子束eb的照射后增加至1234.12μm。
[0065]
在喷砂条件“9”中,用维氏硬度为450hv,粒度为2.5mm的钢丸对工件w进行了喷砂加工。喷砂加工完成的工件w的rz在电子束eb的照射前为39.45μm,在电子束eb的照射后降低至35.29μm。在该情况下,rz的降低率为11%。另一方面,rsm在电子束eb的照射前为1024.41μm,在电子束eb的照射后增加至1400.89μm。
[0066]
在喷砂条件“10”中,用维氏硬度大于800hv,粒度为0.3mm的钢砂对工件w进行了喷砂加工。喷砂加工完成的工件w的rz在电子束eb的照射前为44.08μm,在电子束eb的照射后降低至27.91μm(rz的降低率为37%)。另一方面,rsm在电子束eb的照射前为582.93μm,在电子束eb的照射后增加至1298.67μm。
[0067]
在喷砂条件“11”中,用维氏硬度为450hv,粒度为0.7mm的钢砂对工件w进行了喷砂加工。喷砂加工完成的工件w的rz在电子束eb的照射前为53.04μm,在电子束eb的照射后降低至28.44μm。在该情况下,rz的降低率为46%。另一方面,rsm在电子束eb的照射前为610.62μm,在电子束eb的照射后增加至1114.42μm。
[0068]
在喷砂条件“12”中,用维氏硬度为600hv,粒度为0.7mm的钢砂对工件w进行了喷砂加工。喷砂加工完成的工件w的rz在电子束eb的照射前为53.98μm,在电子束eb的照射后降低至37.35μm。在该情况下,rz的降低率为31%。另一方面,rsm在电子束eb的照射前为770.80μm,在电子束eb的照射后增加至1154.21μm。
[0069]
在喷砂条件“13”中,用维氏硬度大于800hv,粒度为0.2mm的钢砂对工件w进行了喷砂加工。喷砂加工完成的工件w的rz在电子束eb的照射前为63.02μm,在电子束eb的照射后降低至51.61μm。在该情况下,rz的降低率为18%。另一方面,rsm在电子束eb的照射前为781.94μm,在电子束eb的照射后增加至1136.86μm。
[0070]
在喷砂条件“14”中,用维氏硬度大于800hv,粒度为0.2mm的钢砂对工件w进行了喷砂加工。喷砂加工完成的工件w的rz在电子束eb的照射前为38.16μm,在电子束eb的照射后降低至24.31μm。在该情况下,rz的降低率为36%。另一方面,rsm在电子束eb的照射前为496.27μm,在电子束eb的照射后增加至1311.28μm。
[0071]
在喷砂条件“15”中,用维氏硬度大于800hv,粒度为0.2mm的钢砂对工件w进行了喷砂加工。喷砂加工完成的工件w的rz在电子束eb的照射前为49.53μm,在电子束eb的照射后降低至38.95μm。在该情况下,rz的降低率为21%。另一方面,rsm在电子束eb的照射前为852.99μm,在电子束eb的照射后增加至1195.85μm。
[0072]
在喷砂条件“16”中,用维氏硬度大于800hv,粒度为0.2mm的钢砂对工件w进行了喷砂加工。喷砂加工完成的工件w的rz在电子束eb的照射前为32.90μm,在电子束eb的照射后降低至16.18μm。在该情况下,rz的降低率为51%。另一方面,rsm在电子束eb的照射前为299.65μm,在电子束eb的照射后增加至1248.80μm。
[0073]
如图6所示,在喷砂条件“2”~“16”下喷砂加工完成的工件w的电子束eb的照射后的rz处于16.18μm~51.61μm的范围内。与此相对,仅进行电子束eb的照射的未经喷砂加工处理的工件w的电子束eb的照射后的rz为139.75μm。因此,确认了通过对进行了喷砂加工的工件w的表面照射电子束eb,能够使工件w的表面更平滑。
[0074]
并且,基于图6的结果,确认了电子束eb的照射前的rsm与基于电子束eb的照射引起的rz的降低率的相关性。图7是表示rsm与rz的降低率的相关性的分布图。横轴是电子束eb的照射前的rsm,纵轴是rz的降低率。在图7中,根据喷砂条件,分类成以下6类并示出数据:无喷砂(喷砂条件“1”)、用钢丸进行的喷砂加工(喷砂条件“5”~“9”)、用钢砂进行的喷砂加工后的rz不足40μm(喷砂条件“9”、“16”)、用钢砂进行的喷砂加工后的rz为40μm~50μm(喷砂条件“10”、“15”)、用钢砂进行的喷砂加工后的rz为50μm~60μm(喷砂条件“2”、“3”、“11”、“12”)、以及用钢砂进行的喷砂加工后的rz为60μm以上。
[0075]
如图7所示那样,确认了当rsm变小时rz的降低率上升的相关关系。而且,确认了为了使rz的降低率实现20%以上,需要满足喷砂加工完成且rsm不足770.80μm的条件。另外,具有与未经喷砂处理的工件w的rsm相同程度的rsm的喷砂加工完成的工件w(喷砂条件“3”、“4”、“6”)与未经喷砂处理的工件w相比,均为2倍以上的rz降低率。由此可推测,喷砂加工后的表面在本次评价的rsm以外的参数中,被控制为容易通过电子束熔融的形状。
[0076]
[表面的截面观察]
[0077]
图8是电子束照射的前后的工件的截面观察结果。图8的(a)~(e)是电子束eb的照射前的工件w的截面观察结果。图8的(a)是未经喷砂处理的工件w的观察结果(喷砂条件“1”),图8的(b)、(d)是喷砂加工完成的工件w的观察结果(喷砂条件“12”)。图8的(d)是图8的(b)的放大图。图8的(c)、(e)是喷砂加工完成的工件w的观察结果(喷砂条件“16”)。图8的(e)是图8的(c)的放大图。如图8的(a)所示那样,在未经喷砂处理的工件w中,确认了100μm以下的微小的凹凸以及大于100μm的凹凸。与此相对,如图8的(b)~(e)所示那样,在喷砂加工完成的工件w中,不存在大于100μm的凹凸。因此,确认了通过喷砂加工去除大于100μm的凹凸,实现了平坦化。另外,如图8的(d)、(e)所示那样,在喷砂加工完成的工件w的表面确认到20μm左右的裂纹。
[0078]
图8的(f)~(h)是进行电子束eb的照射后的截面观察结果。图8的(f)是对图8的(a)所涉及的工件w照射电子束eb后的观察结果。图8的(g)是对图8的(b),(d)所涉及的工件w照射电子束eb后的观察结果。图8的(h)是对图8的(c)、(e)所涉及的工件w照射电子束eb后的观察结果。如图8的(f)所示那样,通过电子束eb照射,去除在电子束eb照射前确认到的100μm以下的微小的凹凸。另一方面,即使照射了电子束eb,大于100μm的凹凸也未完全去除,而残留。由此,确认了电子束eb的照射不能高效地去除大于100μm的凹凸。与此相对,如图8的(g)、(h)所示那样,喷砂加工完成的工件w通过电子束照射而极其平坦化。确认了图8的(b)~(e)所示那样的喷砂加工完成的表面由于不存在大于100μm的凹凸,所以可以说具有容易通过电子束熔融的形状。
[0079]
根据以上,确认了喷砂加工能够去除电子束eb的照射不能去除的大于100μm的凹凸。即,确认了喷砂加工能够将表面控制为容易通过电子束熔融的形状。因此,确认了在进行喷砂加工后进行电子束eb的照射的表面处理方法能够高效地使工件w的表面平滑。另外,确认了电子束eb的照射能够去除由喷砂加工引起的裂纹。