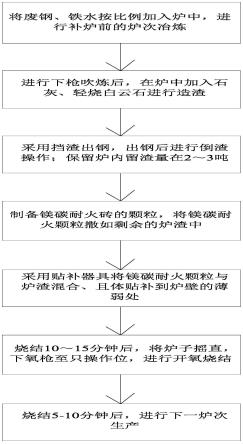
1.本发明属于钢铁冶金领域,涉及一种新型补炉方法,更具体地,涉及一种快速高效的补炉方法。
背景技术:2.现有技术中,顶底复吹转炉长期担负着重点品种的生产任务,低碳、低磷高氧化性是品种的冶炼的特点,但是长期的品种冶炼,给炉况维护带来的巨大的压力,钢水中的氧含量高,炉壁、炉底耐材侵蚀严重,采用补炉料补炉耐侵蚀性不足,冶炼30-50炉后补炉效果会荡然无存,炉况很难保证长期的生产要求。因此如何解决上述问题,就成为现下需要解决的问题了。
技术实现要素:3.发明目的:本发明的目的是提供了一种快速高效的补炉方法,通过将转炉耐火砖同等的材料,进行粒化处理,用与炉渣混合后专门针对炉况薄弱处进行贴补,达到快速高效的补炉的目的。
4.技术方案:本发明所述的一种新型补炉方法,其具体操作步骤如下:
5.(1)、将废钢、铁水按比例加入炉中,进行补炉前的炉次冶炼;
6.(2)、进行下枪吹炼后,在炉中加入石灰、轻烧白云石进行造渣;
7.(3)、采用挡渣出钢,出钢后进行倒渣操作;保留炉内留渣量在2~3吨;
8.(4)、制备镁碳耐火砖的颗粒,将镁碳耐火颗粒撒如剩余的炉渣中;
9.(5)、采用贴补器具将镁碳耐火颗粒与炉渣混合、且体贴补到炉壁的薄弱处,其中,如进行补炉底,则通过前后摇炉,均匀铺至炉底处;
10.(6)、烧结10~15分钟后,将炉子摇直,下氧枪至只操作位,进行开氧烧结;
11.(7)、烧结5-10分钟后,进行下一炉次生产。
12.进一步的,在步骤(1)中,所述废钢与铁水的比例是:1:4.5-5.0;
13.所述炉次冶炼终点出钢的温度为1660~1700度,出钢的碳含量为0.035~0.065%,冶炼终点的氧含量为700~1200ppm。
14.进一步的,在步骤(2)中,所述石灰、轻烧白云石加入比例为2.3~2.6、且为一次性加入;
15.所述进行造渣的炉渣中mgo含量在11%~14%,炉渣碱度控制在3.0~4.0之间。
16.进一步的,在步骤(3)中,所述倒渣操作中倒渣的角度是140~155度。
17.进一步的,在步骤(4)中,所述制备的镁碳耐火砖的颗粒大小为50~150mm的颗粒。
18.进一步的,在步骤(6)中,所述开氧烧结的流量是300~500m3/h。
19.有益效果:本发明与现有技术相比,本发明的特点:1、采用了与炉壁砖一致的材料进行补炉作业,补炉后使用炉次增加,并且炉膛形状更加规则,有利于补炉后冶炼操作;2、补炉时间由之前的40~50分钟缩短的20~30分钟,大大缩短了冶炼周期,生产效率得到了
大幅度的提高;3、操作简单使用,并且适用性强。
附图说明
20.图1是本发明的结构流程图。
具体实施方式
21.下面结合具体实施方式对本发明作进一步描述,并非对本其保护范围的限制:
22.本发明所述的一种新型补炉方法,具体操作步骤:
23.1、将废钢、铁水按一定的比例加入炉中,进行补炉前的炉次冶炼;
24.2、下枪吹炼后,一次性加入石灰、轻烧白云石进行造渣,石灰、轻烧白云石加入比例为2.3~2.6;
25.3、冶炼终点出钢温度为1660~1700度,出钢碳含量为0.035~0.065%,冶炼终点氧含量为700~1200ppm;
26.4、炉渣检测保证炉渣中mgo含量在11%~14%,炉渣碱度控制在3.0~4.0之间;
27.5、采用挡渣出钢,出钢干净,出钢后进行倒渣操作,倒渣角度140~155度,保证炉内留渣量为2~3吨;
28.6、镁碳耐火砖的颗粒制作为50~150mm颗粒,将镁碳耐火颗粒撒如剩余的炉渣中;
29.7、采用专用的贴补器具将镁碳耐火颗粒与炉渣混合体贴补到炉壁薄弱处,如果进行补炉底,可以直接通过前后摇炉,均匀的铺到炉底处;
30.8、烧结10~15分钟后,将炉子摇直,下氧枪至只操作位,开氧烧结,开氧烧结流量300~500m3/h;
31.9、烧结5-10分钟后进行下一炉次生产。
32.根据现有情况结合实际生产需求,本发明了采用低密度的镁碳耐火砖的贴补方法,是一种快速高效的补炉方法;针对转炉炉役后期炉壁与炉底侵蚀严重的情况,镁碳耐火砖与炉壁砖具有高度的一致性,通过控制冶炼终点炉渣中mgo含量及炉渣碱度,在高温条件下,将事先制作好的镁碳耐火砖贴补到炉况薄弱位置,在高温的条件下,耐火砖的中的沥青由炭化到石墨化,形成了具有碳网格作用的碳化骨架作用,将氧化镁颗粒紧密牢固地连接在一起,在高温烧结条件下,与炉壁的镁碳转进行了良好的贴补作用到了快速补炉的效果,节约了生产时间,提高了转炉作业率;补炉时间由之前的40~50分钟缩短的20~30分钟,补炉后使用炉次增加到80~100炉次,有效的提高了生产效率。
33.实施例1
34.本发明所述的一种新型的补炉方法,具体操作步骤如下:
35.1、将废钢、铁水按一定的比例加入炉中,进行补炉前的炉次冶炼;
36.2、下枪吹炼后,一次性加入石灰、轻烧白云石进行造渣,石灰、轻烧白云石加入比例为2.4;
37.3、冶炼终点出钢温度为1691度,出钢碳含量为0.056%,冶炼终点氧含量为910ppm;
38.4、炉渣检测保证炉渣中mgo含量在134%,炉渣碱度控制在3.6之间;
39.5、采用挡渣出钢,出钢干净,出钢后进行倒渣操作,倒渣角度151度,炉内留渣量为
2吨;
40.6、镁碳耐火砖的颗粒制作为80mm颗粒,将镁碳耐火颗粒撒如剩余的炉渣中;
41.7、采用专用的贴补器具将镁碳耐火颗粒与炉渣混合体贴补到炉壁薄弱处,如果进行补炉底,可以直接通过前后摇炉,均匀的铺到炉底处;
42.8、烧结13分钟后,将炉子摇直,下氧枪至只操作位,开氧烧结,开氧烧结流量330m3/h;
43.9、烧结8分钟后进行下一炉次生产。
44.实施例2
45.本发明所述的一种快速高效的补炉方法,具体操作步骤如下:
46.1、将废钢、铁水按一定的比例加入炉中,进行补炉前的炉次冶炼;
47.2、下枪吹炼后,一次性加入石灰、轻烧白云石进行造渣,石灰、轻烧白云石加入比例为2.4;
48.3、冶炼终点出钢温度为1686度,出钢碳含量为0.039%,冶炼终点氧含量为1080ppm;
49.4、炉渣检测保证炉渣中mgo含量在13%,炉渣碱度控制在3.6之间;
50.5、采用挡渣出钢,出钢干净,出钢后进行倒渣操作,倒渣角度147度,保证炉内留渣量为3吨;
51.6、镁碳耐火砖的颗粒制作为100mm颗粒,将镁碳耐火颗粒撒如剩余的炉渣中;
52.7、采用专用的贴补器具将镁碳耐火颗粒与炉渣混合体贴补到炉壁薄弱处,如果进行补炉底,可以直接通过前后摇炉,均匀的铺到炉底处;
53.8、烧结12分钟后,将炉子摇直,下氧枪至只操作位,开氧烧结,开氧烧结流量430m3/h;
54.9、烧结7分钟后进行下一炉次生产。
55.以上仅是本发明的优选实施方式,本发明的保护范围并不仅局限于上述实施例,凡属于本发明思路下的技术方案均属于本发明的保护范围。应当指出,对于本技术领域的普通技术人员来说,在不脱离本发明原理前提下的若干改进和润饰,应视为本发明的保护范围。