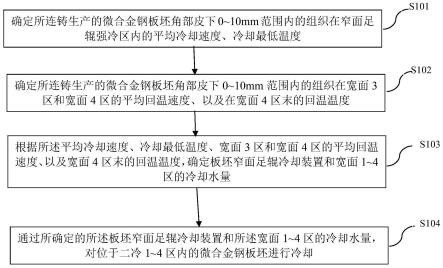
1.本发明属于炼钢-连铸领域,具体涉及一种微合金钢板坯角部裂纹控制的冷却方法及系统。
背景技术:2.向钢中添加微量nb、al、b、v等合金元素,可显著细化成品钢组织晶粒、提升钢的强度和韧性等力学性能,广泛用于微合金钢生产。然而,在实际含nb、al、b、v等元素的微合金钢铸坯母材连铸生产过程中,其角部却高发微横裂纹缺陷,制约了微合金钢的高质与高效化生产。
3.国内外针对微合金钢板坯角部横裂纹控制方法较多。例如,申请号为202110259907.x的发明专利,公开了一种通过优化钢种的微合金成分、保护渣物性参数、结晶器与二冷冷却工艺、结晶器振动与锥度参数等措施的厚板坯角部裂纹控制工艺;申请号为201510976823.2的发明专利,公开了一种通过降低钢中氮含量并添加ti合金,以减少铸坯凝固过程nb(c,n)和aln析出,防止冷轧低合金高强钢边部翘皮缺陷的方法。申请号为201510928837.7的发明专利,同样公开了一种通过向钢中添加ti合金,减少铸坯凝固过程nb(c,n)析出量,并整体控制二冷比水量的防止微合金化钢连铸板坯角部横裂纹的方法。专利号为201510158824.6的发明专利,公开了一种基于窄面双锥度倒角结晶器,并控制钢中氮含量、结晶器水流速度与温度、保护渣物性参数以及二冷区比水量等措施降低含nb钢板坯角部横裂纹的方法。上述这些一种微合金钢板坯角部裂纹控制方法,多通过控制钢中的氮含量、调整合金种类与含量、优化结晶器保护渣与二冷配水工艺等,以提高铸坯角部组织的高温塑性而减少裂纹产生。然而,在实际生产中,钢的合金种类与含量由其力学性能所决定,无法大幅改变。钢中的氮含量受限于冶炼技术,亦难以大幅降低。同时,仅通过优化保护渣物性及整体提高或降低连铸配水比,无法改变直角铸坯角部组织的结构与晶粒尺寸,因而亦无法显著改善铸坯角部组织的热塑性。
4.为了有效避开钢的第三脆性温度区,以减少铸坯角部裂纹产生,专利号为201610004640.9的发明专利,公布了一种通过线圈加热铸坯角部温度,使铸坯角部高温避开钢的第三脆性温度区而减少微合金化板坯角部裂纹的装置及方法。而实际板坯连铸机的二冷区由密排辊列的扇形段构成,无安装加热线圈的位置,且铸流内为高温、高湿环境,实施难度大。鉴于实际板坯连铸过程难以通过优化二冷配水工艺以大幅提高直角铸坯进矫直区角部温度的难题,专利号为201510846986.9和201120136707.7等的专利公开了利用大倒角结晶器,即通过该类结晶器改变传统直角结晶器所生产的4个直角板坯为8个钝角结构板坯,从而大幅提高铸坯进矫直区的角部温度而避开钢的第三脆性区的微合金钢连铸坯角部裂纹控制方法,较有效控制了微合金钢板坯角部裂纹产生。
5.已有研究表明,造成含nb、al、b、v等元素的微合金钢板坯连铸过程角横裂纹高发的主要原因是:在现有板坯连铸工艺条件下,铸坯角部凝固过程中极易形成粗大的奥氏体晶粒,在随后的冷却过程中,钢中的nb、al、b、v等微合金元素与c,n等元素结合形成碳化物、
氮化物或碳氮化物,并在钢组织晶界呈链状形式集中析出,脆化晶界。与此同时,当铸坯角部温度进一步降低降至铁素体转变温度时,粗大的奥氏体晶界将生成网状先共析铁素体膜,大幅弱化钢组织的塑性与强度。当铸坯进入矫直区时,在矫直等作用下,铸坯角部极易因塑性不足沿晶界开裂形成横裂纹缺陷。因此,细化含nb、al、b、v等钢连铸坯角部组织晶粒并弥散其微合金碳氮化物析出以整体提高钢组织的塑性,是从根本上控制微合金钢连铸坯角部横裂纹产生的关键。
6.研究表明,对高温钢组织实施奥氏体向铁素体、铁素体再向奥氏体快速转变的循环相变控冷工艺,可显著细化高温钢组织晶粒,从而消除因粗大奥氏体组织晶粒及其后续晶界形成先共析铁素体膜而大幅降低其高温塑性的难题。同时,若能在含nb、al、b、v等微合金碳氮化物的析出温度区内快速冷却钢组织,可弥散微合金碳氮化物于组织晶内析出,从而解决含nb、al、b、v等微合金钢凝固过程因组织晶界呈链状形式集中析出碳氮化物而脆化晶界的难题,从而从根本上消除铸坯角部裂纹产生。
7.由理论与实测可知,当前主流含nb、al成分微合金钢的碳氮化物晶界析出“鼻子点”温度为900~970℃。对照板坯连铸过程角部温度沿铸流方向的演变可知,该温度区对应铸流位置主要集中在连铸机窄面足辊区内。因此,需对窄面足辊区内铸坯角部实施强喷淋冷却,使其组织快速通过含nb、al碳氮化物的析出“鼻子点”温度。
8.同时,铸坯出结晶器后的角部温度多为950~1000℃。该温度下的钢组织为奥氏体,满足了奥氏体向铁素体、铁素体再向奥氏体快速转变的循环相变工艺实施前组织结构须为原奥氏体的要求,亦需强喷淋冷却控制铸坯角部,促使其组织产生奥氏体向铁素体快速转变。且由于在结晶器出口至立弯段出口的铸流区域内的铸坯凝固坯壳较薄,经窄面足辊区强冷后的铸坯角部,可在出二冷4区前快速回温至组织完全奥氏体化温度,从而实现铸坯角部组织奥氏体向铁素体、铁素体再向奥氏体快速转变的循环相变转变而晶粒细化。
9.然而,在实际板坯连铸生产中,传统窄面足辊区的喷淋仅为中间3~6支单列喷嘴的结构,受喷嘴喷射角度及其水量分布特性的限制,喷射出的扇面边部冷却水无法高效冷却铸坯角部,因而难以实现高温的铸坯角部的快速冷却而使组织产生奥氏体向铁素体快速转变和碳氮化物弥散析出。
10.目前,已开发针对连铸板坯角部强冷却而细化组织晶粒或弥散其微合金碳氮化物析出的方法,主要通过整体增加整个铸坯宽面或窄面的水量。例如,专利号为201010259985.1的发明专利,公开了一种在连铸机垂直段内整体增大铸坯宽面与窄面水量2~5倍的方法,使铸坯表面以3~10℃/s的冷却速冷却。然而,宝钢与攀钢等实践表明,整体大幅增加连铸坯宽面与窄面冷却水量,极易造成铸坯宽面纵裂纹缺陷,且对铸坯角部局部的强冷却作用效果有限。同时,强化铸坯在垂直段内的宽面与窄面冷却,将加速铸坯凝固,使铸坯凝固终点位置提前,从而改变铸坯凝固末端压下等工艺。
11.专利号为201210348907.8的发明专利,公开了一种降低微合金钢板坯角部横裂纹的二次冷却控制方法,其亦通过整体增加出结晶器后铸坯的冷却强度,使铸坯表面以3~8℃/s的冷却速度冷却,弥散化铸坯表层碳氮化物析出,并使组织产生奥氏体向铁素体转变,而后通过弱冷回温实现组织产生铁素体向奥氏体转变而细化钢组织晶粒。同样,专利号201810964557.5的发明专利,公开了一种消除冷轧基料铸坯角部横裂纹的方法,通过整体强冷宽面足辊段内的铸坯,使铸坯表层析出物固溶于基体中,并在弯曲段内弱冷铸坯,避免
其表层组织晶界生成先共析铁素体膜。申请号为201210348907.8和201810964557.5的发明专利与申请号为201010259985.1的专利思想类似,均通过整体增大二冷高温区内铸坯的冷却水量而强冷却其角部。实际实施过程,同样存在易引发铸坯宽面表面纵裂纹、改变铸坯凝固末端位置、以及铸坯角部局部强冷却效果不佳的缺点。
12.专利号为201510005720.1的发明专利,公开了一种在连铸机窄面足辊区下方的立弯段两侧,安装适应铸坯宽度变化且水量独立调控的针对铸坯角部强喷淋冷却系统,强冷细化铸坯角部组织晶粒。针对铸坯角部强冷却的喷淋架是通过一水平驱动装置,实现其喷嘴对准不同宽度的铸坯角部强喷淋冷却。然而,实际板坯连铸立弯段内的空间狭小,难以在其内增加伸缩控制驱动装置实现对喷淋架的整体水平移动。同时,立弯段为高温蒸汽环境,驱动结构难以长时间服役。此外,窄面足辊下方的铸坯角部温度往往已降至900℃以下,低于含nb、al、b等碳氮化物的析出“鼻子点”温度,无法有效控制该类碳氮化物的弥散析出。
13.鉴于专利号为201510005720.1专利喷淋架难以驱动的不足,专利号为201510534316.3的发明专利,公开了一种通过在连铸机窄面足辊区的末端加装3~7组针对铸坯内弧与外弧角部强喷淋冷却的喷嘴,以强冷却铸坯角部的连铸坯角部组织晶粒细化的控制系统及方法。在该专利中,强冷却喷淋架以固定连接方式安装在窄面足辊的下方。但在实际生产中,结晶器及其窄面足辊延长喷淋架需由天车吊装入连铸机狭小的铸流内,在装入时,极易因天车晃动而撞坏该延长强冷却喷淋架。同时,带有延长强冷却喷淋架的结晶器停放需新建专用的结晶器存放台。此外,该专利的喷淋结构易装在窄面足辊下方,即铸坯角部温度亦已降至900℃以下,低于含nb、al、b等碳氮化物的析出“鼻子点”温度,同样存在无法有效控制该类碳氮化物的弥散析出的问题。
14.而专利号为201810329636.9的发明专利,公开了一种微合金钢薄板坯角部裂纹控制装备与工艺,该控制装备包括新增结晶器窄面下口强喷淋系统,使薄板坯角部以20℃/s~35℃/s的平均冷却速度强冷却铸坯边角部,从而弥散薄板坯角部微合金碳氮化物析出,并细化薄板坯角部组织晶粒。但薄板坯连铸机与常规板坯、宽厚板坯、以及特厚板坯连铸机的结构相差较大,薄板坯连铸机结晶器窄面下方无足辊结构,该专利仅需在薄板坯结晶器窄面下方增加一组针对铸坯内弧与外弧角部强冷喷淋的交错式布局喷淋架即可。而常规板坯、宽厚板坯、以及特厚板坯连铸机的窄面下方是带有侧导辊、窄面喷嘴等复杂结构的窄面足辊。专利号为201820702023.0的实用新型专利,同样公开了一种与专利号为201810329636.9相似、在薄板坯结晶器窄面下方增加一组针对薄板坯内弧与外弧角部交错式布局的强冷喷淋结构,其亦仅适用于薄板坯连铸机。
15.专利号为201911192737.7的发明专利,公开了一种控制连铸板坯角部奥氏体晶粒尺寸的方法和装置。该装置通过缩短结晶器窄面铜板,并在其下方足辊区安装多排强喷淋喷嘴。其中,上部喷嘴向下倾斜与铸坯表面成30~80
°
夹角,下部喷嘴垂直铸坯表面喷淋,提高铸坯出结晶器后窄面的冷却强度,细化连铸坯角部奥氏体晶粒。但该足辊强喷淋装置亦是强冷却整个铸坯窄面。同时,其延长的喷淋结构,亦与专利号为201510534316.3的发明专利类似,不利于结晶器上线安装。
16.此外,题分别为“微合金钢连铸坯角部裂纹控制技术研发及应用”和“含铌微合金钢连铸坯角部裂纹控制二冷新工艺”的学术论文中,开发出了一种立足于结晶器窄面足辊的铸坯角部强冷却结构,其虽然针对铸坯角部局部强冷却并独立回路控制,但从图中可以
看出,该控冷结构仍然是通过一对安装在窄面足辊下方针对铸坯内弧角部或内弧与外弧角部喷淋的喷淋架,其实质是专利号为201510534316.3的专利技术的一种实际应用。
17.因此,结合实际常规板坯、宽厚板坯以及特厚板坯连铸机结构及其微合金钢连铸生产工艺特点、连铸机在线调宽等实际生产要求,于连铸结晶器出口下方开发一种便于现场安装并稳定实施铸坯角部组织强喷淋冷却的控冷装置及其自动化配水控制系统,基此开发满足铸坯角部皮下0~10mm范围内组织发生奥氏体向铁素体、铁素体再向奥氏体循环相变晶粒细化和微合金碳氮化物弥散析出而高塑化铸坯角部组织的裂纹控制冷却工艺,实现微合金钢常规板坯、宽厚板坯、以及特厚板坯角部无缺陷连铸生产,具有重要的意义和广阔的推广应用前景。
技术实现要素:18.本发明要解决的技术问题是针对上述现有一种微合金钢板坯角部裂纹控制技术不足,提供一种微合金钢板坯角部裂纹控制的冷却方法及系统。
19.本发明一方面提供了一种微合金钢板坯角部裂纹控制的冷却方法,包括:
20.确定所连铸生产的微合金钢板坯角部皮下0~10mm范围内的组织在窄面足辊强冷区内的平均冷却速度、冷却最低温度;
21.确定所连铸生产的微合金钢板坯角部皮下0~10mm范围内的组织在宽面3区和宽面4区的平均回温速度、以及在宽面4区末的回温温度;
22.根据所述平均冷却速度、冷却最低温度、宽面3区和宽面4区的平均回温速度、以及宽面4区末的回温温度,确定位于结晶器下方的板坯窄面足辊冷却装置和宽面1~4区的冷却水量;
23.通过所确定的所述板坯窄面足辊冷却装置和所述宽面1~4区的冷却水量,对位于二冷1~4区内的微合金钢板坯进行冷却。
24.进一步的,还包括:
25.获取所述连铸生产的微合金钢板坯的连铸工艺参数;
26.基于所述连铸工艺参数,利用商业有限元软件或自编程建立包括结晶器和二冷1~4区阶段的连铸板坯三维非稳态温度场计算模型,并计算获得所连铸生产的微合金钢板坯温度场分布;
27.根据所述计算获得的微合金钢板坯温度场分布,确定所连铸生产的微合金钢板坯角部皮下0~10mm范围内的组织在窄面足辊区内的平均冷却速度、冷却最低温度、以及确定所连铸生产的微合金钢板坯角部皮下0~10mm范围内的组织在宽面3区和宽面4区内的平均回温速度、以及在宽面4区末的回温温度;
28.其中,所述连铸工艺参数包括铸坯断面尺寸、拉速、以及所连铸生产的微合金钢板坯的钢水过热度、结晶器的宽面冷却水量及水温差、以及结晶器的窄面冷却水量及水温差。
29.进一步的,所述铸坯断面尺寸为2100mm
×
250mm,拉速为0.8~1.3m/min、以及铸造所述连铸生产的微合金钢板的钢水过热度为25℃;所述结晶器宽面冷却水量为3250l/min、水温差7.5℃,所述结晶器窄面冷却水量为390l/min、水温差8.2℃。
30.进一步的,所述连铸生产的微合金钢板坯角部皮下0~10mm范围内的组织在窄面足辊强冷区内的平均冷却速度≥5℃/s、冷却最低温度为550~600℃、以及其在宽面3区和
宽面4区内的平均回温速度均≥3.5℃/s、在宽面4区末的回温温度≥900℃。
31.本发明另一方面还提供了一种微合金钢板坯角部裂纹控制的冷却系统,包括:
32.第一参数确定模块,用于确定所连铸生产的微合金钢板坯角部皮下0~10mm范围内的组织在窄面足辊强冷区内的平均冷却速度、冷却最低温度;
33.第二参数确定模块,用于确定所连铸生产的微合金钢板坯角部皮下0~10mm范围内的组织在宽面3区和宽面4区的平均回温速度、以及在宽面4区末的回温温度;
34.第三参数确定模块,用于根据所述平均冷却速度、冷却最低温度、宽面3区和宽面4区的平均回温速度、以及宽面4区末的回温温度,确定位于结晶器下方的板坯窄面足辊冷却装置和宽面1~4区的冷却水量;
35.冷却模块,用于通过所确定的所述板坯窄面足辊冷却装置和所述宽面1~4区的冷却水量,对位于二冷1~4区内的微合金钢板坯进行冷却。
36.进一步的,所述板坯窄面足辊冷却装置包括:
37.第一喷嘴组,设在所述窄面足辊面侧的框架边部,并与所述通水通道连通;
38.第二喷嘴组,设在所述窄面足辊面侧的框架另一侧边部,与所述第一喷嘴组在所述窄面足辊面侧的框架的宽度上对称;
39.通水通道,设在所述窄面足辊框架内,与所述第一喷嘴组和第二喷嘴组分别连通;
40.供水管路,与所述通水通道连通,所述供水管路上设有流量计、气动调节阀和截止阀,所述流量计、气动调节阀和截止阀分别与所述冷却模块电连接,所述冷却模块用于根据所确定的所述窄面足辊冷却装置的水量,启动所述截止阀,基于所述流量计检测到的所述供水管路的流量,控制所述气动调节阀的开度大小。
41.进一步的,所述板坯窄面足辊冷却装置还包括工控机、人机交互界面、plc控制系统,所述工控机、plc控制系统、流量计和气动调节阀通过电缆与所述plc控制系统连接,所述工控机与所述plc控制系统通信连接,所述人机交互界面安装于所述工控机内,所述人机交互界面包括系统维护后台、实时工况信息显示与操作前台界面,所述系统维护后台包括数据通讯模块、数据实时采集模块、水表设定模块、流量标定模块、水量实时下发模块、数据存储模块和历史数据查询模块;
42.其中,数据通讯模块用于所述工控机与所述plc控制系统之间的实时通讯连接,并显示所述工控机与所述plc控制系统之间的当前通讯状态;数据实时采集模块用于实时采集所述连铸生产的微合金钢板坯的钢种、炉号、拉速、气动调节阀开度、流量计流量数据;水表设定模块用于新建、修改并保存水表的功能;水量实时下发模块用于根据实时工况信息显示与操作前台界面所选中的水表和水量下发模式,下发与当前拉速匹配的冷却水量;数据存储模块用于将对应数据采集周期的钢种、炉号、拉速、气动调节阀开度、流量计流量以及系统当前时间实时数据存储于设定的数据库中;所述历史数据查询模块用于根据实时工况信息显示与操作前台界面所选择的数据查询方式、数据查询范围,调用数据存储数据库,提取拟查询的数据。
43.进一步的,所述第一喷嘴组和第二喷嘴组设置在原有窄面足辊中间列喷嘴组的两侧,沿所述连铸生产的微合金钢板坯的拉速方向均设置4~6个喷嘴;所述第一喷嘴组的4~6个喷嘴的中心位于同一直线上,且该4~6个所述第一喷嘴组的喷嘴中心所在的直线与所述原有中间列喷嘴组的喷嘴中心所在的直线相平行;所述第二喷嘴组位于所述原有中间列
喷嘴组的另一侧,其4~6个喷嘴的中心位于同一直线上,且4~6个所述第二喷嘴组的喷嘴中心所在的直线与所述原有中间列喷嘴组的喷嘴中心所在的直线相平行;4~6个所述第一喷嘴组的喷嘴和4~6个所述第二喷嘴组的喷嘴的高度分别两两对应相同,位于最高位置的第一喷嘴组的喷嘴和第二喷嘴组的喷嘴从原有中间列喷嘴组的最上面或第2个喷嘴开始,且各喷嘴的安装高度与对应高度处的原有中间列喷嘴组的喷嘴高度相同,相邻的两个所述第一喷嘴组的喷嘴之间的距离和相邻的两个所述第二喷嘴组的喷嘴之间的距离均相同;
44.其中,所述第一喷嘴组的喷嘴的喷射角为45
°
~90
°
,喷嘴末端距铸坯窄面表面的垂直高度为40~100mm,喷嘴组各喷嘴的轴向延长线与对应的铸坯窄面角部相交,所述第二喷嘴组的喷嘴的喷射角为-45
°
~-90
°
,喷嘴末端距铸坯窄面表面的垂直高度为40~100mm,喷嘴组各喷嘴的轴向延长线与对应的铸坯窄面角部相交;所述第一喷嘴组的喷嘴和第二喷嘴组的喷嘴喷射出的冷却水对所述连铸生产的微合金钢板坯窄面角部的作用宽度为由角部向窄面中心方向的30~60mm。
45.本发明再一方面还提供了一种工控机设备,包括存储器、处理器以及存储在所述存储器中并可在所述处理器上运行的计算机程序,其特征在于,所述处理器执行所述计算机程序时实现如上述所述一种微合金钢板坯角部裂纹控制的冷却方法的步骤。
46.本发明再又一方面还提供了一种工控机可读存储介质,所述工控机可读存储介质存储有计算机程序,所述计算机程序被处理器执行时实现如上述所述一种微合金钢板坯角部裂纹控制的冷却方法的步骤。
47.本发明提供的一种微合金钢板坯角部裂纹控制的冷却方法及系统,相比于现有技术,通过本发明所确定的窄面足辊冷却装置和铸坯宽面1和2区强冷却控制,实现微合金钢板坯角部皮下0~10mm范围内的组织在窄面足辊区内快速完成奥氏体向铁素体相变,并弥散其微合金碳氮化物析出,而后弱冷却控制宽面3区和宽面4区水量,使铸坯角部皮下0~10mm范围内的组织在宽面4区出口前再次完全奥氏体化,从而使板坯角部皮下0~10mm范围内的组织完成奥氏体至铁素体再到奥氏体2次相变而晶粒大幅细化,高塑化含nb、al微合金钢铸坯角部组织而控制其裂纹产生。
附图说明
48.本发明的下列附图在此作为本发明实施例的一部分用于理解本发明。附图中示出了本发明的实施例及其描述,用来解释本发明的原理。
49.附图中:
50.图1为本发明实施例提供的一种微合金钢板坯角部裂纹控制的冷却方法的流程示意图;
51.图2为根据本发明另一个实施例提供的一种微合金钢板坯角部裂纹控制的冷却方法的流程示意图;
52.图3为本发明实施后的含nb微合金钢的铸坯角部组织析出物透射电镜检测图;
53.图4为本发明实施后的铸坯角部组织金相形貌;
54.图5为根据本发明的一个可选实施例的一种微合金钢板坯角部裂纹控制的冷却系统的模块连接示意图;
55.图6为本发明实施例提供的板坯窄面足辊冷却装置的结构示意图;
56.图7为本发明实施例提供的供水管路的结构示意图;
57.图8为本发明实施例提供的板坯窄面足辊冷却装置的局部结构示意图;
58.图9为本发明实施例提供的针对铸坯内弧与外弧窄面角部强冷却的板坯窄面足辊冷却装置与中间喷嘴横向布置图;
59.图10为本发明实施例提供的板坯窄面足辊冷却装置的运行原理与逻辑框图;
60.图11是本发明一实施例中工控机设备的一结构示意图;
61.图12是本发明一实施例中工控机设备的另一结构示意图。
62.图中:
63.1-通水通道2-供水管路,3-窄面足辊框架,4-流量计,5-气动调节阀,6-截止阀,7-新增进水口,8-工控机,9-plc控制系统,10-原有中间列喷嘴,11-第一喷嘴,12-第二喷嘴,13-喷淋管。
具体实施方式
64.在下文的描述中,给出了大量具体的细节以便提供对本发明更为彻底的理解。然而,对于本领域技术人员而言显而易见的是,本发明可以无需一个或多个这些细节而得以实施。在其他的例子中,为了避免与本发明发生混淆,对于本领域公知的一些技术特征未进行描述。
65.应予以注意的是,这里所使用的术语仅是为了描述具体实施例,而非意图限制根据本发明的示例性实施例。如在这里所使用的,除非上下文另外明确指出,否则单数形式也意图包括复数形式。此外,还应当理解的是,当在本说明书中使用术语“包含”和/或“包括”时,其指明存在所述特征、整体、步骤、操作、元件和/或组件,但不排除存在或附加一个或多个其他特征、整体、步骤、操作、元件、组件和/或它们的组合。
66.现在,将参照附图更详细地描述根据本发明的示例性实施例。然而,这些示例性实施例可以多种不同的形式来实施,并且不应当被解释为只限于这里所阐述的实施例。应当理解的是,提供这些实施例是为了使得本发明的公开彻底且完整,并且将这些示例性实施例的构思充分传达给本领域普通技术人员。
67.本发明提供的一种微合金钢板坯角部裂纹控制的冷却方法,参见图1,包括如下步骤:
68.s101、确定所连铸生产的微合金钢板坯角部皮下0~10mm范围内的组织在窄面足辊强冷区内的平均冷却速度、冷却最低温度。
69.s102、确定所连铸生产的微合金钢板坯角部皮下0~10mm范围内的组织在宽面3区和宽面4区的平均回温速度、以及在宽面4区末的回温温度。
70.s103、根据所述平均冷却速度、冷却最低温度、宽面3区和宽面4区的平均回温速度、以及宽面4区末的回温温度,确定板坯窄面足辊冷却装置和宽面1~4区的冷却水量。
71.s104、通过所确定的所述板坯窄面足辊冷却装置和所述宽面1~4区的冷却水量,对位于二冷1~4区内的微合金钢板坯进行冷却。
72.下面对一种铸坯厚度为250mm、宽度2100mm的ah36含nb微合金钢板坯角部裂纹控制的冷却方法的实施例做进一步说明,其钢种成分如表1所示:
73.表1 ah36含nb高强船板钢的主要成分(wt%)
74.csimnpsalnnb0.090.251.500.0150.0050.030.00520.03
75.本实施例中,一种微合金钢板坯角部裂纹控制的冷却方法,立足于窄面足辊,针对连铸生产厚度为250mm厚度板坯内弧与外弧窄面角部的强冷却,根据现场连铸的拉速变化在线实时下发满足板坯角部皮下0~10mm范围组织快速发生奥氏体至铁素体再到奥氏体循环相变晶粒细化与nb(c,n)弥散析出的板坯窄面足辊冷却装置、以及宽面1~4区分别对应的冷却水量,实现ah36含nb钢板坯连铸过程铸坯4个角皮下0~10mm深度范围内的室温铁素体晶粒细化至≤35μm和nb(c,n)弥散析出,进而高塑化控制铸坯角部裂纹产生。
76.通过本发明所确定的板坯窄面足辊冷却装置、以及宽面1~4区分别对应的冷却水量对连铸生产的微合金钢板坯进行强冷却控制,实现微合金钢板坯角部皮下0~10mm范围内的组织在窄面足辊区内快速完成奥氏体向铁素体转变,并弥散其微合金碳氮化物析出,而后弱冷却控制宽面3区和宽面4区水量,使铸坯角部皮下0~10mm范围内的组织在宽面4区出口前再次完全奥氏体化,从而使板坯角部组织完成奥氏体至铁素体再到奥氏体循环相变而晶粒大幅细化,高塑化ah36含nb微合金钢板坯角部组织而控制其裂纹产生。
77.在一些实施方式中,参见图2,冷却方法还包括:
78.s201、获取所述连铸生产的微合金钢板坯的连铸工艺参数。
79.其中,所述连铸工艺参数包括铸坯断面尺寸、拉速、以及所连铸生产的微合金钢板坯的钢水过热度、结晶器的宽面冷却水量及水温差、以及结晶器的窄面冷却水量及水温差。
80.这里,所述铸坯断面尺寸为2100mm
×
250mm,拉速为0.8~1.3m/min、以及铸造所述连铸生产的微合金钢板的钢水过热度为25℃;所述结晶器宽面冷却水量为3250l/min、水温差7.5℃,所述结晶器窄面冷却水量为390l/min、水温差8.2℃。
81.s202、基于所述连铸工艺参数,利用商业有限元软件或自编程建立包括结晶器和二冷1~4区阶段的连铸板坯三维非稳态温度场计算模型,并计算获得所连铸生产的微合金钢板坯温度场分布;
82.s203、根据所述计算获得的微合金钢板坯温度场分布,确定所连铸生产的微合金钢板坯角部皮下0~10mm范围内的组织在窄面足辊区内的平均冷却速度、冷却最低温度、以及确定所连铸生产的微合金钢板坯角部皮下0~10mm范围内的组织在宽面3区和宽面4区内的平均回温速度、以及在宽面4区末的回温温度。
83.更进一步的,所述连铸生产的微合金钢板坯角部皮下0~10mm范围内的组织在窄面足辊强冷区内的平均冷却速度≥5℃/s、冷却最低温度为550~600℃、以及其在宽面3区和宽面4区内的平均回温速度均≥3.5℃/s、在宽面4区末的回温温度≥900℃。
84.这里,根据表2计算所确定的ah36钢连铸板坯不同拉速下的确定连铸生产的微合金钢板坯角部皮下0~10mm范围内的组织在窄面足辊区内的平均冷却速度、宽面3区和宽面4区内的平均回温速度、以及宽面4区末的回温温度,下发表2所示的板坯窄面足辊原有中间列喷嘴组10、第一喷嘴组11、第二喷嘴组12、以及宽面1~4区的冷却水量试验生产2100mm
×
250mm断面连铸坯。将试验生产所得的微合金钢板坯的内弧与外弧角部皮下0~10mm范围内的组织进行透射与金相显微镜检测,获得图3和图4所示的坯角部皮下10mm处的nb(c,n)弥散状分布和晶粒细化组织。将表2所示的不同拉速下“冷却方法”所对应的板坯窄面足辊冷却装置、以及所述宽面1~4区分别对应的冷却水量作为ah36含nb钢2100mm
×
250mm断面板
坯连铸角部裂纹控制的冷却方法。
85.表2 2100mm
×
250mm断面ah36钢连铸部分拉速与水量的关系(水量单位:l/min)
[0086][0087]
注:表2中a为某一水量值。
[0088]
本发明提供的一种微合金钢板坯角部裂纹控制的冷却方法,可有效强冷却位于板坯连铸机窄面足辊区内的微合金钢连铸坯角部,满足铸坯角部组织循环相变晶粒细化与微合金碳氮化物弥散析出工艺的强冷却要求。
[0089]
本发明提供的一种微合金钢板坯角部裂纹控制的冷却系统,参见图5,包括第一参数确定模块、第二参数确定模块、第三参数确定模块和冷却模块。各功能模块详细说明如下:
[0090]
第一参数确定模块51,用于确定所连铸生产的微合金钢板坯角部皮下0~10mm范围内的组织在窄面足辊强冷区内的平均冷却速度、冷却最低温度;
[0091]
第二参数确定模块52,用于确定所连铸生产的微合金钢板坯角部皮下0~10mm范围内的组织在宽面3区和宽面4区的平均回温速度、以及在宽面4区末的回温温度;
[0092]
第三参数确定模块53,用于根据所述平均冷却速度、冷却最低温度、宽面3区和宽面4区的平均回温速度、以及宽面4区末的回温温度,确定板坯窄面足辊冷却装置和宽面1~4区的冷却水量;
[0093]
冷却模块54,用于通过所确定的所述板坯窄面足辊冷却装置和所述宽面1~4区的冷却水量,对位于二冷1~4区内的微合金钢板坯进行冷却。
[0094]
本发明提供的一种微合金钢板坯角部裂纹控制的冷却系统,相比于现有技术,通过本发明所确定的窄面足辊冷却装置和铸坯宽面1和2区强冷却控制,实现微合金钢板坯角部皮下0~10mm范围内的组织在窄面足辊区内快速完成奥氏体向铁素体转变,并弥散其微合金碳氮化物析出,而后弱冷却控制宽面3区和宽面4区水量,使铸坯角部皮下0~10mm范围内的组织在宽面4区出口前再次完全奥氏体化,从而使板坯角部组织完成奥氏体至铁素体
再到奥氏体循环相变而晶粒大幅细化,高塑化微合金钢铸坯角部组织而控制其裂纹产生。
[0095]
在一实施例中,冷却系统还包括:
[0096]
参数获取模块,用于获取所述连铸生产的微合金钢板坯的连铸工艺参数;
[0097]
温度场分布范围获取模块,用于基于所述连铸工艺参数,利用商业有限元软件或自编程建立包括结晶器和二冷1~4区阶段的连铸板坯三维非稳态温度场计算模型,并计算获得所连铸生产的微合金钢板坯温度场分布;
[0098]
参数确定模块,用于根据所述计算获得的微合金钢板坯温度场分布,确定所连铸生产的微合金钢板坯角部皮下0~10mm范围内的组织在窄面足辊区内的平均冷却速度、冷却最低温度、以及确定所连铸生产的微合金钢板坯角部皮下0~10mm范围内的组织在宽面3区和宽面4区内的平均回温速度、以及在宽面4区末的回温温度。
[0099]
在一实施例中,参见图6至9,所述板坯窄面足辊冷却装置包括第一喷嘴组、第二喷嘴组、通水通道1和供水管路2,第一喷嘴组设在窄面足辊面侧的框架3边部,并与通水通道1连通;第二喷嘴组设在窄面足辊面侧的框架3另一侧边部,与第一喷嘴组在窄面足辊面侧的框架3的宽度上对称;通水通道1设在窄面足辊框架3内,与第一喷嘴组和第二喷嘴组分别连通;供水管路2与通水通道1连通,供水管路2上设有流量计4、气动调节阀5和截止阀6,流量计4、气动调节阀5和截止阀6分别与冷却模块电连接,冷却模块用于根据所确定的板坯窄面足辊冷却装置的水量,启动截止阀6,基于流量计4检测到的供水管路的流量,控制气动调节阀5的开度大小。
[0100]
本发明提供的板坯窄面足辊冷却装置立足于连铸机窄面足辊,由窄面足辊新增外接供水管路2、窄面足辊面侧的框架3内设置通水通道1、针对微合金钢板坯的内弧与外弧窄面角部强冷却的足辊边部设置第一喷嘴组和第二喷嘴组。其中,供水管路2独立于窄面足辊的侧部喷嘴组件,由尺寸为dn50或dn65的不锈钢管与二冷水阀站内的二冷主供水管路2相连,而后依次连接截止阀6、气动调节阀5、流量计4水路控制与检测元件,其铺设至结晶器振动框架3附近再分成2路,通过金属软管分别与通至结晶器两侧窄面足辊面侧的框架3新增进水口7相连接。窄面足辊面侧的框架3新增外接供水管路2的供水能力,设计原则为:在满足最大连铸拉速下的铸坯4个角皮下0~10mm深度范围的微合金碳氮化物弥散化析出与奥氏体向铁素体快速转变的水量基础上,上浮20%。窄面足辊面侧的框架3新增外接的供水管路2的各控制与检测元件流量参数与供水管路2的供水能力相匹配。与结晶器两侧的窄面足辊面侧的框架3新增接水点相连接的金属软管7的公称直径选为dn40或dn50;其中,窄面足辊面侧的框架3设在结晶器的下方。
[0101]
在一实施例中,参见图10,板坯窄面足辊冷却装置还包括工控机8、人机交互界面、plc控制系统9,工控机8、plc控制系统9、流量计4和气动调节阀5通过电缆与plc控制系统9连接,工控机8与plc控制系统9通信连接,人机交互界面安装于工控机8内,人机交互界面包括系统维护后台、实时工况信息显示与操作前台界面,系统维护后台包括数据通讯模块、数据实时采集模块、水表设定模块、流量标定模块、水量实时下发模块、数据存储模块和历史数据查询模块;其中,数据通讯模块用于工控机8与plc控制系统9之间的实时通讯连接,并显示工控机8与所述plc控制系统9之间的当前通讯状态;数据实时采集模块用于实时采集连铸生产的微合金钢的钢种、炉号、拉速、气动调节阀开度、流量计4流量数据;水表设定模块用于新建、修改并保存水表的功能;水量实时下发模块用于根据实时工况信息显示与操
作前台界面中的水表和水量下发模式,下发与当前拉速匹配的冷却水量;数据存储模块用于将对应数据采集周期的钢种、炉号、拉速、气动调节阀开度、流量计4流量以及系统当前时间实时数据存储于设定的数据库中;历史数据查询模块用于根据实时工况信息显示与操作前台界面所选择的数据查询方式、数据查询范围,调用数据存储数据库,提取拟查询的数据。
[0102]
其中,数据实时采集模块的数据采集周期一般选择0.5~3s;流量标定模块用于负责标定气动调节阀开度与流量关系,使得实时工况信息显示与操作前台界面在选择气动调节阀开度水量下发模式或流量水量下发模式下,均可准确下发要求的水量。实时工况信息显示与操作前台界面,包括实时工况显示区和操作区2部分。所述实施工况显示区,采用数字与曲线形式实时显示连铸钢种、炉号、拉速、气动调节阀开度、实际下发水量、以及设定下发水量信息。操作区包括水量下发模式选择下拉列表、安全水量设定按钮、水表选择下拉列表、历史数据查询按钮、后台维护按钮、系统退出按钮构成。其中,水量下发模式选择下拉列表中包括气动调节阀开度水量下发模式、流量水量下发模式、安全水量模式。选中气动调节阀开度水量下发模式和流量水量下发模式,系统均根据经流量标定模块标定后的气动调节阀开度与水量间的关系,由水量实时下发模块根据实时工况信息显示与操作前台界面所选中的水表,准确下发水表中与当前拉速匹配的水量。安全水量模式为各拉速下,水量实时下发模块均下发同一个固定水量值,一般可设定40~80l/min,该值由安全水量设定按钮设定和修改;水表选择下拉列表具备自动关联维护后台所建立的水表的功能。经水表选择下拉列表选中水表后,水量实时下发模块将匹配对应名称的水表,并根据当前拉速按照水量下发模式选择列表所选中的模式,准确下发水量;历史数据查询按钮,具备供操作人员按照时间段或单炉号与多炉号查询的方式,以曲线、数据表的形式提供拟查询的炉号、拉速、气动调节阀开度、实际下发水量的部分或全部信息的功能;后台维护按钮,提供进入系统维护后台的通道;系统退出按钮,退出并关闭系统。
[0103]
plc控制系统9与工控机8、调节阀及流量计4相连。通过plc控制系统9将调节阀与流量计4信号转变后送至工控机8,由人机交互界面系统维护后台接收、存储和实时工况信息显示与操作前台界面显示,并根据人机交互界面下发的水量(经流量标定模块标定后,转化为气动调节阀开度)或气动调节阀开度信号,由plc控制系统9实时调节调节阀的开度,从而控制所述板坯角部裂纹控制的冷却系统的水量实时、准确下发。
[0104]
参见图11,板坯窄面足辊冷却装置的运行原理与逻辑如下:
[0105]
控制系统启动后,后台维护界面通过与plc控制系统9间的通讯模块,判定工控机8与plc控制系统9是否通讯良好。如果通讯失败,则提示通讯失败,否则读取上次系统关闭前保存的气动调节阀开度与流量关系和安全水量。若需要进行气动调节阀开度与流量关系重新标定,则点击后台维护按钮,进入流量标定模块,并基于数据实时采集模块实时采集空载条件下的气动调节阀开度与流量计4流量数据,进行流量重新标定并保存。同样,若需要修订安全水量,则点击安全水量设定按钮,设置新的安全水量。若上述环节均不需要,则根据当前连铸钢种,确定是否需新建或修订水表,如果需要,则点击后台维护按钮,进入水表设定模块,新建或修订水表。否则,进入水表选择下拉列表和水量下发模式下拉列表,选定对应的水表和水量下发模式,水量实时下发模块根据所选择的水表与水量下发模式,经plc控制系统9实时下发不同拉速水量下的气动调节阀开度,为所述的板坯角部裂纹控制的冷却
系统准确下发冷却水量,并将对应各数据采集周期的钢种、炉号、拉速、气动调节阀开度、流量计4流量以及系统当前时间实时数据存储于设定的数据库中。
[0106]
基于上述板坯窄面足辊冷却装置,结合所生产的微微合金种及其铸坯断面尺寸、拉速、钢水过热度等参数,由板坯窄面足辊冷却装置的自动化配水控制系统和连铸机原二级控制系统,根据连铸拉速在线实时下发按照下述方法确定的板坯角部裂纹控制的冷却系统第一喷嘴组和第二喷嘴组水量、窄面足辊的原有中间列喷嘴10回路水量、以及二冷宽面1~4区水量。连铸机弧形区各段、矫直区各段及其水平段二冷各区的水量保持与原二冷各区的水量不变。
[0107]
所述的不同微微合金种及其连铸断面与拉速下,针对出铸坯内弧与外弧窄面角部强喷淋冷却的板坯角部裂纹控制的冷却系统的第一喷嘴组和第二喷嘴组水量、窄面足辊原有中间列喷嘴10回路水量、以及二冷宽面1~4区水量的确定方法为:由连铸板坯二冷温度场计算机数值模拟计算和现场试验生产下的铸坯内弧与外弧角部皮下0~10mm范围的组织晶粒细化效果共同确定。
[0108]
进一步的,原有中间列喷嘴组包括沿连铸生产的微合金钢板坯的长度方向分布设置的4~6个中间喷嘴10,且4~6个中间喷嘴10的中心位于同一直线上;窄面足辊冷却装置包括第一喷嘴组和第二喷嘴组,第一喷嘴组和第二喷嘴组设置在原有窄面足辊中间列喷嘴组的两侧,沿连铸生产的微合金钢板坯的拉速方向均设置4~6个第一喷嘴11;第一喷嘴组的4~6个第一喷嘴11的中心位于同一直线上,且该4~6个第一喷嘴组的第一喷嘴11中心所在的直线与原有中间列喷嘴组的中间喷嘴10的中心所在的直线相平行;第二喷嘴组位于原有中间列喷嘴组的另一侧,其4~6个第二喷嘴12的中心位于同一直线上,且4~6个第二喷嘴组的第二喷嘴12中心所在的直线与原有中间列喷嘴组的中间喷嘴10中心所在的直线相平行;4~6个第一喷嘴组的第一喷嘴11和4~6个第二喷嘴组的第二喷嘴12的高度分别两两对应相同,位于最高位置的第一喷嘴组的第一喷嘴11和第二喷嘴组的第二喷嘴12从原有中间列喷嘴组的最上面或第2个中间喷嘴10开始,且各喷嘴的安装高度与对应高度处的原有中间列喷嘴组的中间喷嘴10高度相同,相邻的两个第一喷嘴组的第一喷嘴11之间的距离和相邻的两个第二喷嘴组的第二喷嘴12之间的距离均相同;其中,第一喷嘴组的第一喷嘴11的喷射角为45
°
~90
°
,第一喷嘴11末端距铸坯窄面表面的垂直高度为40~100mm,第一喷嘴组上的各喷嘴的延长线与对应的铸坯窄面角部相交,第二喷嘴组的第二喷嘴12的喷射角为-45
°
~90
°
,第二喷嘴12末端距铸坯窄面表面的垂直高度为40~100mm,第二喷嘴组上的各喷嘴的延长线与对应的铸坯窄面角部相交,第一喷嘴组的第一喷嘴11和第二喷嘴组的第二喷嘴12喷射出的冷却水对所述连铸生产的微合金钢板坯窄面角部的作用宽度为30~60mm。
[0109]
窄面足辊面侧的框架3内新增的供水管路2,独立于原有窄面足辊中间列喷嘴组件的供水管路,在窄面足辊面侧的框架3内的边部两侧新开两条相互连通,并平行于侧部喷嘴组件的通水通道1。两条通水通道1的直径一般设计为25~40mm,每条通水通道1的最大通水量一般设计为100l/min,由窄面足辊面侧的框架3的底部竖直通至与侧部喷嘴组件的最上面或倒数第二个侧部喷嘴的高度平齐。两条通水通道1均沿铸坯厚度方向的位置,根据窄面足辊面侧的框架3的宽度和连铸坯厚度而定,设计原则为:保证窄面足辊面侧的框架3的两条通水通道1与针对铸坯内弧和外弧窄面角部强冷却的第一喷嘴组和第二喷嘴组连接互
通,以保证对第一喷嘴组和第二喷嘴组的稳定供水。框架3内边部新增的两条通水通道1距足辊面侧的位置为靠近足辊面侧的通水通道1壁面距足辊面侧框架3边的距离为5~30mm。两条窄面足辊面侧的框架3内边部新增的通水通道1的连通,可在现有窄面足辊面侧的框架3的下部密封焊接长度40~80mm、横截面与现有窄面足辊面侧的框架3底部结构相同的延长框架3,在延长框架3内横向钻孔,并在竖直方向上与窄面足辊面侧的框架3内边部两条新增通水通道1互通。也可在每条边部新增通水通道1对应的窄面足辊面侧的框架3单独设置新增接水点,由金属软管7连接2个新增接水点汇合实现连通。窄面足辊面侧的框架3新增接水点与窄面足辊面侧的框架3内新增边部通水通道1相连接,接口尺寸为dn40或dn50,与由结晶器振动框架3铺设至结晶器两侧窄面足辊面侧的框架3新增接水点附近的金属软管7相连接。
[0110]
针对铸坯内弧与外弧窄面角部强冷却的足辊边部的新增强喷淋结构,由第一喷嘴组和第二喷嘴组构成。第一喷嘴11和第二喷嘴12均从原有的中间列喷嘴10上部的第一排或第二排起水平高度起,沿窄面足辊高度方向设计3~5排,每排可与原有中间列喷嘴10平齐,使得窄面足辊的各辊间的喷嘴横向数量为3个。第一喷嘴11和第二喷嘴12分别连接的喷淋管13的内径均为12~20mm,与窄面足辊面侧的框架3连接段,采用螺纹拧入或焊接形式与窄面足辊面侧的框架3内的两条通水通道1固定相连接。各喷淋管13从窄面足辊面侧的框架3出来后,根据所生产的铸坯厚度,以第一喷嘴11和第二喷嘴12的连接端的轴向延长线与铸坯窄面角部至窄面中心方向0~20mm区域相交为原则,设计第一喷嘴11和第二喷嘴12的喷淋管13向铸坯内弧与外弧窄面角部侧弯曲呈一定角度,保证弯曲后的第一喷嘴11和第二喷嘴12的连接端的轴向延长线与铸坯窄面角部至窄面中心方向0~20mm区域相交。第一喷嘴11和第二喷嘴12分别对应的喷淋管13的长度确定原则为保证弯曲后的喷淋管13连接喷嘴后,第一喷嘴11和第二喷嘴12的末端均与铸坯窄面间的垂直距离为40~100mm。与第一喷嘴11和第二喷嘴12的连接端所对应的喷淋管13的螺纹结构分别根据第一喷嘴11和第二喷嘴12的螺纹结构设计。
[0111]
所述针对铸坯内弧与外弧窄面角部强喷淋结构的第一喷嘴11和第二喷嘴12为纯水冷却的矩形或圆锥形喷嘴。若为圆锥形喷嘴,其喷射角度为45~90
°
。若为矩形喷嘴,其沿拉坯以及与其垂直方向的喷射角度均选为45~90
°
,根据铸坯厚度、喷淋管13弯曲角度、喷嘴末端距铸坯窄面角部的距离,保证由喷嘴喷射出的冷却水在铸坯内弧与外弧窄面角部至其中心方向的作用宽度为30~60mm。
[0112]
关于一种微合金钢板坯角部裂纹控制的冷却系统的具体限定可以参见上文中对于一种微合金钢板坯角部裂纹控制的冷却方法的限定,在此不再赘述。上述一种微合金钢板坯角部裂纹控制的冷却系统中的各个模块部分通过软件、硬件及其组合来实现。上述各模块可以硬件形式内嵌于或独立于工控机设备中的处理器中,也可以以软件形式存储于工控机设备中的存储器中,以便于处理器调用执行以上各个模块对应的操作。
[0113]
在一个实施例中,提供了一种工控机设备,该工控机设备可以是服务端,其内部结构图可以如图11所示。该工控机设备包括通过系统总线连接的处理器、存储器、网络接口和数据库。其中,该工控机设备的处理器用于提供计算和控制能力。该工控机设备的存储器包括非易失性和/或易失性存储介质、内存储器。该非易失性存储介质存储有操作系统、计算机程序和数据库。该内存储器为非易失性存储介质中的操作系统和计算机程序的运行提供
环境。该工控机设备的网络接口用于与外部的客户端通过网络连接通信。该计算机程序被处理器执行时以实现一种微合金钢板坯角部裂纹控制的冷却方法服务端侧的功能或步骤。
[0114]
在一个实施例中,提供了一种工控机设备,该工控机设备可以是客户端,其内部结构图可以如图12所示。该工控机设备包括通过系统总线连接的处理器、存储器、网络接口、显示屏和输入装置。其中,该工控机设备的处理器用于提供计算和控制能力。该工控机设备的存储器包括非易失性存储介质、内存储器。该非易失性存储介质存储有操作系统和计算机程序。该内存储器为非易失性存储介质中的操作系统和计算机程序的运行提供环境。该计算机设备的网络接口用于与外部服务器通过网络连接通信。该计算机程序被处理器执行时以实现一种基于点云的矿区灰尘滤除方法客户端侧的功能或步骤。
[0115]
在一个实施例中,提供了一种工控机设备,包括存储器、处理器及存储在存储器上并可在处理器上运行的计算机程序,处理器执行计算机程序时实现以下步骤:确定所连铸生产的微合金钢板坯角部皮下0~10mm范围内的组织在窄面足辊强冷区内的平均冷却速度、冷却最低温度;确定所连铸生产的微合金钢板坯角部皮下0~10mm范围内的组织在宽面3区和宽面4区的平均回温速度、以及在宽面4区末的回温温度;根据所述平均冷却速度、冷却最低温度、宽面3区和宽面4区的平均回温速度、以及宽面4区末的回温温度,确定板坯窄面足辊冷却装置和宽面1~4区的冷却水量;通过所确定的所述板坯窄面足辊冷却装置和所述宽面1~4区的冷却水量,对位于二冷1~4区内的微合金钢板坯进行冷却。
[0116]
在一个实施例中,提供了另一种工控机可读存储介质,其上存储有计算机程序,计算机程序被处理器执行时实现以下步骤:确定所连铸生产的微合金钢板坯角部皮下0~10mm范围内的组织在窄面足辊强冷区内的平均冷却速度、冷却最低温度;确定所连铸生产的微合金钢板坯角部皮下0~10mm范围内的组织在宽面3区和宽面4区的平均回温速度、以及在宽面4区末的回温温度;根据所述平均冷却速度、冷却最低温度、宽面3区和宽面4区的平均回温速度、以及宽面4区末的回温温度,确定板坯窄面足辊冷却装置和宽面1~4区的冷却水量;通过所确定的所述板坯窄面足辊冷却装置和所述宽面1~4区的冷却水量,对位于二冷1~4区内的微合金钢板坯进行冷却。
[0117]
所属领域的技术人员可以清楚地了解到,为了描述的方便和简洁,仅以上述各功能单元、模块的划分进行举例说明,实际应用中,可以根据需要而将上述功能分配由不同的功能单元、模块完成,即将所述装置的内部结构划分成不同的功能单元或模块,以完成以上描述的全部或者部分功能。
[0118]
最后应说明的是:以上实施例仅用以说明本发明的技术方案,而非对其限制;尽管参照前述实施例对本发明进行了详细的说明,本领域的普通技术人员应当理解:其依然可以对前述实施例所记载的技术方案进行修改,或者对其中部分或者全部技术特征进行等同替换;而这些修改或者替换,并不使相应技术方案的本质脱离本发明权利要求所限定的范围。