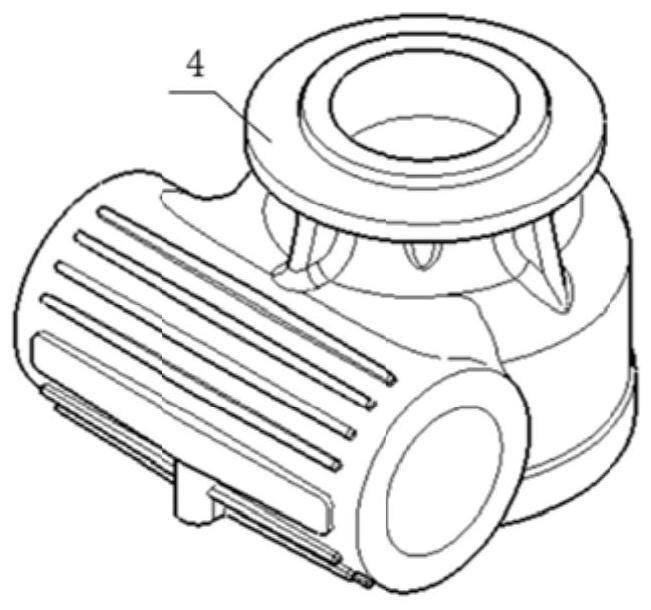
1.本发明属于铝合金低压铸造技术领域,尤其是一种爪型铝合金壳体的浇铸技术,具体地说是一种铝合金壳体爪型周向等分式浇注系统及其浇注方法。
背景技术:2.铝合金具有质量轻、耐腐蚀、导热性能好等优点,近年来在轻量化技术上得到广泛应用。传统的壳体多由球墨铸铁采用重力铸造而成,重量较大且容易出现铸造缺陷。壳体类铸件是机械传动系统中的关键部件之一,它的质量好坏直接影响整机的性能和使用寿命。
3.低压铸造是一种先进的反重力铸造技术,使用较低的气压将合金液体压入浇注系统以及型腔,并在一定压力下补缩成型,能够解决传统重力铸造中金属液平稳充型与凝固补缩之间的矛盾,具有充型速度与压力可控,充型过程平稳,金属液补缩能力强,使铸件组织致密、力学性能良好等优点,广泛应用于生产汽车缸体、壳体及轮毂等零件。浇注系统的设计是低压铸造工艺设计的重要内容之一,其作用是引导金属液平稳充型补缩,使铸件符合顺序凝固原则,浇注系统设计的成功与否直接影响铸件的成型质量。
4.本发明中的铝合金壳体(如图1所示),体积较大,平均壁厚大且不均匀,在铸造过程中,壁薄部分容易提前凝固,不利于合金液体补缩,壁厚部分容易形成热结,尤其在采用传统浇注系统时,铸件型腔底部厚大部分与内浇道的接触面积较大,最后凝固且散热较慢,在实际生产中极易产生缩松缩孔等缺陷,降低合金性能且影响生产效率。
技术实现要素:5.本发明的目的是针对体积较大、平均壁厚大且不均匀的铝合金壳体在铸造过程中壁薄部分容易提前凝固,不利于合金液体补缩,壁厚部分容易形成热结,尤其在采用传统浇注系统时,铸件型腔底部厚大部分与内浇道的接触面积较大,最后凝固且散热较慢,在实际生产中极易产生缩松缩孔等缺陷,降低合金性能且影响生产效率的问题,发明一种结构简单、充型平稳、能提高铸件毛坯质量的铝合金壳体爪型周向等分式浇注系统及其浇注方法。
6.本发明的技术方案之一是:
7.一种铝合金壳体爪型周向等分式浇注系统,其特征在于:在铸件型腔底部平面的对称轴上设置浇注系统;浇注系统包括圆柱形升液管、圆锥形漏斗状横浇道、阶梯型内浇道;所述横浇道的一端与所述升液管连接,另一端与所述内浇道连接,内浇道与所述铸件型腔底部的圆形型腔连接。
8.所述升液管设置成圆柱形,根据充型所需铝液体积计算升液管的半径以及高度,即升液管圆柱体积大于或等于充型所需铝液体积。
9.所述横浇道设置为圆锥形漏斗状,锥面与底部夹角为150
°
,上下高度差为铸件上下高度差的1/3。
10.所述内浇道为沿圆形型腔圆周方向设置的椭圆柱形浇道,且上下成阶梯状,设置多个内浇道,为呈环形均匀分布在壳体底部圆形型腔面上的爪型结构,所述内浇道上下高
度差与横浇道上下高度差的比值为1:1.6,内浇道上下阶梯高度差的比值为3:2,上下阶梯横截面积的比值为1:4,且内浇道上下阶梯连接处设置斜面及倒角。
11.本发明的技术方案之二是:
12.一种铝合金壳体爪型周向等分式浇注系统的浇注方法,其包括以下步骤,浇注时,通过较小的升液压力下将熔化的合金液体引入铝合金壳体成型模具的升液管,所述合金液体沿升液管注入横浇道,从横浇道进入内浇道,经过内浇道注入所述铝合金壳体成型模具型腔的底侧。所述合金液体在一定的充型压力下从型腔内上升并填充型腔,最后在较大的保压压力下完成铸件的凝固及补缩。
13.所述铝合金壳体铸件的升液压力为20kpa,充型压力为40kpa,保压压力为60kpa。
14.所述铝合金壳体铸件的浇注温度为720℃,模具预热温度为280℃。
15.本发明的有益效果是:
16.本发明公开了一种铝合金壳体爪型周向等分式浇注系统,为满足铸件凝固过程中建立良好的补缩条件,以及合金液体平稳充型原则,本发明采用底注式低压铸造浇注系统,根据铝合金壳体铸件的成型特点,合理设置升液管、横浇道、内浇道的形状和尺寸。升液管通过较小的压力进行导流和补缩,圆锥形漏斗状横浇道可以保证合金液体沿横浇道平稳上升。阶梯型内浇道区别于传统带有坡度的内浇道,可以保证铝液沿铸件底部型腔垂直上升,减少铝液与型腔壁的冲击,使合金液体平稳上升并充满型腔,保证铸件充型过程平稳有效,利于凝固补缩,从而减少铸件生产过程中的缩松缩孔缺陷,降低铸件毛坯废品率。同时呈爪型周向等分式内浇道相较于传统环状内浇道,可有效减少铸件底部与内浇口的接触面积,大大缩短凝固时间。
17.本发明通过设定升液、充型和保压压力,保证合金液体具备合理的充型速度,速度过快易使得合金液体飞溅或卷气,过慢则易使得充型时发生冷隔、浇不足。通过设定浇注温度,避免铸件在铸造过程中产生冷隔、氧化夹渣和疏松等缺陷。
18.本发明具有较强的适用性,能够有效提高铸件的成型质量和生产效率,且结构简单,容易推广。
附图说明
19.图1是本发明中铸件的立体图。
20.图2是本发明中铸件和浇注系统的总成示意图。
21.图3是本发明中横浇道的示意图。
22.图4是本发明中内浇道的示意图。
23.图5是本发明中的铸造工艺图。
具体实施方式
24.为使本发明实现的技术手段、创作特征、达成目的与功效易于理解,下面结合附图和具体实施方式,进一步阐述本发明。
25.参照图1-图5。
26.一种铝合金壳体爪型周向等分式浇注系统,在铸件型腔底部平面的对称轴上设置浇注系统;铝合金壳体的结构如图1所示,浇注系统如图2示,它包括圆柱形升液管1、圆锥形
漏斗状横浇道2、阶梯型内浇道3;所述横浇道的一端与所述升液管1连接,另一端与所述内浇道3连接,内浇道3与所述铸件型腔底部的圆形型腔连接。升液管1用于将熔化的合金液体引入铝合金壳体成型模具中,所述升液管1垂直设置,所述升液管1设置于所述铝合金壳体成型模具型腔正下方,所述升液管1上端连接横浇道2,所述横浇道2设置为圆锥形漏斗状(如图2所示),在整个型腔的中心位置,可以保证合金液体沿圆锥形横浇道均匀上升。所述横浇道2连接如图3所示的内浇道3,所述内浇道3为沿圆形型腔圆周方向设置的椭圆柱形浇道,且上下成阶梯状,共设置四个内浇道,为使浇铸液均匀分布在壳体底部圆形型腔面上的爪型结构中,内浇道上下阶梯连接处设置斜面及倒角,如图4所示。同时呈爪型周向等分式内浇道相较于传统环状内浇道,可有效减少铸件底部与内浇口的接触面积,大大缩短凝固时间。本发明中的阶梯型内浇道区别于传统带有坡度的内浇道,可以保证铝液沿铸件底部型腔垂直上升,减少铝液与型腔壁的冲击,使合金液体平稳上升并充满型腔,保证铸件充型过程平稳有效,利于凝固补缩,从而减少铸件生产过程中的缩松缩孔缺陷,降低铸件毛坯废品率。
27.采用铝合金壳体爪型周向等分式浇注系统的浇注方法,包括以下步骤,浇注时,通过较小的升液压力下将熔化的合金液体引入铝合金壳体成型模具的升液管1,所述合金液体沿升液管1注入横浇道2,从横浇道2进入内浇道3,经过四个内浇道3注入所述铝合金壳体成型模具型腔4的底侧。所述合金液体在一定的充型压力下从型腔4内上升并填充型腔,最后在较大的保压压力下完成铸件的凝固及补缩。如图5所示。
28.浇注温度设计:浇注温度是铸造过程中非常关键的工艺参数,设计合理的浇注温度,可以避免铸件铸造过程中产生冷隔、氧化夹渣和疏松缺陷。铸件的浇注温度取决于铸件截面大小和合金凝固温度范围,该合金液的熔化温度范围为580-640℃,浇注温度范围为700-740℃,根据数值模拟及生产试制,选定铸件浇注温度为720℃,模具预热温度为280℃。
29.浇注过程控制:通过设定升液、充型和保压压力,保证合金液体具备合理的充型速度,速度过快易使得合金液体飞溅或卷气,过慢则易使得充型时发生冷隔、浇不足。通过设定浇注温度,避免铸件在铸造过程中产生冷隔、氧化夹渣和疏松等缺陷。根据帕斯卡原理及经验公式,计算各阶段的加压压力。
30.其中升液压力:
31.p1=μ1ρgh1(pa)
32.式中:μ1为升液过程的流动阻力系数;ρ为金属液的密度,kg/m3;g为重力加速度,m/s2;h1为升液高度,m。
33.充型压力:
34.p2=p1+μ2ρgh2(pa)
35.式中:μ2为充型阻力系数,h2为型腔的高度,m。
36.保压压力:
37.p3=kp238.式中:k为增压系数,一般取1.3-2.0。
39.因此设置升液压力p1为20kpa,升液时间t1为3s;充型压力p2为40kpa,充型时间t
2-t1为12s;增压时间t
3-t2为3s;保压压力p3为60kpa,保压时间t
4-t3为300s;卸压时间t
5-t4为2s。
40.为满足铸件凝固过程中建立良好的补缩条件,以及合金液体平稳充型原则,本发明采用底注式低压铸造浇注系统,根据铝合金壳体铸件的成型特点,合理设置升液管、横浇道、内浇道的形状和尺寸。升液管通过较小的压力进行导流和补缩,圆锥形漏斗状横浇道2可以保证合金液体沿横浇道平稳上升。阶梯型内浇道3区别于传统带有坡度的内浇道,可以保证铝液沿铸件底部型腔垂直上升,减少铝液与型腔壁的冲击,使合金液体平稳上升并充满型腔,保证铸件充型过程平稳有效,利于凝固补缩,从而减少铸件生产过程中的缩松缩孔缺陷,降低铸件毛坯废品率。同时呈爪型周向等分式内浇道相较于传统环状内浇道,可有效减少铸件底部与内浇口的接触面积,大大缩短凝固时间。
41.以上所述具体阐释了本发明的基本原理、主要特征和优点。所应理解的是,本发明不受上述实施例的限制,上述实施例和说明书中描述的只是说明本发明的原理,在不脱离本发明精神和范围的前提下,本发明还会有各种变化和改进,这些变化和改进都落入要求保护的本发明范围之内。本发明要求保护范围由所附的权利要求书及其等效物界定。
42.本发明未涉及部分与现有技术相同或可采用现有技术加以实现。