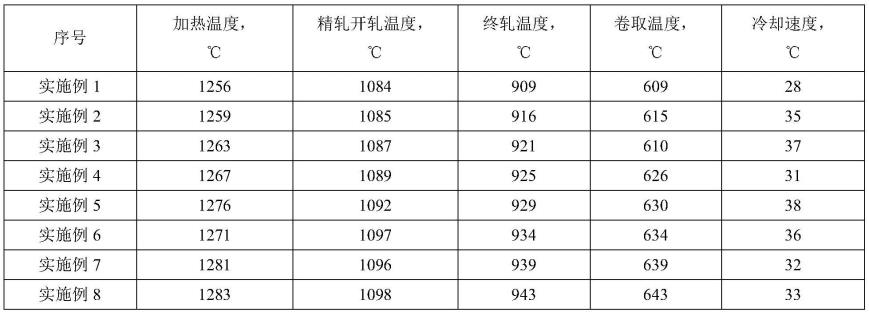
一种700mpa级耐磨损腐蚀钢及其制造方法
技术领域
1.本发明涉及耐蚀钢领域,尤其涉及一种700mpa级耐磨损腐蚀钢及其制造方法。
背景技术:2.近年来,随着社会和经济的高速发展,节能降耗、减少污染和节约资源成为大家面临的一个十分迫切的问题。对于铁路集装箱来说,降低自身重量,不但可以节能降耗、减少环境污染,而且还可以增加集装箱的载重量。为了适应这种需要,目前普遍采用的方法是使用更高强度的钢板,从而降低所使用钢板的厚度,实现减重的目标。然而,随着钢板的使用级别越来越高,当继续减薄时,所制造部件由于硬度的不足,导致在运输矿石或者煤炭时,局部出现磨损腐蚀严重的情况,严重影响安全性。
3.公开号为cn112159934a的“一种抗腐蚀磨损耐磨钢板及其制备方法”专利文件,它是通过合金成分设计以及结合热处理工艺获得以马氏体为基体组织,制备得到在酸性环境下具有优异的抗腐蚀磨损性能的新型钢板。公开号为cn107653423b的“用于铁路运煤车辆的耐煤水磨损腐蚀钢板及其制造方法”专利文件,它通过控制c、cr、ni含量,使其满足1.6%≤12c+cr/ni≤2.8%,相对q450nqr1的磨损腐蚀速率为20%-30%。它添加较多的ni元素,使成本较高,不利于其推广和应用。公开号为cn104662193a为的“一种低温韧性和耐腐蚀磨损性优异的耐磨损钢板”,它通过控制钢中固溶cr和mo含量,使其满足0.05≤(cr+2.5mo)≤2.0(%),并控制主相为淬火态马氏体相且原奥氏体粒径为30μm以下的组织,达到大幅度提高耐腐蚀磨损性的目的,但其使用环境为建筑、土木、矿山等工地中含有水分的土与沙子接触而产生的磨损。公开号为cn101423916b的“一种低合金耐磨耐蚀钢及其制造方法”专利文件,它通过适当调节碳含量并加入有助于提高合金耐蚀性的元素al、nb,以及稀土变质处理,形成mn-si-cr-mo-al系无碳化物贝氏体钢,从而获得了一种适合海洋泥沙磨损腐蚀环境使用的低合金耐磨耐蚀钢。其主要采用了高si、高al的成分设计抑制碳化物的形成,并加入cr、ni、mo等元素提高耐蚀性,其由于添加了贵重金属mo、ni和nb,成本较高。
4.上述现有技术主要采用热处理工艺获得以马氏体为基体组织的耐磨钢板或耐磨损腐蚀钢板,或者添加较多贵重金属,成本较高,对于采用热轧工艺生产耐磨损腐蚀钢板的研究较少。因此,如何采用热轧工艺获得耐磨损腐蚀钢是本领域亟待解决的技术难点之一。
技术实现要素:5.本发明的目的在于提供一种700mpa级耐磨损腐蚀钢及其制造方法,钢板具有良好的耐腐蚀性能、耐磨损性能及优异的成型性能,适合于轻量化集装箱的制造。
6.为了达到上述目的,本发明采用以下技术方案实现:
7.一种700mpa级耐磨损腐蚀钢,钢中化学成分按重量百分比计为:c 0.069%~0.090%、si 0.65%~0.93%、mn 1.18%~1.59%、p≤0.018%、s≤0.006%、cr 0.91%~1.48%、cu 0.14%~0.24%、sb 0.055%~0.091%、w 0.45%~0.65%、ti 0.071%~0.096%、als 0.015%~0.045%、n≤0.004%,余量为fe以及不可避免的杂质。
8.本发明所以选择以上合金元素种类及其含量是因为:
9.c是钢板获得高的强度和硬度的关键元素,可以与ti形成细小的碳化物tic,起到沉淀强化作用。但较多的c对钢板焊接、韧性及塑性不利。本发明中限定c的含量在0.069%-0.090%。
10.si能溶于铁素体和奥氏体中提高钢的硬度和强度,但是含量过高的话,易导致轧后钢板表面红色氧化铁皮严重,还不利于钢板的焊接。本发明中限定si的含量在0.65%-0.93%。
11.mn在钢中的主要作用是固溶强化,起到提高钢板强度的作用。能显著降低奥氏体向铁素体转变的相变温度,细化钢的显微组织,保证钢板的强度指标和耐磨性能,但mn含量过多会使淬透性增大,从而导致可焊性和焊接热影响区韧性恶化,同时考虑成本因素,本发明将其含量控制在1.18%-1.59%。
12.p和s为钢中杂质元素,显著降低塑韧性和焊接性能,控制较低的p、s有利于提高性能。本发明钢中控制p≤0.018%,s≤0.006%。
13.cr在钢的表面形成致密的氧化膜,提高钢的钝化能力。当与cu同时加入钢中,耐腐蚀效果尤为明显。此外,cr元素在钢中可以形成渗碳体及多种碳化物,能显著提高钢的强度、硬度和耐磨性。本发明限定其含量范围为0.91%-1.48%。
14.cu是耐大气腐蚀钢中对提高耐大气腐蚀性能最主要的,此外还能提高钢的强度,含量过高的化,容易引起热脆。本发明限定其含量范围为0.14%-0.24%。
15.sb通常作为有害元素在钢中不断富集,严重地影响钢材的质量。本发明中sb是改善耐蚀性的有效元素,通过sb、cr和w的复合添加,协同在锈层中富集,除了形成wo3保护性产物膜外,促进了sb2o5与cuo的形成,显著阻碍浸蚀性离子传输。本发明限定其含量范围为0.055%-0.091%。
16.w能够形成钨酸根或w碳化物,促进保护性产物膜或钝化膜的形成,部分地溶入铁中形成固溶体,能显著提高钢的耐磨性,综合考虑成本因素,本发明限定其含量范围为0.45%-0.65%。
17.ti是强碳氮化物形成元素,在本发明中是重要的微合金强化元素,不但可以有效细化晶粒外,而且能与c和n形成细小的碳化物和氮化物或碳氮化物,尤其是在卷取及缓冷过程中析出的纳米级的tic具有很高的沉淀强化作用。本发明中tic不仅能够强化基体的强度,而且能够提高钢板的耐磨性。本发明限定其范围为0.071%-0.096%。
18.als:是常用的脱氧剂,本发明限定其范围为0.015%-0.045%。
19.n是冶炼过程中存在的元素,由于本发明的特点之一是采用ti微合金化技术提高钢板的耐磨损性能,而ti是活性很强的元素,将与钢中o、n、s等元素反应,如果n含量过高的化,会在钢水中析出尺寸粗大的tin,既不能阻止奥氏体晶粒长大,也起不到沉淀强化作用,相反会降低ti的细化晶粒和沉淀强化作用。因此本发明中控制n≤0.004%。
20.所述耐磨损腐蚀钢的屈服强度均大于700mpa,抗拉强度大于750mpa,延伸率大于18%。
21.一种700mpa级耐磨损腐蚀钢的制造方法,该方法通过水预脱硫、转炉顶底复合吹炼、lf炉外精炼、板坯连铸、板坯加热、热连轧、层流冷却和卷取制造得到含有上述化学成分的耐磨损腐蚀钢板,具体包括如下方法:
22.1)连铸板坯经加热炉加热至1256~1283℃,加热烧钢气氛为还原性气氛,空燃比低于2.0,低于1100℃时缓慢加热,加热速率7.5~8.5℃/min;1100℃以上高温快烧,加热速率12.1~14.1℃/min,均热段保温时间29~45min,总在炉时间不大于185min;以防止低熔点元素cu、sb在带钢表面的析出而造成的表面缺陷,从而使得板坯表面低熔点cu、sb产生细微缺陷能够充分氧化,形成疏松易除氧化铁皮,以提高带钢表面质量。
23.2)采用两阶段控制轧制,所述粗轧采用3+3模式,粗轧每道次均进行除鳞,粗轧出口温度为1100℃以上;
24.3)精轧采用7机架连续轧制,精轧开轧温度为1084℃~1098℃,精轧终轧温度为909℃~943℃。
25.4)精轧之后进行层流冷却,以28~38℃/s的冷却速率冷却到609℃~643℃卷取,然后空冷到室温。层流冷却采用前段集中冷却。
26.在高于1100℃的温度范围内进行粗轧,带钢不允许摆动,在1084℃~1098℃开始精轧,精轧开轧温度高于1098℃,成品晶粒不易细化,细晶强化效果不好;低于1084℃,带钢尾部降温快,增加精轧机架的负荷,容易导致事故;当终轧温度较低时,有利于铁素体晶粒尺寸的细化,提高细晶强化作用,但与此同时,较低的终轧温度将诱发碳氮化物的形变诱导析出。虽然这种析出物可以抑制奥氏体晶粒长大,起到一定的细晶强化作用和析出强化作用,但是和铁素体析出的纳米级颗粒相比,其尺寸相对较为粗大,降低了沉淀强化作用。因此,本发明终轧温度优选控制在909℃~943℃。轧制结束后进行层流冷却、卷取。层流采用前段集中冷却,冷却速度过低,ti的碳化物会在冷却过程中析出,成品中粗大的粒子增多,在卷取后的沉淀强化作用将不足,为了保证在卷取后获得大量细小的第二相析出粒子,本发明冷却速度设定为28-38℃/s。卷取温度过高,卷取后得到的析出相较粗大,析出强化效果弱;卷取温度过低,则析出物的析出不充分,不能获得期望的强度。因此,本发明卷取温度优选控制在609~643℃。
27.铁水预处理采用转炉冶炼经顶吹或顶底复合吹炼,lf炉脱硫处理,连铸采用电磁搅拌和动态轻压下,以提高连铸板坯的质量。转炉工序采用出钢后加入锑锭的方式,利用氩气进行搅拌,使合金完全熔化、成分均匀。
28.所述连铸坯的厚度为200~230mm。
29.与现有技术相比,本发明的有益效果是:
30.本发明采用高si,辅以耐腐蚀元素cr、cu、sb以及微合金元素ti和w元素的合金成分设计,通过si、mn、cr和w元素的协同作用,以及形成一定量的femncrc、tic和wc,从而提高钢板在大气环境下的抗磨损性能,其抗磨损性能达到现有钢种的15%-25%。并且,本发明的抗腐蚀耐磨损钢板的制备方法简单,不需要热处理工序,可广泛应用于矿石、煤炭等的点对点运输,方便快捷。
具体实施方式
31.通过实施例对本发明进行更详细的描述,这些实施例仅仅是对本发明最佳实施方式的描述,并不对本发明的范围有任何的限制。
32.以下通过实施例对本发明进行较为具体的说明。
33.表1是实施例1-8的化学成分,wt%
34.序号csimnpsalscrcuwtisbn实施例10.0690.651.180.0160.0060.0150.910.140.450.0960.0550.0033实施例20.0720.691.250.0180.0050.0251.250.240.630.0920.0620.0037实施例30.0770.721.320.0170.0040.0351.170.190.550.0870.0910.0034实施例40.0810.771.380.0150.0050.0210.950.230.610.0850.0840.0035实施例50.0830.811.410.0180.0040.0271.340.160.580.0820.0680.0039实施例60.0850.851.450.0130.0030.0301.410.170.510.0790.0750.0034实施例70.0880.901.510.0160.0050.0401.280.150.480.0750.0880.0037实施例80.0900.931.590.0140.0040.0451.480.220.650.0710.0590.0035
35.具有表1化学成分的实施例1-8是通过以下过程制造的:
36.采用转炉冶炼,然后进行炉外精炼,浇铸后得到连铸坯。连铸坯厚度200-230mm,将连铸坯送至热轧生产线,铸坯加热出口温度1256-1283℃,精轧开轧温度1084℃~1098℃,精轧终轧温度909℃~943℃,轧后采用层流冷却,冷却速度为28-38℃/s,卷取温度609℃~643℃,卷取后空冷到室温。
37.本发明钢各个实施例钢的轧制工艺参数如表2所示。
38.表2实施例1-8的轧制工艺参数
[0039][0040]
表3实施例1-8的力学性能
[0041][0042][0043]
从表3中可以看出,本发明实施例钢的屈服强度均大于700mpa以上,抗拉强度均大于750mpa,延伸率均大于18%,冷弯性能均合格,耐磨损率达到spa-h的15%-25%左右。表3能整体表现出本发明钢的力学性能优良。
[0044]
表4本发明实施例钢与比较钢的耐腐蚀性能结果(g/m2.h)
[0045]
序号72h10h2so4+3.5nacl,24h实施例11.08280.8623实施例21.28720.8584实施例31.26510.8650实施例41.30840.8329实施例51.22350.8586实施例61.08290.8639实施例71.09540.8985实施例81.30390.8654spa-h1.64212.1391q345b3.19575.9052
[0046]
依据tb/t 2375-1993,进行72小时周期浸润腐蚀试验。参照jb/t7901-1999,进行10h2so4+3.5nacl的浸泡试验,浸泡时间24h。表4为本发明实施例钢与比较钢的耐大气腐蚀性能结果,其中比较钢为spa-h和q345b。从表4中可以看出,本发明实施例钢的耐候性明显优于spa-h和q345b,能够有效地保证钢板厚度减薄时的使用寿命。
[0047]
上述实施例只为说明本发明的技术构思及特点,而并非对本发明的限制,其目的在于让熟悉此项技术的人士能够了解本发明的内容并据以实施。凡根据本发明精神实质所作的等效变化或修饰,都应涵盖在本发明的保护范围之内。