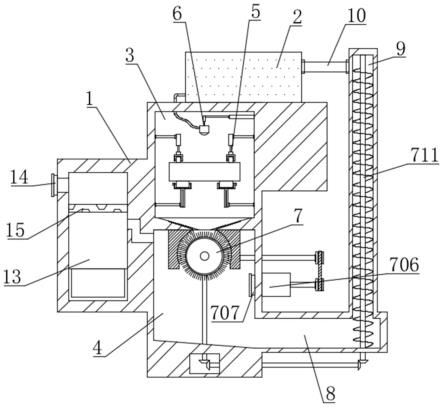
1.本发明涉及抛丸机技术领域,具体是一种智能化焊缝抛丸机。
背景技术:2.抛丸机指利用抛丸器抛出的高速弹丸清理或强化工件表面的机械设备,抛丸机能同时对铸件进行落砂、除芯和清理,也可用于锻压件、铝镁合金件、钣焊件等进行表面处理;焊缝是焊件经焊接后所形成的结合部分,目前在对筒状或管状加工件的焊缝进行处理时一般需要使用到抛丸机。
3.现有技术中通过抛丸机对焊缝进行处理时,需要先通过夹持结构固定住加工件,然后通过抛丸机对加工件的焊缝部位进行抛丸处理,但筒状或管状加工件的焊缝大都为圈状,在对一圈焊缝的整个处理过程中需要进行多次夹持和翻转加工件,加工效率低,操作辛苦,并且难以将丸料清洁和回收集于一体以实现丸料的循环使用,而且实际使用过程中难以对抛丸过程和丸料清洁过程进行综合分析以实现自动调节,智能化程度低。
4.针对上述的技术缺陷,现提出一种解决方案。
技术实现要素:5.本发明的目的在于提供一种智能化焊缝抛丸机,通过定位驱动组件对筒状或管状加工件进行有效承托和固定并实现抛丸过程中加工件的旋转,显著提高了焊缝抛丸操作效率,通过清洁回收组件将刷扫清洁、鼓风除尘清洁、丸料收集和丸料提升输送功能于一体并同步运行,功能多样,显著提高了使用效果,且通过将清料分析和诊断分析相结合,显著提高了设备的智能化程度,解决了现有技术加工效率低,操作辛苦,难以实现丸料的循环使用,以及难以对抛丸过程和丸料清洁过程进行综合分析以实现自动调节,智能化程度低的问题。
6.为实现上述目的,本发明提供如下技术方案:一种智能化焊缝抛丸机,包括抛丸机本体,所述抛丸机本体的顶部通过螺栓固定安装有丸料箱,所述抛丸机本体内开设有抛丸室和清洁室,且抛丸室位于清洁室的上方并通过下料斗与其相通,所述下料斗内设有接料板,所述抛丸室内设有抛丸器和定位驱动组件;所述抛丸机本体内设有清洁回收组件,所述清洁回收组件对下落的丸料进行清洁和回收;所述抛丸器包括喷丸头、横向推杆和升降推杆,所述横向推杆设置在抛丸室内,所述升降推杆连接横向推杆和喷丸头,且喷丸头与丸料箱通过喷丸管连接;所述抛丸机本体上安装有操控面板,且操控面板包括数据采集单元、处理器、清料分析单元、诊断调节单元和智能控制单元;数据采集单元采集到清料数据和诊断数据,并将清料数据和诊断数据发送至处理器;处理器生成回料的清料分析信号,并将清料分析信号和清料数据发送至清料分析单元;清料分析单元用于进行清料分析,生成快清信号或维清信号,并将快清信号或维清信号发送至处理器,处理器发出“快速清洁”或“维持现速”的控制指令并通过智能控制单元对清洁
回收组件的运转进行调节;处理器生成抛丸机的调节分析信号,并将调节分析信号和诊断数据发送至诊断分析单元;诊断分析单元用于进行调节分析,生成诊断判定信号,并将诊断判定信号发送至处理器,处理器发出调节指令并通过智能控制单元对抛丸过程进行调节。
7.进一步的,清料分析单元的清料分析过程具体如下:接收到接料板的受压值,并将接料板的受压值标记为syz;比较接料板的受压值syz和接料板的受压阈值syzi,当接料板的受压值syz≥接料板的受压阈值syzi,生成快清信号并将快清信号发送至处理器;当接料板的受压值syz<接料板的受压阈值syzi,继续进行下一步;接收到抛丸器的喷速值,并将抛丸器的喷速值标记为psz;基于接料板的受压值syz和抛丸器的喷速值psz进行分析,通过分析后获取到抛丸机的待清系数qlx;比较抛丸机的待清系数qlx和抛丸机的待清系数阈值qlxi,当抛丸机的待清系数qlx≥抛丸机的待清系数阈值qlxi,则生成快清信号并将快清信号发送至处理器;当抛丸机的待清系数qlx<抛丸机的待清系数阈值qlxi,则生成维清信号并将维清信号发送至处理器。
8.进一步的,诊断调节单元的调节分析过程具体如下:接收到抛丸器的抛距值,并将抛丸器的抛距值标记为pjz;其中,抛丸器的抛距值表示抛丸器与加工件之间的最短间距;接收到抛丸器的喷速值psz、抛丸器的抛距阈值范围和抛丸器的喷速阈值范围,并将抛丸器的抛距阈值范围和抛丸器的喷速阈值范围分别标记为pjzi和pszi;当抛丸器的喷速值psz≥喷速阈值范围pszi的最大值时,生成降速信号并将降速信号发送至处理器;当抛丸器的喷速值psz≤喷速阈值范围pszi的最小值时,生成升速信号并将升速信号发送至处理器;当抛丸器的抛距值pjz≥抛丸器的抛距阈值范围pjzi的最大值时,生成减距信号并将减距信号发送至处理器;当抛丸器的抛距值pjz≤抛丸器的抛距阈值范围pjzi的最小值时,生成加距信号并将加距信号发送至处理器;在抛丸器的喷速值psz∈抛丸器的喷速阈值范围pszi且抛丸器的抛距值pjz∈抛丸器的抛距阈值范围pjzi时,则基于抛丸器的喷速值psz和抛丸器的抛距值pjz进行分析,通过分析后获取到抛丸器的抛况系数ykx;比较抛丸器的抛况系数ykx与抛丸器的抛况系数阈值范围ykxi,当抛丸器的抛况系数ykx∈抛丸器的抛况系数阈值范围ykxi时,生成维运信号并将维运信号发送至处理器;当抛丸器的抛况系数ykx≥抛丸器的抛况系数阈值范围ykxi的最大值时,生成快转信号并将快转信号发送至处理器;当抛丸器的抛况系数ykx≤抛丸器的抛况系数阈值范围ykxi的最小值时,生成缓转信号并将缓转信号发送至处理器。
9.进一步的,所述定位驱动组件包括固定柱和下压气缸,所述固定柱通过第一可调杆安装在抛丸室内,且固定柱的顶部安装有驱动托轮;所述下压气缸通过第二可调杆安装在抛丸室内,且下压气缸的底端安装有下压轮;所述驱动托轮的两侧均设有辅助托轮,所述辅助托轮上安装有连接杆,所述连接杆通过斜杆与固定柱连接。
10.进一步的,所述固定柱内转动安装有竖直设置的螺杆,且螺杆上螺纹连接有螺套,所述连接杆上安装有推拉杆,所述推拉杆的另一端与螺套连接,且固定柱上对应开设有导
向口;所述固定柱内安装有辅助电机,且辅助电机的输出端与螺杆连接。
11.进一步的,所述下压轮的顶部安装有缓冲盒,所述缓冲盒内滑动安装有缓冲板,所述下压气缸延伸入缓冲盒内并与缓冲板连接,且缓冲板的底部安装有与缓冲盒连接的弹簧。
12.进一步的,所述清洁回收组件包括清洁毛刷辊、清洁电机、吹扫风机和螺旋提料轴,所述抛丸机本体上开设有回料通道和提料通道,所述回料通道位于提料通道的下方并连通清洁室和提料通道,所述提料通道的顶端通过回收管与丸料箱连通,且清洁室的底部朝回料通道的方向向下倾斜;所述清洁毛刷辊设置于下料斗的下方,且清洁毛刷辊的两侧设有与其相配合的弧形毛刷座,所述清洁电机通过电机座固定安装在抛丸机本体上,且清洁电机的输出端安装有与清洁毛刷辊连接的旋转轴,所述螺旋提料轴竖直设置于提料通道内,且螺旋提料轴向下延伸入回料通道中,所述吹扫风机安装在抛丸机本体上,所述清洁室内安装有与吹扫风机连接的吹扫管,且吹扫风机通过驱动轴驱动,所述抛丸机本体远离吹扫风机的一侧设有排灰通道;所述旋转轴通过锥齿轮啮合连接第一传动轴和第二传动轴,所述第二传动轴通过锥齿轮与第三传动轴啮合连接,所述第三传动轴通过锥齿轮传动连接螺旋提料轴,所述第一传动轴通过传动带传动连接驱动轴。
13.进一步的,所述抛丸机本体内开设有粉尘腔,且粉尘腔内通过螺栓固定安装有滤网,所述排灰通道连通粉尘腔和清洁室,且排灰通道与粉尘腔的连通处位于滤网的下方,所述抛丸机本体上安装有与粉尘腔连通的排风管,且排风管与粉尘腔的连通处位于滤网的上方。
14.进一步的,当处理器接收到降速信号时,发出“降速指令”至智能控制单元,智能控制单元使抛丸器的喷丸速度降低;当处理器接收到升速信号时,发出“升速指令”至智能控制单元,智能控制单元使抛丸器的喷丸速度升高;当处理器接收到减距信号时,发出“减距指令”至智能控制单元,智能控制单元使抛丸器下降以减小抛距;当处理器接收到加距信号时,发出“加距指令”至智能控制单元,智能控制单元使抛丸器上升以增大抛距;当处理器接收到维运信号时,发出“维持现状指令”至智能控制单元,智能控制单元使加工件保持现有旋转速度;当处理器接收到快转信号时,发出“快转指令”至智能控制单元,智能控制单元使加工件的旋转速度加快;当处理器接收到缓转信号时,发出“缓转指令”至智能控制单元,智能控制单元使加工件的旋转速度减缓。
15.与现有技术相比,本发明的有益效果是:1、本发明中,通过定位驱动组件不仅能够对筒状或管状加工件进行有效承托和固定,保证抛丸操作过程的稳定,还能够在抛丸过程中使筒状或管状加工件进行旋转,实现对圈状焊缝的有效处理,不需人工对加工件进行多次翻转和夹持,显著提高了焊缝抛丸操作的操作效率;2、本发明中,通过清洁回收组件不仅能够对使用过程中下落的丸料进行有效清洁,还能够对清洁后的丸料进行收集和输送,实现丸料的循环使用,且清洁回收组件将刷扫清洁、鼓风除尘清洁、丸料收集和丸料提升输送功能于一体并同步运行,功能多样,显著提高了使用效果;
3、本发明中,通过清料分析单元进行清料分析并生成快清信号或维清信号,当处理器接收到快清信号时生成“快速清洁”的控制指令,处理器接收到维清信号时发出“维持现速”的控制指令,此时通过智能控制单元对清洁回收组件的运转进行自动调节,起到提高清洁效率和清洁效果,以及起到降低能耗和节约能源的作用;通过诊断调节单元进行综合分析以实现抛距调节、喷速调节和加工件转速调节,显著提高了抛丸效率和抛丸效果,实现了自动化调节,且清料分析和诊断分析相结合,显著提高了设备的智能化程度。
附图说明
16.为了便于本领域技术人员理解,下面结合附图对本发明作进一步的说明;图1为本发明的整体结构示意图;图2为本发明中抛丸器的结构示意图;图3为图1中定位驱动组件的放大图;图4为本发明中位驱动组件的左视示意图;图5为本发明中固定柱、驱动托轮、辅助托轮的连接示意图;图6为本发明中下压气缸、缓冲盒和下压轮的结构示意图;图7为图1中清洁回收组件的局部放大图;图8为本发明中旋转轴、第一传动轴、第二传动轴、第三传动轴、陆轩提料轴、驱动轴的连接示意图;图9为本发明中清洁毛刷辊和旋转轴的连接示意图(俯视);图10为本发明的系统框图。
17.附图标记:1、抛丸机本体;2、丸料箱;3、抛丸室;4、清洁室;5、定位驱动组件;6、抛丸器;7、清洁回收组件;8、回料通道;9、提料通道;10、回收管;11、下料斗;12、接料板;13、粉尘腔;14、排风管;15、滤网;501、固定柱;502、驱动托轮;503、下压轮;504、下压气缸;505、辅助托轮;506、连接杆;507、斜杆;508、推拉杆;509、第一可调杆;510、第二可调杆;511、辅助电机;512、螺杆;513、螺套;514、导向口;515、缓冲盒;516、缓冲板;517、弹簧;61、喷丸头;62、喷丸管;63、横向推杆;64、升降推杆;701、清洁毛刷辊;702、旋转轴;703、清洁电机;704、弧形毛刷座;705、排灰通道;706、吹扫风机;707、吹扫管;708、第一传动轴;709、驱动轴;710、传动带;711、螺旋提料轴;712、第二传动轴;713、第三传动轴。
具体实施方式
18.下面将结合本发明实施例中的附图,对本发明实施例中的技术方案进行清楚、完整地描述,显然,所描述的实施例仅仅是本发明一部分实施例,而不是全部的实施例。基于本发明中的实施例,本领域普通技术人员在没有做出创造性劳动前提下所获得的所有其他实施例,都属于本发明保护的范围。
19.实施例一:如图1-9所示,本发明提出的一种智能化焊缝抛丸机,包括抛丸机本体1,抛丸机本体1的顶部通过螺栓固定安装有丸料箱2,丸料箱2内储存有抛丸用的丸料,抛丸机本体1内开设有抛丸室3和清洁室4,且抛丸室3位于清洁室4的上方并通过下料斗11与其相通,下料斗11内设有接料板12,抛丸室3内设有抛丸器6,具体的,抛丸器6包括喷丸头61、横向推杆63
和升降推杆64,横向推杆63设置在抛丸室3内,升降推杆64连接横向推杆63和喷丸头61,且喷丸头61与丸料箱2通过喷丸管62连接,丸料箱2内的丸料通过喷丸管62和喷丸头61喷出,以实现抛丸操作,且喷丸管62上设有控制喷丸速度的阀门;横向推杆63用于调节喷丸头61的横向位置,升降推杆64用于调节喷丸头61的高度以改变其与加工件之间的间距,横向推杆63和升降推杆64为电动推杆,横向推杆63和升降推杆64由电力驱动以进行伸长或缩短;抛丸室3内设有定位驱动组件5,定位驱动组件5包括固定柱501和下压气缸504,固定柱501通过第一可调杆509安装在抛丸室3内,第一可调杆509的长度可进行调节,且固定柱501的顶部安装有驱动托轮502;下压气缸504通过第二可调杆510安装在抛丸室3内,且下压气缸504的底端安装有下压轮503,驱动托轮502承托住上方的加工件,下压轮503下压住加工件,在驱动托轮502和下压轮503的共同作用下实现对加工件的固定;驱动托轮502的两侧均设有辅助托轮505,辅助托轮505上安装有连接杆506,连接杆506通过斜杆507与固定柱501连接;辅助托轮505托住加工件的两侧,进一步提高对加工件的固定效果,且驱动托轮502通过电力驱动,驱动托轮502转动时,由于摩擦力作用而使加工件随之进行旋转,实现加工件的稳定顺利转动,有助于对圈状焊缝的有效处理;进一步而言,固定柱501内转动安装有竖直设置的螺杆512,且螺杆512上螺纹连接有螺套513,连接杆506上安装有推拉杆508,推拉杆508的另一端与螺套513连接,且固定柱501上对应开设有导向口514,固定柱501内安装有辅助电机511,且辅助电机511的输出端与螺杆512连接;当对不同尺寸的筒状或管状加工件进行加工时,通过辅助电机511使螺杆512进行转动,从而使螺套513上升或下降,最终通过推拉杆508的作用而使两组辅助托轮505之间的夹角改变,以实现对不同尺寸加工件的辅助固定;优选的,下压轮503的顶部安装有缓冲盒515,缓冲盒515内滑动安装有缓冲板516,下压气缸504延伸入缓冲盒515内并与缓冲板516连接,且缓冲板516的底部安装有与缓冲盒515连接的弹簧517,弹簧517处于压缩状态并第缓冲盒515施加向下的压力,从而使下压轮503向下紧压住加工件,在起到压紧功能的同时还起到缓冲作用,有助于避免因刚性挤压而导致加工件难以进行转动;抛丸机本体1内设有清洁回收组件7,清洁回收组件7对下落的丸料进行清洁和回收;具体而言,清洁回收组件7包括清洁毛刷辊701,抛丸机本体1上开设有回料通道8和提料通道9,回料通道8位于提料通道9的下方并连通清洁室4和提料通道9,提料通道9的顶端通过回收管10与丸料箱2连通,且清洁室4的底部朝回料通道8的方向向下倾斜;清洁毛刷辊701设置于下料斗11的下方,下料斗11中的丸料聚集在清洁毛刷辊701的上部,且清洁毛刷辊701的两侧设有与其相配合的弧形毛刷座704,清洁电机703通过电机座固定安装在抛丸机本体1上,且清洁电机703的输出端安装有与清洁毛刷辊701连接的旋转轴702;在抛丸过程中,抛丸过程中产生的丸料落入下方并聚集于下料斗11中,启动清洁电机703,清洁电机703使旋转轴702进行转动,旋转轴702带动清洁毛刷辊701进行转动,在清洁毛刷辊701的转动过程中带动上方的丸料运动,在清洁毛刷辊701和弧形毛刷座704的共同作用下将丸料上的金属粉尘刷扫下来,实现丸料的清洁和输送;进一步而言,吹扫风机706安装在抛丸机本体1上,清洁室4内安装有与吹扫风机706连接的吹扫管707,且吹扫风机706通过驱动轴709驱动,在清洁过程中,驱动轴709带动吹扫风机706工作,吹扫风机706通过吹扫管707向清洁室4内进行鼓风,从而将刷扫下来的粉尘吹走,以及对丸料进行鼓风清洁,通过将刷扫清洁和鼓风清洁相结合以提高对丸料的
清洁效果,抛丸机本体1远离吹扫风机706的一侧设有排灰通道705,鼓风清洁过程中产生的粉尘空气通过排灰通道705排出;螺旋提料轴711竖直设置于提料通道9内,且螺旋提料轴711向下延伸入回料通道8中,清洁后的丸料进入回料通道8中,螺旋提料轴711进行旋转并对回料通道8中的丸料进行提升,最终将清洁后的丸料输送至丸料箱2中,实现丸料的回收和循环利用;优选的,旋转轴702通过锥齿轮啮合连接第一传动轴708和第二传动轴712,旋转轴702在转动时会带动第一传动轴708和第二传动轴712进行转动,第二传动轴712通过锥齿轮与第三传动轴713啮合连接,第二传动轴712在进行转动时会带动第三传动轴713进行转动,第三传动轴713通过锥齿轮传动连接螺旋提料轴711,第三传动轴713会带动螺旋提料轴711进行转动,第一传动轴708通过传动带710传动连接驱动轴709,第一传动轴708会带动驱动轴709进行转动,不需设置多个驱动设备来分别带动对应的部件单独运转,降低了设备成本和运行成本,且保证了各个部件的同步运转,使用效果好。
20.实施例二:如图10所示,本实施例与实施例1的区别在于,抛丸机本体1上安装有操控面板,且操控面板包括数据采集单元、处理器、清料分析单元、诊断调节单元和智能控制单元;数据采集单元采集到清料数据,并将清料数据发送至处理器;其中,清料数据包括接料板12的受压值(受压值为接料板12上方所承载的丸料重量,由重力传感器检测得到)和抛丸器6的喷速值(喷速值为抛丸时丸料的喷出速度,由喷速传感器检测得到),处理器生成回料的清料分析信号,并将清料分析信号和清料数据发送至清料分析单元;清料分析单元用于进行清料分析,清料分析过程具体如下:步骤s1:接收到接料板的受压值,并将接料板12的受压值标记为syz;步骤s2:比较接料板12的受压值syz和接料板12的受压阈值syzi,当接料板12的受压值syz≥接料板12的受压阈值syzi,生成快清信号并将快清信号发送至处理器;当接料板12的受压值syz<接料板的受压阈值syzi,继续进行下一步;步骤s3:接收到抛丸器6的喷速值,并将抛丸器6的喷速值标记为psz;基于接料板12的受压值syz和抛丸器6的喷速值psz进行分析,通过公式并代入上述数据进行计算分析,通过分析后获取到抛丸机的待清系数qlx;其中,k1、k2为预先设置的权重系数,k1>k2>0,优选的,k1=3.628,k2=1.917;步骤s4:比较抛丸机的待清系数qlx和抛丸机的待清系数阈值qlxi,待清系数阈值由操作人员预先设置,且待清系数阈值的取值大于零;当抛丸机的待清系数qlx≥抛丸机的待清系数阈值qlxi,代表此时下料斗11内聚集的丸料数量多且单位时间内丸料的喷出量大,需要加快对丸料的清洁并输出,则生成快清信号并将快清信号发送至处理器;当抛丸机的待清系数qlx<抛丸机的待清系数阈值qlxi,代表此时下料斗11内聚集的丸料数量少且单位时间内丸料的喷出量小,无需加快对丸料的清洁并输出,则生成维清信号并将维清信号发送至处理器;当处理器接收到快清信号时,生成“快速清洁”的控制指令,此时通过智能控制单元对清洁回收组件7的运转进行调节,即此时使旋转轴702的转速提升,从而加快清洁毛刷辊701的转速,提高对丸料的清洁效率,避免下料斗11内的丸料持续聚集;处理器接收到维清信号时,发出“维持现速”的控制指令,此时通过智能控制单元对清洁回收组件7的运转进
行调节,即此时使旋转轴702的转速降低,从而减慢清洁毛刷辊701的转速,起到降低能耗和节约能源的作用。
21.实施例三:如图10所示,本实施例与实施例1、实施例2的区别在于,操控面板还包括诊断调节单元,数据采集单元采集到诊断数据,并诊断数据发送至处理器;其中,诊断数据包括抛丸器6的抛距值和抛丸器6的喷速值;处理器生成抛丸机的调节分析信号,并将调节分析信号和诊断数据发送至诊断分析单元;诊断分析单元用于进行调节分析,调节分析过程具体如下:步骤x1:接收到抛丸器6的抛距值,并将抛丸器6的抛距值标记为pjz;其中,抛丸器6的抛距值表示抛丸器6与下方的加工件之间的最短间距(通过抛丸器6上安装的测距传感器检测得到);接收到抛丸器6的喷速值psz、抛丸器6的抛距阈值范围和抛丸器6的喷速阈值范围,并将抛丸器6的抛距阈值范围和抛丸器6的喷速阈值范围分别标记为pjzi和pszi;抛丸器6的抛距阈值范围和抛丸器6的喷速阈值范围均由操作人员预先设置,且抛丸器6的抛距阈值范围和抛丸器6的喷速阈值范围均大于零;步骤x2:当抛丸器6的喷速值psz≥喷速阈值范围pszi的最大值时,生成降速信号并将降速信号发送至处理器;当处理器接收到降速信号时,发出“降速指令”至智能控制单元,智能控制单元使抛丸器6的喷丸速度降低;当抛丸器6的喷速值psz≤喷速阈值范围pszi的最小值时,生成升速信号并将升速信号发送至处理器;当处理器接收到升速信号时,发出“升速指令”至智能控制单元,智能控制单元使抛丸器6的喷丸速度升高;步骤x3:当抛丸器6的抛距值pjz≥抛丸器6的抛距阈值范围pjzi的最大值时,生成减距信号并将减距信号发送至处理器;当处理器接收到减距信号时,发出“减距指令”至智能控制单元,智能控制单元使抛丸器6下降以减小抛距;当抛丸器6的抛距值pjz≤抛丸器6的抛距阈值范围pjzi的最小值时,生成加距信号并将加距信号发送至处理器;当处理器接收到加距信号时,发出“加距指令”至智能控制单元,智能控制单元使抛丸器6上升以增大抛距;步骤x4:在抛丸器6的喷速值psz∈抛丸器6的喷速阈值范围pszi且抛丸器6的抛距值pjz∈抛丸器6的抛距阈值范围pjzi时,则基于抛丸器6的喷速值psz和抛丸器6的抛距值pjz进行分析,通过公式并代入上述数据进行计算分析,通过分析后获取到抛丸器6的抛况系数ykx;其中,为预设修正因子,的取值为0.368;h1、h2为操作人员预先设置的比例系数,0<h1<h2,优选的,h1=1.327,h2=1.864;由上述分析公式可知,抛况系数的数值大小与抛距值pjz成正比,与喷速值psz成反比,抛况系数的数值越大,则代表抛丸效率越高,抛况系数的数值越小,则代表效率越低;步骤x5:比较抛丸器6的抛况系数ykx与抛丸器6的抛况系数阈值范围ykxi,当抛丸器6的抛况系数ykx∈抛丸器6的抛况系数阈值范围ykxi时,生成维运信号并将维运信号发送至处理器;当抛丸器6的抛况系数ykx≥抛丸器6的抛况系数阈值范围ykxi的最大值时,代表此时抛丸效率高,可适当加快加工件的转速,生成快转信号并将快转信号发送至处理器;当抛丸器6的抛况系数ykx≤抛丸器6的抛况系数阈值范围ykxi的最小值时,代表此时抛丸效率低,可适当降低加工件的转速,生成缓转信号并将缓转信号发送至处理器;步骤x6:当处理器接收到维运信号时,发出“维持现状指令”至智能控制单元,智能
控制单元使驱动托轮502的转速不变,从而使加工件保持现有旋转速度;当处理器接收到快转信号时,发出“快转指令”至智能控制单元,智能控制单元使驱动托轮502的转速加快,从而使加工件的旋转速度加快;当处理器接收到缓转信号时,发出“缓转指令”至智能控制单元,智能控制单元使驱动托轮502的转速减慢,从而使加工件的旋转速度降低,保证对圈状焊缝每个位置处的有效处理;通过诊断调节单元进行综合分析以实现抛距调节、喷速调节和加工件转速调节,分析结果更加准确,调节效果好,显著提高了抛丸效率和抛丸效果,且不需人工进行控制和调节,实现了自动化调节,智能化程度高,操作简单。
22.实施例四:如图1所示,本实施例与实施例1、实施例2、实施例3的区别在于,抛丸机本体1内开设有粉尘腔13,且粉尘腔13内通过螺栓固定安装有滤网15,排灰通道705连通粉尘腔13和清洁室4,且排灰通道705与粉尘腔13的连通处位于滤网15的下方,抛丸机本体1上安装有与粉尘腔13连通的排风管14,且排风管14与粉尘腔13的连通处位于滤网15的上方;在实际的使用过程中,清洁过程中,通过鼓风作用使粉尘脱离丸料,粉尘空气通过排灰通道705进入粉尘腔13内,滤网15对粉尘空气进行过滤,过滤后的空气通过排风管14排出,金属粉尘聚集于粉尘腔13的底部,不仅有助于降低粉尘空气对附近环境和操作人员带来的危害,还实现了对金属粉尘的收集,使用效果好。
23.本发明的工作原理:使用时,通过定位驱动组件5不仅能够对筒状或管状加工件进行有效承托和固定,保证抛丸操作过程的稳定,还能够在抛丸过程中使筒状或管状加工件进行旋转,实现对圈状焊缝的有效处理,不需人工对加工件进行翻转,以及不需人工多次进行夹持操作,显著提高了焊缝抛丸操作的操作效率,操作简单,操作过程省时省力;通过清洁回收组件7不仅能够对使用过程中下落的丸料进行有效清洁,还能够对清洁后的丸料进行收集,以及能够将收集的丸料同步输送至丸料箱2,实现丸料的循环使用,清洁回收组件7将刷扫清洁、鼓风除尘清洁、丸料收集和丸料提升输送功能于一体并同步运行,功能多样,显著提高了使用效果;清料分析单元进行清料分析并获取到抛丸机的待清系数,比较待清系数和抛丸机的待清系数阈值,通过比较分析生成快清信号或维清信号并发送至处理器,当处理器接收到快清信号时,生成“快速清洁”的控制指令,此时通过智能控制单元对清洁回收组件7的运转进行调节,加快清洁毛刷辊701的转速,提高对丸料的清洁效率,避免下料斗11内的丸料持续聚集,处理器接收到维清信号时,发出“维持现速”的控制指令,此时通过智能控制单元对清洁回收组件7的运转进行调节,从而减慢清洁毛刷辊701的转速,起到降低能耗和节约能源的作用;诊断分析单元进行调节分析,通过诊断调节单元进行综合分析以实现抛距调节、喷速调节和加工件转速调节,分析结果更加准确,调节效果好,显著提高了抛丸效率和抛丸效果,且不需人工进行控制和调节,实现了自动化调节,操作简单,清料分析和诊断分析相结合,显著提高了设备的智能化程度。
24.上述公式均是去量纲取其数值计算,公式是由采集大量数据进行软件模拟得到最接近真实情况的一个公式,公式中的预设参数由本领域的技术人员根据实际情况进行设置。以上内容仅仅是对本发明结构所作的举例和说明,所属本技术领域的技术人员对所描述的具体实施例做各种各样的修改或补充或采用类似的方式替代,只要不偏离发明的结构或者超越本权利要求书所定义的范围,均应属于本发明的保护范围。
25.在本说明书的描述中,参考术语“一个实施例”、“示例”、“具体示例”等的描述意指结合该实施例或示例描述的具体特征、结构、材料或者特点包含于本发明的至少一个实施例或示例中。在本说明书中,对上述术语的示意性表述不一定指的是相同的实施例或示例。而且,描述的具体特征、结构、材料或者特点可以在任何的一个或多个实施例或示例中以合适的方式结合。
26.以上公开的本发明优选实施例只是用于帮助阐述本发明。优选实施例并没有详尽叙述所有的细节,也不限制该发明仅为的具体实施方式。显然,根据本说明书的内容,可作很多的修改和变化。本说明书选取并具体描述这些实施例,是为了更好地解释本发明的原理和实际应用,从而使所属技术领域技术人员能很好地理解和利用本发明。本发明仅受权利要求书及其全部范围和等效物的限制。