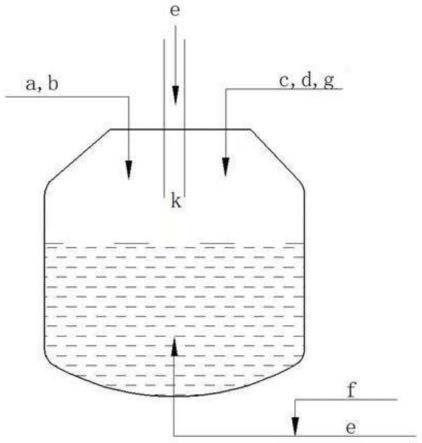
1.本发明属于合金冶炼领域,具体涉及一种由高碳锰铁吹炼中低碳锰铁的方法。
背景技术:2.中、低碳锰铁是炼钢的重要原料,目前主要采用电硅热法生产,使用的原料为锰矿、锰硅合金、石灰,使用的热源主要来自于电能,生产成本比较高,虽然工艺稳定、成熟,但发展潜力较小。
3.目前许多国家都对高碳锰铁吹炼中低碳锰铁工艺进行了大量的研究,其中转炉法生产合金的工艺以其成本低等优点尤为引人注目。美国专利公开文本us5047081a公开一种熔融cr金属的脱碳方法,欧洲专利公开文本ep446860b1公开一种在备有顶、底吹的转炉中熔化原料金属和合金。但转炉吹氧法生产中、低碳锰铁,普遍存在以下问题:1、挥发现象,因为锰的熔点(1246℃)和沸点(2120℃)都很低,在吹氧脱碳过程中,温度达到1600℃以上,致使锰挥发严重,从而挥发现象严重的影响锰的回收率;2、喷溅现象,由于在吹氧脱碳逐渐进行的过程中,随着熔池温度的升高,会有co气体的产生,而产生的气体会促进溶液从炉口喷出现象的产生,从而会造成熔体和设备等的严重损失,继而影响操作和锰的回收率;3、炉衬腐蚀现象,由于在吹氧脱碳过程中,碳素锰铁水中的硅首先被氧化,形成sio2熔体,从而会浸蚀炉墙,造成炉体寿命短,继而影响生产成本。
技术实现要素:4.本发明为克服上述转炉生产中低碳锰铁工艺所带来的挥发、喷溅及腐蚀现象,提供一种操作简单、锰回收率高,能减少炉衬腐蚀,节省能源的高炉高碳锰铁精铸直接生产中、低碳锰铁的方法。
5.为了达到上述目的,本发明是通过如下技术方案实现的:
6.一种由高碳锰铁吹炼中低碳锰铁的方法,包括以下步骤:
7.(1)原料准备,原料为75~82重量份的高碳锰铁铁水、7~12重量份的造渣剂、0~5重量份的冷却剂以及5~12重量份的硅锰合金。
8.(2)吹氧脱碳,将熔融的高碳锰铁铁水按步骤(1)的重量份倒入到脱碳容器内,倒入温度为1320-1500℃,同时从脱碳容器顶部的顶吹氧枪和底部的喷气管分别向脱碳容器内吹入氧气进行脱碳反应,供氧强度为1~2nm3/min
·
t;当吹炼过程中脱碳容器内熔池温度到达1530℃-1700℃时,按照步骤(1)的重量份比例向炉内加入造渣剂和冷却剂,使炉渣的二元碱度为1.2-1.5;当碳在熔体中的质量百分比小于1.8wt%时,脱碳结束,停止供氧。
9.(3)搅拌还原:按照步骤(1)的重量份比例向脱碳容器内加入硅锰合金,同时从脱碳容器底部的喷气管吹入情性气体进行搅拌,吹入强度为0.1-0.3nm3/min
·
t,结束后出炉得到液态的中低碳锰铁。
10.(4)制粒或浇铸:将步骤(3)出炉后液态的中低碳锰铁作为原料,进行制粒或模铸得到中低碳锰铁成品(即采用现有的铁水粒化法和浇铸的模铸法进行制粒或模铸)。
11.其中熔融的所述高碳锰铁铁水的成分按照重量百分比计为:mn:60.0~82.0wt%,si:1.0~2.0wt%,c:2.0~8.0wt%,p:≤0.30wt%,s:≤0.03wt%,余量为铁和不可避免的杂质。
12.所述脱碳容器包括炉身和炉盖,在脱碳容器的顶部设置有一个或多个加料口,所述加料口用于向脱碳容器内加入固体或液体原料,在脱碳容器的顶部中央贯穿竖直设置有顶吹氧枪,所述顶吹氧枪的喉口的直径为10-20mm,在脱碳容器底部的侧壁或底壁上设置有喷气管(最优选设置在侧壁上),所述喷气管的直径为5-8mm,在喷气管的内部设置有气体调节阀。所述气体调节阀用于调节气体流速和喷入气体的种类。
13.所述脱碳容器以aod设备进行改造而成,包括炉体、托圈、倾动机构、气体混合调制与吹气部件、测温取样部件,炉体包括炉身和炉盖,进料从底部排入,吹炼结束后,通过倾动机构将炉体倾翻,从倾翻的炉体顶部排出,通过调整顶吹氧枪的喉口的直径以及喷气管的直径等结构,使其能够顶部喷吹氧气,底部侧部喷吹氧气和惰性气体。
14.作为优选,得到所述中低碳锰铁的成分按重量百分比计为:mn:60.0~85.0wt%,si:≤2.5wt%,c:1.0~2.9wt%,p:≤0.40wt%,s:≤0.03wt%,余量为铁和不可避免的杂质。
15.作为优选,原料中的所述高碳锰铁铁水的制备方法为:将45~55重量份的锰烧结矿、25~35重量份的锰块矿、12~15重量份的焦炭以及10~12重量份的熔剂加入到高炉中,设定高炉的风温为800~1100℃,高炉出铁周期为120~150min,排出的铁水即为熔融的所述高碳锰铁铁水。
16.作为优选,所述的熔剂为石灰、或石灰和萤石的混合料;所述石灰中cao≥90wt%,粒度为10~50mm;萤石中caf2≥85wt%,粒度为10~40mm。
17.作为优选,步骤(1)中所述冷却剂为碳素锰铁和/或中碳锰铁,所述碳素锰铁的成分为:mn:65.0~72.0wt%,c≤7.0wt%,si≤4.5wt%,p≤0.4wt%,s≤0.03wt%,余量为fe和不可避免的杂质;所述中碳锰铁的成分为:mn:75.0~82.0wt%,c≤2.0wt%,si≤2.5wt%,p≤0.4wt%,s≤0.03wt%,余量为fe和不可避免的杂质。
18.作为优选,步骤(1)中所述硅锰合金的成分为:mn:60.0~67.0wt%,c:1.2wt%,si:20.0~25.0wt%,p≤0.25wt%,s≤0.04wt%,其余为fe和杂质。
19.作为优选,步骤(2)中所述的造渣剂包括白云石、石灰和氧化铝中的一种或几种的任意组合,其中白云石中cao≥30wt%,sio2≤3.0wt%,石灰中cao≥80wt%,氧化铝中al2o3≥97wt%。
20.作为优选,步骤(2)中,吹炼过程中吹入氧气进行脱碳反应的时间是每吹炼25吨高碳锰铁铁水用时60~90min。
21.作为优选,步骤(3)中所述的情性气体为氮气、氩气或二氧化碳中的一种或多种的混合气体。
22.本发明相对于现有技术所产生的有益效果为:
23.本发明改变了传统的电硅热法、转炉法,采用新型的脱碳容器对液态的高炉高碳锰铁铁水进行吹氧脱碳,通过对氧枪喉口和底枪(喷气管)的直径等参数进行限定,使得其能够高效满足本发明吹炼的要求;通过对吹氧量、熔池温度、炉渣碱度的调控,使得在避免了挥发、喷溅等现象的情况下而得到符合中低碳要求的锰铁,锰的回收率达到92%以上,在
不增加成本的基础上,提高工业生产的稳定性。其中对吹氧量的调控即供氧强度的设置,供氧强度过高,熔液喷溅严重,导致锰损失严重,且氧气利用率降低;供氧强度过低,熔池温度偏低,炉内脱碳反应不彻底;其中熔池温度中,温度过高,锰挥发损失严重;温度过低,转炉冶炼容易出现“冻炉”现象;对于炉渣碱度而言,炉渣碱度过低:渣较稀,炉衬侵蚀严重;炉渣碱度过高:渣较稠,流动性较差,导致锰回收率偏低。
24.本发明通过对各个步骤进行具体设置以及对各步骤中的参数进行具体设置,使得整体流程操作简单、原料要求范围宽,生产周期短的技术效果;本发明为保护炉衬,使炉渣成为碱性渣和保证炉渣的流动性,防止喷溅损失。通过在特定的时间内进行氧的喷吹以及惰性气体的合理喷吹,实现以氧代电,节省了能源,适合中、低碳锰铁的大规模连续生产。
附图说明
25.图1是本发明脱碳容器的结构和加料示意图。
26.图中,a为碳素锰铁;b为石灰;c为白云石;d为还原剂锰硅合金;e为氧气;f为惰性气体(氮气、氩气或二氧化碳);g为冷却剂(锰矿及中碳锰铁);k为氧枪喉口。
具体实施方式
27.本说明书中公开的任一特征,除非特别叙述,均可被其他等效或具有类似目的的替代特征加以替换。除非特别叙述,每个特征只是一系列等效或者类似特征中的一个例子而已。所述仅仅是为了帮助理解本发明,不应该视为对本发明的具体限制。
28.下面以附图和实施例对本发明作进一步详细的说明。
29.实施例1
30.将液态高炉高碳锰铁铁水25t,其成分(按重量百分比计)为:mn:74.5wt%,si:0.2wt%、p:0.19wt%、c:6.7wt%、s:0.004wt%,装入到图1所示的脱碳容器内,向炉内顶底复吹氧,供氧强度2nm3/min
·
t,图1中所示的脱碳容器为加料示意图,底部的喷吹并不是从底部中央喷吹,而是从底部的侧壁上喷吹,即底部的喷气管设置在脱碳容器底部的侧壁上,吹炼过程脱碳温度控制在1530℃;吹炼时间70分钟,为保护炉衬,使炉渣成为碱性渣和保证炉渣的流动性,防止喷溅损失,吹氧的过程中,向炉内加入造渣剂:2500kg石灰;为控制熔池温度,防止锰的挥发,向炉内加入冷却剂:500kg中碳锰铁,脱碳结束后,底枪切换为情性气体n2进行搅拌,同时加入3000kg硅锰合金,还原渣中的氧化锰。反应完毕出炉,出炉温度1500℃,得到中碳锰铁25.0t,其成分为:mn:75.5wt%、si:0.5wt%、p:0.2wt%、c:1.8wt%、s:0.006wt%,炉渣碱度r=1.24。
31.实施例2
32.将液态碳素锰铁25t,其成分(按重量百分比计)为:mn:74.6wt%、si:0.5wt%、p:0.19wt%、c:6.7wt%、s:0.004wt%,装入到图1所示的脱碳容器内,向炉内吹氧,供氧强度1nm3/min
·
t,吹炼时间90分钟,同时加入1000kg锰矿,2250kg石灰,脱碳结束后,底枪切换为惰性气体ar和co2进行搅拌,后加入3250kg硅锰合金,还原渣中的氧化锰,反应完毕出炉,出炉温度1570℃,得到低碳锰铁24.9t,其成分为:mn:75.5wt%、si:0.5wt%、p:0.2wt%、c:0.60wt%、s:0.006wt%,炉渣碱度r=1.2。