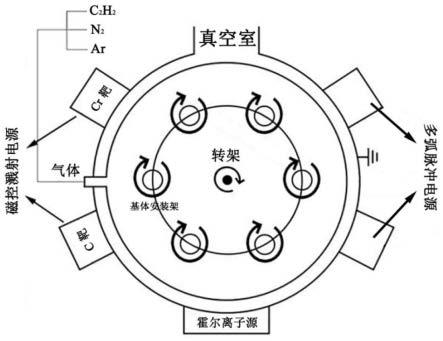
一种金属表面cr/crn/crcn/cr-dlc多层复合自润滑薄膜及其制备方法
技术领域
1.本发明属于表面薄膜制备技术领域,具体涉及一种cr/crn/crcn/cr-dlc多层复合自润滑薄膜及其制备方法。
背景技术:2.随着低碳,环保开始备受重视,能源的利用效率的问题逐步进入人们的视野。摩擦磨损的现象在日常生活中十分常见,据统计,全球约1/3的一次性能源浪费在摩擦过程中,带来了能源的大量耗损。由摩擦磨损造成的机械零部件失效,也让人们的生活安全受到威胁。因此,如何减少机械零部件表面的摩擦磨损一直都是工业生产以及科研人员关注的课题。
3.类金刚石(dlc)薄膜是一种由碳元素构成,兼具了金刚石和石墨的特性的高性能薄膜,具有高硬度、低摩擦系数、低磨损率、生物相容性和化学稳定性强等特点,引起了人们的广泛关注,常被应用于机械部件的减磨耐磨,密封润滑等方面,同时在汽车零部件,太空密封润滑,生物医学等领域也发挥着重要作用。采用适当的制备工艺和技术能够特化dlc的性能使其适用于更多的实际应用工况。所谓金属掺杂薄膜是指在dlc制备过程中同时掺杂加入其它金属元素,dlc薄膜在金属掺杂的作用下能够有效提升其力学性能,同时在适当条件下也能获得更加优异的摩擦学性能。
4.然而,dlc薄膜存在着内应力大的缺点,使其表面易产生裂纹,褶皱甚至脱落,在金属表面沉积dlc薄膜时以上现象更为突出,制约着dlc薄膜的进一步应用。国内外众多学者对此进行了深入的研究,通过工艺参数改进、掺杂、多层结构等方法来释放薄膜内应力,提高薄膜的稳定性。由于薄膜和基材之间热膨胀系数、化学成分和晶体结构等之间的差异,dlc薄膜与基材的结合力受到限制,过度层的存在缓解了这一差异,提高了薄膜和基材之间的结合能力,相比于传统过渡层,带有梯度变化的过渡层更能够缓和dlc薄膜和基体之间的差异,使得薄膜不易脱落,同时cr元素的掺杂也有降低薄膜内应力,提高膜基结合力的作用。
5.在中国专利申请号为cn106835040b的专利文件中公开了《一种掺金属的类金刚石涂层的制备方法》,上述专利文件中通过化学气相沉积技术完成了类金刚石薄膜的cr元素掺杂,过渡层为cr层和crc层。磁控溅射沉积技术属于物理气相沉积,具有膜层致密和表面光洁度高等优点,但缺点是薄膜结合力不高和沉积速度较慢,梯度过渡层的应用和cr元素的掺杂不仅大大提高了薄膜的膜基结合力,还降低了薄膜的摩擦系数,使得薄膜能够更好的适应各类工作环境。
技术实现要素:6.为了克服现有技术的缺点,提高薄膜附着能力,本发明的目的在于提供一种带梯度过渡层的掺杂dlc薄膜的制备方法。本发明的梯度过渡层能够提升薄膜材料的结合性能,
cr元素的掺杂能够进一步提升薄膜与基体间的结合力,使得dlc薄膜能够更为容易的附着在不锈钢基体上,同时降低了薄膜的摩擦系数。
7.本发明的上述目的是通过以下技术方案实现的。
8.一种金属表面cr/crn/crcn/cr-dlc多层复合自润滑薄膜,其特征在于:由基体材料、梯度过渡层和cr-dlc薄膜层和从下到上构成;所述梯度过渡层由依次叠加的cr、crn、梯度crcn所构成,薄膜的基体材料为304不锈钢;所述梯度分布的crcn共分为5个周期,每个周期对应的薄膜厚度随着时间增加略有增大;
9.所述梯度过渡层能提高膜基结合力,使得dlc薄膜能够附着在较软基体上,所述cr-dlc薄膜层的厚度为4~4.5μm,梯度过渡层的总厚度约为0.8~1μm。
10.所述dlc薄膜的厚度为4~4.5μm,梯度过渡层的总厚度为0.7~1μm。
11.所述薄膜基体为304不锈钢。
12.本发明还提供了dlc薄膜的制备方法,采用直流磁控溅射技术加射频磁控溅射技术共同制备,所用到的靶材为圆柱形碳靶和圆柱形铬靶,操作简便,成功率高,能够获得性能优良的薄膜,有利于实现大批量的生产。
13.本发明采用复合多功能离子镀膜设备,该镀膜设备主要包括真空室、两个弧源、直流磁控溅射电源、射频磁控溅射电源、加热源、转动单元、进气单元、分子泵和脉冲偏压电源等。其中直流电源和射频电源可更换所连靶材,真空室中设有可公转、自转的基体安装架。复合多功能离子镀膜设备示意图如图1所示。
14.本发明在所述磁控溅射电源上分别安装cr靶和c靶,并将基体安装在基体安装架上。
15.金属表面cr/crn/crcn/cr-dlc多层复合自润滑薄膜的制备方法,其特征在于:包括以下步骤:
16.(1)对基体表面预处理,并将基体安装在基体安装架上;
17.(2)在基体表面进行cr元素轰击和cr层沉积;
18.(3)在cr层上沉积crn层;
19.(4)在crn层上沉积梯度crcn层;
20.(5)在crcn层上沉积cr-dlc层。
21.步骤(2)、(3)和(4)中采用直流磁控溅射电源连接cr靶进行过渡层的沉积,基体安装在基体安装架上并随之进行公转和自转;步骤(5)中采用直流磁控溅射电源连接c靶,射频磁控溅射电源连接cr靶,通过共沉积的方法进行沉积。
22.所述c靶的纯度为99.99%,直径为120mm,厚度为6mm。
23.所述cr靶的纯度为99.99%,直径为120mm,厚度为6mm。
24.所述沉积过程中靶材和基体的距离为8~10cm。
25.步骤(1)中所述基体表面预处理是将基体打磨、抛光至粗糙度低于20nm,然后在超声波清洗设备中,利用无水乙醇和丙酮中进行清洗,所述声波频率为20~30khz,清洗时间约为30分钟;然后在复合多功能离子镀膜设备中进行等离子体辉光清洗。
26.所述等离子体辉光清洗的具体操作为:将基体放入真空室中,抽真空至低于1.5
×
10-3
pa后,再通入高纯氩气,流量为70~80sccm,维持真空室偏压在0.5~1.0pa,同时调节基体直流偏压为0v,脉冲偏压为500~700v,占空比为60%~80%,开启霍尔离子源,对基体进
行25~30min的等离子体辉光清洗。
27.步骤(2)中所述的轰击条件为真空度在1~1.5pa,氩气的流量为35~40sccm,同时调节基体直流偏压为80~120v,脉冲偏压为500~700v,占空比为40%~60%,采用cr靶,靶电流为2.2~2.5a;轰击时间为180~360s;轰击激活表面之后进行cr过渡层的沉积,cr靶电流为1.5~2a,基体直流偏压为80~120v,脉冲偏压为200~300v,占空比为15%~25%,沉积的时间为8~10min。
28.步骤(3)中所述的沉积条件为真空度在0.8~1.2pa,氩气的流量为50~55sccm,氮气的流量为50~55sccm,在氩气和氮气的混合气氛中,同时调节基体直流偏压为v,脉冲偏压为v,占空比为15~25%,沉积时间为8~10min。
29.步骤(4)中所述沉积条件为真空度在0.4~1.2pa,氩气流量为20~60sccm,氮气流量为15~40sccm,乙炔气体流量为15~40sccm,cr靶电流为1.5~2a,基体直流偏压为80~120v,脉冲偏压为200~300v,占空比为25%~35%。沉积过程中各类气体的通量和基体偏压不断增大,共五种参数沉积出梯度crcn过渡层,每层沉积的时间分别为4min、5min、5min、8min和8min。
30.步骤(5)中所述沉积条件为真空度在0.8~1.2pa,氩气流量为70~90sccm,乙炔气体流量为20~30sccm,c靶电流为1.5~2a,cr靶功率为50~150w,沉积时间为150min,沉积过程中取消基体安装架的公转,使其位于碳靶和铬靶的中间位置进行自转。
31.通过采用上述方案,通过调整cr靶射频磁控溅射的功率,可以改变薄膜中cr元素掺杂的含量,cr元素的掺杂使得薄膜内应力有所释放,膜基结合力获得了极大的提高,且提升了薄膜的摩擦学性能,降低薄膜的摩擦系数。
32.与现有技术相比较,本发明有如下优点:
33.(1)本发明的多层过渡层可以很好的缓和dlc薄膜的内应力,其中crcn层采用了梯度形式,逐步增加过渡层中c的含量,使得dlc薄膜能够稳定附着在不锈钢等基体上而不发生脱落,扩展了dlc薄膜的使用领域。
34.(2)本发明所采用的薄膜制备工艺适当,薄膜表面均匀,薄膜厚度在4μm以上,相较于常见dlc薄膜,薄膜厚度较厚,耐磨性较高。
35.(3)本发明采用的复合多功能离子镀膜设备,与工业生产中的镀膜设备类似,同时采用应用成熟的直流磁控溅射技术和射频磁控溅射技术制备目标薄膜,操作简单,有利于工业中的大规模批量生产。
36.(4)本发明所制备的cr-dlc薄膜致密程度高,硬度较大,具有良好的机械性能和较低的摩擦系数。
37.(5)本发明所掺杂的cr元素以碳化物的形式存在与薄膜中,改变薄膜中的微观结构,同时在高温摩擦实验中生成cr的氧化物保护薄膜,能够提高薄膜的高温摩擦学性能。
附图说明
38.图1为本发明所使用的复合多功能离子镀膜设备示意图;
39.图2a为本发明实施例2的断面横截面形貌的扫描电镜图;
40.图2b为本发明实施例2的断面横截面eds线扫描元素分布图;
41.图3为本发明实施例2的微观表面形貌的原子力显微镜扫描图;
42.图4为本发明所制备dlc薄膜结构示意图
具体实施方式
43.下面结合附图和实施例对本发明的具体实施做进一步说明,但本发明的实施方式不限于此。
44.实施例1
45.将经过打磨、抛光处理的不锈钢基体,分别在无水乙醇和丙酮溶液中利用超声波清洗设备清洗干净。之后检查基体表面是否干净并将烘干后的基体安装在真空室的基体安装架上,关闭密封门并将真空室内气压抽到1
×
10-3
pa后,向真空室内通入氩气,氩气通量为75sccm,维持真空室内气压在0.9pa,之后开启霍尔离子源对基体进行30min辉光清洗,清洗时的基体脉冲偏压为600v,占空比为40%,基体安装架同时进行公转和自转。辉光清洗结束后,关闭霍尔离子源,调节氩气通量为40sccm,维持真空室内气压在0.5pa,打开直流磁控溅射开关进行cr元素的轰击,直流电流为2.5a,进行5min的轰击激活基体表面;然后调节氩气通量至真空室内气压为0.6pa,在直流电流2a,直流偏压80v,脉冲偏压300v,占空比20%的条件下沉积cr层,沉积时间为8min。通入氮气,改变氩气通量为50sccm,氮气通量为50sccm进行crn层的沉积,沉积时真空室气压维持在0.9pa,直流电流2a,直流偏压60v,脉冲偏压200v,占空比20%,沉积时间为9min。完成crn层的沉积后,打开乙炔通道,进行crcn梯度过渡层的沉积,梯度沉积过程中乙炔和氮气的通量分别为15、20、25、30、35sccm,对应氩气通量为25、33、36、43、54sccm,直流电流2a,脉冲偏压200v,直流偏压60v,沉积时间分别为4、5、5、8、8min,在沉积中逐步将脉冲偏压降低到100v,直流偏压降低到45v,整个沉积过程中基体安装架的自转转速稳定在5rpm,公转转速稳定在0.5rpm。之后调节氩气通量为75sccm,乙炔通量为25sccm,维持真空腔内气压为1pa,将基体安装架转至铬靶和碳靶的中间位置进行自转,自传转速稳定在5rpm,完成cr掺杂dlc薄膜的制备,直流电流为1.5a,射频功率为50w,直流偏压60v,脉冲偏压200v,占空比40%,dlc薄膜的制备时间为2.5h。制备结束后试样随炉自然冷却,得到带有梯度过渡层的cr-dlc薄膜。
46.本实例中所得的cr-dlc薄膜,经过检测,cr元素原子百分比含量为2.04%,dlc薄膜的厚度为4.49μm。在常温环境下,dlc薄膜与si3n4对偶球进行摩擦摩擦实验,平均摩擦系数为0.104且摩擦界面无明显磨损迹象。
47.实施例2
48.将经过打磨、抛光处理的不锈钢基体,分别在无水乙醇和丙酮溶液中利用超声波清洗设备清洗干净。之后检查基体表面是否干净并将烘干后的基体安装在真空室的基体安装架上,关闭密封门并将真空室内气压抽到1
×
10-3
pa后,向真空室内通入氩气,氩气通量为75sccm,维持真空室内气压在0.9pa,之后开启霍尔离子源对基体进行30min辉光清洗,清洗时的基体脉冲偏压为600v,占空比为40%,基体安装架同时进行公转和自转。辉光清洗结束后,关闭霍尔离子源,调节氩气通量为40sccm,维持真空室内气压在0.5pa,打开直流磁控溅射开关进行cr元素的轰击,直流电流为2.5a,进行5min的轰击激活基体表面;然后调节氩气通量至真空室内气压为0.6pa,在直流电流2a,直流偏压80v,脉冲偏压300v,占空比20%的条件下沉积cr层,沉积时间为8min。通入氮气,改变氩气通量为50sccm,氮气通量为50sccm进行crn层的沉积,沉积时真空室气压维持在0.9pa,直流电流2a,直流偏压60v,脉冲偏压
200v,占空比20%,沉积时间为9min。完成crn层的沉积后,打开乙炔通道,进行crcn梯度过渡层的沉积,梯度沉积过程中乙炔和氮气的通量分别为15、20、25、30、35sccm,对应氩气通量为25、33、36、43、54sccm,直流电流2a,脉冲偏压200v,直流偏压60v,沉积时间分别为4、5、5、8、8min,在沉积中逐步将脉冲偏压降低到100v,直流偏压降低到45v,整个沉积过程中基体安装架的自转转速稳定在5rpm,公转转速稳定在0.5rpm。之后调节氩气通量为75sccm,乙炔通量为25sccm,维持真空腔内气压为1pa,将基体安装架转至铬靶和碳靶的中间位置进行自转,自传转速稳定在5rpm,完成cr掺杂dlc薄膜的制备,直流电流为1.5a,射频功率为100w,直流偏压60v,脉冲偏压200v,占空比40%,dlc薄膜的制备时间为2.5h。制备结束后试样随炉自然冷却,得到带有梯度过渡层的cr-dlc薄膜。
49.本实例中所得的cr-dlc薄膜,经过检测,cr元素原子百分比含量为3.34%,dlc薄膜的厚度为4.26μm。图2a为本实例所制得样品的断面横截面形貌的扫描电镜图,可以看出本实例所制得的样品连接紧密,层间无明显缺陷,表层平整,属于高质量的类金刚石薄膜。图3为本实例所制得样品利用原子力显微镜测得的微观表面形貌图,计算分析得样品微观表面粗糙度为6.16nm。在常温环境下,dlc薄膜与si3n4对偶球进行摩擦摩擦实验,平均摩擦系数为0.096且摩擦界面无明显磨损迹象。
50.实施例3
51.将经过打磨、抛光处理的不锈钢基体,分别在无水乙醇和丙酮溶液中利用超声波清洗设备清洗干净。之后检查基体表面是否干净并将烘干后的基体安装在真空室的基体安装架上,关闭密封门并将真空室内气压抽到1
×
10-3
pa后,向真空室内通入氩气,氩气通量为75sccm,维持真空室内气压在0.9pa,之后开启霍尔离子源对基体进行30min辉光清洗,清洗时的基体脉冲偏压为600v,占空比为40%,基体安装架同时进行公转和自转。辉光清洗结束后,关闭霍尔离子源,调节氩气通量为40sccm,维持真空室内气压在0.5pa,打开直流磁控溅射开关进行cr元素的轰击,直流电流为2.5a,进行5min的轰击激活基体表面;然后调节氩气通量至真空室内气压为0.6pa,在直流电流2a,直流偏压80v,脉冲偏压300v,占空比20%的条件下沉积cr层,沉积时间为8min。通入氮气,改变氩气通量为50sccm,氮气通量为50sccm进行crn层的沉积,沉积时真空室气压维持在0.9pa,直流电流2a,直流偏压60v,脉冲偏压200v,占空比20%,沉积时间为9min。完成crn层的沉积后,打开乙炔通道,进行crcn梯度过渡层的沉积,梯度沉积过程中乙炔和氮气的通量分别为15、20、25、30、35sccm,对应氩气通量为25、33、36、43、54sccm,直流电流2a,脉冲偏压200v,直流偏压60v,沉积时间分别为4、5、5、8、8min,在沉积中逐步将脉冲偏压降低到100v,直流偏压降低到45v,整个沉积过程中基体安装架的自转转速稳定在5rpm,公转转速稳定在0.5rpm。之后调节氩气通量为75sccm,乙炔通量为25sccm,维持真空腔内气压为1pa,将基体安装架转至铬靶和碳靶的中间位置进行自转,自传转速稳定在5rpm,完成cr掺杂dlc薄膜的制备,直流电流为1.5a,射频功率为150w,直流偏压60v,脉冲偏压200v,占空比40%,dlc薄膜的制备时间为2.5h。制备结束后试样随炉自然冷却,得到带有梯度过渡层的cr-dlc薄膜。
52.本实例中所得的cr-dlc薄膜,经过检测,cr元素原子百分比含量为5.43%,dlc薄膜的厚度为4.18μm。在常温环境下,dlc薄膜与si3n4对偶球进行摩擦摩擦实验,平均摩擦系数为0.101且摩擦界面无明显磨损迹象。