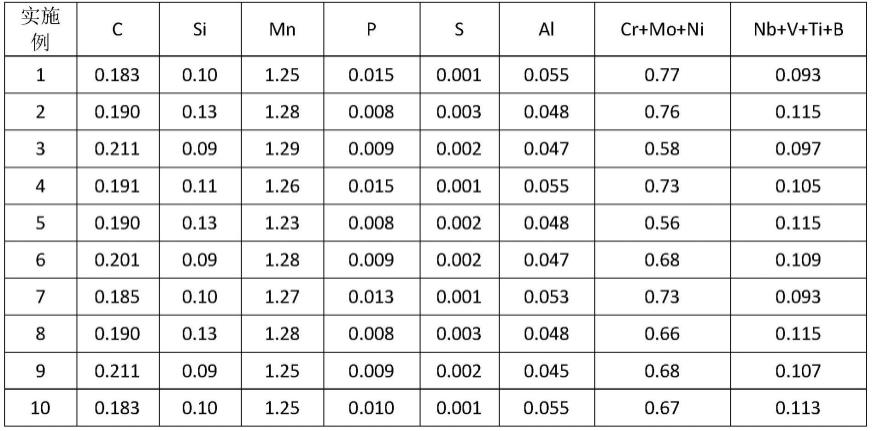
1.本发明属于黑色金属制造领域,主要涉及一种通过热处理工艺控制,保证屈服强度大于981mpa宽钢板平直度的制造技术。
背景技术:2.中厚板淬火线配置辊压式淬火机,其极限规格厚度与淬火机辊缝设计相关。一般中厚板淬火线的起始接料厚度≥8mm,钢板厚度再降低钢板的冷却质量受设备条件限制会发生急剧变化。淬火后的钢板板形会出现浪形、扭曲等缺陷。这些缺陷在后续的工序中均没有办法挽救。因此淬火工序理所当然的成为了整个淬火——回火热处理工序的瓶颈及难点。
3.目前,屈服强度高于700mpa的低合金钢板微观组织一般均采用马氏体强化。这是由于马氏体在冷却过程中的相变特性,其体积会显著长大。由于马氏体形成过程的不一致性及其在钢板不同位置的差异,导致钢板表面出现变形即不平度。这种现象终端用户的使用不利。
4.cn101597684a一种导板的热处理方法,公开一种导板的热处理方法,本发明要解决的技术问题是,提供一种导板的热处理方法,保证导板柔韧性,500mm内弯曲45
°
正常反弹不变形,在1000mm的距离内平整度小于0.2mm,整体硬度达hrc50
°±2°
。其实现不平度方式为:“将导板每20块夹在一起进行精整形,使平整度达到1000mm距离内小于0.2mm,最后将导板放入70kw井式回火炉,200℃回火1小时。”。其方法只能处理零件类钢板对于大尺寸的钢板则无法实施。
5.cn102676787a一种金属薄板淬火装置,公开一种金属薄板淬火装置,关键在于:所述装置包括具有升降机构的上部压辊和下部传送辊道,所述上部压辊与下部传送辊道为十字交叉布置,其中上部压辊为辊面带有沟槽的花辊,下部传送辊道的标高与热处理炉辊面标高一致。本发明采用与下部传送辊道十字交叉的上部压辊,能够抵抗金属薄板淬火变形,下部传送辊道的标高与热处理炉辊面标高一致使淬火金属板运送方便,而采用花辊的结构使得淬火金属板上表面的排水更加顺畅。此方法为设备控制类,无法就具体钢的生产提供工艺技术。
6.cn102953000a一种超高强度钢板及其制造方法,发明公开提供一种超高强度钢板及其制造方法,其成分:c 0.10%~0.20%、si 0.8%~1.5%、mn 1.00%~1.50%、nb 0.02%~0.06%、mo0.20%~0.40%、b 0.0005%~0.003%、ti 0.015%~0.03%、als 0.015%~0.045%,余为fe。其方法包括冶炼、连铸、轧制和热处理,板坯加热温度1220~1240℃,加热时间60~110秒/厘米;第一阶段轧制温度≥990℃;第二阶段开轧温度920~870℃,终轧温度800~850℃,变形量大于60%;轧后开冷温度730~780℃,返红温度600~700℃;淬火温度900~930℃,保温1.5~2.5分/毫米;回火温度200~300℃,保温3~5分/毫米。本发明钢板不含ni,成本较低,两阶段控轧后经离线淬火加低温回火即可获得屈服强度大于1100n/mm2,-40℃纵向低温韧性大于30j的超高强度钢板。此方法只提供钢板的工艺及
力学性能保障,对于成品的平直度则无要求。
7.本发明通过热处理工艺控制,通过淬火——回火——矫平工艺实现钢板全板面360度方向不平度小于4/1000mm。
技术实现要素:8.本发明在于克服现有技术存在的不足,提供一种在保证屈服强度大于981mpa且7mm厚的宽钢板经过辊压式淬火机淬火+回火,实现钢板每1000mm的平直度≤4mm的大宽厚比高强度钢及生产方法。
9.实现上述目的的措施:
10.一种大宽厚比高强度钢,其化学成分及其重量百分比含量如下:c:0.12~0.21%;si:0.06~0.13%;mn:1.17~1.53%;p≤0.010%;s≤0.002%;al:≤0.049%;cr+mo+ni:0.58~0.79%;nb+ti+v+b:0.07~0.10%;余量为fe及不可避免杂质。
11.优选地:cr+mo+ni的重量百分比含量在0.61~0.75%。
12.优选地:nb+ti+v+b的重量百分比含量在0.079~0.093%。
13.一种大宽厚比高强度钢的热处理方法,其在于以下步骤:
14.1)钢板经轧制、卷取后开卷;
15.2)对钢板按照厚度段进行无氧化分段加热:
16.当厚度在3至≤4.5mm时:
17.第i加热段加热速率控制在9.11~11.78℃/min;
18.第ii加热段加热速率控制在0.53~3.54℃/min;
19.均热段加热速率控制在0.08~0.84℃/min;且控制出炉温度在871~883℃;
20.当厚度在4.5至≤6.5mm时:
21.第i加热段加热速率控制在7.41~9.78℃/min;
22.第ii加热段加热速率控制在0.69~5.54℃/min;
23.均热段加热速率控制在0.58~1.14℃/min;且控制出炉温度在861~883℃;
24.当厚度在6.5至≤8.0mm时:
25.第i加热段加热速率控制在6.41~8.78℃/min;
26.第ii加热段加热速率控制在5.53~7.54℃/min;
27.均热段加热速率控制在0.98~1.44℃/min;且控制出炉温度在861~873℃;
28.3)在19.9~24.3m/min的速度范围内以其中任一速度进入淬火机;
29.4)进行淬火,在淬火速度为20~30℃/s下根据厚度段按照进行四个阶段进行淬火:
30.当厚度在3至≤4.5mm时:
31.第一阶段水流量控制在449~506m3/h,上下水量比控制在1.05~1.11;
32.第一阶段水流量控制在295~340m3/h,上下水量比控制在0.88~0.83;
33.第一阶段水流量控制在208~233m3/h,上下水量比控制在1.00~0.84;
34.以上三个阶段各段水压力均控制在0.75~0.78mpa;
35.第四阶段水量控制在480~510m3/h,上下水比控制在1.05~1.10,水压力控制在0.35~0.39mpa;
36.当厚度在4.5至≤6.5mm时:
37.第一阶段水流量控制在443~531m3/h,上下水量比控制在1.05~1.11;
38.第一阶段水流量控制在315~390m3/h,上下水量比控制在0.88~0.83;
39.第一阶段水流量控制在218~263m3/h,上下水量比控制在1.00~0.84;
40.以上三个阶段各段水压力均控制在0.75~0.78mpa;
41.第四阶段水量控制在480~510m3/h,上下水比控制在1.05~1.10,水压力控制在0.35~0.39mpa;
42.当厚度在6.5至≤8.0mm时:
43.第一阶段水流量控制在493~566m3/h,上下水量比控制在1.05~1.11;
44.第一阶段水流量控制在315~390m3/h,上下水量比控制在0.88~0.83;
45.第一阶段水流量控制在238~293m3/h,上下水量比控制在1.00~0.84;
46.以上三个阶段各段水压力均控制在0.75~0.78mpa;
47.第四阶段水量控制在480~510m3/h,上下水比控制再1.05~1.10,水压力控制在0.35~0.39mpa;
48.5)进行常规回火。
49.其在于:淬火后的钢板经过回火处理,工艺为加热温度558~619℃,保温时间2.5倍板厚,回火后自然冷却。
50.本发明中主要的杂质元素控制及主要工艺的作用及机理
51.本发明之所以控制cr+mo+ni:0.58~0.79%,优选地cr+mo+ni的重量百分比含量在0.61~0.75%,是由于cr、mo、ni均为强化奥氏体元素,在钢中起固溶强化作用。同时增加钢的淬透性。cr、mo、ni元素的复合添加有效提高钢的强度,同时保证在本钢中限制碳元素的过度添加影响钢的韧性。本发明采用此三种元素的添加充分考虑其合金价格成本,以成本较低的元素作为主要添加合金,配以其他合金在保证钢的性能基础上有效减低制造成本。
52.本发明之所以控制nb+ti+v+b:0.07~0.10%,优选地nb+ti+v+b在0.079~0.093%,是由此四种微合金化元素在钢中主要起弥散强化的作用,nb的添加还可以保证钢在轧制过程中起促进回复再结晶效果,减少轧制过程中的加工硬化。ti+b添加还可提高钢的淬透性,提高钢的强度。v添加在强化作用的基础上提高钢的回火稳定性,保证钢在此工艺条件下的强度和韧性匹配。由于是微合金化此钢中以nb为基础添加,b元素严格控制与ti的比例。此钢中优选四种微合金化元素的添加是保证钢中的微合金化元素形成有效的碳氮化物。以细质点的形态存在钢的晶粒内部,在后续的热处理过程中保证尺寸大小和颗粒数量。充分起到弥散强化的作用,而不降低钢的韧性。
53.本发明之所以对钢板按照厚度段进行无氧化分段加热,是根据传热原理而制定加热速率保证钢板的单位面积受热均匀。钢板的厚度不同相同的宽厚比条件下其表面积也不同。为保证受表面积及厚度影响的单位体积内的钢板受热均匀,本发明采取按厚度进行分段加热。
54.本发明之所以在淬火速度为20~30℃/s下,在四个阶段根据厚度段进行淬火,并控制四个阶段的上下水量比及水压,是由于钢板经过加热炉均匀化加热后,以恒定的速度进入淬火机。淬火机以20~30℃/s的冷却速度对钢板上下表面进行喷水冷却。淬火阶段分
为四个阶段:强冷固定段—粗调段—精调段—冷却降温段。前三个阶段由高压水进行控制,第四阶段由低压水控制。i阶段水流量493~566m3/h,ii阶段水流量315~390m3/h,iii阶段水流量238~293m3/h。各段上下水量比按i阶段1.05~1.11,ii阶段0.88~0.83,iii阶段1.00~0.84控制。高压段水压力0.75~0.78mpa。第四阶段水量按480~510m3/h,上下水比按1.30~1.15控制,低压段水压力0.35~0.39mpa。高压段各段的任务:i阶段大水量急速将钢板的表面温度降低,同时最大程度固定板形。设定大于1的水比使下表面与上表面有效冷却水量均匀;ii、iii阶段水量逐渐减少,同时水比降低是分阶段小幅度调整i阶段大水量过后钢板内部组织相变潜热释放引起的板形变化。i阶段与ii、iii阶段钢板上下表面的收缩相反,通过温度变化和组织变化结合调整钢板内部应力差,使钢板变形均匀。
55.本发明与现有技术相比,其通过准确控制钢板在无氧化加热炉的温度、时间;淬火机中高压水及低压水流量等参数;通过回火,以及矫直实现7mm厚度屈服强度≥981mpa,宽厚比为215~258的钢板全板面360度方向不平度不超过4mm/1000mm。
具体实施方式
56.下面对本发明予以详细描述:
57.表1为本发明各实施例及对比例的化学成分列表;
58.表2为本发明各实施例及对比例的主要工艺取值列表;
59.表3为经520℃回火后本发明各实施例及对比例的性能检测列表;
60.表4为淬火与回火后本发明各实施例及对比例的不平度检测列表。
61.本发明各实施例按照如下步骤生产:
62.1)钢板经轧制、卷取后开卷;
63.2)对钢板按照厚度段进行无氧化分段加热:
64.当厚度在3至≤4.5mm时:
65.第i加热段加热速率控制在9.11~11.78℃/min;
66.第ii加热段加热速率控制在0.53~3.54℃/min;
67.均热段加热速率控制在0.08~0.84℃/min;且控制出炉温度在871~883℃;
68.当厚度在4.5至≤6.5mm时:
69.第i加热段加热速率控制在7.41~9.78℃/min;
70.第ii加热段加热速率控制在0.69~5.54℃/min;
71.均热段加热速率控制在0.58~1.14℃/min;且控制出炉温度在861~883℃;
72.当厚度在6.5至≤8.0mm时:
73.第i加热段加热速率控制在6.41~8.78℃/min;
74.第ii加热段加热速率控制在5.53~7.54℃/min;
75.均热段加热速率控制在0.98~1.44℃/min;且控制出炉温度在861~873℃;
76.3)在19.9~24.3m/min的速度范围内以其中任一速度进入淬火机;
77.4)进行淬火,在淬火速度为20~30℃/s下根据厚度段按照进行四个阶段进行淬火:
78.当厚度在3至≤4.5mm时:
79.第一阶段水流量控制在449~506m3/h,上下水量比控制在1.05~1.11;
80.第一阶段水流量控制在295~340m3/h,上下水量比控制在0.88~0.83;
81.第一阶段水流量控制在208~233m3/h,上下水量比控制在1.00~0.84;
82.以上三个阶段各段水压力均控制在0.75~0.78mpa;
83.第四阶段水量控制在480~510m3/h,上下水比控制在1.05~1.10,水压力控制在0.35~0.39mpa;
84.当厚度在4.5至≤6.5mm时:
85.第一阶段水流量控制在443~531m3/h,上下水量比控制在1.05~1.11;
86.第一阶段水流量控制在315~390m3/h,上下水量比控制在0.88~0.83;
87.第一阶段水流量控制在218~263m3/h,上下水量比控制在1.00~0.84;
88.以上三个阶段各段水压力均控制在0.75~0.78mpa;
89.第四阶段水量控制在480~510m3/h,上下水比控制在1.05~1.10,水压力控制在0.35~0.39mpa;
90.当厚度在6.5至≤8.0mm时:
91.第一阶段水流量控制在493~566m3/h,上下水量比控制在1.05~1.11;
92.第一阶段水流量控制在315~390m3/h,上下水量比控制在0.88~0.83;
93.第一阶段水流量控制在238~293m3/h,上下水量比控制在1.00~0.84;
94.以上三个阶段各段水压力均控制在0.75~0.78mpa;
95.第四阶段水量控制在480~510m3/h,上下水比控制再1.05~1.10,水压力控制在0.35~0.39mpa;
96.5)进行常规回火。
97.表1本发明各实施例及对比例的化学成分列表(wt%)
[0098][0099]
表2本发明各实施例及对比例的主要工艺取值列表
[0100][0101]
续表2-1
[0102][0103][0104]
续表2-2
[0105][0106]
表3经520℃回火后本发明各实施例及对比例的性能检测列表
[0107][0108]
表4淬火与回火后本发明各实施例及对比例的不平度检测列表
[0109][0110]
从表3及表4可以看出通过准确控制钢板在无氧化加热炉的温度、时间;淬火机中高压水及低压水流量等参数;通过回火,以及矫直实现屈服强度大于等于981mpa钢板全板面360度方向不平度小于4mm/1000mm。
[0111]
具体实施方式仅为最佳例举,并非对本发明技术方案的限制性实施。