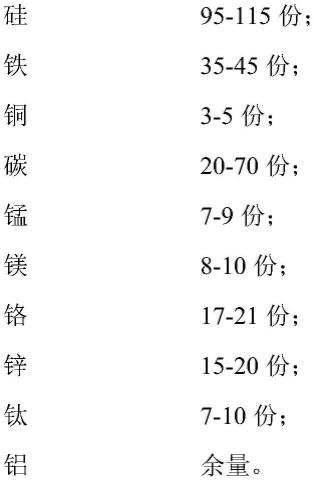
1.本发明涉及铝合金型材技术领域,尤其涉及一种高强度铝合金型材及其制备方法。
背景技术:2.铝合金具有轻巧、坚固的优势,是“汽车轻量化”的理想材料。国际研究机构实验表明,若汽车整车重量降低10%,则燃油效率可提高6%~8%;汽车整备质量每减少100公斤,百公里油耗可降低0.3~0.6升;汽车重量降低1%,油耗可降低0.7%。在整车中,动力系统、底盘系统以及车身是质量最大的3大系统,其总质量达到整车质量的83%。因此,用铝合金材料制造汽车底盘零部件“以铝代钢”,对实现汽车轻量化,达到节能减排、提升动力、提高安全性的目标具有重要意义。
3.在众多轻量化汽车材料中,铝合金以其独特的性能优势成为汽车制造业中广泛使用的轻量化金属材料。铝合金材料由于具有密度低、耐蚀性好、导热性好、比强度高、易于加工等特点,并且易于回收循环利用。近年来,随着材料技术的进步和环保及节能减排意识的增强,铝合金在汽车轻量化中的应用规模快速增长。
技术实现要素:4.本发明的目的是针对现有技术中的不足,提供一种高强度铝合金型材及其制备方法。
5.为实现上述目的,本发明采取的技术方案是:
6.本发明的第一方面是提供一种高强度铝合金型材,按重量份数计,组分包括:
[0007][0008][0009]
优选地,所述碳选自碳纳米管或石墨烯纳米颗粒中的至少一种。
[0010]
本发明的第二方面是提供一种上述高强度铝合金型材的制备方法,步骤包括:
[0011]
s1、按重量份数称取硅、铁、铜、碳、锰、镁、铬、锌、钛以及铝并混合,将混合物料进行预热处理,将预热处理完成后的所述混合物料放入熔炼炉中熔炼成液态铝合金,对所述液态铝合金进行冷却处理,制得铝合金铸块;
[0012]
s2、对步骤s1中制得的所述铝合金铸块进行均匀化处理,将均质化处理完成后的所述铝合金铸块进行加热并采用挤压机挤压成型,制得铝合金板材;
[0013]
s3、对步骤s2制得的所述铝合金板材进行调质处理,即得所述高强度铝合金型材。
[0014]
优选地,步骤s1中,所述预热处理的温度为350℃-450℃,所述预热处理的时间为0.6-0.8小时。
[0015]
优选地,步骤s1中,所述熔炼的温度为750℃-770℃,所述熔炼的时间为7-9小时。
[0016]
优选地,步骤s1中,所述冷却处理的降温速度为100℃/min-120℃/min。
[0017]
优选地,步骤s2中,所述均匀化处理包括:以30℃/min-40℃/min的速率升温至370℃-390℃保温3-4小时,再以50℃/min-60℃/min的速率升温至440℃-460℃保温2-3小时,最后以60℃/min-70℃/min的速率升温至520℃-530℃保温6-8小时。
[0018]
优选地,步骤s3中,所述调质处理包括:淬火以及回火;所述淬火的温度为630℃-650℃,所述回火的温度为500℃-550℃,所述回火的时间为1.2-1.8小时。
[0019]
本发明采用以上技术方案,与现有技术相比,具有如下技术效果:
[0020]
本发明的高强度铝合金型材中加入了碳,不仅增加了铝合金的机械强度以及延展性,还提高了铝合金的抗腐蚀性能;本发明中各元素的含量分配使得各元素的作用得到了充分的发挥,显著提高了铝合金的力学性能;本发明的制备方法使得铝合金的硬度得到了极大的提升,三段式均匀化处理的温度以及时间的控制使得铝合金的内部组织得到了改善,使得后续铝合金内的组织在后续挤压成型工序中更均匀。
具体实施方式
[0021]
下面将对本发明实施例中的技术方案进行清楚、完整地描述,显然,所描述的实施例仅仅是本发明一部分实施例,而不是全部的实施例。基于本发明中的实施例,本领域普通技术人员在没有作出创造性劳动的前提下所获得的所有其他实施例,都属于本发明保护的范围。
[0022]
需要说明的是,在不冲突的情况下,本发明中的实施例及实施例中的特征可以相互组合。
[0023]
下面结合具体实施例对本发明作进一步说明,但不作为本发明的限定。
[0024]
实施例1
[0025]
本实施例提供了一种高强度铝合金型材的制备方法,步骤包括:
[0026]
s1、按质量百分比计,称取1.05%硅、0.37%铁、0.041%铜、0.5%碳、0.8%锰、0.91%镁、0.19%铬、0.18%锌、0.084%钛以及余量铝并混合,以400℃的预热温度,将混合物料进行0.7小时的预热处理,将预热处理完成后的所述混合物料放入熔炼炉中,以760℃的温度熔炼8小时,即得液态铝合金,以110℃/min的降温速度对所述液态铝合金进行冷却处理,制得铝合金铸块;
[0027]
s2、对步骤s1中制得的所述铝合金铸块进行三段式均匀化处理,第一段均匀化处理为以35℃/min的速率升温至380℃保温3.5小时,第二段均匀化处理为以55℃/min的速率
升温至450℃保温2.5小时,第三段均匀化处理为以65℃/min的速率升温至525℃保温7小时;将均质化处理完成后的所述铝合金铸块进行加热并采用挤压机挤压成型,制得铝合金板材;
[0028]
s3、对步骤s2制得的所述铝合金板材进行调质处理,所述调质处理包括:以640℃的温度进行淬火后,再以525℃的温度回火1.5小时;即得所述高强度铝合金型材。
[0029]
实施例2
[0030]
本实施例提供了另一种高强度铝合金型材的制备方法,步骤包括:
[0031]
s1、按质量百分比计,称取0.95%硅、0.35%铁、0.03%铜、0.2%碳、0.7%锰、0.8%镁、0.17%铬、0.15%锌、0.07%钛以及余量铝并混合,以350℃的预热温度,将混合物料进行0.6小时的预热处理,将预热处理完成后的所述混合物料放入熔炼炉中,以750℃的温度熔炼7小时,即得液态铝合金,以100℃/min的降温速度对所述液态铝合金进行冷却处理,制得铝合金铸块;
[0032]
s2、对步骤s1中制得的所述铝合金铸块进行三段式均匀化处理,第一段均匀化处理为以30℃/min的速率升温至370℃保温3小时,第二段均匀化处理为以50℃/min的速率升温至440℃保温2小时,第三段均匀化处理为以60℃/min的速率升温至520℃保温6小时;将均质化处理完成后的所述铝合金铸块进行加热并采用挤压机挤压成型,制得铝合金板材;
[0033]
s3、对步骤s2制得的所述铝合金板材进行调质处理,所述调质处理包括:以630℃的温度进行淬火后,再以500℃的温度回火1.2小时;即得所述高强度铝合金型材。
[0034]
实施例3
[0035]
本实施例提供了另一种高强度铝合金型材的制备方法,步骤包括:
[0036]
s1、按质量百分比计,称取1.15%硅、0.45%铁、0.05%铜、0.7%碳、0.9%锰、1.0%镁、0.21%铬、0.2%锌、0.1%钛以及余量铝并混合,以450℃的预热温度,将混合物料进行0.8小时的预热处理,将预热处理完成后的所述混合物料放入熔炼炉中,以770℃的温度熔炼9小时,即得液态铝合金,以120℃/min的降温速度对所述液态铝合金进行冷却处理,制得铝合金铸块;
[0037]
s2、对步骤s1中制得的所述铝合金铸块进行三段式均匀化处理,第一段均匀化处理为以40℃/min的速率升温至390℃保温4小时,第二段均匀化处理为以60℃/min的速率升温至460℃保温3小时,第三段均匀化处理为以70℃/min的速率升温至530℃保温8小时;将均质化处理完成后的所述铝合金铸块进行加热并采用挤压机挤压成型,制得铝合金板材;
[0038]
s3、对步骤s2制得的所述铝合金板材进行调质处理,所述调质处理包括:以650℃的温度进行淬火后,再以550℃的温度回火1.8小时;即得所述高强度铝合金型材。
[0039]
对比例
[0040]
本对比例提供一种铝合金的制备方法,步骤包括:
[0041]
s1、按照重量百分比进行取料:铜0.2%、镁0.5%、硅0.1-0.3%、锌0.02%、锂0.4%、锰0.1%、钛0.03%、钒0.01%、硼0.02%、镍0.03%、铬0.05%、铁0.3%,其余为铝及不可避免的杂质;
[0042]
s2、将s1中的物料进行混合,将混合后的物料先进行预热,预热温度为400℃,预热时间为0.5h,将预热后的混合物料放入熔炼炉内进行熔融,熔炼温度为700℃,熔炼时间为8h;
[0043]
s3、将熔化后的混合物进行浇铸,浇铸温度为750℃,对浇铸后的材料进行退火处理,退火温度为300℃;
[0044]
s4、将退火后铝合金材料冷却至常温,获得铝合金型材,然后通过打磨机进行平整打磨。
[0045]
检测实施例
[0046]
对实施例1-3制备的高强度铝合金型材进行力学检测,结果如下表所示:
[0047] 屈服强度(mpa)抗拉强度(mpa)抗腐蚀性能实施例1358395p实施例2337346p实施例3342354p对比例296317eb
[0048]
综上所述,本发明的高强度铝合金型材中加入了碳,不仅增加了铝合金的机械强度以及延展性,还提高了铝合金的抗腐蚀性能;本发明中各元素的含量分配使得各元素的作用得到了充分的发挥,显著提高了铝合金的力学性能;本发明的制备方法使得铝合金的硬度得到了极大的提升,三段式均匀化处理的温度以及时间的控制使得铝合金的内部组织得到了改善,使得后续铝合金内的组织在后续挤压成型工序中更均匀。
[0049]
以上所述仅为本发明较佳的实施例,并非因此限制本发明的实施方式及保护范围,对于本领域技术人员而言,应当能够意识到凡运用本发明说明书内容所作出的等同替换和显而易见的变化所得到的方案,均应当包含在本发明的保护范围内。