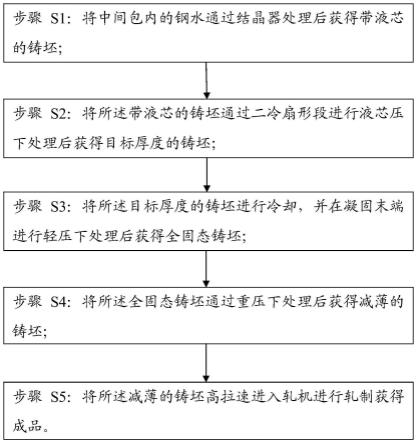
1.本发明涉及薄板坯连铸连轧技术领域,尤其涉及一种薄板坯连铸连轧在线减薄铸坯的生产方法。
背景技术:2.薄板坯连铸连轧无头轧制技术将传统流程分散的连铸、加热和热连轧等工序集约为一体,流程更简约高效。由于铸坯增厚、拉坯速度提高、钢通量大幅度提高,实现了单流连铸机和连轧机的匹配生产。无头轧制技术2009年初在意大利阿维迪的esp生产线上首次工业化应用,2013年我国的日照钢铁开始引进阿维迪的无头轧制技术,随着无头轧制技术优势的不断体现,展现出越来越广阔的发展前景。
3.从薄板坯连铸连轧无头轧制工艺流程考虑,为了实现铸坯的直接轧制,达到大量节能的目的,需要将铸坯的厚度限制在连轧所能接受的范围内,这样才能充分发挥连铸连轧在技术经济上的优势。而从连铸角度考虑,生产薄板坯会给结晶器和浸入式水口带来负担。如果结晶器内腔厚度太小,不利于浸入式水口的插入,而且结晶器内的熔池也太小,增加了钢水注流对凝固坯壳的冲刷,加剧了结晶器内钢液面的波动,增加了浇铸的难度,所以结晶器内腔的厚度不应太小。为了增加结晶器内腔尺寸、改善结晶器流场、提高浸入式水口寿命,同时为轧机提供直接连续轧制的薄板坯,连铸坯在线减薄技术一直被广泛采用。目前mccr生产线采用了液芯压下和动态轻压下的融合技术,即在结晶器出口采用液芯压下,在凝固末端采用动态轻压下。
4.但本技术在实现本技术的过程中,发现上述技术至少存在如下技术问题:
5.mccr的液芯压下和动态轻压下的融合技术,达到了在线减薄铸坯和改善内部质量同时不影响扇形段寿命。但由于无头产线对金属秒流量铸机拉速的要求,限制了铸坯厚度的进一步增加,增加了铸机浇铸的难度,同时影响了产线产能的发挥。
技术实现要素:6.本技术实施例通过提供一种薄板坯连铸连轧在线减薄铸坯的生产方法,解决了现有无头产线由于拉速限制无法继续提高铸坯厚度的技术问题。
7.本技术实施例提供了一种薄板坯连铸连轧在线减薄铸坯的生产方法,包括:
8.将中间包内的钢水通过结晶器处理后获得带液芯的铸坯;
9.将所述带液芯的铸坯通过二冷扇形段进行液芯压下处理后获得目标厚度的铸坯;
10.将所述目标厚度的铸坯进行冷却,并在凝固末端进行轻压下处理后获得全固态铸坯;
11.将所述全固态铸坯通过重压下处理后获得减薄的铸坯;
12.将所述减薄的铸坯高拉速进入轧机进行轧制获得成品。
13.进一步地,所述结晶器采用漏斗型结晶器,所述结晶器出口厚度为100-160mm,以生产宽度为1100-1600mm的板坯。
14.进一步地,所述结晶器的宽面冷却水量为6000-8600l/min,所述结晶器的窄面冷却水流量为400-600l/min,冷却水流速为10-13m/s。
15.进一步地,将所述带液芯的铸坯通过二冷扇形段进行液芯压下处理后获得目标厚度的铸坯包括:
16.所述带液芯的铸坯出所述结晶器后进入二冷扇形段,在0、1、2号扇形段对所述带液芯的铸坯进行液芯压下,总压下量为5-20mm。
17.进一步地,所述扇形段带有位置传感器,通过位置控制将铸坯压到目标厚度,其中,所述的零号扇形段入口位置保持与所述结晶器出口位置一致,只在出口位置进行压下。
18.进一步地,将所述目标厚度的铸坯进行冷却,并在凝固末端进行轻压下处理后获得全固态铸坯包括:
19.所述带液芯铸坯通过弧形段,经过连续弯曲和矫直进入水平段,在二次冷却水的不断冷却下,使所述带液芯铸坯的液芯逐减消失;
20.在所述带液芯铸坯内部液相完全消失前,将凝固末端通过扇形段进行轻压下处理获得全固态铸坯。
21.进一步地,所述扇形段内二次冷却为气雾冷却,二冷比水量为1.5-2.5l/kg,二冷气压力为1.1-4.0bar,经过二次冷却,铸坯出扇形段后厚度为90-135mm。
22.进一步地,所述凝固末端的轻压下量为3-5mm,通过2-3个扇形段完成,其中,所述凝固末端轻压下时固液分率为0.6-0.8之间。
23.进一步地,将所述全固态铸坯通过重压下处理后获得减薄的铸坯包括:
24.所述全固态铸坯出扇形段后,经过重压下装置后进行固态压下,所述的铸机出扇形段后正常运行速度为4.5-6m/min。
25.进一步地,铸机为直弧型,所述铸机半径为5.5-6.0m,冶金长度为20-40m。
26.本技术实施例中提供的一个或多个技术方案,至少具有如下技术效果或优点:
27.本技术通过在连铸机出口增加重压下处理,达到进一步减薄铸坯的目的,可将进入轧机前的板坯厚度在当前基础上减薄10-30mm,从而提高板坯运行速度,降低轧机负荷,满足无头产线对金属秒流量和铸机拉速的要求,同时可以实现增加结晶器出口厚度,可有效增加结晶器内腔容积,结晶器内流场和温度场更加均匀,有利于保护渣融化和控制结晶器液面波动,可显著减少卷渣等质量问题,同时减少漏钢等恶性事故发生率,提高了无头产线的生产能力。
附图说明
28.为了更清楚地说明本技术实施例中的技术方案,下面将对实施例描述中所需要使用的附图作简单地介绍,显而易见地,下面描述中的附图是本技术的一些实施例,对于本领域普通技术人员来讲,在不付出创造性劳动的前提下,还可以根据这些附图获得其他的附图。
29.图1是本技术实施例一中提供的薄板坯连铸连轧在线减薄铸坯的生产方法的流程框图;
30.图2是本技术实施例中典型薄板坯连铸机示意图;
31.图3是本技术实施例中重压下装置主视图;
32.图4是本技术实施例中重压下装置侧视图。
具体实施方式
33.为了克服现有技术的不足,本技术提供了一种薄板坯连铸连轧无头产线在线减薄铸坯的方法,通过采用漏斗型结晶器,铸坯出结晶器后采用液芯压下,在铸坯凝固末端采用动态软压下,铸机出扇形段后采用进一步重压下,达到进一步减薄铸坯的目的,解决了现有无头产线由于拉速限制无法继续提高铸坯厚度的技术问题。
34.为了更好的理解上述技术方案,下面将结合说明书附图以及具体的实施方式对上述技术方案进行详细的说明。
35.实施例一
36.如图1所示,本技术实施例提供的一种薄板坯连铸连轧无头产线在线减薄铸坯的方法,包括:
37.步骤s1:将中间包内的钢水进入铸机并通过结晶器1处理后获得带液芯的铸坯;
38.步骤s2:将带液芯的铸坯通过二冷扇形段进行液芯压下处理后获得目标厚度的铸坯;
39.步骤s3:将目标厚度的铸坯进行冷却,并在凝固末端进行轻压下处理后获得全固态铸坯;
40.步骤s4:将全固态铸坯通过重压下处理后获得减薄的铸坯;
41.步骤s5:将减薄的铸坯高拉速进入轧机进行轧制获得成品。
42.结合图2所示,其中步骤s1将中间包内的钢水通过结晶器1处理后获得带液芯的铸坯包括:
43.中间包内的钢水通过浸入式水口流入结晶器1内,通过结晶器1的冷却,形成目标厚度的坯壳,同时结晶器1伴随高频振动,实现坯壳脱模,在驱动辊拉坯力的作用下,带液芯的铸坯向前运动。结晶器1可采用漏斗型结晶器,结晶器1出口厚度可以为100-160mm,可生产板坯宽度为1100-1600mm。结晶器1的宽面冷却水量为6000-8600l/min,结晶器1的窄面冷却水流量可以为400-600l/min,冷却水流速可以为10-13m/s。
44.步骤s2将带液芯的铸坯通过二冷扇形段进行液芯压下2处理后获得目标厚度的铸坯包括:带液芯的铸坯出结晶器1后进入二冷扇形段,在0、1、2号扇形段对带液芯的铸坯进行液芯压下2,扇形段带有位置传感器,通过位置控制将铸坯压到目标厚度,总压下量为5-20mm,其中,的零号扇形段入口位置保持与结晶器1出口位置一致,只在出口位置进行压下。
45.步骤s3将目标厚度的铸坯进行冷却,并在凝固末端进行轻压下3处理后获得全固态铸坯包括:
46.步骤s31:带液芯铸坯通过弧形段,经过连续弯曲和矫直进入水平段,在二次冷却水的不断冷却下,使带液芯铸坯的液芯逐减消失;
47.步骤s32:在带液芯铸坯内部液相完全消失前,将凝固末端通过扇形段进行轻压下3处理获得全固态铸坯。扇形段内二次冷却为气雾冷却,二冷比水量为1.5-2.5l/kg,二冷气压力为1.1-4.0bar,经过二次冷却,铸坯出扇形段后厚度为90-135mm。凝固末端的轻压下3量为3-5mm,通过2-3个扇形段完成,其中,凝固末端轻压下3时固液分率为0.6-0.8之间。
48.如图3、图4所示,步骤s4将全固态铸坯通过重压下4处理后获得减薄的铸坯包括:
全固态铸坯出扇形段后,经过重压下装置5后进行固态压下,进一步减薄铸坯厚度,提高铸坯运行速度,其中的铸机出扇形段后正常运行速度为4.5-6m/min。铸机为直弧型,铸机半径为5.5-6.0m,冶金长度为20-40m。
49.实施例二
50.本实施例通过本技术提供的一种薄板坯连铸连轧无头产线在线减薄铸坯的方法,生产了一种典型的普通低碳钢种sphc(具体成分如下表1),该铸机冶金长度26m,浇铸板坯断面规格为1270
×
110mm,采用漏斗型结晶器,结晶器1出口厚度为130mm,中间包内钢水通过5孔浸入式水口进入结晶器1内,钢水过热度22度,结晶器1宽面冷却水量为8380l/min,窄面冷却水量为550l/min,结晶器1振动频率为350次/min,正常生产拉速为5.3m/min。
51.表1
52.钢种csimnpsaltalssphc0.0370.0310.140.0050.00130.0390.037
53.带液芯的铸坯出结晶器1后进入二冷垂直段,垂直段高度为3.54m。其中零段入口与结晶器1出口保持一致,开口度为130mm,在零段、1段、2段对凝固坯壳进一步压下,1段出口铸坯厚度为118.2mm,铸坯在扇形段驱动辊拉坯力的作用下,以5.3m/min的速度向前运行,整个二冷区域采用气雾冷却,二冷比水量为2.3l/kg,二冷气的压力为1.5-3.5bar。
54.铸坯经过弯曲矫直后进入水平段,跟进凝固液芯位置计算,凝固末端在12、13段,这两个扇形段各压下2mm,其余扇形段辊缝根据凝固收缩设定,出扇形段时铸坯厚度为110mm。
55.铸坯出扇形段后,重压下装置5进一步对凝固铸坯进行压下,压下量为20mm,此时铸坯厚度为90mm,铸坯的运行速度提高到6.48m/min,并以此速度进入到后面的轧机进行轧制。
56.实施例三
57.本实施例通过本技术提供的一种薄板坯连铸连轧无头产线在线减薄铸坯的方法,生产了一种典型的q235b成分钢种(具体如下表2)。该铸机冶金长度26m,浇铸板坯断面规格为1500
×
120mm,采用漏斗型结晶器,结晶器1出口厚度为130mm,中间包内钢水通过5孔浸入式水口进入结晶器1内,钢水过热度为20度。结晶器1宽面冷却水量为8250l/min,窄面冷却水量为539l/min,结晶器1振动频率为343次/min,正常生产拉速为4.8m/min。
58.表2
59.钢种csimnpsaltalsnq235b0.0410.180.750.0060.00120.0360.0350.0048
60.带液芯的铸坯出结晶器1后进入二冷垂直段,垂直段高度为3.54m。其中零段入口与结晶器1出口保持一致,开口度为130mm,在0段、1段、2段对凝固坯壳进一步压下,2段出口铸坯厚度为125mm,铸坯在扇形段驱动辊拉坯力的作用下,以4.8m/min的速度向前运行,整个二冷区域采用气雾冷却,二冷比水量为2.0l/kg,二冷气的压力为1.2-3.5bar。
61.铸坯经过弯曲矫直后进入水平段,跟进凝固液芯位置计算,凝固末端在10、11段,在这两个扇形段各压下1.5mm,其余扇形段辊缝根据凝固收缩设定,出扇形段时铸坯厚度为125mm。
62.铸坯出扇形段后,重压下装置5进一步对凝固铸坯进行压下,压下量为15mm,此时
铸坯厚度为110mm,铸坯的运行速度提高到5.45m/min,并以此速度进入到后面的轧机进行轧制。本技术实施例中提供的一个或多个技术方案,至少具有如下技术效果或优点:
63.1、本技术针对薄板坯连铸连轧无头产线,通过在铸机出口增加重压下装置,进一步在线减薄铸坯,不仅提高了铸坯运行速度,而且可以降低后续轧机的负荷。
64.2、本技术通过在线减薄铸坯,可以进一步增加结晶器出口厚度,进一步提高无头产线的生产能力,可在当前200-220万吨/年的基础上提高到250-300万吨/年,有效提高产线生产能力。
65.3、本技术通过对结晶器出口铸坯厚度的增加,可有效增加结晶器内腔容积,结晶器内流场和温度场更加均匀,有利于保护渣融化和控制结晶器液面波动,可显著减少卷渣等质量问题,同时减少漏钢等恶性事故发生率。
66.4、本技术为薄板坯连铸连轧产线独创工艺,具有较高的经济、社会效益,为无头产线未来的发展提供了新的方向。
67.最后所应说明的是,以上具体实施方式仅用以说明本发明的技术方案而非限制,尽管已描述了本发明的优选实施例,但本领域内的技术人员一旦得知了基本创造性概念,则可对这些实施例作出另外的变更和修改。所以,所附权利要求意欲解释为包括优选实施例以及落入本发明范围的所有变更和修改。
68.显然,本领域的技术人员可以对本发明进行各种改动和变型而不脱离本发明的精神和范围。这样,倘若本发明的这些修改和变型属于本发明权利要求及其等同技术的范围之内,则本发明也意图包含这些改动和变型在内。