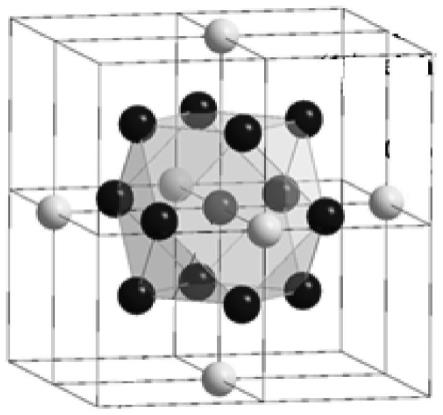
1.本发明涉及合金技术领域,具体涉及一种耐强酸冲蚀的磷酸反应槽搅拌桨叶片修复用高熵合金涂层及其制备方法。
背景技术:2.我国是磷化工生产大国,磷化工产品产量丰富,磷化工企业生产磷酸过程中,搅拌桨叶片与磷矿石强烈碰撞,容易发生冲刷腐蚀。904l不锈钢搅拌叶片广泛用于制备磷化工产品,但其硬度低,在强酸环境下耐矿石颗粒冲蚀能力不够,每年所需修复费用过亿,迫切需要找到合适的耐冲刷腐蚀的表面涂覆合金。
3.高熵合金于2004年由中国台湾地区学者叶均蔚教授首先提出,它的出现为开拓新材料提供了新思路,高熵合金一般由5种或5种以上主要元素按等原子比或近等原子比配制后,经过熔炼、烧结、激光熔覆等方法获得的具有金属特性的材料,每种元素的原子分数介于5%-35%之间。高熵合金具有众多优于传统 fe、ti、ni基合金的性质,如组织结构上呈现简单的固溶体结构以及优异的高温组织稳定性,性能上表现出高强度和硬度、优良的耐蚀及耐磨性等,在高速切削用刀具、各类工模具、涡轮机叶片等领域具有广阔的应用前景。高熵合金因其独特的成分及组织结构而具有优异的性能,与传统合金设计理念不同,高熵合金通过合理地成分设计,加上适当的制备手段,达到兼具耐磨性和耐蚀性,有希望作为替代材料。但是高熵合金成分复杂、组织多变,需要在理论指导下实施精确的成分设计。
4.近年来大连理工大学董闯教授提出利用团簇加连接原子模型来设计合金成分。该模型是将理想结构单元分为团簇和连接原子两个部分。其中,团簇是由中心原子及其最近邻壳层原子组成,而连接原子则是处于中心原子的次近邻位置。溶剂与溶质原子在模型中的占位由各元素之间的混合焓δhmix决定。通常,溶剂原子占据团簇的壳层位置,溶质与溶剂原子之间δhmix越负,则溶质原子占据团簇中心位置。反之,溶质原子占据连接原子位置。如fcc 结构固溶体的团簇加连接原子模型中,中心原子周围最近邻原子的配位数是 12,连接原子个数一般为1-6,因此可表示为[a-b12]c1-6,其中a为中心原子,b为壳层原子,c为连接原子。
[0005]
该模型的特点是从短程序的角度解释了理想固溶体模型,准确描述合金固溶体的理想结构单元以及溶剂与溶质原子的点阵占位情况,进而对固溶体成分进行优化,可有效取代传统“炒菜式”的合金成分设计,大大节约时间和人力成本。那么如何在904l不锈钢表面制备耐强酸冲刷腐蚀的高熵合金涂层,为我国磷化工产业提供耐强酸冲刷腐蚀的材料配方及表面涂层制备技术,成为我们需要解决的问题。
技术实现要素:[0006]
针对现有技术中所存在的不足,本发明的目的在于提供一种耐强酸冲蚀的磷酸反应槽搅拌桨叶片修复用高熵合金涂层,第二目的在于提供该种涂层的制备方法。
[0007]
为实现上述第一目的,本发明采用了如下的技术方案:一种耐强酸冲蚀的磷酸反应槽搅拌桨叶片修复用高熵合金涂层,其特征在于:基于904l不锈钢,牌号00cr
20
ni
25
mo
4.5
cu,采用fe、co、ni作为溶剂原子,取代壳层原子位置的fe、ni,由此构建团簇模型式为[cr-fe4co4ni4]cr
2.6
mo
0.4
,在连接原子位置添加al得到有序相共格高熵合金式为:[cr-fe4co4ni4]cr
2.6-x
al
x
mo
0.4
, x=0-1。
[0008]
上述方案中:x为0.6。
[0009]
本发明的第二目的是这样实现的:所述耐强酸冲蚀的磷酸反应槽搅拌桨叶片修复用高熵合金涂层的制备方法,其特征在于,按照如下步骤制备:
[0010]
1)称取高纯度fe、co、ni、cr、al、mo金属粉末;
[0011]
2)将称量好的粉末置于不锈钢球磨罐中进行球磨,使粉末混合均匀,球磨后的粉末过筛,干燥;
[0012]
3)选用904不锈钢板作为基材,用砂轮机清除基材熔覆面的氧化皮,利用酒精清洗表面油污,吹干;
[0013]
4)利用不锈钢模具在基材表面预置一层粉末,并用不锈钢片压实,氩气保护,采用激光熔覆方法制备涂层。
[0014]
上述方案中:fe、co、ni、cr、al、mo金属粉末的纯度均大于99.6%,颗粒度大于200目。
[0015]
上述方案中:球磨参数为:球料比:5:1,球磨转速200-250rmp/min,球磨时间2h,球磨完后过120目筛。
[0016]
上述方案中:基材表面预置粉末的厚度为1-1.5mm。
[0017]
上述方案中:保护气氛ar气的纯度为99.995%,气流密度为25l
·
min-1
,熔覆的工艺参数为:激光功率p=2500w,扫描速率v=5mm/s,矩形光斑尺寸20mm*2mm。
[0018]
由于宽带激光熔覆具有超快速加热和超快速冷却的特点,如果涂层与基材的适配性差,将会导致熔覆过程中裂纹产生。我们在解析904l不锈钢的基础上,设计出与之成分性质相近的高熵合金涂层成分,使涂层与基材的热物性参数接近,可以降低涂层开裂敏感性。
[0019]
通过溶入足够cr含量以保证耐蚀性的前提下,并在连接原子位置添加 al原子进一步构建有序相共格析出的[cr-fe4co4ni4]cr
2.6-x
al
x
mo
0.4
高熵合金,提升耐磨性,具有明显的强度增益效果,且不降低塑性,本发明在提高耐蚀性能的前提下,提高合金硬度和韧性,适用于强酸腐蚀和矿石粉强烈冲刷环境条件下使用,为我国磷化工产业提供耐强酸冲刷腐蚀的材料配方及表面涂层制备技术。
附图说明
[0020]
图1为fcc型固溶体团簇加连接原子模型示意图。
[0021]
图2为[cr-fe4co4ni4]cr
2.6-x
al
x
mo
0.4
高熵合金涂层xrd图谱。
[0022]
图3为[cr-fe4co4ni4]cr
2.6-x
al
x
mo
0.4
高熵合金涂层显微组织图(a)fecocrni涂层(b)al0涂层(c)al
0.2
涂层(d)al
0.4
涂层(e)al
0.6
涂层(f)al
0.8
涂层(g)al
1.0
涂层。
[0023]
图4为[cr-fe4co4ni4]cr
2.6-x
al
x
mo
0.4
高熵合金涂层透射组织(a)al
0.6
涂层明场相、析出相eds和衍射斑点(b)al
1.0
涂层明场相、析出相eds和衍射斑点(c) al
1.0
涂层高分辨图像和傅立叶转变斑点。
[0024]
图5为[cr-fe4co4ni4]cr
2.6-x
al
x
mo
0.4
高熵合金涂层硬度分布曲线图。
[0025]
图6为[cr-fe4co4ni4]cr
2.6-x
al
x
mo
0.4
高熵合金涂层摩擦磨损质量损失图。
[0026]
图7为[cr-fe4co4ni4]cr
2.6-x
al
x
mo
0.4
高熵合金涂层摩擦磨损曲线图。
[0027]
图8为[cr-fe4co4ni4]cr
2.6-x
al
x
mo
0.4
高熵合金涂层磨痕形貌图。
[0028]
图9为[cr-fe4co4ni4]cr
2.6-x
al
x
mo
0.4
高熵合金涂层在0.5mol/l h2so4溶液中的电化学曲线图(a)极化曲线图(b)阻抗图(c)模值图(d)相角图。
[0029]
图10为[cr-fe4co4ni4]cr
2.6-x
al
x
mo0.4高熵合金涂层冲蚀腐蚀质量曲线图(冲刷腐蚀条件:50%硫酸溶液,30%不规则玻璃颗粒,实验温度80
±
2℃)。
[0030]
图11为cr-fe4co4ni4]cr
2.6-x
al
x
mo0.4高熵合金涂层冲刷腐蚀形貌(a)904基材(b)fecocrni涂层(c)al0涂层(d)al
0.2
涂层(e)al
0.4
涂层(f)al
0.6
涂层(g) al
0.8
涂层(h)al
1.0
涂层。
[0031]
图12为[cr-fe4co4ni4]cr
2.6-x
al
x
mo
0.4
高熵合金涂层冲蚀腐蚀前后的xrd图谱。
具体实施方式
[0032]
下面通过具体实施方式对本发明作进一步详细的说明:
[0033]
实施例1
[0034] (1)成分设计:根据904l不锈钢牌号(00cr
20
ni
25
mo
4.5
cu),化为相应的原子比:fe-24.2ni-22.9cr-2.6mo-1.5mn-1.3cu,根据团簇加连接原子模型,其团簇式可描述为[cr-fe
7.6
ni
3.9
mn
0.3
cu
0.2
]cr
2.6
mo
0.4
。在不考虑mn和cu的情况下,引入“平均原子”概念,将原子性质相近、相互作用力较弱的第
ⅷ
族fe、 co、ni看作平均原子m,并选用m为溶剂原子,取代壳层原子位置的fe和 ni,由此我们构建的团簇模型式为[cr-fe4co4ni4]cr
2.6
mo
0.4
(co
25
cr
22.5
fe
25
ni
25
mo
2.5
,at.%)。在此基础上,我们拟在连接原子位置添加 al原子进一步构建有序相共格析出的[cr-fe4co4ni4]cr
2.6-x
al
x
mo
0.4
高熵合金体系,以期提高合金硬度,其中x=0、0.2、0.4、0.6、0.8、1.0at.%中的一个,等原子比的fecocrni合金作为对照组,具体成分列于表一。
[0035]
表一 高熵合金化学成分
[0036]
[0037] (b)粉末配制:选用高纯度fe、co、ni、cr、al、mo(纯度皆在99.6%以上、颗粒度200目以上)金属粉末,其中fe、co、ni、cr、al、mo的原子比为fe:co:ni:cr:al:mo=4:4:4:3.6-x:x:0.4,其中x=0、0.2、0.4、 0.6、0.8、1.0、at.%,后面分别用al0、al
0.2
、al
0.4
、al
0.6
、al
0.8
和al1表示。配制原子比fe:co:ni:cr=1:1:1:1作为参照组,采用精度为0.1mg的 al204型电子天平按照表一进行称量。
[0038] (c)粉末球磨:将称量好的粉末置于不锈钢球磨罐中进行球磨,使粉末混合均匀,球磨参数为:球料比:5:1,球磨转速200-250rmp/min,球磨时间2h。球磨后的粉末经过120目不锈钢分样筛过筛后,将样品放置于真空干燥箱中保存。
[0039] (d)基材选择:选用尺寸为尺寸50mm(长)*30mm(宽)*10mm(厚)的904 不锈钢板作为基材,基材成分列于表二。先用砂轮机清除基材熔覆面的氧化皮,利用酒精清洗表面油污,并用吹风机吹干,干燥保存。
[0040]
表二904l不锈钢化学成分(wt%)
[0041][0042] (e)激光熔覆涂层制备:采用预置粉末法,利用不锈钢模具在基材表面预置一层1.5mm厚的粉末,并用不锈钢片压实。保护气氛ar气的纯度为 99.995%,气流密度为25l
·
min-1。熔覆的工艺参数为:激光功率p=2500w,扫描速率v=5mm/s,矩形光斑尺寸20mm*2mm。
[0043]
表三[cr-fe4co4ni4]cr
2.6-x
al
x
mo
0.4
高熵合金涂层晶格常数(jade 6.0software统计)
[0044][0045]
图2中[cr-fe4co4ni4]cr
2.6-x
al
x
mo
0.4
高熵合金涂层xrd图谱表明所有涂层主要由单一fcc固溶体组成。从图中可以看出,随着al元素增加,(111)(200)峰的逐渐向低角度方向偏移,是由于al元素的添加,引起晶格畸变,导致涂层晶格常数增加(见表三)。al元素具有较大的原子半径 al原子进入fcc晶胞,会使晶格常数增加,导致晶格畸变效应。此外,高能密度的激光照射涂层和基材会产生热膨胀,也会导致晶格畸变。
[0046]
图3为[cr-fe4co4ni4]cr
2.6-x
al
x
mo
0.4
高熵合金涂层显微组织图(a)fecocrni涂层(b)al0涂层(c)al
0.2
涂层(d)al
0.4
涂层(e)al
0.6
涂层(f)al
0.8
涂层(g)al
1.0
涂层。从图中可以看出,随着al元素添加,涂层组织逐渐变细。
[0047]
图4为[cr-fe4co4ni4]cr
2.6-x
al
x
mo
0.4
高熵合金涂层透射组织(a)al
0.6
涂层明场相、析出相eds和衍射斑点(b)al
1.0
涂层明场相、析出相eds和衍射斑点(c)al
1.0
涂层高分辨图像和傅立叶转变斑点。在图4ab中我们能看到黑色不规则形状的析出相,析出相与基材呈良好的冶金结合,结合区没有裂纹、孔洞等产生。析出相尺寸大约~200nm。图4a中选区衍射斑点表明了高熵合金具有沿[-112]晶带轴的fcc相,同时,沿[011]晶带轴的微弱的衍射斑点表明al
0.6
涂层中具有l12超点阵结构相。图4c中al
1.0
涂层高分辨图像和傅立叶转变斑点表明
析出相和基材是界面共格关系,晶胞尺寸约为0.2122nm,晶间析出相尺寸约为0.2094nm。从图4ab中析出相eds可以看出,析出相具有较高的ni、 al含量,而co、cr、,mo元素含量相对较低。l12相的一般为a3b结构, co、cr能够取代ni的位置占据a原子位置,al一般占据b原子位置,因此这里推测该涂层中的析出相为(n、co、cr)3(al)相。
[0048]
图5为[cr-fe4co4ni4]cr
2.6-x
al
x
mo
0.4
高熵合金涂层硬度分布曲线图。从图5中可以看出,当x≤0.6时涂层硬度逐渐增高,al
0.6
涂层硬度最高达297.8hv
0.2
,当x》0.6时,涂层硬度略微下降。相比于基材(~190hv
0.2
)和fecocrni涂层(~200hv
0.2
)硬度,alx涂层硬度明显提高,主要是由于固溶强化,弥散强化,细晶强化等。fcc基底中l12析出相的形成会导致固溶强化和弥散强化,有利于硬度的提高。
[0049]
图6为[cr-fe4co4ni4]cr
2.6-x
al
x
mo
0.4
高熵合金涂层摩擦磨损质量损失图。从图6可以看出,随着al元素添加,当x≤0.6涂层磨损质量逐渐减少,当x》0.6 涂层磨损质量增加。相比基材(12.5mg)和fecocrni涂层(12.2mg),al
0.6
涂层磨损质量最少(9.7mg),说明其耐磨性较好。
[0050]
图7为[cr-fe4co4ni4]cr
2.6-x
al
x
mo
0.4
高熵合金涂层摩擦磨损曲线图。从图7可以看出,磨损开始时,摩擦系数急剧增加,之后趋于稳定。当x≤0.6时涂层平均摩擦系数值逐渐降低,x》0.6时涂层平均摩擦系数值略微增加,al
0.6
涂层具有最低的平均系数(f
ave
=0.6721)。
[0051]
图8为[cr-fe4co4ni4]cr
2.6-x
al
x
mo
0.4
高熵合金涂层磨痕形貌图。从图8可以看出涂层磨损表面出现许多粘附痕迹和平行于滑动方向的犁沟,此外还有一些剥落、分层现象发生,涂层磨损机制主要是粘着磨损和磨粒磨损。图8ab 中基材和fecocrni涂层发生严重的粘着磨损和剥落,主要由于其较低的硬度不能承受摩擦副的塑性挤压。随着al元素的添加,涂层磨损形貌逐渐变得光滑,剥落现象减少,al
0-al
0.6
涂层出现不连续的塑性变形和显微犁沟,但在 al
0.8-al
1.0
涂层,涂层剥落程度加深。说明al
0-al
0.6
涂层耐磨性优于al
0.8-al
1.0
涂层。
[0052]
图9为[cr-fe4co4ni4]cr
2.6-x
al
x
mo
0.4
高熵合金涂层在0.5mol/l h2so4溶液中的电化学曲线图(a)极化曲线图(b)阻抗图(c)模值图(d)相角图。
[0053]
表四 涂层在0.5mol/l h2so4溶液中的电化拟合参数和阻抗等效电路拟合参数
[0054]
[0055][0056]
图9a中在阳极极化过程中,涂层表面表现出主动钝化的特性,电流密度快速波动,表明钝化膜可以自发形成。涂层耐蚀性通常与其化学稳定性有关,自腐蚀电位越高,自腐蚀电流密度越小,表明材料耐蚀性越好。当x≤0.6时,涂层腐蚀电位逐渐增加,之后涂层腐蚀电位下降。al
0.6
涂层自腐蚀电位最大(-0.398v)。并且al
0.6
涂层有最低的自腐蚀电流密度(0.2945ma/cm2),表明涂层中合适的al含量添加能够提高涂层耐蚀性。然而al元素添加太多,涂层耐蚀性下降,主要是由于al元素的增加促进了组织中枝晶的产生,加速了电偶腐蚀,降低耐蚀性。涂层耐点蚀性能随着al元素增加也出现了先增加后下降的趋势,al
0.6
涂层具有最好的耐点蚀能力。图9b-d为涂层相应的阻抗图,图9b中,阻抗半径越大,表明涂层耐蚀性越好,相应的趋势也发生在模值图和相角图上。al
0.6
涂层表现出最高耐蚀性。涂层中合适的al元素添加能够促进fcc和l12相生成,能够有效减少涂层腐蚀速率,提高涂层耐蚀性。
[0057]
图10为[cr-fe4co4ni4]cr
2.6-x
al
x
mo0.4高熵合金涂层冲蚀腐蚀质量曲线图(冲刷腐蚀条件:50%硫酸溶液,30%不规则玻璃颗粒,实验温度80
±
2℃)
[0058]
从图10中可以看出,涂层在强酸冲蚀条件下出现质量损失,在0-10h涂层质量损失增加迅速,10-24h涂层质量损失变化缓慢增加。在所有试样中,fecocrni和al1.0涂层质量损失多于904基材,其他涂层冲蚀质量损失均低于基材,al
0.6
涂层质量损失最少(5.0mg),表明耐冲刷腐蚀性能较好。
[0059]
图11为cr-fe4co4ni4]cr
2.6-x
al
x
mo0.4高熵合金涂层冲刷腐蚀形貌(a)904 基材(b)fecocrni涂层(c)al0涂层(d)al
0.2
涂层(e)al
0.4
涂层(f)al
0.6
涂层(g) al
0.8
涂层(h)al
1.0
涂层
[0060]
图11a中904基材在冲蚀条件下由于微切割边缘挤压唇的出现,出现了塑性变形。图b-h中alx涂层在不规则颗粒冲蚀条件下发生微切割+混合切割犁沟的冲蚀机制。图b中fecocrni涂层冲蚀表面出现严重的冲蚀刮痕和腐蚀坑。随着al元素添加,涂层冲蚀表面出现较少的冲蚀刮痕,冲蚀表面相对光滑。al
0.6
涂层表面冲蚀刮痕和腐蚀坑最少,al
0.8
,al
1.0
涂层由于硬度略微下降,冲刷腐蚀略微加强。
[0061]
图12为[cr-fe4co4ni4]cr
2.6-x
al
x
mo
0.4
高熵合金涂层冲蚀腐蚀前后的 xrd图谱。涂层在冲刷腐蚀前后试样表面的xrd图谱,可以看出,经过冲刷腐蚀实验后,涂层(111)峰减弱,而(200)峰增强。峰强度的变化说明冲蚀腐蚀过程会影响涂层显微织构。织构的变化需要借助更精密的仪器如 ebsd来分析,这里暂不讨论。总的来说,涂层在强酸冲刷腐蚀过程
中,fcc 相在冲蚀颗粒冲击下会变软。涂层显微织构会被影响。
[0062]
最后说明的是,以上实施例仅用以说明本发明的技术方案而非限制,尽管参照较佳实施例对本发明进行了详细说明,本领域的普通技术人员应当理解,可以对本发明的技术方案进行修改或者等同替换,而不脱离本发明技术方案的宗旨和范围,其均应涵盖在本发明的权利要求范围当中。