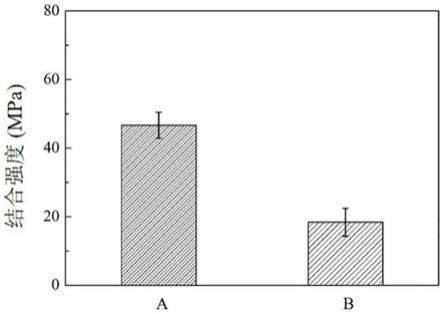
1.本发明属于金属材料领域,具体涉及到一种增强金属间化合物边界润滑性能涂层的制备方法。
背景技术:2.特种车辆、航空航天和石化冶金等国家重大高新技术装备长期处于高/低温(宽温域)、特殊介质和高速重载等极端恶劣工况条件下,其关键金属摩擦运动副零部件承受强烈摩擦磨损而导致零部件的使役寿命降低,进而影响整个装备的可靠性和稳定性。通常情况下,运动副的失效始于它们的表面。因此,在保持零部件基体材料固有的综合特性的同时,在运动副表面制备涂层以控制摩擦减少磨损、改善润滑性能,被认为是解决上述问题即经济又切实可行的有效方法。
3.ni3al金属间化合物具有许多优良的性能,如较高的熔点、显微硬度、比强度,良好的导热性、耐磨和抗氧化性,已成为具有广泛应用潜力的涂层防护材料和高温结构材料。然而,ni3al金属间化合物存在室温脆性和蠕变抗力小等瓶颈问题,是阻碍其工程广泛应用的重要原因。尽管可采用机械合金化的等方式改善ni3al金属间化合物自身存在的问题,但性能提升的幅度非常有限。
4.专利cn103498074a提出了一种石墨烯增强ni3al复合涂层的制备方法,涂层制备方法为放电等离子烧结,该专利由于石墨烯在温度350℃以上发生氧化,进而降低了该材料高温下的摩擦学性能。专利cn103233223a提供了一种tic增强ni3al复合涂层的制备方法,涂层制备方法为激光熔覆,该专利所采用的微米级的添加相在高温条件下会因晶粒长大而出现涂层性能下降和失效的问题。专利cn112553566a提供了一种氮化硼纳米片增强ni3al金属间化合物复合涂层的制备方法,涂层的制备方法为等离子喷涂技术,该专利所采用的添加相不能与ni3al金属间化合物基材形成良好的冶金结合,颗粒间结合界面强度低,从而导致涂层在服役过程中容易出现颗粒剥落现象。
5.现有技术中仅仅通过向ni3al金属间化合物基材中添加增强相或润滑相提高涂层的摩擦学性能,制备涂层的微观结构致密度交底,对涂层耐磨性能的提升幅度有限。
技术实现要素:6.本部分的目的在于概述本发明的实施例的一些方面以及简要介绍一些较佳实施例。在本部分以及本技术的说明书摘要和发明名称中可能会做些简化或省略以避免使本部分、说明书摘要和发明名称的目的模糊,而这种简化或省略不能用于限制本发明的范围。
7.鉴于上述和/或现有技术中存在的问题,提出了本发明。
8.因此,本发明的目的是,克服现有技术中的不足,提供一种增强金属间化合物边界润滑性能涂层的制备方法。
9.为解决上述技术问题,本发明提供了如下技术方案:一种增强金属间化合物边界润滑性能涂层的制备方法,包括,
采用惰性气体雾化法制备ni3al金属间化合物;将ni3al金属间化合物和mos2混合,机械球磨,得到喷涂混合粉体;采用等离子喷涂技术在基体表面喷涂nicraly打底层;在氩气气氛中对nicraly打底层预氧化处理,制得预处理后nicraly打底层;将喷涂混合粉体喷涂在预处理后nicraly打底层表面,获得涂层。
10.作为本发明所述制备方法的一种优选方案,其中:所述ni3al金属间化合物,其中,镍粉与铝粉质量比为87:90。
11.作为本发明所述制备方法的一种优选方案,其中:所述喷涂混合粉体,其中,混合粉体组分:ni3al粉:80~90wt%;mos2粉:10~20wt%。
12.作为本发明所述制备方法的一种优选方案,其中:所述惰性气体雾化法制备ni3al金属间化合物,其中,雾化介质为氮气,雾化压力为5.5 mpa,雾化结束后,用100目筛过筛后称取粒径小于150 μm粉末作为喷涂材料。
13.作为本发明所述制备方法的一种优选方案,其中:所述采用等离子喷涂技术在基体表面喷涂nicraly打底层,其中,等离子喷涂的工艺参数:喷涂距离为110 mm,等离子气流h2流量为2 l/min,ar流量为40 l/min,电流为400 a,喷枪移动速度为150 mm/s,送粉速率为25 g/min。
14.作为本发明所述制备方法的一种优选方案,其中:所述预氧化处理,其中,预氧化处理在氩气气氛中进行,随炉升温至1000℃,保温4 h,然后再升温至1080℃,保温4 h,随后随炉冷却至室温。
15.作为本发明所述制备方法的一种优选方案,其中:所述将喷涂混合粉体喷涂在预处理后nicraly打底层表面,其中,喷涂为等离子喷涂工艺。
16.作为本发明所述制备方法的一种优选方案,其中:所述等离子喷涂工艺参数:喷涂距离为150 mm,等离子气流h2流量为5 l/min,ar流量为50 l/min,电流为500 a,喷枪移动速度为200 mm/s,送粉率为50 g/min,重复喷涂3次。
17.作为本发明所述制备方法的一种优选方案,其中:所述基体包括镍基高温合金基体mga1400ds。
18.本发明有益效果:(1)本发明采用在氩气气氛环境下,对等离子喷涂制备的nicraly打底层进行分级热处理,能够在其表面形成均匀的α-al2o3基热生长氧化物,从而显著提高涂层与基体之间的界面结合强度。
19.(2)本发明巧妙利用mos2和ni3al在高温条件下发生的自蔓延反应,并基于mos2层状的晶体结构,改善了制备的ni3al基自润滑涂层微观组织结构的均匀性,有效改善了涂层层间结合状态。
20.(3)本发明提出的利用层状结构的mos2固体润滑剂增强ni3al金属间化合物的方法,由于mos2固体润滑剂在边界润滑条件下,能够在摩擦表面生成一层均匀的边界润滑膜,有利于改善涂层的边界润滑状态,该涂层相比于ni3al自润滑涂层在耐磨损性能方面得到显著提升。
附图说明
21.为了更清楚地说明本发明实施例的技术方案,下面将对实施例描述中所需要使用的附图作简单地介绍,显而易见地,下面描述中的附图仅仅是本发明的一些实施例,对于本领域普通技术人员来讲,在不付出创造性劳动性的前提下,还可以根据这些附图获得其它的附图。其中:图1为本发明所提供的等离子喷涂涂层形成原理示意图,图中,1为喷枪、2为送粉管、3为熔融颗粒、4为涂层、5为基材;图2为本发明实施例1中制备涂层结合强度对比图;图3为本发明实施例1中“边界润滑-干摩擦”摩擦系数曲线图。
具体实施方式
22.为使本发明的上述目的、特征和优点能够更加明显易懂,下面结合说明书实施例对本发明的具体实施方式做详细的说明。
23.在下面的描述中阐述了很多具体细节以便于充分理解本发明,但是本发明还可以采用其他不同于在此描述的其它方式来实施,本领域技术人员可以在不违背本发明内涵的情况下做类似推广,因此本发明不受下面公开的具体实施例的限制。
24.其次,此处所称的“一个实施例”或“实施例”是指可包含于本发明至少一个实现方式中的特定特征、结构或特性。在本说明书中不同地方出现的“在一个实施例中”并非均指同一个实施例,也不是单独的或选择性的与其他实施例互相排斥的实施例。
25.本发明提供的一种增强金属间化合物边界润滑性能涂层的制备方法,改善了涂层微观组织结构的均匀性,有效克服纯ni3al金属间化合物存在室温脆性和蠕变抗力小等问题,显著提高了复合涂层的边界润滑摩擦学性能。
26.本发明所采用的等离子喷涂原理图如图1所示:喷枪1、送粉管2选用径向送粉方式将复合粉体送入焰流中心;由等离子弧的焰流产生的热源加热复合粉末,形成熔融颗粒3,复合涂层4沉积在基体5的表面。
27.本发明所用粉末、仪器设备等均可从市场购得或通过常规方法制备。
28.实施例1:一种增强金属间化合物边界润滑性能涂层的制备方法,按如下步骤进行:(1)喷涂用混合粉末的组分(质量百分比)为:ni3al粉:80%;mos2粉:20%。
29.(2)将按照复合涂层的成分配比称取ni3al合金和mos2固体润滑剂粉末倒入罐装容器中,以转速为500 r/min的球磨参数球磨3 h,球磨完毕后,于100℃下干燥2 h。
30.(3)用丙酮对基体表面(镍基高温合金基体mga1400ds)进行超声清洗以去除油污锈渍等杂质,清洗完成后立刻烘干防止生锈。
31.(4)用粒度24目的棕刚玉对待喷涂的基体表面进行喷砂粗化处理以提高涂层与基体间的结合强度,要求粗化后表面粗糙度不低于ra 7.0。
32.(5)nicraly打底层的制备:nicraly粉末中各元素质量比为cr:22.59%,al:11.23%,y:1.83%,ni:余量;等离子喷涂工艺参数:喷涂距离为110 mm,等离子气流h2流量为2 l/min, ar流量为40 l/min,电流为400 a,送粉率为 25 g/min。
33.(6)打底层表面预氧化处理。在氩气气氛中进行,随炉升温至1000℃,保温4 h,然
后再升温至1080℃,保温4 h,随后随炉冷却至室温。
34.(7)将干燥好的混合粉末倒入送粉器中,调节送粉气流使得粉末刚好送入等离子焰流中心。等离子喷涂的工艺参数为:喷涂距离为150 mm,等离子气流h2流量为5 l/min, ar流量为50 l/min,电流为500 a,喷枪移动速度为200 mm/s,每次向下移动3 mm,重复喷涂4次。最终在喷砂处理的镍基高温合金基体表面沉积厚度约350-400 μm的复合涂层。
35.(8)经检测,制备复合涂层组织致密,孔隙率为2%,远低于ni3al合金涂层的15%;ni3al合金涂层的结合强度为18 mpa,远低于ni3al-mos2复合涂的结合强度(46 mpa),如图2所示,图中,a为喷涂ni3al合金涂层的结合强度,b为喷涂ni3al-mos2复合涂层的结合强度。
36.(9)对所制备涂层进行球盘摩擦磨损实验,作为对照,在同等条件下同时进行摩擦实验。
37.其中对偶球选用直径为5 mm的si3n4球,载荷10 n,频率4 hz,磨痕长度5 mm。
38.结果表明,喷涂的ni3al合金涂层的“边界润滑-干摩擦”摩擦系数为0.7,远高于ni3al-mos2复合涂层的“边界润滑-干摩擦”摩擦系数(0.4);如图3所示,图中,a曲线为喷涂ni3al合金涂层“边界润滑-干摩擦”摩擦系数曲线,b曲线为喷涂ni3al-mos2复合涂层“边界润滑-干摩擦”摩擦系数曲线。同时,ni3al-mos2复合涂层“边界润滑-干摩擦”曲线转变时间为6 h,远长于ni3al合金涂层边界润滑曲线转变时间(4 h)。
39.实施例2:与实施例1的不同之处在于:步骤(2)中的添加相为软金属ag。
40.为了保证软金属ag与ni3al合金混合均匀,以实施例1中的步骤(2)进行混粉。
41.在步骤(8)中,复合涂层的孔隙率为5%,远低于ni3al合金涂层的15%;复合涂层的结合强度为36 mpa,远高于ni3al合金涂层的结合强度(18 mpa)。
42.在步骤(9)中,喷涂的ni3al合金涂层的摩擦系数为0.7,远高于ni3al-ag复合涂层的摩擦系数(0.6)。
43.同时,ni3al-ag复合涂层“边界润滑-干摩擦”曲线转变时间为5 h,远长于ni3al合金涂层的“边界润滑-干摩擦”曲线转变时间(4 h)。
44.实施例3:与实施例1的不同之处在于:步骤(2)中的添加相为软金属mo。
45.为了保证软金属mo与ni3al合金混合均匀,以实施例1中的步骤(2)进行混粉。
46.在步骤(8)中,复合涂层的孔隙率为8%,远低于ni3al合金涂层的15%;复合涂层的结合强度为31 mpa,远高于ni3al合金涂层的结合强度(18 mpa)。
47.在步骤(9)中,喷涂的ni3al合金涂层的摩擦系数为0.7,远高于ni3al-mo复合涂层的摩擦系数(0.5)。
48.同时,ni3al-mo复合涂层“边界润滑-干摩擦”曲线转变时间为4.5 h,远长于ni3al合金涂层的“边界润滑-干摩擦”曲线转变时间(4 h)。
49.实施例4:与实施例1的不同之处在于:步骤(2)中的添加相为ni包石墨。
50.为了保证ni包石墨与ni3al合金混合均匀,以实施例1中的步骤(2)进行混粉。
51.在步骤(8)中,复合涂层的孔隙率为11%,低于ni3al合金涂层的15%;复合涂层的结
ar流量为50 l/min,电流为500 a,喷枪移动速度为200 mm/s,每次向下移动3 mm,重复喷涂4次。最终在喷砂处理的镍基高温合金基体表面沉积厚度复合涂层。
64.(8)经检测,制备涂层组织较为致密,孔隙率为6%,高于实施例1(2%);涂层的结合强度为32 mpa,低于实施例1(46 mpa)。摩擦学性能测试结果表明,喷涂层的“边界润滑-干摩擦”摩擦系数为0.6,高于实施例1(0.4);涂层“边界润滑-干摩擦”曲线转变时间为5 h,短于实施例1(6)。
65.应说明的是,以上实施例仅用以说明本发明的技术方案而非限制,尽管参照较佳实施例对本发明进行了详细说明,本领域的普通技术人员应当理解,可以对本发明的技术方案进行修改或者等同替换,而不脱离本发明技术方案的精神和范围,其均应涵盖在本发明的权利要求范围当中。