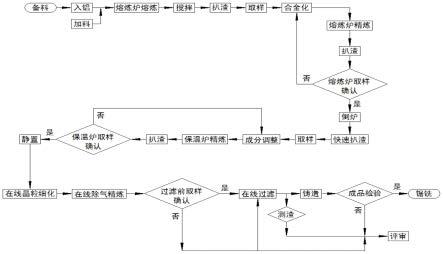
一种铝合金罐料熔炼中添加ubc回收废料的生产工艺
技术领域
1.本发明涉及用于铝合金罐体料的高精铝熔炼生产技术领域,具体涉及一种铝合金罐料熔炼中添加ubc回收废料的生产工艺。
背景技术:2.铝合金罐体包装由于其优良的综合性能、回收利用率高、环境污染小等特点,在未来的包装市场中前景光明;啤酒罐化、罐头食品接受度提高和限塑将会是未来金属包装需求增长的三大驱动因素。
3.用于铝合金罐的铝材属于铝加工行业的高端产品,其对于夹渣(杂)、气体(主要是h)、合金含量及机械性能有着及其严格的要求,例如用于铝合金罐体生产的3004、3104对针孔、断罐生产缺陷容忍度为17ppm,用于铝合金罐盖生产的5052、5042、5151对生产缺陷的容忍度为0ppm,如此高的要求也决定了用于铝合金罐铝材的高成本和高价格;但由于目前国内对于ubc的回收重利用尚处于较低的技术水平,存在ubc回收工艺参差不齐的问题,导致ubc回收生产出的复化料存在化学成分及夹渣(杂)的不稳定,因此只能用于整装油漆、广告色、涂料、染料、粘合剂、种子和洗衣粉的包装及小五金零件等低价值产品用铝,使得ubc回收价值较低。
4.经研究发现,ubc回收生产出的复化料用于铝合金罐体料的生产时,其主要问题是ubc复化料的夹渣(杂)会导致生产出的铝合金罐体料的夹渣(杂)及气体(主要为氢)偏高,由于夹渣(杂)及气体的存在破坏了金属铝的连续性,且由于夹渣(杂)和金属机体之间有着不同的弹性模量和膨胀系数,在夹渣(杂)相的尖角处易出现应力集中,常成为材料的断裂源和腐蚀源,尤其在合金罐体变薄拉伸过程中,这些缺陷使其所在区域金属塑性、强度不能满足变薄拉伸的最低要求,最终造成铝合金罐体、铝合金罐盖的各种产品缺陷;因此如何改进现有铝合金罐体料的熔炼生产工艺,使得ubc复化料用于铝合金罐体料的熔炼生产时也能生产出合格的铝合金罐用铝材,以提高ubc回收价值,成为铝合金罐料熔炼生产技术领域亟待解决的技术难题。
技术实现要素:5.为了克服背景技术中的不足,本发明公开了一种铝合金罐料熔炼中添加ubc回收废料的生产工艺,包括备料-加料/入铝-熔炼炉熔炼-搅拌-扒渣-取样-合金化-熔炼炉精炼-扒渣-熔炼炉取样确认-倒炉-快速扒渣-取样-成分调整-保温炉精炼-扒渣-保温炉取样确认-静置-在线晶粒细化-在线除气精炼-过滤前取样确认-过滤-铸造-成品检验-锯铣加工,其中加料工艺使用了30%-60%ubc复化料;在该工艺中,熔炼炉熔炼、保温炉熔炼中均采用了浮游溶剂法精炼工艺,同时在熔炼炉精炼、保温炉精炼工艺后均增加了渣含量检测,以充分保证在过滤前铝熔体夹渣和气体的含量达标,使使用ubc复化料的铝合金罐料熔炼的质量也能满足使用要求,提高了ubc回收价值。
6.为了实现所述发明目的,本发明采用如下技术方案:一种铝合金罐料熔炼中添加
ubc回收废料的生产工艺,包括备料-加料/入铝-熔炼炉熔炼-搅拌-扒渣-取样-合金化-熔炼炉精炼-扒渣-熔炼炉取样确认-倒炉-快速扒渣-取样-成分调整-保温炉精炼-扒渣-保温炉取样确认-静置-在线晶粒细化-在线除气精炼-过滤前取样确认-过滤-铸造-成品检验-锯铣加工;其中入铝为电解铝熔融料;ubc复化料允许使用的质量占比(总铝熔体质量)为30%-60%,自产废料允许使用的质量占比(总铝熔体质量)为10%-70%,电解铝熔融料允许使用的质量占比(总铝熔体质量)为0%-60%;熔炼炉实际熔炼时,ubc复化料、自产废料、电解铝熔融料的实际质量配比(总铝熔体质量)以下述方法确定:首先通过光谱分析测得待使用ubc复化料、自产废料、电解铝熔融料中各种合金化元素的含量,配料工程师根据测得的待使用物料中各种合金化元素的含量、及待生产铝合金罐料的各种合金化元素含量,提前制定出排产计划配料表,确保熔炼炉加入的炉料(包括ubc复化料、自产废料、电解铝熔融料)中的各种合金化元素不超过待生产铝合金罐料的各种合金化元素的上限值;熔炼时,首先将ubc复化料、自产废料分若干次加入熔炼炉中后,再加入电解铝熔融料;待铝熔体温度达到720c
°
以上时,取母液样进行成分检测,根据母液样中各种合金化元素的实际值与待生产铝合金罐料的各种合金化元素的目标值的差,计算出需加入的各种中间合金的质量,称取后加入铝熔体中,充分升温搅拌,然后进行熔炼炉精炼;在熔炼炉精炼、保温炉精炼中,均采用浮游溶剂法进行精炼除气除渣;在线除气精炼中,采用浮游法进行精炼除气除渣;本发明的铝合金罐料熔炼中添加ubc回收废料的生产工艺,与现有铝合金生产工艺相比,在熔炼炉熔炼、保温炉熔炼中均采用了浮游溶剂法精炼工艺,通过多次精炼工艺减少铝熔体夹渣,以充分保证在过滤前铝熔体夹渣和气体含量达标,使采用ubc复化料的铝合金罐料熔炼的质量能满足使用标准。
7.进一步的,在熔炼炉取样确认、保温炉取样确认中,均需通过铝熔体渣含量检测、成分检测后,才可进入下一工序;如在熔炼炉精炼结束后,进行熔炼炉取样确认,取样检测铝熔体中各种合金化元素的含量及渣含量,若铝熔体中各种合金化元素的含量及渣含量均满足工艺要求,则将铝熔体倒炉进入保温炉;若铝熔体中部分合金化元素的含量或渣含量不满足工艺要求时,需要重新计算需加入的中间合金的质量,称取后加入铝熔体中,充分升温搅拌,再次进行熔炼炉精炼,此时熔炼炉精炼则采用浮游法进行精炼除气除渣。
8.进一步的,熔炼炉精炼的浮游溶剂法精炼除气除渣,采用氩气与精炼剂同时加入熔融的铝熔体中,其中精炼剂为43%氯化镁(mgcl2)与57%氯化钾(kcl)混合而成的颗粒状,采用颗粒状精炼剂可减少精炼剂在使用过程中产生的“扬尘”现象,改善生产现场环境;熔炼炉精炼的浮游溶剂法精炼除气除渣的具体操作工艺条件为:s1.1、开始条件确认:熔体温度:720~750℃;熔炼炉合金化已结束;开启电磁搅拌;熔炼炉精炼的熔体温度较保温炉精炼、在线除气精炼稍高,但其最高温度不允许超过760℃,因铝合金罐料中,3系列镁的含量为1%左右,5系列镁的含量为5%左右,过高的熔体温度会形成难熔的“铝氧镁化合物”(mgal2o4),即尖晶石,该物质的存在对铝合金的连续性影响是致命的,因此须严格控制熔体温度;s1.2、熔炼炉浮游溶剂精炼除气除渣:通过手持精炼管将氩气与精炼剂一起加入熔融的铝熔体中,精炼管插入熔融铝熔体深度2/3以下;氩气流量为150~175升/分钟,通气时间为20-25分钟;精炼剂用量50公斤/百吨熔体,精炼剂在15-20分钟内随氩气匀速加入熔融的铝熔体中;浮游溶剂精炼除气除渣过程中,需不断移动精炼点位置,以便氩气与精炼剂
能均匀融入铝熔体中;熔炼炉精炼采用浮游溶剂精炼除气除渣工艺,是将氩气作为载体将精炼剂均匀加入熔炼炉对铝熔体进行联合除氢、除渣,其具有除氢、除渣速度快、效率高的优点;s1.3、精炼剂加入熔融铝熔体结束后,继续保持纯氩气精炼5分钟,在通过熔炼炉取样确认后,立即进行倒炉;虽然熔炼炉纯氩气精炼时间较短,铝熔体中有精炼剂“残渣”残留,但在后续的保温炉熔炼及倒炉过程中,这些“残渣”将有充分的时间逸出铝熔体,因此实际并不影响铝合金罐料最终铸造的质量。
9.进一步的,保温炉精炼的浮游溶剂法精炼除气除渣,采用氩气和精炼剂加入熔融的铝熔体中,其中精炼剂为43%氯化镁(mgcl2)与57%氯化钾(kcl)混合而成的颗粒物;保温炉精炼的浮游溶剂法精炼除气除渣的具体操作工艺条件为:s2.1、开始条件确认:熔体温度:720~730℃;已进行保温炉成分调整;开启电磁搅拌;s2.2、保温炉浮游溶剂精炼除气除渣:氩气和精炼剂通过设置在保温炉上部的石墨转子旋转搅拌加入熔融的铝熔体中,石墨转子插入熔融铝熔体深度为2/3;氩气流量为220升/分钟,精炼剂用量25公斤/百吨熔体,精炼剂加入熔融铝熔体中的流量为0.5-2.5 公斤/分钟,直至所有精炼剂随氩气加入完成;同样的,保温炉精炼采用浮游溶剂精炼除气除渣工艺,是利用浮游溶剂法精炼除气除渣工艺的除氢、除渣速度快、效率高的优点,控制缩短在保温炉中精炼时间,避免铝熔体在保温炉中与大气的接触时间过长而造成氢含量的增加;s2.3、精炼剂加入熔融铝熔体结束后,继续通入氩气精炼5分钟后,在通过保温炉取样确认后,即进入静置工艺;虽然保温炉纯氩气精炼时间较短,铝熔体中有精炼剂“残渣”残留,但在后续的在线除气精炼过程中,这些“残渣”将有充分的时间逸出铝熔体,因此实际并不影响铝合金罐料最终铸造的质量;若保温炉取样确认发现铝熔体中部分合金化元素的含量或渣含量不满足工艺要求时,需要重新计算需加入中间合金的质量,称取后加入铝熔体中,充分升温搅拌,再次进行保温炉精炼,此时保温炉精炼采用浮游法进行精炼除气除渣,直至保温炉取样确认通过。
10.进一步的,在线除气精炼的浮游法精炼除气除渣,采用氩气、氯气混合气加入熔融的铝熔体中,其中氩气和氯气的体积比为200:1;氩气、氯气混合气通过设置在除气箱底部的若干个加气转子旋转搅拌加入熔融的铝熔体中;在线除气精炼采用浮游法精炼除气除渣,是因为在线除气精炼为铝熔体在线过滤的最后一次精炼,采用浮游法精炼可避免精炼剂产生新的“残渣”;在线除气精炼的浮游法精炼除气除渣的具体操作工艺条件为:s3.1、开始条件确认:熔体温度:700~720℃;已进行在线晶粒细化;开启加气转子旋转;s3.2、在线除气浮游法精炼除气除渣:氩气、氯气混合气通过设置在除气箱底部的若干个加气转子旋转搅拌加入熔融的铝熔体中;混合气流量为175~200升/分钟。
11.进一步的,渣含量检测采用prefil-footprinter进行检测;熔炼炉取样确认、保温炉取样确认、过滤前取样确认中的渣含量检测结果曲线与相应的prefil-footprinter标准曲线进行比对,当熔炼炉取样确认、保温炉取样确认、过滤前取样确认中的渣含量检测结果
曲线位于相应的prefil-footprinter标准曲线上方,确认渣含量检测结果符合要求;prefil-footprinter标准曲线通过实验确定。
12.进一步的,过滤包括顺序进行的板式过滤和管式过滤,管式过滤为铝熔体净化的最后工序;新更换管式过滤器需先通过500吨不含镁的其他牌号铝熔体后,才可用于铝合金罐料铝熔体的过滤,设置此条件的原因为:铝合金罐料中均含有镁(mg)元素,而镁(mg)元素的氧化物会影响管式过滤器中铝熔体表面覆盖的氧化膜的致密性,从而导致铝熔体会从大气中吸氢、吸氧和进一步氧化,最终使铝合金罐料的铸锭质量下降;而新更换管式过滤器通过500吨不含镁的其他牌号铝熔体后,会在管式过滤器中铝熔体表面形成致密的氧化膜,从而防止上述情况的发生;管式过滤器在铝合金罐料铝熔体过滤量达到5000吨后,不可再用于铝合金罐料铝熔体的过滤,设置此条件的原因为:铝合金熔体过滤分为表面过滤和内部过滤两种,管式过滤属于表面和内部双重过滤;表面过滤是指固体杂质主要沉积在过滤介质表面;内部过滤是指铝液携带夹渣物在过滤介质中沿曲折的通道和空隙流动;受到直接拦截、吸附、沉淀等作用,与孔壁碰撞而牢固地粘附在孔壁上;随着过滤的进行,孔道有效过滤截面逐渐减少,透过能力下降,过滤精度有所提高,但是,随着过滤介质内的杂质的增加,管式进出口的液位差越来越大,达到一定程度后,聚集在过滤介质通道内的杂质会集中释放,直接进入产品,导致夹渣缺陷,因此,当达到一定通过量时,会影响到铝合金罐料的性能,必须限制管式过滤器对铝合金罐料的过滤量;对已不适合铝合金罐料铝熔体的过滤的管式过滤器,其仍可以继续供其他要求较低铝合金熔体的过滤。
13.由于采用如上所述的技术方案,本发明具有如下有益效果:本发明公开的一种铝合金罐料熔炼中添加ubc回收废料的生产工艺,包括备料-加料/入铝-熔炼炉熔炼-搅拌-扒渣-取样-合金化-熔炼炉精炼-扒渣-熔炼炉取样确认-倒炉-快速扒渣-取样-成分调整-保温炉精炼-扒渣-保温炉取样确认-静置-在线晶粒细化-在线除气精炼-过滤前取样确认-过滤-铸造-成品检验-锯铣加工,其中加料工艺可使用30%-60%ubc复化料;在该工艺中,熔炼炉熔炼、保温炉熔炼中均采用了浮游溶剂法精炼工艺,同时在熔炼炉精炼、保温炉精炼、在线除气精炼工艺后均增加了渣含量检测,以充分保证在过滤前铝熔体夹渣和气体的含量达标,使采用ubc复化料的铝合金罐料熔炼的质量也能满足使用要求,提高了ubc回收价值,从而解决了使用ubc复化料熔炼铝合金罐料的技术难题,极大提高了ubc回收价值,降低了铝合金罐体料的生产成本,为企业带来了良好的经济收益。
附图说明
14.图1为铝合金罐料熔炼中添加ubc回收废料的生产工艺流程图;图2为prefil-footprinter标准曲线示意图;图3为实例一ubc复化料、自产废料、电解铝熔融料投料占比关系表;图4为实例一合金化元素成分控制表;图5为实例二ubc复化料、自产废料、电解铝熔融料投料占比关系表;图6为实例二合金化元素成分控制表;图7为实例三ubc复化料、自产废料、电解铝熔融料投料占比关系表;图8为实例三合金化元素成分控制表。
15.具体实施方式
16.通过下面的实施例可以详细的解释本发明,公开本发明的目的旨在保护本发明范围内的一切技术改进。
17.一种铝合金罐料熔炼中添加ubc回收废料的生产工艺,包括备料-加料/入铝-熔炼炉熔炼-搅拌-扒渣-取样-合金化-熔炼炉精炼-扒渣-熔炼炉取样确认-倒炉-快速扒渣-取样-成分调整-保温炉精炼-扒渣-保温炉取样确认-静置-在线晶粒细化-在线除气精炼-过滤前取样确认-过滤-铸造-成品检验-锯铣加工;其中入铝为电解铝熔融料,其中加料为ubc复化料、自产废料,ubc复化料允许使用的质量占比(总铝熔体质量)为30%-60%,自产废料允许使用的质量占比(总铝熔体质量)为10%-70%,电解铝熔融料允许使用的质量占比(总铝熔体质量)为0%-60%;熔炼炉实际熔炼时,ubc复化料、自产废料、电解铝熔融料的实际质量配比(总铝熔体质量)以下述方法确定:首先通过光谱分析测得待使用ubc复化料、自产废料、电解铝熔融料中各种合金化元素的含量,配料工程师根据测得的待使用物料中各种合金化元素的含量、及待生产铝合金罐料的各种合金化元素含量,提前制定出排产计划配料表,确保熔炼炉加入的炉料(包括ubc复化料、自产废料、电解铝熔融料)中的各种合金化元素不超过待生产铝合金罐料的各种合金化元素的上限值;熔炼时,首先将ubc复化料、自产废料分若干次加入熔炼炉中后,再加入电解铝熔融料;待铝熔体温度达到720c
°
以上时,取母液样进行成分检测,根据母液样中各种合金化元素的实际值与待生产铝合金罐料的各种合金化元素的目标值的差,计算出需加入的各种中间合金的质量,称取后加入铝熔体中,充分升温搅拌,然后进行熔炼炉精炼;熔炼炉精炼精炼时采用浮游溶剂法精炼除气除渣,采用氩气与精炼剂同时加入熔融的铝熔体中,其中精炼剂为43%氯化镁(mgcl2)与57%氯化钾(kcl)混合而成的颗粒状;熔炼炉精炼的浮游溶剂法精炼除气除渣的具体操作工艺条件为:s1.1、开始条件确认:熔体温度:730~740℃;熔炼炉合金化已结束;开启电磁搅拌;s1.2、熔炼炉浮游溶剂精炼除气除渣:通过手持精炼管将氩气与精炼剂一起加入熔融的铝熔体中,精炼管插入熔融铝熔体深度2/3以下;氩气流量为175升/分钟,通气时间为20分钟;精炼剂用量50公斤/百吨熔体,精炼剂在15分钟内随氩气匀速加入熔融的铝熔体中;浮游溶剂精炼除气除渣过程中,需不断移动精炼点位置,以便氩气与精炼剂能均匀融入铝熔体中;s1.3、精炼剂加入熔融铝熔体结束后,继续保持纯氩气精炼5分钟;在通过熔炼炉取样确认后,立即进行倒炉;保温炉精炼时采用浮游溶剂法精炼除气除渣,氩气和精炼剂同时加入熔融的铝熔体中,其中精炼剂为43%氯化镁(mgcl2)与57%氯化钾(kcl)混合而成的颗粒状;保温炉精炼的浮游溶剂法精炼除气除渣的具体操作工艺条件为:s2.1、开始条件确认:熔体温度:720~730℃;已进行保温炉成分调整;开启电磁搅拌;s2.2、保温炉浮游溶剂精炼除气除渣:氩气和精炼剂通过设置在保温炉上部的石
墨转子旋转搅拌加入熔融的铝熔体中,石墨转子插入熔融铝熔体深度为2/3;氩气流量为220升/分钟,精炼剂用量25公斤/百吨熔体,精炼剂加入熔融铝熔体中的流量为2.0公斤/分钟,直至所有精炼剂随氩气加入完成;s2.3、精炼剂加入熔融铝熔体结束后,继续通入氩气精炼5分钟后,在通过保温炉取样确认后,即进入静置工艺;在线除气精炼采用浮游法精炼除气除渣,氩气、氯气混合气加入熔融的铝熔体中,其中氩气和氯气的体积比为200:1;氩气、氯气混合气通过设置在除气箱底部的若干个加气转子旋转搅拌加入熔融的铝熔体中;在线除气精炼的浮游法精炼除气除渣的具体操作工艺条件为:s3.1、开始条件确认:熔体温度:700~720℃;已进行在线晶粒细化;开启加气转子旋转;s3.2、在线除气浮游法精炼除气除渣:氩气、氯气混合气通过设置在除气箱底部的若干个加气转子旋转搅拌加入熔融的铝熔体中;混合气流量为200升/分钟;在线除气精炼后进行过滤前取样确认,但过滤前取样确认不管其结果如何,均不对铝熔体再进行任何处理,过滤前取样确认结果仅用于最终铸锭质量的评定参考;熔炼炉取样确认、保温炉取样确认、过滤前取样确认的渣含量检测采用prefil-footprinter进行检测;熔炼炉取样确认、保温炉取样确认、过滤前取样确认中的渣含量检测结果曲线与相应的prefil-footprinter标准曲线进行比对,当熔炼炉取样确认、保温炉取样确认、过滤前取样确认中的渣含量检测结果曲线位于相应的prefil-footprinter标准曲线上方,确认渣含量检测结果符合要求;prefil-footprinter标准曲线通过实验确定;补充说明的是:在现有ubc复化料来料质量较差的情况下,熔炼炉取样确认、保温炉取样确认、过滤前取样确认中除进行铝熔体各合金化成分的检测外,还同步进行渣含量检测,但随着ubc复化料来料质量的逐步改善,可逐步取消熔炼炉取样确认、保温炉取样确认、过滤前取样确认中的渣含量检测,以进一步降低铝合金罐料的生产成本;过滤包括顺序进行的板式过滤和管式过滤,管式过滤为铝熔体净化的最后工序;新更换管式过滤器需先通过500吨不含镁的其他牌号铝熔体后,才可用于铝合金罐料铝熔体的过滤;管式过滤器在铝合金罐料铝熔体过滤量达到5000吨后,不可再用于铝合金罐料铝熔体的过滤。
18.以下用实际生产中的实际数据说明在铝合金罐料熔炼中,ubc复化料、自产废料、电解铝熔融料的投料质量占比关系,以及各合金化元素的控制情况:实例一:熔炼炉一炉的产量为120吨,生产3104铝合金罐体料;通过光谱分析测得待使用ubc复化料、自产废料、电解铝熔融料中各种合金化元素的含量,配料工程师根据测得的ubc复化料、自产废料、电解铝熔融料中各种合金化元素的含量,及待生产3104铝合金罐体料的各种合金化元素含量,制定出排产计划配料表为:ubc复化料55.6吨,质量占比为46%;自产废料39吨,质量占比为32.3%;电解铝熔融料26.2吨,质量占比为21.7%;炉料熔化到720℃以上时,取母液进行检测,根据母液样中各种合金化元素的实际值与待生产铝合金罐料的各种合金化元素的目标值的差,计算出需加入的各种中间合金的质量分别为:alsi20中间合金160kg,alfe20中间合金260kg,alcu50中间合金70kg,almn20中间合金400kg,mg锭280kg;
经熔炼炉精炼、保温炉精炼、在线除气精炼后,过滤前取样确认结果所有合金化元素含量符合要求;具体数据参见说明书附图3、附图4。
19.实例二:熔炼炉一炉的产量为100吨,生产3104铝合金罐体料;通过光谱分析测得待使用ubc复化料、自产废料、电解铝熔融料中各种合金化元素的含量,配料工程师根据测得的ubc复化料、自产废料、电解铝熔融料中各种合金化元素的含量,及待生产3104铝合金罐体料的各种合金化元素含量,制定出排产计划配料表为:ubc复化料57.7吨,质量占比为57.8%;自产废料11吨,质量占比为11%;电解铝熔融料31.2吨,质量占比为31.2%;炉料熔化到720℃以上时,取母液进行检测,根据母液样中各种合金化元素的实际值与待生产铝合金罐料的各种合金化元素的目标值的差,计算出需加入的各种中间合金的质量分别为:alsi20中间合金250kg,alfe20中间合金350kg,alcu50中间合金55kg,almn20中间合金300kg,mg锭350kg;经熔炼炉精炼、保温炉精炼、在线除气精炼后,过滤前取样确认结果所有合金化元素含量符合要求;具体数据参见说明书附图5、附图6。
20.实例三:熔炼炉一炉的产量为110吨,生产3104铝合金罐体料;通过光谱分析测得待使用ubc复化料、自产废料、电解铝熔融料中各种合金化元素的含量,配料工程师根据测得的ubc复化料、自产废料、电解铝熔融料中各种合金化元素的含量,及待生产3104铝合金罐体料的各种合金化元素含量,制定出排产计划配料表为:ubc复化料35.2吨,质量占比为30.4%;自产废料75吨,质量占比为64.8%;电解铝熔融料5.5吨,质量占比为4.8%;炉料熔化到720℃以上时,取母液进行检测,根据母液样中各种合金化元素的实际值与待生产铝合金罐料的各种合金化元素的目标值的差,计算出需加入的各种中间合金的质量分别为:alsi20中间合金30kg,alfe20中间合金0kg,alcu50中间合金150kg,almn20中间合金0kg,mg锭0kg;经熔炼炉精炼、保温炉精炼、在线除气精炼后,过滤前取样确认结果所有合金化元素含量符合要求;具体数据参见说明书附图7、附图8。
21.本发明未详述部分为现有技术。