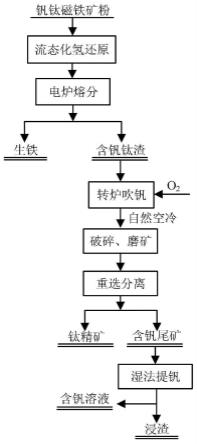
1.本发明涉及钒钛磁铁矿处理技术领域,更具体地说,本发明涉及一种流态化氢还原-电炉熔分综合处理钒钛磁铁矿的方法。
背景技术:2.钒钛磁铁矿被世界各国公认为是重要的战略资源,其主要成分中的铁、钒、钛等有价金属,广泛应用于钢铁制造、航空航天、医疗军事等领域,综合利用价值极高。我国钒钛磁铁资源储量约为300亿吨,位居世界第三;其中攀西地区钒钛磁铁矿储量约为100亿吨,约占全国铁矿储量的20%、占全国钒储量的62%、占全国钛储量的90%。钒钛磁铁矿既是钢铁行业又是有色行业的重要战略资源,共扼两大行业,实现其高效开发与综合利用意义重大。
[0003]“高炉-转炉法”是目前国内钒钛磁铁精矿冶炼分离的主流工艺。其具体工艺流程为,将钒钛磁铁精矿造块后送入高炉冶炼,焦炭和喷煤作为还原剂和燃料。在冶炼过程中钒氧化物部分被还原进入铁水,成为含钒铁水;含钒铁水经转炉吹炼,分离成钒渣和半钢。钒渣通过湿法浸出工艺提钒,半钢再经过转炉处理得到钢水。钛则进入高炉渣中形成高钛炉渣(w(tio2)》20%),无法回收利用。“高炉-转炉法”能有效地回收钒钛磁铁矿中的铁和部分钒,具有技术成熟、生产效率高、产能巨大等优点。
[0004]
在当今倡导节能减排和环境友好发展的时代背景下,传统的“高炉-转炉法”工艺的弊端日趋明显。钒钛磁铁矿“高炉-转炉法”存在工艺流程长、能耗高、对焦炭资源的依赖程度大以及难以进一步提高钒有价组元的利用率、无法实现钛元素的回收与利用等明显弊端。此外,在冶炼过程中,由于炉渣中tio2的存在,常导致冶炼过程泡沫渣严重、铁损严重,造成冶炼困难,难以实现炉渣的利用,使得钛资源无法回收,故导致钒钛磁铁矿的综合利用率低。
[0005]
为此,我们提出了一种流态化氢还原-电炉熔分综合处理钒钛磁铁矿的方法来解决上述问题。
[0006]
发明新型内容
[0007]
为了克服现有技术的上述缺陷,本发明的实施例提供一种流态化氢还原-电炉熔分综合处理钒钛磁铁矿的方法,以解决上述背景技术中提出的问题。
[0008]
为实现上述目的,本发明提供如下技术方案:一种流态化氢还原-电炉熔分综合处理钒钛磁铁矿的方法,具体包括如下步骤:
[0009]
步骤一:还原,将粒度≤1mm的钒钛磁铁精矿粉置于流化床层内,首先从床层底部引入一定体积的保护性气体,在排净床层内空气的同时,并使得物料处于良好的流化状态后;预热至一定反应温度时,通入还原性气体,开始进行流态化氢还原,得到具有高金属化率的还原产物;
[0010]
步骤二:熔分,将所得还原物料和氧化钙混合均匀,制成碱性熔分物料,将其置于电炉中;在一定的熔分条件下进行分离,熔分过程中通入一定体积的保护性气体,最终生成生铁和含钒钛渣;
[0011]
步骤三:吹钒,将含钒钛渣经转炉吹钒,自然空冷至室温,使得钒元素主要以v2o5的形式存在、而钛元素主要以tio2的形式赋存于渣中,其中tio2结晶粒度增大,有利于后续钛精矿的选别分离;
[0012]
步骤四:钛精矿的选别分离,将自然空冷的含钒钛渣,经破碎-磨矿工艺后制成一定粒度的粉料,使得tio2充分解离;然后将粉料置于重力分选设备中进行分离富集,所得精矿为tio2精矿,尾矿为含钒尾矿;
[0013]
步骤五:酸浸,将含钒尾矿经酸性浸出,在一定的浸出条件下,获得含钒溶液(v5+)和浸出渣,浸出渣经水洗烘干,作为水泥添加剂使用;最终实现了铁钒钛的有效分离与利用,提高了钒钛磁铁矿的综合利用率,为实现其高效开发利用提供技术支撑。
[0014]
在一个优选地实施方式中,步骤一中所述钒钛磁铁精矿粉的铁品位tfe45-60%,按质量百分比含feo 5-15%,tio25-20%,v2o50.2-2%,sio21.5-10%,al2o31.5-10%,cao 0.05-1.5%,mgo 0.5-10%,p《0.05%,s《0.006%。
[0015]
在一个优选地实施方式中,所述步骤一中的保护性气体为氮气,其流量为500-1000ml/min,所述还原性气体为氢气与氮气组成的混合气体,混合气体中氢气的体积百分比≥60%,气体流量为800-1100ml/min;所述步骤二熔分过程中所用保护性气体为氩气,气体流量为1000-2000ml/min;熔分所得生铁中fe的回收率≥90%,含钒钛渣自然空冷滞留时间为≥5h。
[0016]
在一个优选地实施方式中,步骤一中所述钒钛磁铁精矿粉料在流化床层内加热温度为750-900℃,还原时间为20-40min,钒钛磁铁矿流态化氢还原产物的金属化率≥80%;步骤二中所述还原物料和氧化钙混合制得的碱性熔分物料,其二元碱度(按质量百分比计算)为:r=w(cao)/w(sio2)=1.0-1.5;碱性熔分物料进行电炉熔分时,熔分温度为1400-1600℃,熔分时间≥40min。
[0017]
在一个优选地实施方式中,步骤四中所述含钒钛渣粒度磨细至小于0.074mm的部分占总质量的60%-90%,所用重选设备设置为摇床,最终获得钛精矿中tio2的回收率≥46%;所述步骤五中硫酸浓度≥10%、浸出时间≥2d、浸出温度20-50℃、液固比2:1-3:1,最终获得v的回收率≥60%。
[0018]
在一个优选地实施方式中,还包括任意一项所述的一种流态化氢还原-电炉熔分综合处理钒钛磁铁矿的重力分选设备,包括重力分选机本体1和位于上料口2两侧的侧壳体3,所述重力分选机本体1的顶端连接有上料口2,所述重力分选机本体1的两侧开设均开设有连接通孔17,所述重力分选机本体1的内部安装有筛选组件,所述筛选组件的下方开设有斜撑块21,所述重力分选机本体1对应斜撑块21的侧壁开设有第一出口22,所述重力分选机本体1位于筛选组件一侧的位置处开设有第二出口23,所述筛选组件的上方安装有滞留组件,所述上料口2的内部开设有曝气内腔19,所述曝气内腔19的内部安装有曝气组件;
[0019]
所述筛选组件包括位于重力分选机本体1内部的振筛滤板14,所述振筛滤板14的两端部上下方对称设置有与重力分选机本体1的内侧壁相铰接的斜挡块15,所述振筛滤板14的两端部伸入均连接有穿过摆动块18的连接通孔17。
[0020]
在一个优选地实施方式中,所述连接通孔17的横截面设置成梯形,较短的平面朝向重力分选机本体1内部,所述振筛滤板14的端部伸入至连接通孔17内部,所述振筛滤板14的中部位置处通过转轴与重力分选机本体1的侧壁转动连接,所述振筛滤板14的两端部上
下侧壁对应斜挡块15端部的位置处开设有弧状凹槽20,所述斜挡块15的端部形状设置设置成与弧状凹槽20相适配的弧状。
[0021]
在一个优选地实施方式中,所述曝气组件包括位于曝气内腔19内部的转接箱体5和位于上料口2一侧的鼓气泵4,所述鼓气泵4和转接箱体5之间通过管道相连通,所述转接箱体5的顶端线性阵列分布有若干个曝气管6,所述曝气管6与转接箱体5相连通。
[0022]
在一个优选地实施方式中,所述转接箱体5的内部安装有第一转轴8和第二转轴11,第一转轴8和第二转轴11与上料口2的内侧壁转动连接,所述转接箱体5的顶端安装有若干个与曝气管6相连通的密封箱体7,所述密封箱体7的上下端部均开设有开口,所述第一转轴8和第二转轴11上下设置并分布在密封箱体7下方,所述第一转轴8外部线性设置有与曝气管6数量相同的间歇遮挡组件,所述间歇遮挡组件包括四个圆周分布在第一转轴8外侧的弧形挡板9,所述第一转轴8的外部等距安装与曝气管6数量相同的传动齿轮10,所述传动齿轮10与所述弧形挡板9间隔设置,所述第二转轴11的两端部对应传动齿轮10的位置处均安装有十字凸轮12,所述十字凸轮12与传动齿轮10相适配。
[0023]
在一个优选地实施方式中,所述滞留组件包括对称安装在重力分选机本体1两侧壁的输风管16,所述输风管16的端部安装有可以更换的滤风网26,所述输风管16的内部安装有风扇25,所述风扇25等距分布有若干个风扇25,所述重力分选机本体1的侧壁对应输风管16的位置处开设有至少一个透气孔27,所述输风管16与所述曝气内腔19通过透气孔27相连通。
[0024]
本发明的技术效果和优点:
[0025]
1、通过本发明设计的工艺,与现有技术相比,针对传统“高炉-转炉法”处理钒钛磁铁矿存在的明显弊端。可以提高钒钛磁铁矿的综合利用回收率。本发明能够直接处理细粒级粉矿、还原效率高、热交换好、环境污染小、并且能够有效的分离与回收主要成分中的铁、钒、钛等有价元素。其具体为,首先利用流态化氢还原技术对钒钛磁铁行预还原金属化率≥80%,然后将预还原产物进行电炉熔分,分离生铁和含钒钛渣;含钒钛渣经转炉吹钒后自热缓慢变冷,经“破碎-磨矿-重选”分离后获得钛精矿tio2和含钒尾矿;含钒尾矿采用酸性浸出提钒,最后获得含钒溶液和浸出渣,浸出渣作为水泥添加剂。因此,该方法极大的提高了钒钛磁铁矿的综合利用率;
[0026]
2、通过重力分选机的整体结构,与现有技术相比,通过筛选组件、曝气组件和滞留组件的相互配合,使得物料在筛选组件的你凹面停留的时间更长,同时物料在振筛滤板14表面进行滚动和跳动,从而更进一步的提高筛选组件对物料的筛选效果,并且两侧的曝气组件间隔式振动从而使得振筛滤板14在重力分选机本体1内部做左右摆动,更进一步提高筛选效果。
附图说明
[0027]
图1为本发明提出的流态化氢还原-电炉熔分综合处理钒钛磁铁矿方法路线图。
[0028]
图2为本发明提出的重力分选设备的整体结构示意图。
[0029]
图3为本发明提出的重力分选设备去掉侧壳体后的结构示意图。
[0030]
图4为本发明提出的曝气组件的结构示意图。
[0031]
图5为本发明提出的转接箱体内部结构的示意图。
[0032]
图6为本发明提出曝气组件的竖截面剖视图。
[0033]
图7为本发明图6的截断示意图。
[0034]
图8为本发明图6中a处结构放大图。
[0035]
图9为本发明提出的重力分选机本体剖视结构示意图。
[0036]
附图标记为:1、重力分选机本体;2、上料口;3、侧壳体;4、鼓气泵;5、转接箱体;6、曝气管;7、密封箱体;8、第一转轴;9、弧形挡板;10、传动齿轮;11、第二转轴;12、十字凸轮;13、伺服电机;14、振筛滤板;15、斜挡块;16、输风管;17、连接通孔;18、摆动块;19、曝气内腔;20、弧状凹槽;21、斜撑块;22、第一出口;23、第二出口;24、中隔板;25、风扇;26、滤风网;27、透气孔。
具体实施方式
[0037]
下面将结合本发明实施例中的附图,对本发明实施例中的技术方案进行清楚、完整地描述,显然,所描述的实施例仅仅是本发明一部分实施例,而不是全部的实施例。基于本发明中的实施例,本领域普通技术人员在没有做出创造性劳动前提下所获得的所有其他实施例,都属于本发明保护的范围。
[0038]
实施例1
[0039]
如附图1所示,本实施例提供了一种流态化氢还原-电炉熔分综合处理钒钛磁铁矿的方法,具体包括如下步骤:
[0040]
步骤一:还原,将粒度≤1mm的钒钛磁铁精矿粉置于流化床层内,首先从床层底部引入一定体积的保护性气体,在排净床层内空气的同时,并使得物料处于良好的流化状态后;预热至一定反应温度时,通入还原性气体,开始进行流态化氢还原,得到具有高金属化率的还原产物,
[0041]
其中,所述钒钛磁铁精矿粉的铁品位tfe 45-60%,按质量百分比含feo5-15%,tio25-20%,v2o50.2-2%,sio21.5-10%,al2o31.5-10%,cao0.05-1.5%,mgo 0.5-10%,p《0.05%,s《0.006%,保护性气体为氮气,其流量为500-1000ml/min,还原性气体为氢气与氮气组成的混合气体,混合气体中氢气的体积百分比≥60%,气体流量为800-1100ml/min;钒钛磁铁精矿粉料在流化床层内加热温度为750-900℃,还原时间为20-40min,钒钛磁铁矿流态化氢还原产物的金属化率≥80%;
[0042]
步骤二:熔分,将所得还原物料和氧化钙混合均匀,制成碱性熔分物料,将其置于电炉中;在一定的熔分条件下进行分离,熔分过程中通入一定体积的保护性气体,最终生成生铁和含钒钛渣,
[0043]
步骤二熔分过程中所用保护性气体为氩气,气体流量为1000-2000ml/min;熔分所得生铁中fe的回收率≥90%,含钒钛渣自然空冷滞留时间为≥5h;还原物料和氧化钙混合制得的碱性熔分物料,其二元碱度(按质量百分比计算)为:r=w(cao)/w(sio2)=1.0-1.5;碱性熔分物料进行电炉熔分时,熔分温度为1400-1600℃,熔分时间≥40min;
[0044]
步骤三:吹钒,将含钒钛渣经转炉吹钒,自然空冷至室温,使得钒元素主要以v2o5的形式存在、而钛元素主要以tio2的形式赋存于渣中,其中tio2结晶粒度增大,有利于后续钛精矿的选别分离;
[0045]
步骤四:钛精矿的选别分离,将自然空冷的含钒钛渣,经破碎-磨矿工艺后制成一
定粒度的粉料,使得tio2充分解离;然后将粉料置于重力分选设备中进行分离富集,所得精矿为tio2精矿,尾矿为含钒尾矿;
[0046]
其中,含钒钛渣粒度磨细至小于0.074mm的部分占总质量的60%-90%,所用重选设备设置为摇床,最终获得钛精矿中tio2的回收率≥46%;
[0047]
步骤五:酸浸,将含钒尾矿经酸性浸出,在一定的浸出条件下,获得含钒溶液(v5+)和浸出渣,浸出渣经水洗烘干,作为水泥添加剂使用;最终实现了铁钒钛的有效分离与利用,提高了钒钛磁铁矿的综合利用率,为实现其高效开发利用提供技术支撑,
[0048]
所述步骤五中硫酸浓度≥10%、浸出时间≥2d、浸出温度20-50℃、液固比2:1-3:1,最终获得v的回收率≥60%。
[0049]
实施例2
[0050]
本实施例提供一种重力分选设备,如附图2-9所示,适用于实施例1中提供的流态化氢还原-电炉熔分综合处理钒钛磁铁矿的方法,包括重力分选机本体1和位于上料口2两侧的侧壳体3,重力分选机本体1的顶端连接有上料口2,通过上料口2将需要分选的含钒钛渣装入重力分选机本体1中,重力分选机本体1的两侧开设均开设有连接通孔17,重力分选机本体1的内部安装有筛选组件,筛选组件的下方开设有斜撑块21,重力分选机本体1对应斜撑块21的侧壁开设有第一出口22,重力分选机本体1位于筛选组件一侧的位置处开设有第二出口23,筛选组件的上方安装有滞留组件,上料口2的内部开设有曝气内腔19,曝气内腔19的内部安装有曝气组件,重力分选机本体1内部其他与分选相关的零部件均采用现有重力分选装置中的常规技术即可,在此不过多赘述,附图中也不做展示,利用筛选组件使得输入的物料进行更高精度的筛选,利用曝气组件使得筛选组件工作,并利用滞留组件使得在筛选组件上方的物料停留时间更长;
[0051]
筛选组件包括位于重力分选机本体1内部的振筛滤板14,振筛滤板14的两端部上下方对称设置有与重力分选机本体1的内侧壁相铰接的斜挡块15,振筛滤板14的两端部伸入均连接有穿过摆动块18的连接通孔17,当摆动块18受到气体推动时,在推力作用下,使得摆动块18向上倾斜,摆动块18带动振筛滤板14向上倾斜,从而使得振筛滤板14表面的物料会进行滚动,继而使得物料在振筛滤板14表面进行振动筛选脱离,使得筛选效果更好,筛选速率更高。
[0052]
具体的,连接通孔17的横截面设置成梯形,较短的平面朝向重力分选机本体1内部,当摆动块18转动时,由于摆动块18转动的角度会大于振筛滤板14转动角度,所以横截面为梯形的摆动块18会更方便摆动块18和振筛滤板14的倾斜,振筛滤板14的端部伸入至连接通孔17内部,振筛滤板14的中部位置处通过转轴与重力分选机本体1的侧壁转动连接,当振筛滤板14被一侧的摆动块18带动倾斜时,花由于振筛滤板14中部被固定,所以振筛滤板14会在重力分选机本体1内部围绕着中间位置的转动做摆动,振筛滤板14的两端部上下侧壁对应斜挡块15端部的位置处开设有弧状凹槽20,斜挡块15的端部形状设置设置成与弧状凹槽20相适配的弧状,当振筛滤板14不摆动时,两个斜挡块15可以适配的卡合在振筛滤板14的上下两个侧壁,使得振筛滤板14表面的物料与连接通孔17分隔开来,当振筛滤板14向上摆动时,上方的斜挡块15会被振筛滤板14带动向上转动,同时斜挡块15的端部滑出弧状凹槽20外面,将物料向另一侧推动,当振筛滤板14回复至原来位置时,上方的斜挡块15复位,并使得端部进入弧状凹槽20中,从而继续将连接通孔17与物料分隔开,同时,另一端部的斜
挡块15会滑向靠近连接通孔17的位置处,并在振筛滤板14复位时滑动回复至原来位置,从而不断的对连接通孔17进行阻挡,使得连接通孔17与重力分选机本体1颞部的物料分隔开。
[0053]
进一步的,曝气组件包括位于曝气内腔19内部的转接箱体5和位于上料口2一侧的鼓气泵4,鼓气泵4和转接箱体5之间通过管道相连通,转接箱体5的顶端线性阵列分布有若干个曝气管6,曝气管6与转接箱体5相连通,摆动块18的内部设置成一个空槽,曝气管6喷出的气体会喷向摆动块18内部的空槽,之后推动这摆动块18向上移动,之后处于凹槽中的气体会逸散向上方,曝气管6内部的气体会推动摆动块18向上移动,当曝气管6内部的气体停止喷射时,摆动块18则在重力的作用下复位,同时两侧的曝气组件是间隔喷气的,从而使得振筛滤板14在重力分选机本体1内部不断的摇摆,进而使得振筛滤板14上方的物料不断的运动,同时由于振筛滤板14不断的摆动,振筛滤板14表面也会产生一定的震动,进而使得滚动的物料会在振筛滤板14上方跳动,从而更进一步的增强对物料的筛选效果。
[0054]
值得说明的是,转接箱体5的内部安装有第一转轴8和第二转轴11,第一转轴8和第二转轴11与上料口2的内侧壁转动连接,转接箱体5的顶端安装有若干个与曝气管6相连通的密封箱体7,密封箱体7的上下端部均开设有开口,第一转轴8和第二转轴11上下设置并分布在密封箱体7下方,第一转轴8外部线性设置有与曝气管6数量相同的间歇遮挡组件,间歇遮挡组件包括四个圆周分布在第一转轴8外侧的弧形挡板9,第一转轴8的外部等距安装与曝气管6数量相同的传动齿轮10,传动齿轮10与弧形挡板9间隔设置,第二转轴11的两端部对应传动齿轮10的位置处均安装有十字凸轮12,十字凸轮12与传动齿轮10相适配,通过伺服电机13控制第二转轴11转动,第二转轴11每转动四分之一圈,会带动十字凸轮12转动四分之一圈,进而带动传动齿轮10转动四分之一圈,并更进一步的带动第一转轴8转动四分之一圈,从而带动弧形挡板9转动四分之一圈,使得弧形挡板9外侧壁的弧面与密封箱体7下方的弧面相贴合,从而将密封箱体7进行遮挡,密封箱体7的下方开口被遮挡,曝气管6会停止喷射气体,其他转动的时间区间内,传动齿轮10离开密封箱体7的开口,从而使得密封箱体7下方的开口与转接箱体5连通从而使得曝气管6喷射气体,并且由于弧形挡板9外侧的弧面占据八分之一的圆面,所以十字凸轮12转动四分之一圆的时间区间内,有一半时间,弧形挡板9是对密封箱体7下方的开口进行遮挡,另一半时间,密封箱体7下方开口与转接箱体5相连通,实现间歇喷气的效果。
[0055]
值得注意的是,滞留组件包括对称安装在重力分选机本体1两侧壁的输风管16,输风管16的端部安装有可以更换的滤风网26,输风管16的内部安装有风扇25,风扇25等距分布有若干个风扇25,重力分选机本体1的侧壁对应输风管16的位置处开设有至少一个透气孔27,输风管16与曝气内腔19通过透气孔27相连通,逸散至摆动块18上方的气体通过透气孔27进而风扇25中,由于曝气内腔19内部气体较多,从而使得气体会从透气孔27中向输风管16外部流动,从而使得透气孔27带动风扇25抓大北农,继而形成涡流,并透过滤风网26吹向振筛滤板14上方,使得振筛滤板14上方因为振动产生的分成被吹向一边,同时,另一边的直流组件也输送涡流,相向的涡流会对称,在重力分选机本体1内部处于振筛滤板14上方的位置处产生更多的涡流,从而使得颗粒较小的物料在振筛滤板14上方更进一步做不规则的运动,并且停留的时间更长,使得对物料的分离效果更好,并且混乱的涡流会将粉尘带向第二出口23的位置处并从第二出口23中分离,从而使得物料的筛选效果更好,筛选出的物料成分更高。
[0056]
本发明工作原理:
[0057]
参照说明书附图2-9,首先将待筛选的物料通过上料口2加入重力分选机本体1内部,之后筛选设备工作,曝气组件间歇式喷射气体,两侧的曝气组件也间歇式的喷射气体,筛选组件中的振筛滤板14不断的左右摆动,表面更是产生一定的震动,大大提高筛选效果,同时曝气组件产生的气体通过滞留组件在振筛滤板14上方形成涡流并形成对冲,进一步排出随物料一起加入重力分选机本体1内部的粉尘,继而筛选出的物料的成分含量比例,同时利用涡流使跳起的物料的运动趋势改变,从而使得物料在振筛滤板14中停留时间更长,与振筛滤板14接触的速率增快并且不规则,从而减少在振筛滤板14表面堵塞的情况,进而提高筛选的效率。
[0058]
最后应说明的几点是:首先,在本技术的描述中,需要说明的是,除非另有规定和限定,术语“安装”、“相连”、“连接”应做广义理解,可以是机械连接或电连接,也可以是两个元件内部的连通,可以是直接相连,“上”、“下”、“左”、“右”等仅用于表示相对位置关系,当被描述对象的绝对位置改变,则相对位置关系可能发生改变;
[0059]
其次:本发明公开实施例附图中,只涉及到与本公开实施例涉及到的结构,其他结构可参考通常设计,在不冲突情况下,本发明同一实施例及不同实施例可以相互组合;
[0060]
最后:以上仅为本发明的优选实施例而已,并不用于限制本发明,凡在本发明的精神和原则之内,所作的任何修改、等同替换、改进等,均应包含在本发明的保护范围之内。