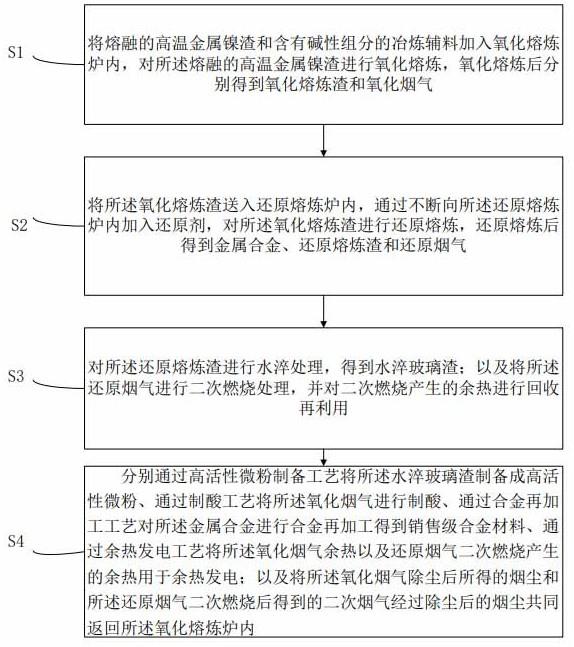
1.本发明涉及化工技术领域,更为具体地,涉及一种金属镍渣的资源化利用方法。
背景技术:2.金属镍渣(以下简称镍渣)是冶炼金属镍过程中排放的固体废渣。通常是指硫化镍矿精矿经过闪速炉熔化成镍锍后,剩余熔融尾渣再经过电加热贫化后排出的固体熔渣,通常也称为贫化镍渣或贫化电炉渣。金属镍渣中主要以feo、sio2、mgo等化学成分为主,大致为feo 30-50%,sio
2 35-45%,mgo 2-15等,矿物相也以铁橄榄石、镁铁橄榄石相为主。此外,金属镍渣中还含有少量ni、cu、co等残余有价金属,以及约1-3%的s。高温镍渣在冶炼到1400-1500℃后排出炉外,通常直接经过水淬处理,但由于水淬镍渣活性不足,且固渣密度又大,导致镍渣在建材化领域应用受限,绝大部分都是堆存在场地中。长此以往,不仅镍渣中的重金属元素会污染周边环境,而且镍渣中这些有价组分元素以及镍渣高温余热也未得到有效利用,造成资源的巨大浪费。
3.现有针对镍铁渣的处理工艺,均没有考虑熔渣余热资源的利用,而且将渣中的金属元素回收,也是需要进行二次加热,能耗较高,成本也高。熔渣经过还原后,镍渣、还原剂等原料中的s还会被还原进入金属铁中,影响金属铁品质。在产品端方面,除了考虑镍渣回收金属得到的金属铁或铁精矿外,剩余尾渣的利用没有实现综合考虑,仅直接作为建材行业的低价原材料使用,没有将其加工成高值建筑材料,导致镍渣总产值很少,工程技术经济性不佳。
技术实现要素:4.鉴于上述问题,本发明的目的是提供一种金属镍渣的资源化利用方法,以解决目前的现有镍铁渣的处理工艺,对熔渣余热资源的利用不够全面、金属元素回收,需要进行二次加热,能耗较高,成本高、s还会被还原进入金属铁中,致使金属铁的品质差、剩余尾渣的利用没有实现综合考虑,经济性差等问题。
5.本发明提供一种金属镍渣的资源化利用方法,包括如下步骤:将熔融的高温金属镍渣和含有碱性组分的冶炼辅料加入氧化熔炼炉内,对所述高温金属镍渣进行氧化熔炼,氧化熔炼后分别得到氧化熔炼渣和氧化烟气;将所述氧化熔炼渣送入还原熔炼炉内,通过不断向所述还原熔炼炉内加入还原剂,对所述氧化熔炼渣进行还原熔炼,还原熔炼后得到金属合金、还原熔炼渣和还原烟气;对所述还原熔炼渣进行水淬处理,得到水淬玻璃渣;以及将所述还原烟气进行二次燃烧处理,并对二次燃烧产生的余热进行回收再利用;分别通过高活性微粉制备工艺将所述水淬玻璃渣制备成高活性微粉、通过制酸工艺将所述氧化烟气进行制酸、通过合金再加工工艺对所述金属合金进行合金再加工得到销售级合金材料、通过余热发电工艺将所述氧化烟气余热以及还原烟气二次燃烧产生的余热用于余热发电;以及将所述氧化烟气除尘后所得的烟尘和所述还原烟气经过二次燃烧后得
到的二次烟气经过除尘后的烟尘共同返回所述氧化熔炼炉内。
6.此外,优选的方案是在对所述熔融的高温金属镍渣进行氧化熔炼的过程中,控制所述氧化熔炼炉内的熔炼渣中的碱性氧化物与酸性氧化物质量之比为0.8-1.2。
7.此外,优选的方案是在对所述熔融的高温金属镍渣进行氧化熔炼的过程中,通过向所述氧化熔炼炉内喷入第一燃料和第一助燃气体,对所述氧化熔炼炉内的熔炼渣进行加热;其中,所述第一燃料为天然气、石油气、煤粉中的任意一种;所述第一助燃气体为工业氧气和空气混合而成;其中,在所述第一助燃气体中的总氧气的浓度为 50-85 v.%;所述氧化熔炼炉内的熔池的内部及熔池的表面的氧气的浓度均为3-8%;所述熔池的内部及熔池的表面的气氛均为微氧化性气氛。
8.此外,优选的方案是,所述含有碱性组分的冶炼辅料为脱硫石膏、煅烧硫铁渣、硫铁矿、石灰石、白云石中的任意一种或按照任意比例混合的几种。
9.此外,优选的方案是,所述氧化熔炼炉为侧吹炉或底吹炉;所述氧化熔炼炉通过富氧浸没燃烧技术,保证喷入所述氧化熔炼炉内的燃料充分燃烧。
10.此外,优选的方案是,在对所述氧化熔炼渣进行还原熔炼的过程中,通过向所述还原熔炼炉的炉内喷入第二燃料和第二助燃气体,对所述还原熔炼炉内的氧化熔炼渣进行加热;其中,所述第二燃料为天然气、石油气、煤粉中的任意一种;和/或,所述第二助燃气体为工业氧气和空气混合而成;其中,在所述第二助燃气体中的总氧气的浓度为 50-85 v.%;和/或,控制所述还原熔炼炉的熔池内及液面上部空间内的气氛为还原性气氛,喷入所述还原熔炼炉内的所述第二助燃气体处于微欠氧状态。
11.此外,优选的方案是,所述还原剂为块煤、焦炭、兰炭、报废石墨电极中的任意一种或按照任意比例混合的几种;其中,所述还原剂的粒度为5-15cm;所述还原剂的加入量为所述氧化熔炼渣的质量的10-15%。
12.此外,优选的方案是,所述还原熔炼炉为侧吹炉或顶吹炉。
13.此外,优选的方案是,在所述对所述还原熔炼渣进行水淬处理,得到水淬玻璃渣的过程中,通过射流和雾化复合型喷水冷却的方式对所述还原熔炼渣进行水淬处理,在水淬处理过程中,所述冷却用水的重量为所述还原熔炼渣的重量的0.8-1.0倍,使所述还原熔炼渣迅速降至200℃以下。
14.此外,优选的方案是,所述通过制酸工艺将所述氧化烟气进行制酸包括:对所述氧化烟气进行余热回收,得到余热回收后的氧化烟气;对所述余热回收后的氧化烟气进行除尘处理,得到除尘后的氧化烟气;通过制酸工艺对所述除尘后的氧化烟气进行制酸处理;和/或,通过高活性微粉制备工艺将所述水淬玻璃渣制备成高活性微粉包括:将所述水淬玻璃渣进行干燥处理,得到干燥的水淬玻璃渣;
将所述干燥的水淬玻璃渣、激发剂、调整料、助磨剂按照预设配比混合,得到玻璃渣混料;其中,所述玻璃渣混料的各种原料质量分数比为:干燥的水淬玻璃渣:激发剂:调整料:助磨剂=100:3-14:5-20:0-1;通过粉磨设备将所述玻璃渣混料进行粉磨处理,使所述玻璃渣混料的细粉比表为400
ꢀ㎡
/kg以上,得到高活性微粉材料。
15.从上面的技术方案可知,本发明提供的金属镍渣的资源化利用方法,通过将排出的高温金属镍渣与含有碱性组分的冶炼辅料直接加入氧化熔炼炉内进行熔炼操作,在充分利用镍渣余热的前提下,实现镍渣中s的脱除和回收利用;含有碱性组分的冶炼辅料主要以含硫、多钙镁、多有价金属特点构成的物料,能够实现镍渣热态改性的同时,实现多种资源的协同化利用;通过本发明提供的方法能够更加全面的对熔渣余热资源进行利用,不仅有效利用了金属镍渣的高温,实现镍渣中s的脱除和回收利用;还利用了氧化烟气余热和还原烟气二次燃烧余热以及利用氧化烟气进行制酸。本发明较传统再加热熔化方式相比较,具有能耗低、能协同其它含硫多金属固废的资源化处理渣、金属回收率高、产品种类多、总产值高、镍渣处理效率高、资源综合利用率高、生产成本低、工程经济性好等优点。
16.为了实现上述以及相关目的,本发明的一个或多个方面包括后面将详细说明的特征。下面的说明以及附图详细说明了本发明的某些示例性方面。然而,这些方面指示的仅仅是可使用本发明的原理的各种方式中的一些方式。此外,本发明旨在包括所有这些方面以及它们的等同物。
附图说明
17.通过参考以下结合附图的说明,并且随着对本发明的更全面理解,本发明的其它目的及结果将更加明白及易于理解。在附图中:图1为根据本发明实施例的金属镍渣的资源化利用方法的流程图。
18.在所有附图中相同的标号指示相似或相应的特征或功能。
具体实施方式
19.在下面的描述中,出于说明的目的,为了提供对一个或多个实施例的全面理解,阐述了许多具体细节。然而,很明显,也可以在没有这些具体细节的情况下实现这些实施例。
20.针对前述提出的目前的现有镍铁渣的处理工艺,对熔渣余热资源的利用不够全面、金属元素回收,需要进行二次加热,能耗较高,成本高、s还会被还原进入金属铁中,致使金属铁的品质差、剩余尾渣的利用没有实现综合考虑,经济性差等问题,提出了一种金属镍渣的资源化利用方法。
21.以下将结合附图对本发明的具体实施例进行详细描述。
22.为了说明本发明提供的金属镍渣的资源化利用方法,图1示出了根据本发明实施例的金属镍渣的资源化利用方法的流程。
23.如图1结所示,本发明提供的金属镍渣的资源化利用方法,包括如下步骤:s1、将熔融的高温金属镍渣和含有碱性组分的冶炼辅料加入氧化熔炼炉内,对高温金属镍渣进行氧化熔炼,氧化熔炼后分别得到氧化熔炼渣和氧化烟气;s2、将氧化熔炼渣送入还原熔炼炉内,通过不断向还原熔炼炉内加入还原剂,对氧
化熔炼渣进行还原熔炼,还原熔炼后得到金属合金、还原熔炼渣和还原烟气;s3、对还原熔炼渣进行水淬处理,得到水淬玻璃渣;以及将还原烟气进行二次燃烧处理,并对二次燃烧产生的余热进行回收再利用;s4、分别通过高活性微粉制备工艺将水淬玻璃渣制备成高活性微粉、通过制酸工艺将氧化烟气进行制酸、通过合金再加工工艺对金属合金进行合金再加工得到销售级合金材料、通过余热发电工艺将氧化烟气余热以及还原烟气二次燃烧产生的余热用于余热发电;以及将氧化烟气除尘后所得的烟尘和还原烟气经过二次燃烧后得到的二次烟气经过除尘后的烟尘共同返回氧化熔炼炉内。
24.其中,金属合金经铸锭后可外售钢铁企业。
25.通过将排出的熔融的高温金属镍渣与含有碱性组分的冶炼辅料直接加入氧化熔炼炉内进行熔炼操作,在充分利用镍渣余热的前提下,实现镍渣中s的脱除和回收利用;含有碱性组分的冶炼辅料主要以含硫、多钙镁、多有价金属特点构成的物料,能够实现镍渣热态改性的同时,实现多种资源的协同化利用;通过本发明提供的方法能够更加全面的对熔渣余热资源进行利用,不仅有效利用了金属镍渣的高温,实现镍渣中s的脱除和回收利用;还利用了还原烟气的二次燃烧的余热以及利用氧化烟气进行制酸。本发明较传统再加热熔化方式相比较,具有能耗低、能协同其它含硫多金属固废的资源化处理渣、金属回收率高、产品种类多、总产值高、镍渣处理效率高、资源综合利用率高、生产成本低、工程经济性好等优点。
26.作为本发明的一个优选实施例,在对高温金属镍渣进行氧化熔炼的过程中,控制氧化熔炼炉内的熔炼渣中的碱性氧化物与酸性氧化物之比为0.8-1.2。
27.能够保证熔渣具有降低的熔化温度和良好的流动性,同时该范围内的熔渣也具有很高的金属还原性。
28.作为本发明的一个优选实施例,在对高温金属镍渣进行氧化熔炼的过程中,通过向氧化熔炼炉内喷入第一燃料和第一助燃气体,对氧化熔炼炉内的熔炼渣进行加热;其中,第一燃料为天然气、石油气、煤粉中的任意一种;第一助燃气体为工业氧气和空气混合而成;其中,在第一助燃气体中总的氧气浓度为 50-85 v.%;氧化熔炼炉内的熔池的内部及熔池的表面的氧气浓度均为3-8%;熔池的内部及熔池的表面的气氛均为微氧化性气氛。
29.氧化熔炼炉内依靠第一燃料和第一助燃气体喷入炉内后进行剧烈氧化放热反应,以保证炉内反应所需温度;通过调整工业氧气和空气的混合比例,控制助燃气体中的氧气的浓度在50-85 v.%,实现富氧燃烧熔炼反应。
30.保证氧化熔炼时熔池内部及表面气氛为微氧化性气氛,氧气浓度维持在3-8%为宜,能够保证金属镍渣和含硫冶炼辅料中的s能够被全部分解成二氧化硫或三氧化硫而进入烟气中,烟气中折算二氧化硫的浓度在5-18%之间,这些烟气送到化工工序后,可用来生产浓硫酸。
31.作为本发明的一个优选实施例,含有碱性组分的冶炼辅料为脱硫石膏、煅烧硫铁渣、硫铁矿、石灰石、白云石中的任意一种或按照任意比例混合的几种。既能为金属镍渣氧化熔炼提供ca、mg等碱性组分,还能同时提供富含s、fe、ni等有价元素,从而能够提高冶炼
处理产品种类和产值等。
32.作为本发明的一个优选实施例,氧化熔炼炉为侧吹炉或底吹炉;氧化熔炼炉通过富氧浸没燃烧技术,保证喷入氧化熔炼炉内的燃料充分燃烧。
33.采用富氧浸没燃烧技术,保证喷入炉内的燃料充分燃烧,并且提高熔池加热速率,促进熔体剧烈翻滚,提高熔炼效率。
34.作为本发明的一个优选实施例,在对氧化熔炼渣进行还原熔炼的过程中,通过向还原熔炼炉的炉内喷入第二燃料和第二助燃气体,对还原熔炼炉内的氧化熔炼渣进行加热;其中,第二燃料为天然气、石油气、煤粉中的任意一种;和/或,第二助燃气体为工业氧气和空气混合而成;其中,在第二助燃气体中的总氧气的浓度为 50-85 v.%;和/或,控制还原熔炼炉的熔池内及液面上部空间内的气氛为还原性气氛,喷入所述还原熔炼炉内的第二助燃气体处于微欠氧状态。
35.经过氧化熔炼后的熔炼渣,再直接送入还原熔炼炉内,以将熔炼渣中铁、镍等氧化物还原成金属合金,回收熔渣中的有价金属元素。通过调整工业氧气和空气的混合比例,控制第二助燃气体中的总氧气的浓度在50-85 v.%,实现富氧燃烧熔炼反应。
36.在还原熔炼过程中,保证熔池内及液面上部空间内的气氛为还原性气氛,此时喷入炉内的助燃气体要处于微欠氧状态,以保证被还原出的金属不会再被氧化。
37.作为本发明的一个优选实施例,还原剂为块煤、焦炭、兰炭、报废石墨电极中的任意一种或按照任意比例混合的几种;其中,还原剂的粒度为5-15cm;还原剂的加入量为氧化熔炼渣的质量的10-15%。
38.还原熔炼过程中,需要向炉内不断加入还原剂,还原剂的粒度为5-15cm;还原剂的加入量为氧化熔炼渣的质量的10-15%,以保证还原剂能够有充分的时间通入熔池。
39.作为本发明的一个优选实施例,还原熔炼炉为侧吹炉或顶吹炉。
40.作为本发明的一个优选实施例,在对还原熔炼渣进行水淬处理,得到水淬玻璃渣的过程中,通过射流和雾化复合型喷水冷却的方式对还原熔炼渣进行水淬处理,在水淬处理过程中,冷却用水的重量为还原熔炼渣的重量的0.8-1.0倍,使还原熔炼渣迅速降至200℃以下。
41.还原熔渣水淬处理,是能够将熔渣固化成具有潜在活性的玻璃渣。
42.熔渣采用射流和雾化复合型喷水冷却方式,控制冷却用水用量约为还原熔渣量的0.8-1.0倍,以控制熔渣温度可迅速降至200℃以下,抑制玻璃渣的再结晶化。玻璃渣剩余温度则可依靠自然散热方式冷却。采用该种复合方式冷却,是由于水淬渣气孔多,渣中残留的自由水较多,将熔渣迅速冷却至抑制净化温度200℃以下,还有利于利用熔渣余热将水淬渣气孔中的这些自由水蒸发干,从而可以得到干燥的水淬玻璃渣。此外,这种冷却方式,较传统直接渣池泡水冷却方式,具有冷却水用量少,水淬渣干燥含水率低,后续应用可免去烘干,少量含水依靠自身余热或粉磨过程实现烘干。
43.作为本发明的一个优选实施例,通过制酸工艺将所述氧化烟气进行制酸包括:
对氧化烟气进行余热回收,得到余热回收后的氧化烟气;对余热回收后的氧化烟气进行除尘处理,得到除尘后的氧化烟气;通过制酸工艺对除尘后的氧化烟气进行制酸处理;和/或,通过高活性微粉制备工艺将水淬玻璃渣制备成高活性微粉包括:将水淬玻璃渣进行干燥处理,得到干燥的水淬玻璃渣;将干燥的水淬玻璃渣、激发剂、调整料、助磨剂按照预设配比混合,得到玻璃渣混料;其中,玻璃渣混料的各种原料质量比为:干燥的水淬玻璃渣:激发剂:调整料:助磨剂=100:3-14:5-20:0-1;通过粉磨设备将玻璃渣混料进行粉磨处理,使玻璃渣混料的细粉比表面积为400
ꢀ㎡
/kg以上,得到高活性微粉材料。
44.将干燥的水淬渣同激发剂、调整料、助磨剂一同加入粉磨设备中进行粉磨激发处理,控制最终细粉比表在400
ꢀ㎡
/kg以上,便得到高活性微粉材料,可作为辅助胶凝材料应用于混凝土、水泥制品等常用建材生产中,产品附加值大。
45.其中,激发剂为:石膏、生石灰、硫酸钠中的任意一种或按照任意比例混合的几种;调整料为:尾矿砂或石屑粉。
46.在熔炼生产过程中产生的各种粉尘、烟尘等,以及尾气净化产生的脱硫石膏等,经集中收集后,可通过压块等方式返回氧化熔炼工序中,进而实现全工程资源的回收再利用,资源综合利用率高。
47.以30万吨/年金属镍渣处理规模计算,当采用脱硫石膏作为冶炼辅料时,侧吹炉作为氧化熔炼和还原熔炼炉,每年的总产值可达6.5亿元,净利润在2亿元以上,投资回收期不到5年,工程经济性高。
48.通过上述具体实施方式可看出,本发明提供的金属镍渣的资源化利用方法,通过将排出的高温金属镍渣与含有碱性组分的冶炼辅料直接加入氧化熔炼炉内进行熔炼操作,在充分利用镍渣余热的前提下,实现镍渣中s的脱除和回收利用;含有碱性组分的冶炼辅料主要以含硫、多钙镁、多有价金属特点构成的物料,能够实现镍渣热态改性的同时,实现多种资源的协同化利用;通过本发明提供的方法能够更加全面的对熔渣余热资源进行利用,不仅有效利用了金属镍渣的高温,实现镍渣中s的脱除和回收利用;还利用了还原烟气的二次燃烧的余热以及利用氧化烟气进行制酸。本发明较传统再加热熔化方式相比较,具有能耗低、能协同其它含硫多金属固废的资源化处理渣、金属回收率高、产品种类多、总产值高、镍渣处理效率高、资源综合利用率高、生产成本低、工程经济性好等优点。
49.如上参照附图以示例的方式描述了根据本发明提出的金属镍渣的资源化利用方法。但是,本领域技术人员应当理解,对于上述本发明所提出的金属镍渣的资源化利用方法,还可以在不脱离本发明内容的基础上做出各种改进。因此,本发明的保护范围应当由所附的权利要求书的内容确定。